
A video version of this case study is available here and a printable PDF is available here.
Jill Kopel owns and operates New Leaf Organics in Bristol, Vermont and has over 19 years of farming experience. After many years of growing crops and growing the business she made the decision to invest significantly in her wash/pack space to improve many aspects of the farm.
About New Leaf Organics
- Grows a variety of vegetables and flowers from A-Z for CSA customers and wedding floral arrangements
- Total of 5.5 acres growing area
- The farm business grosses about $250k
- 80% Retail/20% Wholesale
- Retail sales are to CSA members and Farmers Markets
- Major Crops include bunched greens, garlic, onions, berries, herbs etc.
- The cost of this renovation was ~$90,000 Project
Goals of the Project
Jill had many goals for this project. She wanted to make use of existing infrastructure on site as opposed to building another shed or barn. Doing so meant taking action to preserve the existing barn, and protecting it to keep it in good condition. One part of this was preventing additional damage due to excess water, etc.
A big part of the project was increasing the light in the space. Energy efficient LED lighting was installed and windows were added to let in additional natural light. This improved the comfort of the space and allowed improved visual inspection of products which is important for both flowers and vegetables.
“It’s a pretty dark, dank dairy barn that no one really wants to hang out in downstairs, so we are really looking to bring light into the space for sure.”
Jill Kopel
Renovating the existing dairy barn was intended to expand the space for dedicated tasks. Designated areas for specific tasks was desired to allow the implementation of more efficient systems and to improve produce safety.
This project also improved flow. Careful thought and planning was focused on the flow of people and product. This meant expanding the driveway and parking area. It also meant including a space outside for washing root crops and containers in addition to inside the barn.
About the Project
The major stages of this project were completed over the winter. “That brings its own challenges!” Jill noted, referring to the narrow window that exists to have the space usable by the growing season. The demolition included cleaning out the bottom of the barn where the renovation was taking place. Tearing down part of an attached shed, and jack hammering out the old, broken concrete floor. By removing the majority of the old floor, Jill gained ceiling height. This made the space easier to work with and provided a fresh start to a smooth floor that could be sloped to a drain.
The renovation included insulating the ceilings and walk-in coolers with spray foam, and installing blue board and batt insulation in the walls. Adding insulation makes heating the space when it’s cold out more efficient which makes it a more enjoyable place to work.
One aspect that makes this project unique is that Jill leases part of the space to a local catering business. Sharing this space with another woman-owned business with a similar mission around local organic food has been a great partnership. Getting the space certified added additional cost to the project, but having steady income from the lease helps to cover some of the overhead from the renovations and opens the opportunity to process produce from the farm as well. Jill shares that this has been a really strong win but also one of the biggest hurdles of the project.
Not only is this space used for vegetable wash/pack, flower arranging, two walk-in coolers, and catering but it’s set up to host floral workshops, and has a large table for meeting with clients. Something as simple as having a desk and a place to sit with the crew or clients was something that didn’t exist on the farm before and helps take the work off of the kitchen table and keeps produce out of the garage.
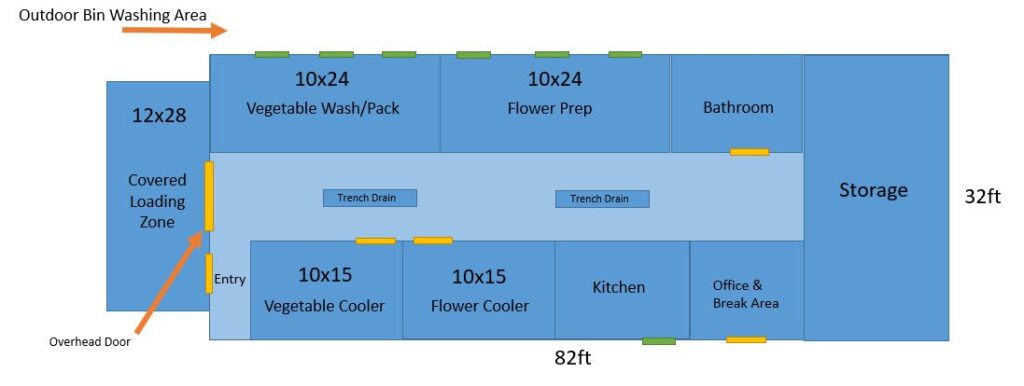
Cost
The cost of the project was about ninety thousand dollars ($90k). This included removing old concrete, pouring new concrete, insulating, plumbing, heating, electrical, finish surfaces and contractor labor to do the majority of the work.
Jill chose to hire out most of the construction for her project and worked with one general contractor to communicate with all the sub contractors. This simplified the project for her and kept the project moving on an aggressive timeline over the winter to be ready to go in the spring.
She received estimates from four different contractors for the project and chose accordingly. Two estimates were able to be dropped quickly as those contractors were coming from high-end home construction, were relatively high estimates, and Jill felt the contractors weren’t a good fit for the unique needs of the project.
Flow
One of the major goals of the project was to improve the overall flow. This includes the flow of produce as well as people and vehicles. A new parking area has been established and a drive path around the barn now streamlines CSA pick-ups. The farm has a space to park farm vehicles and CSA customers have a separate space to park which makes vehicle flow more clear for everyone.
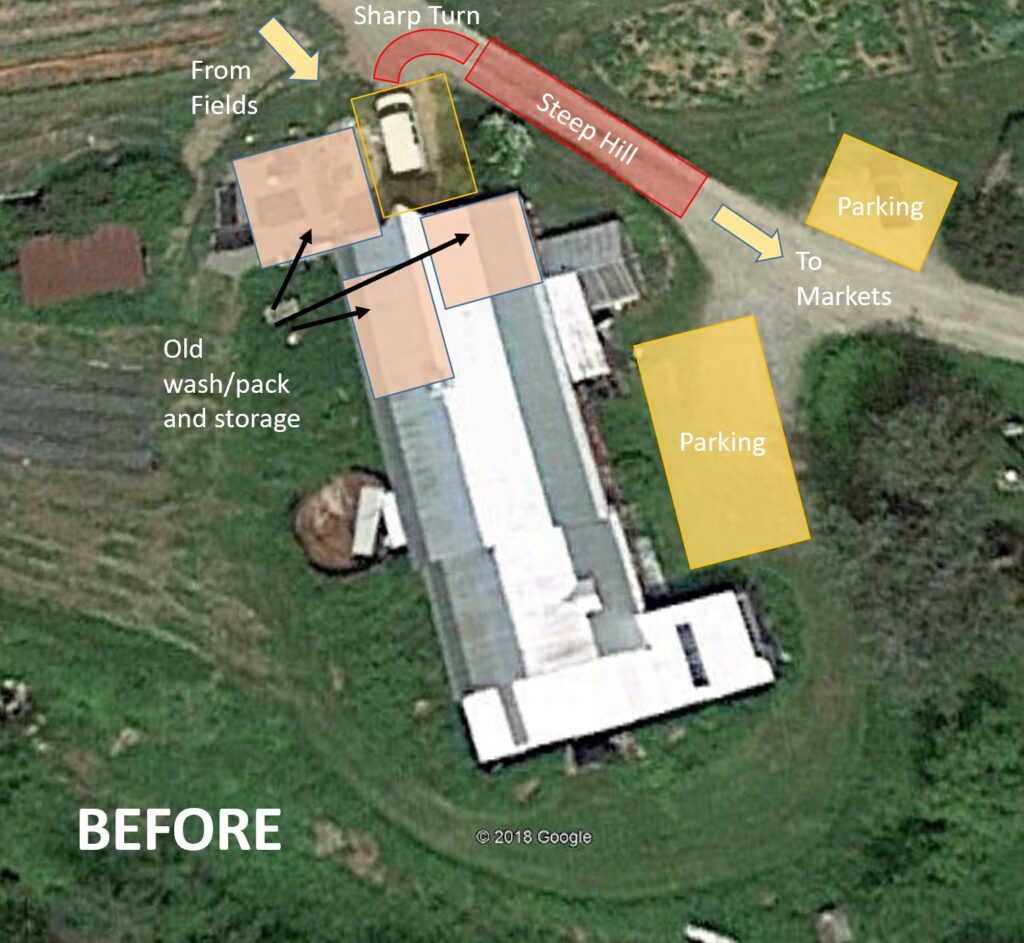
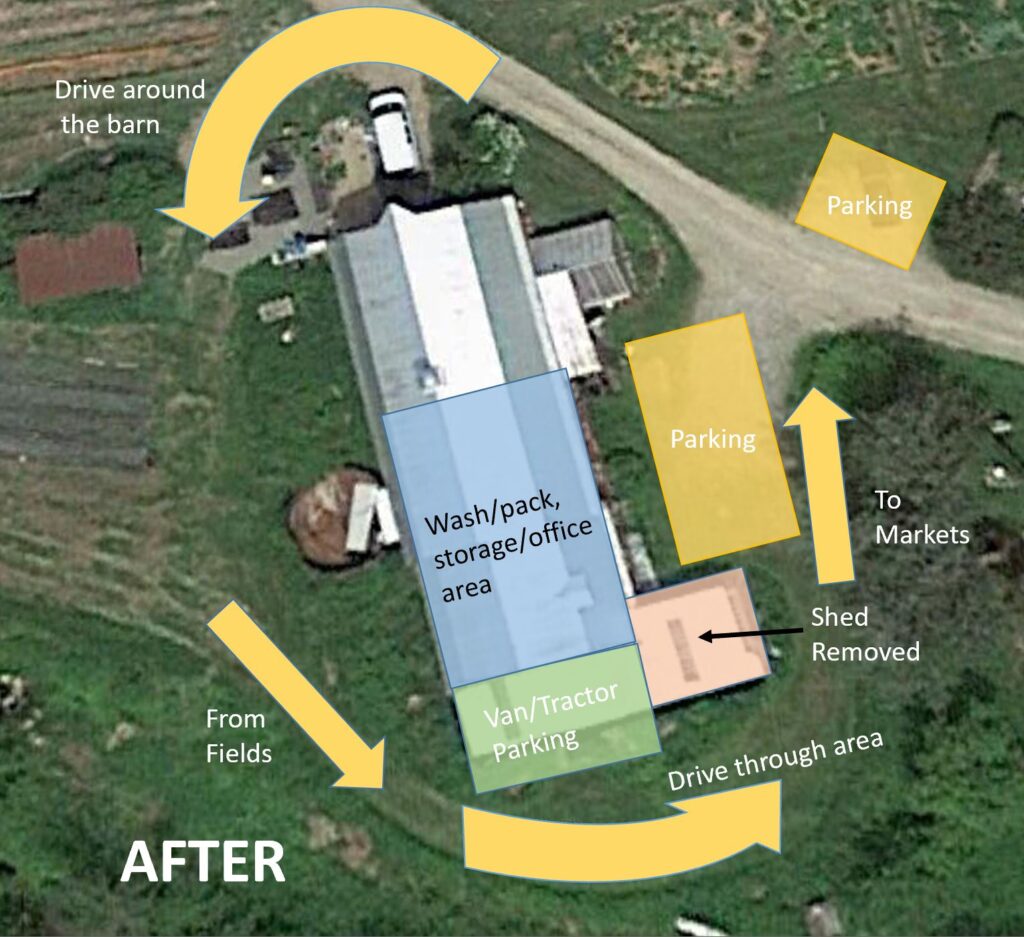
Best Decisions
There are a lot of decisions that Jill is happy to have implemented in her new space. One was having both a people door and an overhead door. Allowing her and her crew to either open up the space when it is nice outside or keep it closed when it’s not. Having an overhead door also makes it easy to move and store larger equipment in the off season.
The plumbing work resulted in both cold and hot water both inside and outside. This is a minor detail with big impact, resulting in warmer hands and better cleaning while spraying produce or cleaning bins.
Not only was a bathroom built in the barn but it features a shower too. Handy for employees heading straight from work to another activity.
One area that often gets overlooked in packsheds is having plenty of storage space for supplies and materials. One end of the bottom of the barn is dedicated to material storage. It’s behind two large doors and is not heated but stays dry and remains easily accessible. It saves a lot of time and effort when the materials don’t need to be brought up or down stairs.
Jill has implemented a low budget U-Boat using a wire rack on wheels with the middle shelves removed. After washing produce, they pack into boxes right onto wire racks for wholesale orders then roll them right into the cooler. At that point it’s ready to go out to the delivery when it’s time. “It’s really minimized our box handling a ton.” Jill notes. This improvement was very inexpensive and has made a huge impact in efficiency and labor. The extra shelves that aren’t used on the cart are refashioned as spray benches outside. These benches are hung by chains under the roof outside keeping a lot of the mud outside which saves the step of cleaning the barn floor. These spray tables work great for heavily soiled crops like carrots and beets.
“I’m really happy with the drainage … [inside the building] … It really works well”
“Having a roof covering the loading area has been awesome,” Jill reports. Getting out of the sun or the rain while moving product between vehicles and the barn is one of the improvements that makes the daily work more comfortable and efficient.
When asked what she’s most pleased with Jill responded, “Overall it’s been positive all around. I don’t really have any complaints!” One issue she highlighted though was humidity control has been a challenge and noted that some mold was showing up around the cooler doors. Air sealing coolers, and including ventilation and air circulation are important for drying out the space. Jill installed energy efficient heat pumps, so not only will these provide heat to the space but can be used as dehumidifiers in the summertime to help reduce humidity in the space.
Jill believes that these upgrades will provide financial benefit going forward for example keeping an employee longer into the winter season to improve retention. She will also be able to host more workshops with the larger space, add value-added products with a dedicated areas, and extend the CSA with large walk-in coolers.
This dedicated wash pack space has also allowed her to create better systems and helps with employee training. It’s a lot more pleasant to have a space for the small things including having a place to sit down, heat up lunch, wash hands with hot water, and go to the bathroom. This all makes the work more comfortable and enjoyable. These are morale boosting improvements that are hard to put a value on.
What does it take to have a certified kitchen? Jill started by asking peers first. The process can be complex and time consuming since it involves discussions with a variety of authorities. In Jill’s case, she needed to work through plans with The Vermont Agency of Agriculture, Food, and Markets, the Vermont Department of Health, Vermont Agency of Natural Resources,, and The Vermont Division of Fire Safety.
Contributors to the Project
Funding for this project was provided by the Vermont Farm Fund and FSA loans. Both of these were not as challenging as traditional banking would have been for a project like this.
Additional funding was provided by a Vermont Agency of Agriculture, Food and Markets Produce Safety Improvement Grant and Local Food Market Development Grant.
UVM Extension’s Ag Engineering & Produce Safety Team helped in the planning of the renovation.
See the Interview and Tour The Barn
The videos in the playlist are:
- New Leaf Organics: Post Harvest Case Study Intro
- Challenges with the Existing Wash Pack
- Dreaming Up The New Packshed
- A Walking Tour of the Packshed
- Outdoor Flow and Efficiency Around the Barn
- Details of the Packshed Renovation Project
- Packshed Improvements That are Hard to Place a Dollar Value On
Acknowledgements
This case study is possible because of the hard work, wisdom, and generosity of Jill Kopel at New Leaf Organics. Without their willingness to take the project on to begin with, deal with all the challenges that such projects bring, and complete it we would have nothing to share. We are grateful to them for their willingness to share their story and knowledge in this form so that others can learn.
Funding for this publication was made possible, in part, the USDA Northeast Sustainable Agriculture Research and Education program through award LNE19-375, by the Food and Drug Administration through The Vermont Agency of Agriculture Food and Markets via the Integrated Extension Educational Programming in Support of the VAAFM Produce Program Grant 02200-FSMA-2018-01. The views expressed in the publication do not necessarily reflect the official policies of the U.S. Department of Health and Human Services or the Vermont Agency of Agriculture; nor does any mention of trade names, commercial practices, or organization imply endorsement by the United States Government or the State of Vermont.