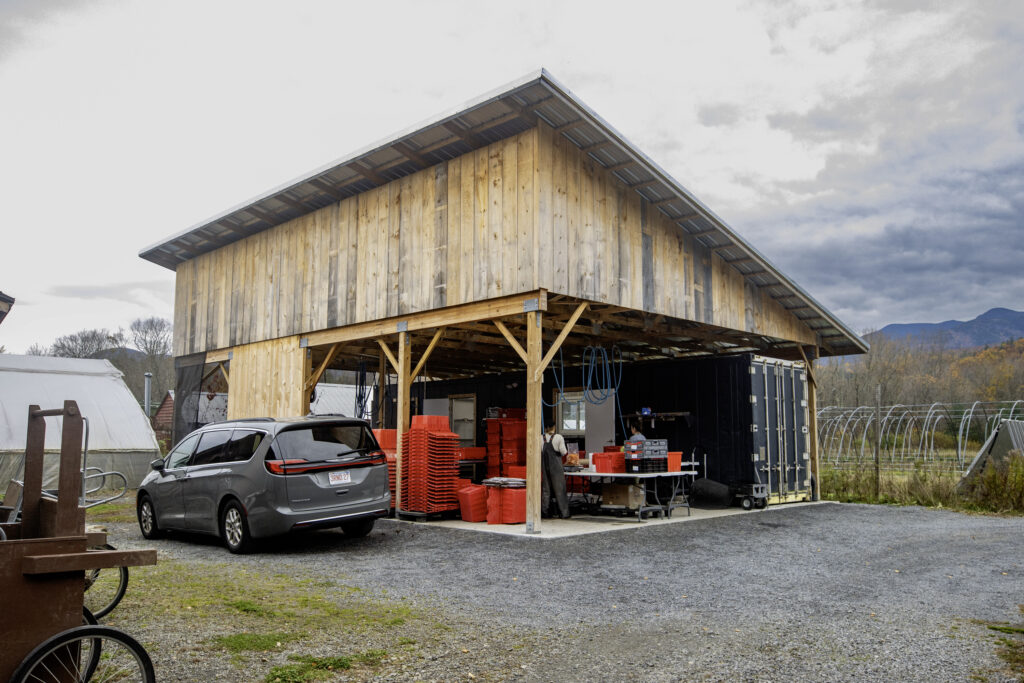
Lissa Goldstein runs the farming operation at Wild Work Farm in Keene Valley, New York nestled in the Adirondack Mountains. Wild Work is a diversified vegetable farm with some blueberries and fruit trees. When Lissa heard we were building out examples of wash/pack areas she reached out to share details of her shipping container project, “I’ve used a lot of the UVM resources when planning our project, so happy to contribute info if it is useful.” Lissa has built a great example of a versatile, easy to clean space.
About Wild Work Farm
- Acreage: Lease 3 acres, grow on 1.5/yr
- Location: Keene Valley, NY
- Gross Sales: $200,000 – 250,000
- Markets: ⅓ farmers market ⅓ free choice CSA ⅓ local wholesale
- 140 member CSA
- Produce available March – Dec
- Crew Size of 5
- 1 Full time year round, 2 full time seasonal, 2 part time seasonal
Goals of the Project
There were some serious constraints coming from working out of an old barn that Lissa was looking to address.
Challenges of existing space:
- Space was too small for amount of product handled
- Didn’t feel clean
- Poor flow
- Poor ergonomics
- Using water was not good for the building
- Did not feel prepared for FSMA Produce Safety Rule Food safety regulations
- Not insulated or heated
- Difficult to clean
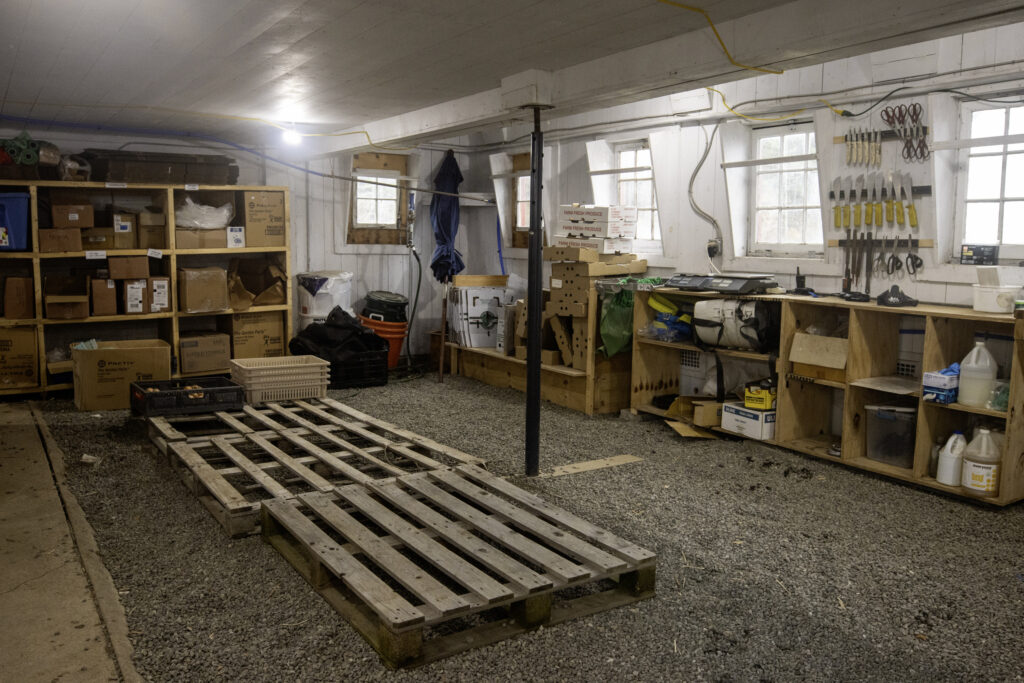
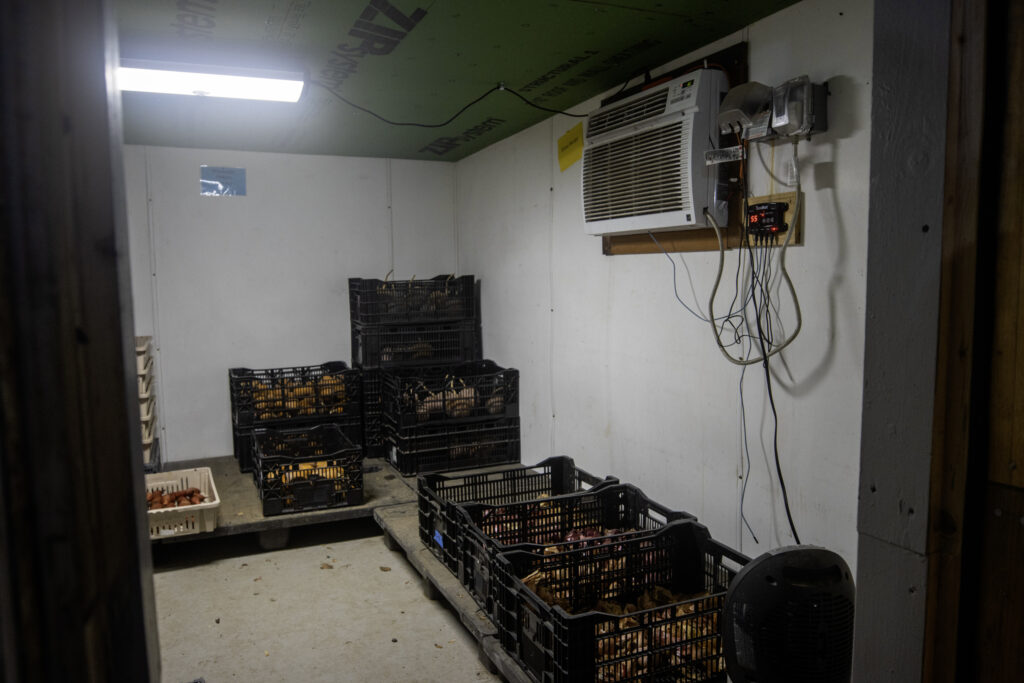
About the Project
This project was built in 2020-2021. It consisted of a 30’ x 40’ poured concrete slab with reinforced edges, trench drain, and built- in sump pit. A retrofitted 8’ x 40’ insulated shipping container was then placed on one edge of the pad and built a roof over the whole thing, which provided both outdoor and indoor washing space and a cooler. Lissa reflects “It’s not huge, but it works for us and is moveable and relatively flood proof (important on our leased, flood-prone land).” The walls of the shipping container came in stainless steel so they are easily washable and the floor inside was built up and pitched to drain into the in-ground sump-pit.
The majority of activity happens on the pad, under the roof as product moves from the blue field bins (dirty) to the red (washed) bins, ready for distribution.
The shipping container was retrofitted by Ed Marin of Gradients LLC based out of Plattsburgh NY. They added walls to divide the space between a farm office, wash/pack and a cooler.
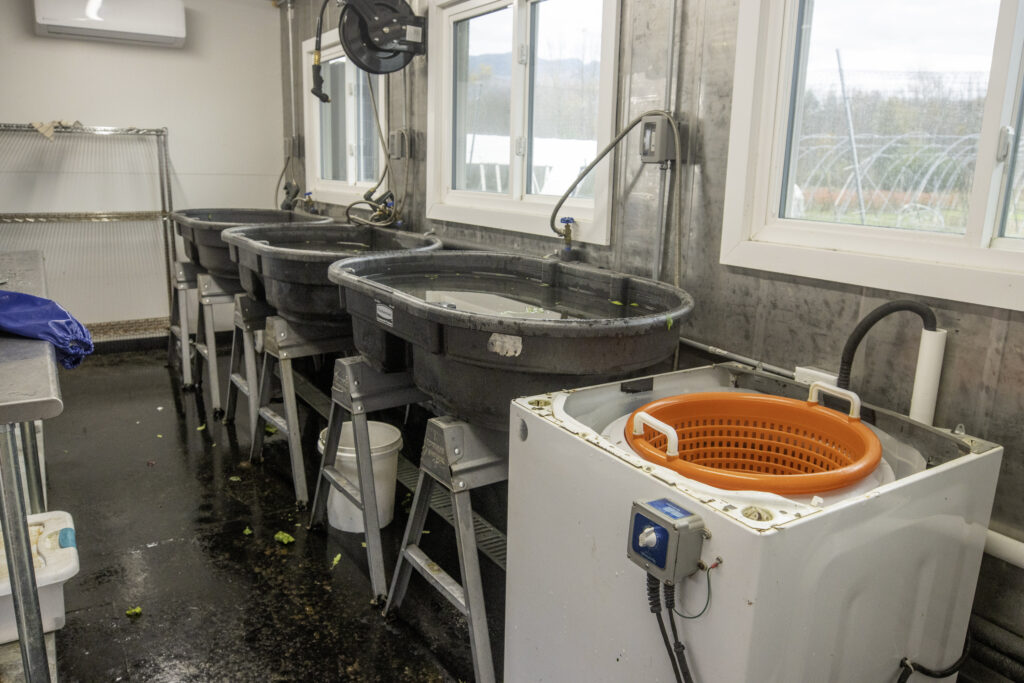
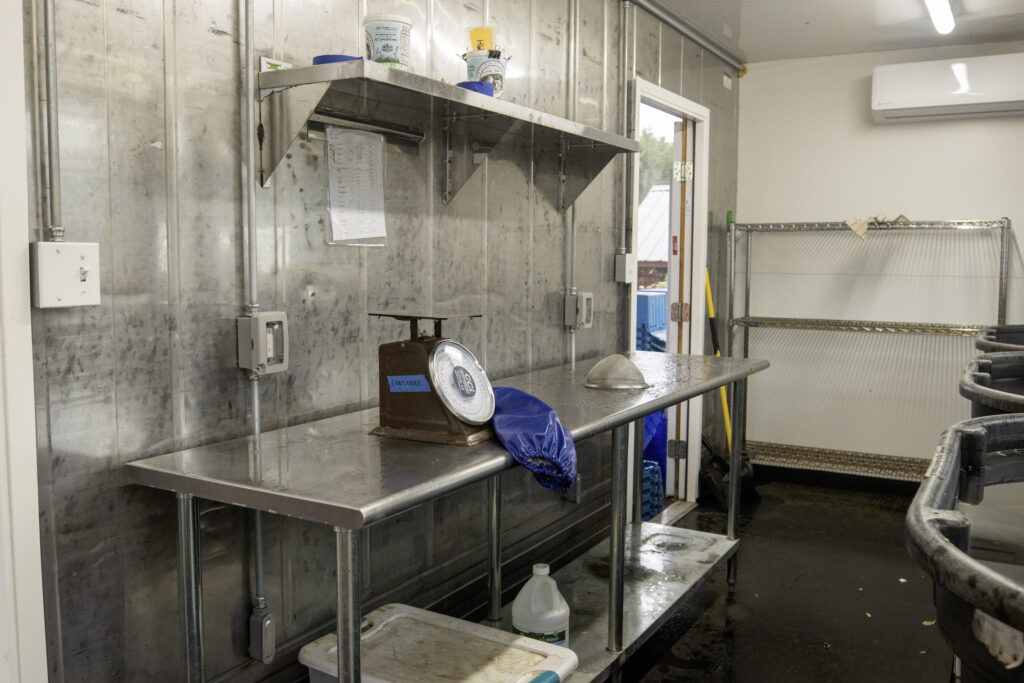
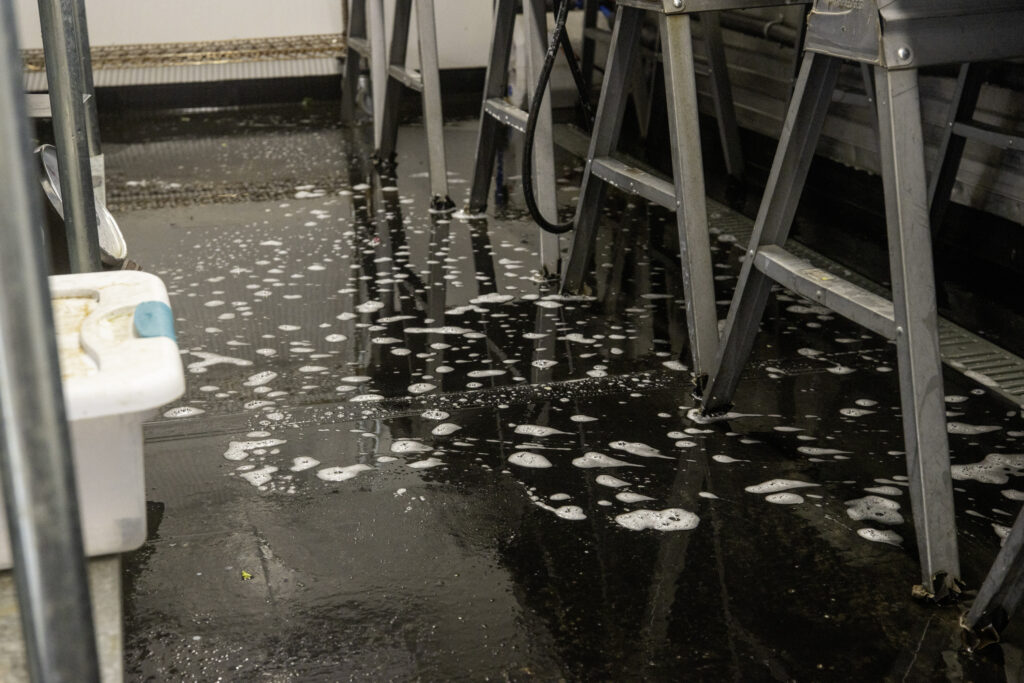
Features of the Space
- High hoses off the ground
- Drunk tanks, & custom built greens spinner
- Use of pallets keep things off the ground
- Greenhouse benches as tables
- Restaurant strips to hold notes to know what to pack
- Heat pumps & commercial refrigeration
- Shade cloth for sun blocking
- Sloped to a trench drain with no need to squeegee
- Motion sensor lights (in cooler)
Cleaning procedures
- Sweep out debris
- Rinse all bins
- Alternate using detergent: One week blue bins get soap, next week the red bins do
- Stack the bins
- Sweep debris
- Wash surfaces, tubs and tools, pallets
- Final sweep
- Wash the floor (rinse)
- Floor gets some detergent from washing tubs and bins and gets an annual deep clean
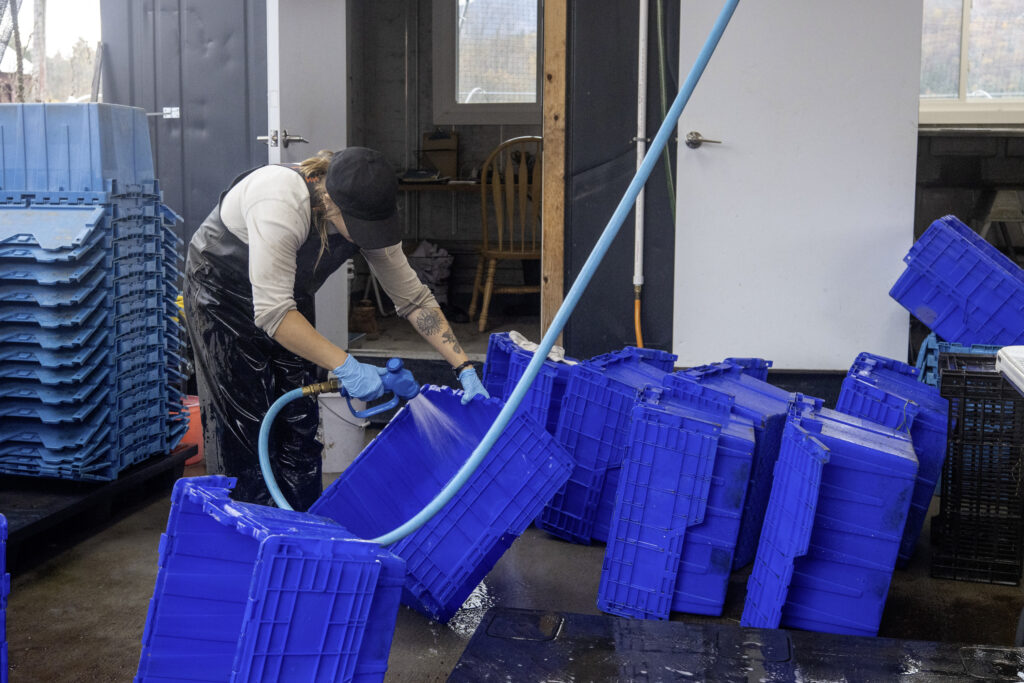
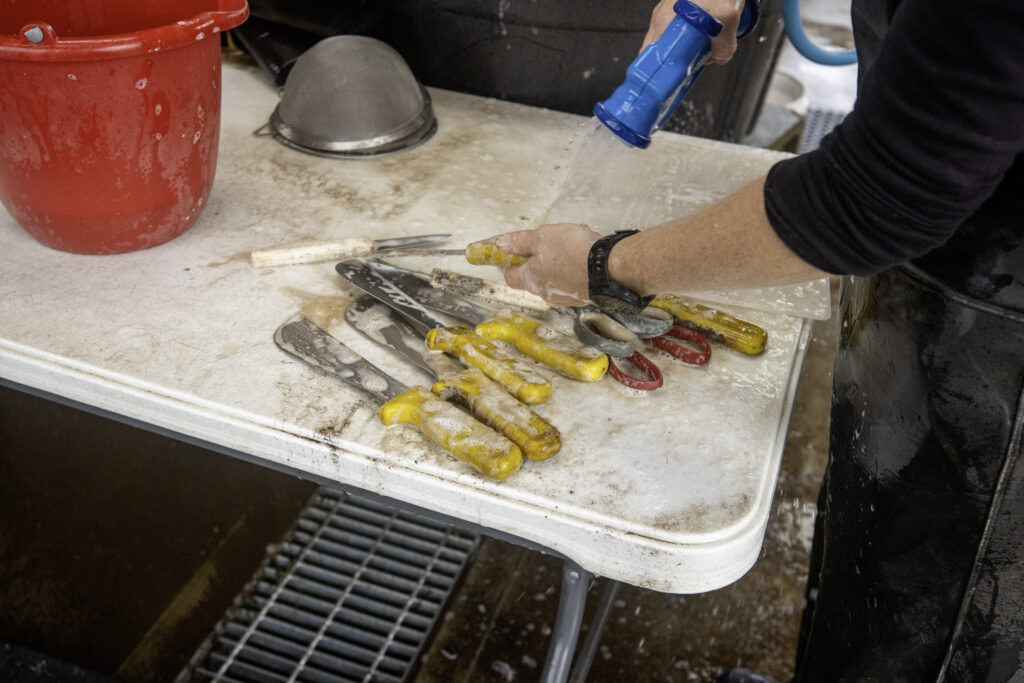
Floor Plan
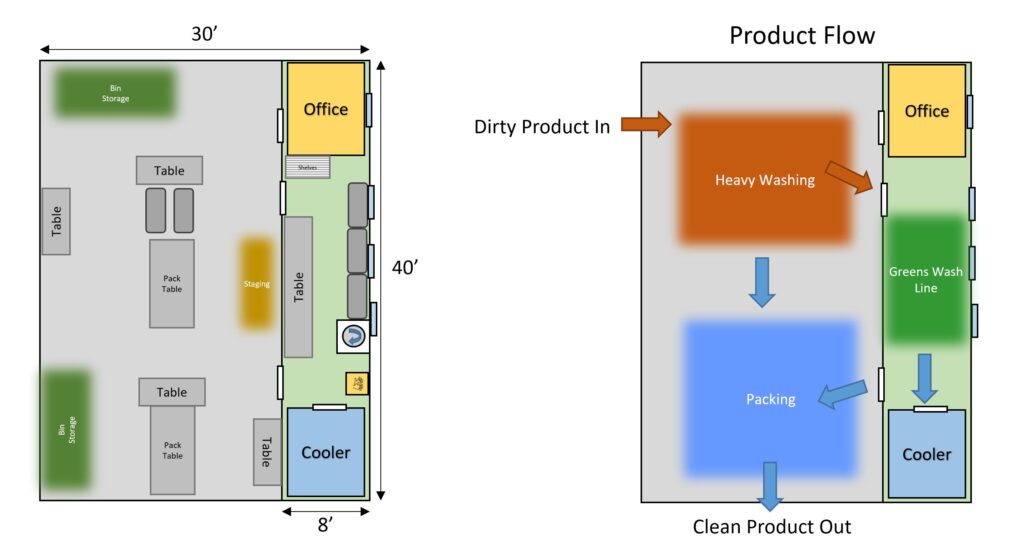
Costs:
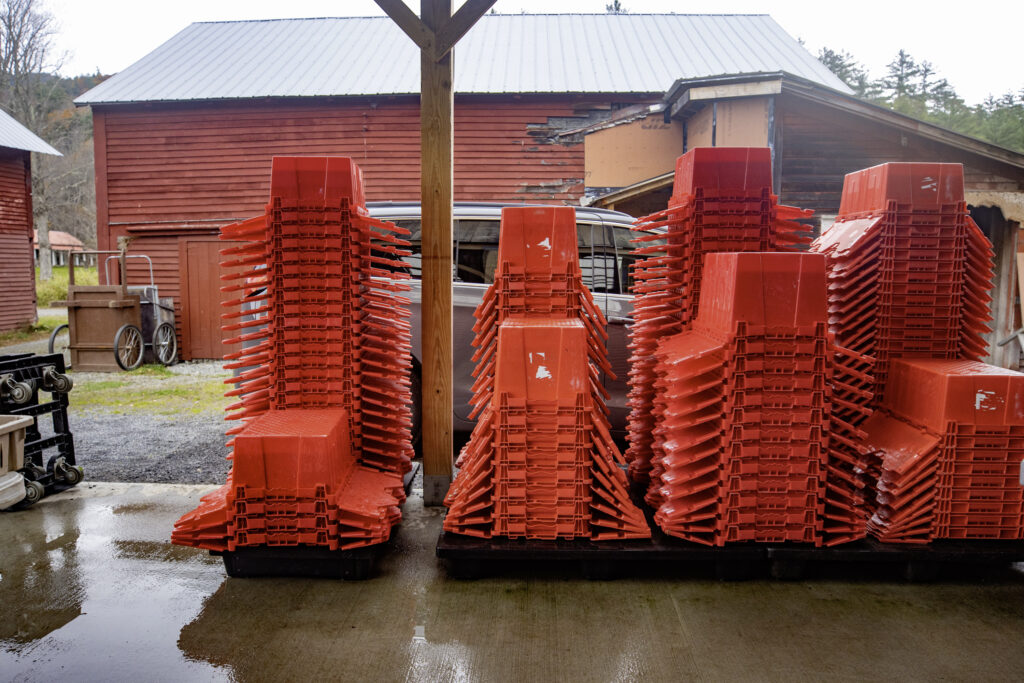
$10,000 – Site Prep (included installation of new driveway for access, main electrical and plumbing lines, and connection to drainage)
$8,000 – Concrete slab
$30,000 – Roof
$40,000 Retrofitted container
$2,000 – Electrical connection
$8,000 – Installation of cooling/heating system
Total Cost: $98,000
Reflections on the Project
Originally the Wild Work Farm team started planning a large barn project, but it got expensive really quickly and would be a large investment into land they don’t own since the farm operates on leased land from extended family.
Instead, they started exploring a more versatile construction project it ever needed to be used for something other than vegetable farming. The thought was: pretty much everyone can benefit from a concrete slab under a roof, and the shipping container could be sold off or moved in the future. The location of this structure was placed in an unused area of the farm so it didn’t impact the existing infrastructure.
Lissa was glad to have hired out this project so she could focus on the farm and let someone else do it who had the tools, know-how, and time.
This space is efficient, and easy to keep clean, it has good lighting and makes it easy to sort produce properly.
It’s nice to be able to work outside, yet be protected from the elements. They have been mindful of bird activity, but it hasn’t been a problem.
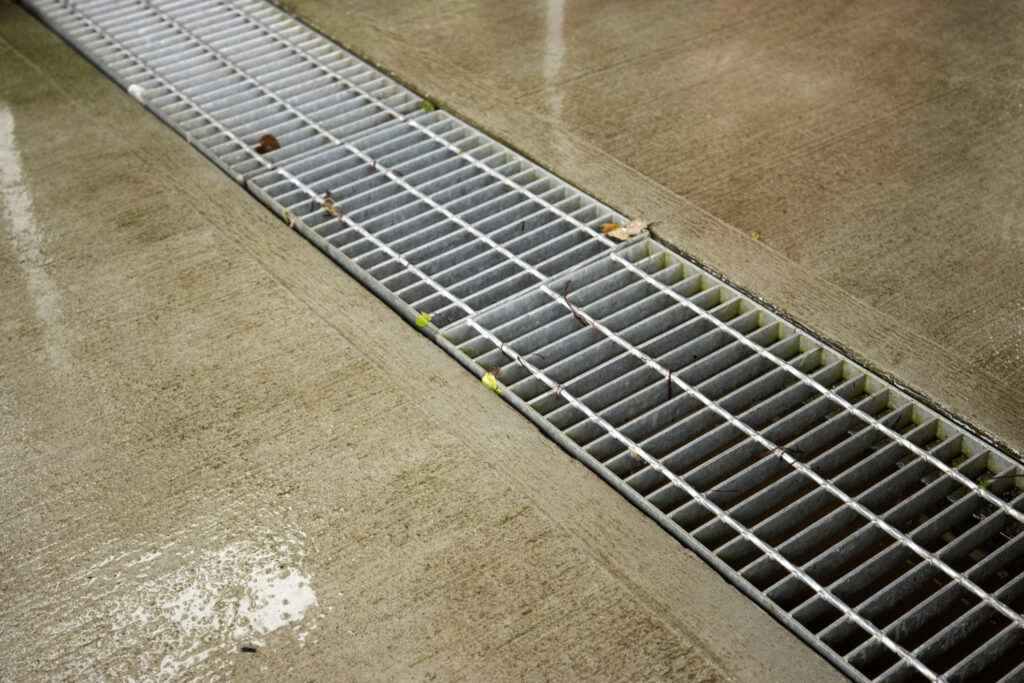
One thing that could have been changed was that the concrete is broom finished, which makes it hard to sweep salad greens off the floor. In hindsight, they think they would have preferred a trowel finish. But this was a trade off between easy to clean and a non-slip surface, and considering it was regularly going to be wet they opted for the anti-slip texture.
This space made production way more efficient, “we harvest, pack, and deliver on the same day, early afternoon.” It’s also increased capacity & sales by being able to handle more winter production. They now use the old cooler for storage crops or tomatoes, and can easily move a lot more produce. Speaking of winter months, a huge morale booster was having hot water available when the outside temperatures started dropping!
Another area that could have been done differently, would have been to have a space that was a little more weather resistant. The drain from the wash/pack can freeze in the winter months, and they have to blow out the lines to keep them from freezing and bursting. A better bin drying system is the next thing that they’d like to find a solution for.
Employee retention is hard on vegetable farms, but the crew here enjoys the new space and reflects that it is easy to talk to people and move around. It’s “a positive work environment” since it is organized, clean, and continuously improving.
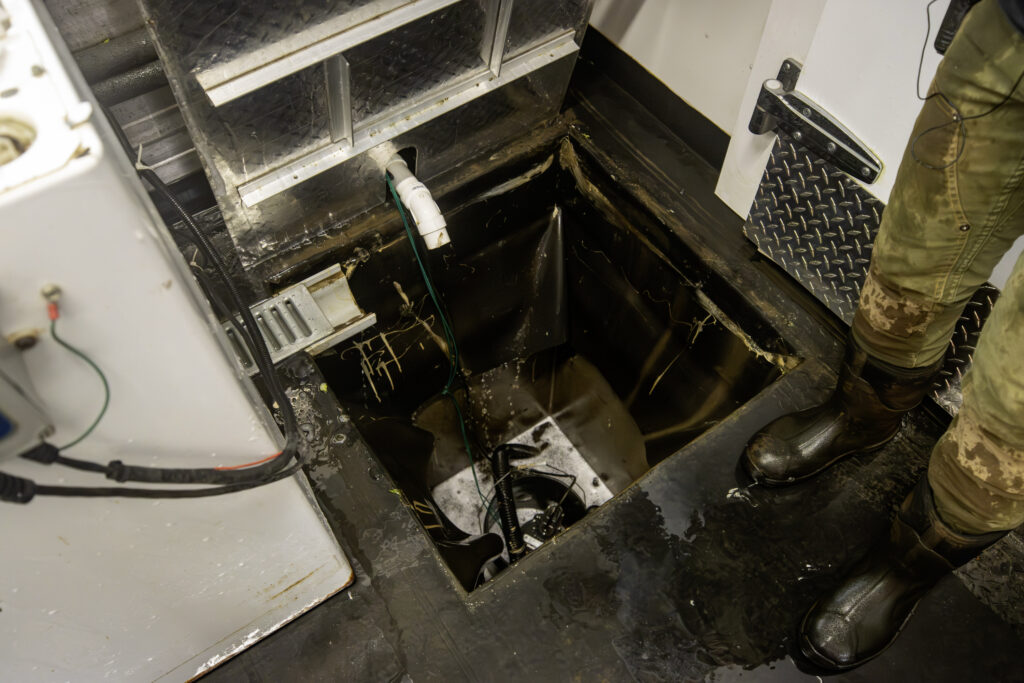
Virtual Tour
Click around and view this project in an immersive experience!
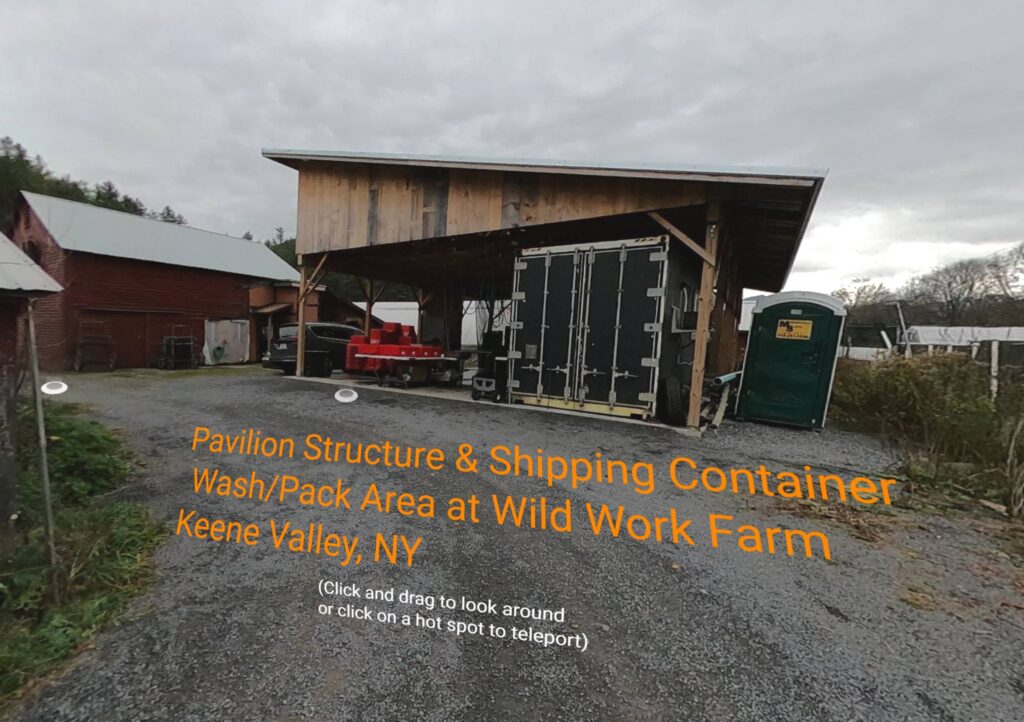
Watch The Interview
Share this post!
Looking for More?
We have additional post harvest case studies of various renovations and new builds that can be seen here. go.uvm.edu/phcs
All things post harvest covers individual blog posts discussing building features, equipment, and other PDF guides.
Acknowledgements
This case study is possible because of the hard work, wisdom, and generosity of Lissa Goldstein of Wild Work Farm. Without her willingness to take the project on to begin with, deal with all the challenges that such projects bring, and complete it we would have nothing to share. We are grateful for her willingness to share the story and knowledge in this form so that others can learn.