Farming requires lots of space. Space to grow vegetables, conditioned space to store harvested produce, and a secure space to house tools out of the weather. Barns and tool sheds can be expensive, and building takes time. If you’re farming on rented land, it’s even harder to justify the investment in a permanent building. Shipping containers have become a popular option for an “off the shelf” solution to fill some of these special needs. They are relatively affordable and portable and can be an easy, modular option for some protected space on the farm.
Shipping containers have a shelf life before they no longer meet specifications for hauling freight across the ocean, but have plenty of life left for general use. After they are decommissioned from their travels they are sold off for auxiliary uses.
Farms have found that they are a fairly inexpensive solution for tool storage, coolers or as a blank structural shell to be built out as a wash/pack or office space.
Below are examples from farms showcasing how they have implemented their use in agriculture.
Table of Contents
Use As Storage
Use as Coolers
Use as Wash/Pack
Purchase Locations
Use As Storage
The simplest use for a container is for storage or as an equipment shed.
Truly Living Well – Atlanta
Truly Living Well, an urban Farm in Atlanta, GA, uses shipping containers as a security measure. They needed a tool shed, and a space to store supplies that they can lock-up when they aren’t supervised, otherwise tools seemed to walk off the farm all too often.
Patchwork City Farm – Atlanta
Patchwork City Farms, an urban farm in Atlanta, GA, uses shipping containers as walls for their wash/pack space. They also provide a secure location for their farm tools and supplies that can be easily locked up.
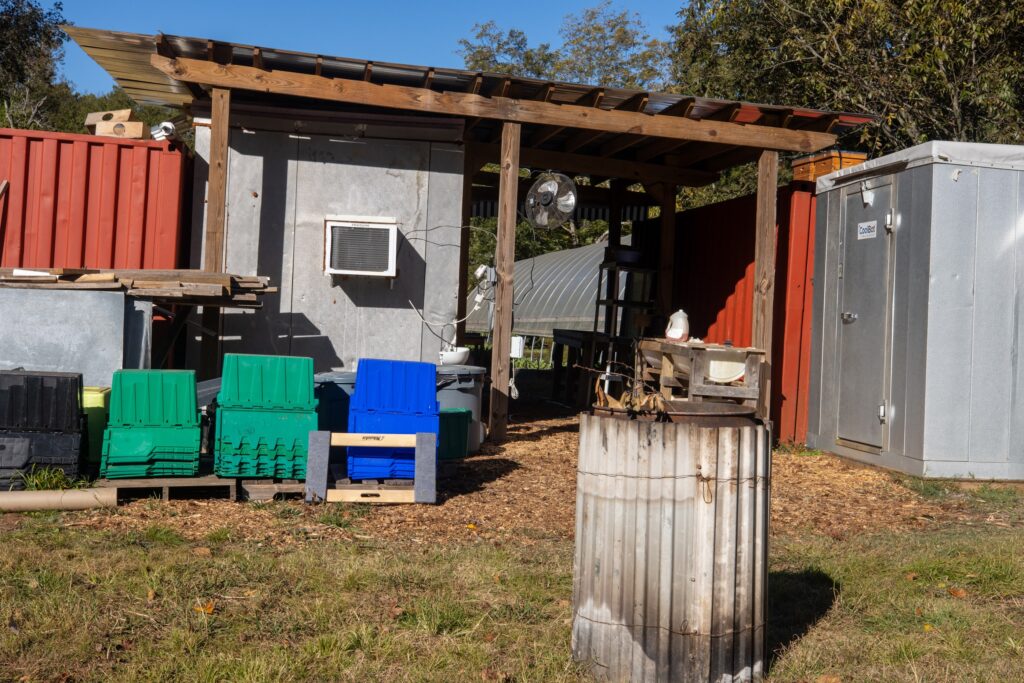
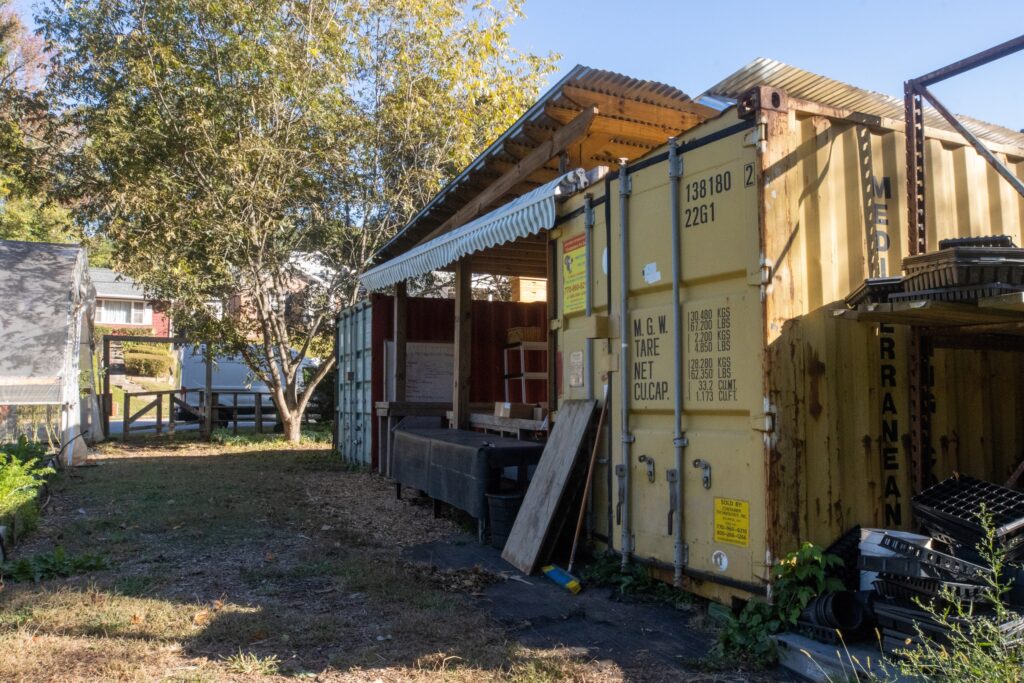
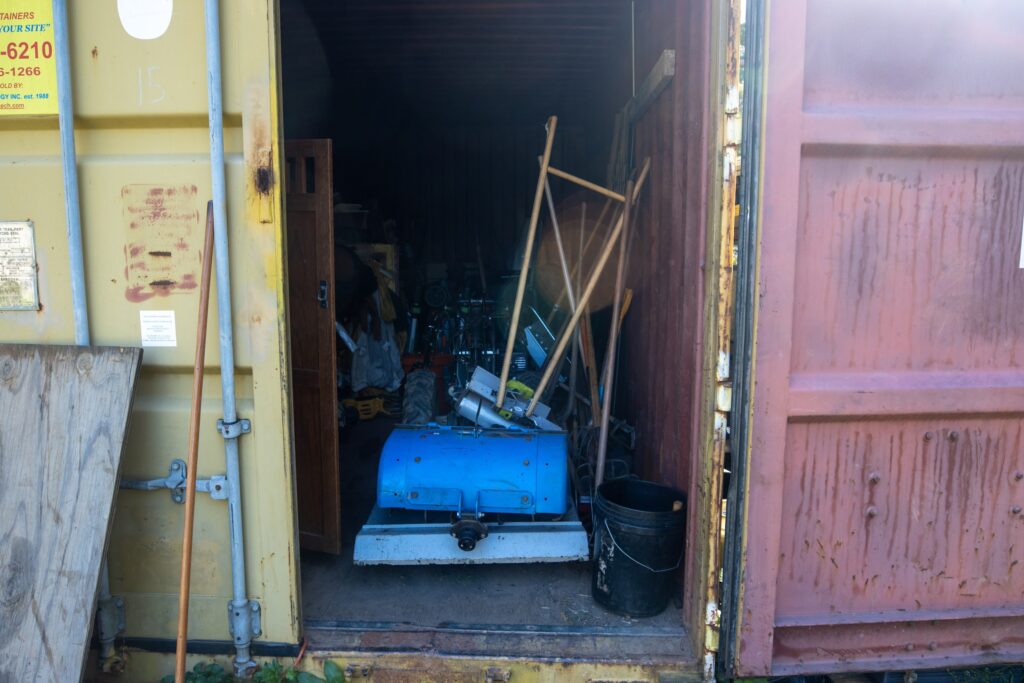
Vermont Youth Conservation Corps
Whether in a rural or urban location, shipping containers are useful for a weather-tight storage solution on farms like this one at the Vermont Youth Conservation Corps Farm
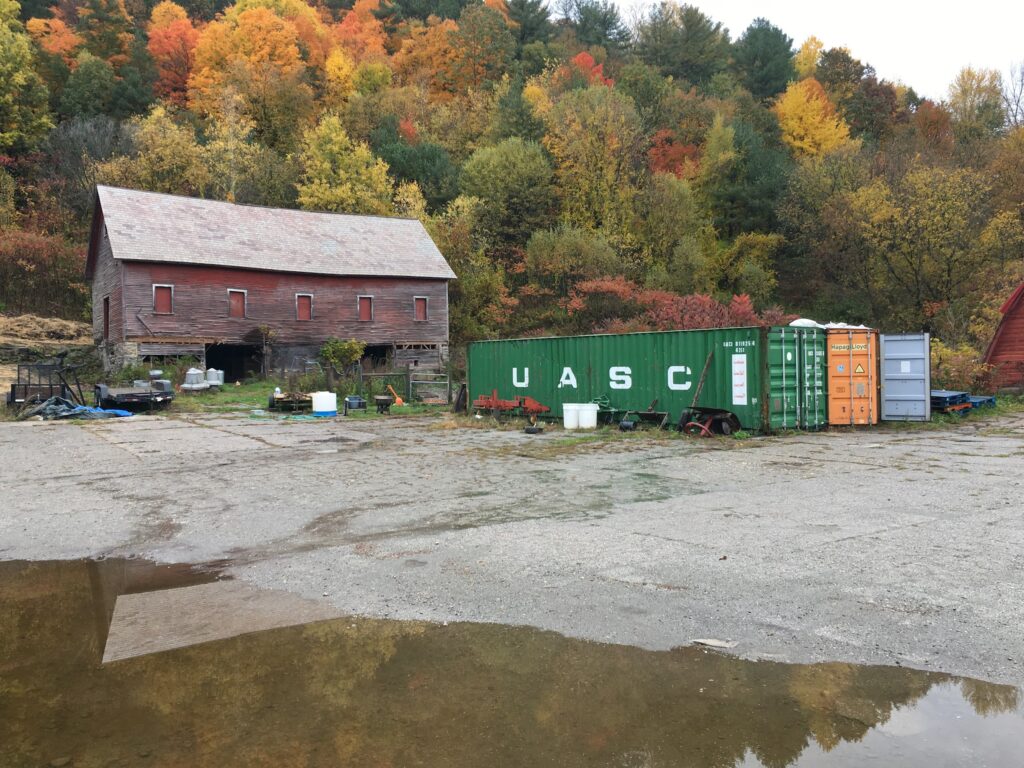
Use as Coolers
Shipping containers make great coolers. Being weather sealed and rodent proof it’s great protection for your crops. You can custom frame in insulated walls, but it is tricky combining wood with steel, especially due to the corrugated surface of the container. Some shipping containers are built as insulated, refrigerated boxes. These can be a great way of getting quick insulated storage areas.
The existing refrigeration systems on these are generally 3 phase (5 pole) 400 VAC power. Off the ship, this is most often provided by ‘portable’ reefer power packs (diesel generators) designed for the job. These are also available on the used market. But, now you’re getting into more of a project perhaps. Used units are typically most available in and near ports.
Most growers adapt insulated shipping containers to their new on-land use by converting the cooling system to 110 or 220 VAC split refrigeration systems. Others have good luck cutting holes in the shell and installing a CoolBot system.
A container measuring 8’x8’x20’ is certainly doable with a CoolBot or perhaps 2, especially for winter storage. Using our heating/cooling load calculator and assuming R28 (common in reefer containers) with an inside temp of 34 °F and an outside temp of 87°F with minimal door openings, it should only take 2,500 BTU/hr, well within the range of a 24,000 BTU/hr CoolBotted AC. Consider a heater for freeze protection as well. There are some companies who have started a rental business specifically aimed at temporary cold storage (NJ) and also CT. I’m not sure of the cost differences, but a drop-in solution sounds tempting as the day length increases.
Another option besides a shipping container is a Reefer Truck or even just the reefer box from a truck. These refrigeration systems are sized for “keeping things cold” not “making things cold.” The boxes are minimally insulated and the refrigeration systems are designed for low loads. The refrigeration systems also seem to be notoriously unreliable, especially on the used market. It could work for a short-term, temporary solution, but could also become a maintenance and baby-sitting headache. Many farms have experience using these during their storage transitions. Reefer trucks are often for sale more than they are in demand.
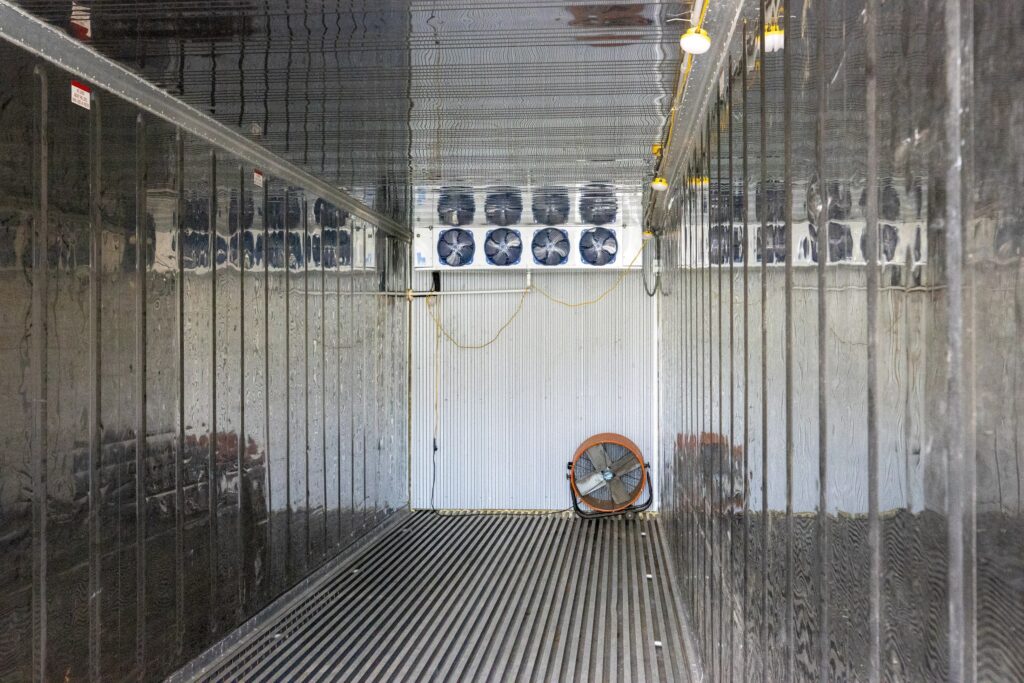
The use of either a trailer body or a shipping container will limit your easy use/access if using full pallets. They’re, of course, designed to be filled completely and emptied by the pallet load in a last-in, first out (LIFO) system.
Use as Wash/Pack
Ascutney Harvest
Lauren Mucha and Oliver Owen of Ascutney Harvest went the extra mile retrofitting a shipping container as a wash pack space. They built in a custom cooler in the end, painted it inside and out, installed good lighting, a study floor, and a stainless sink and tables for washing produce.
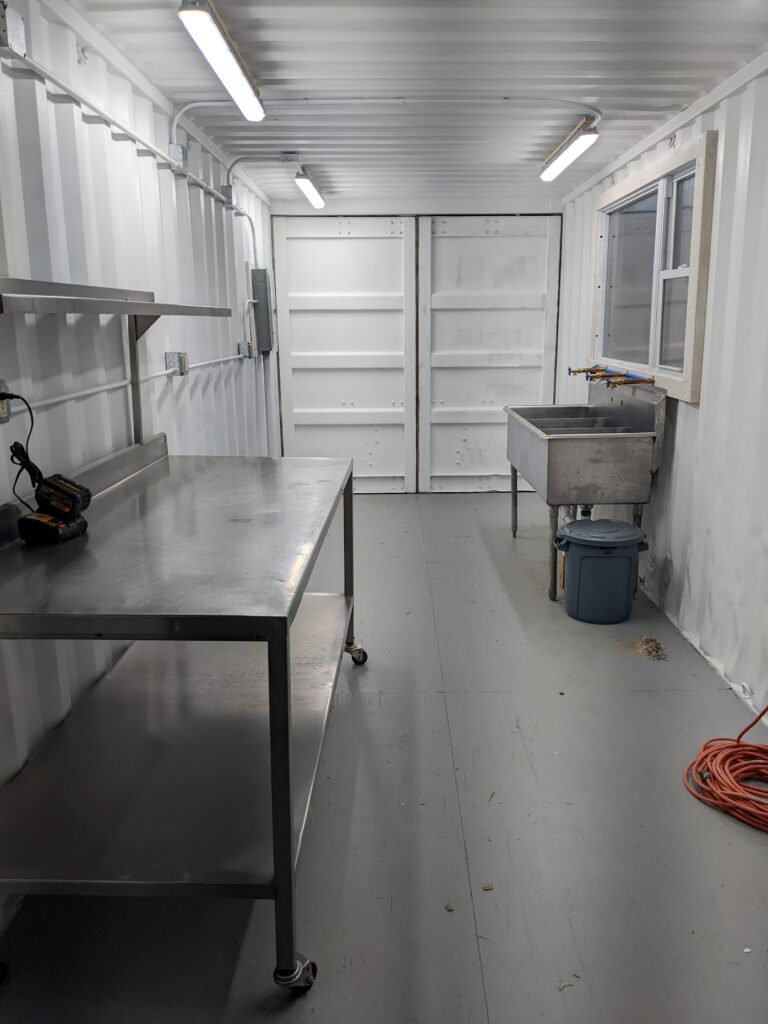
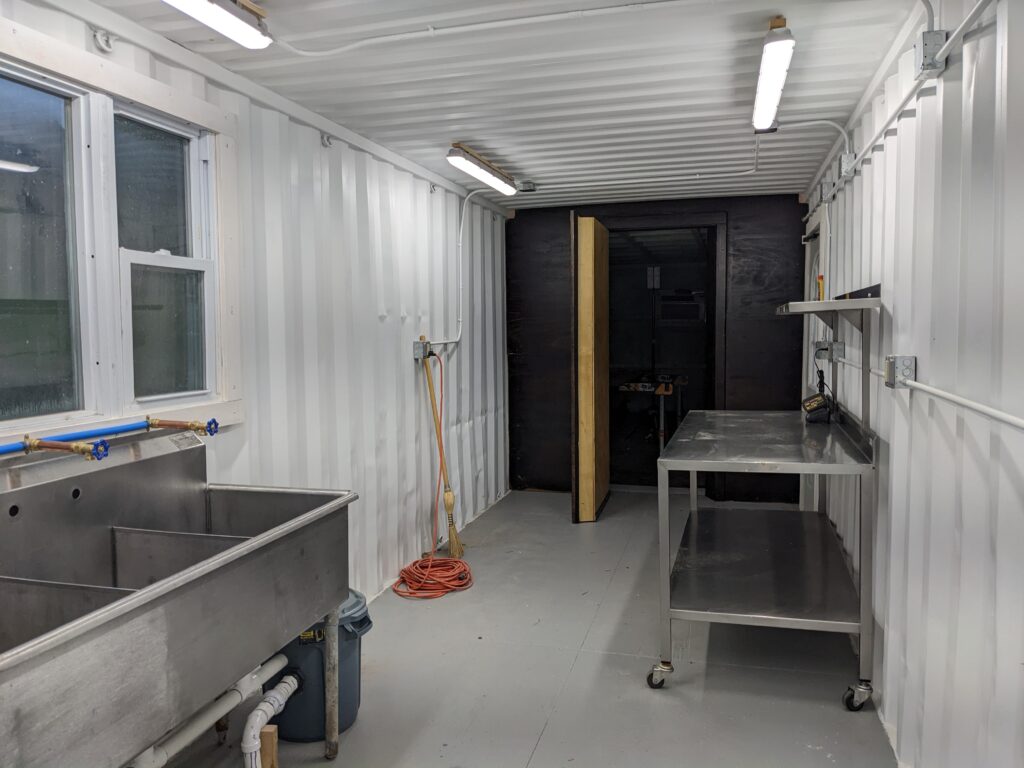
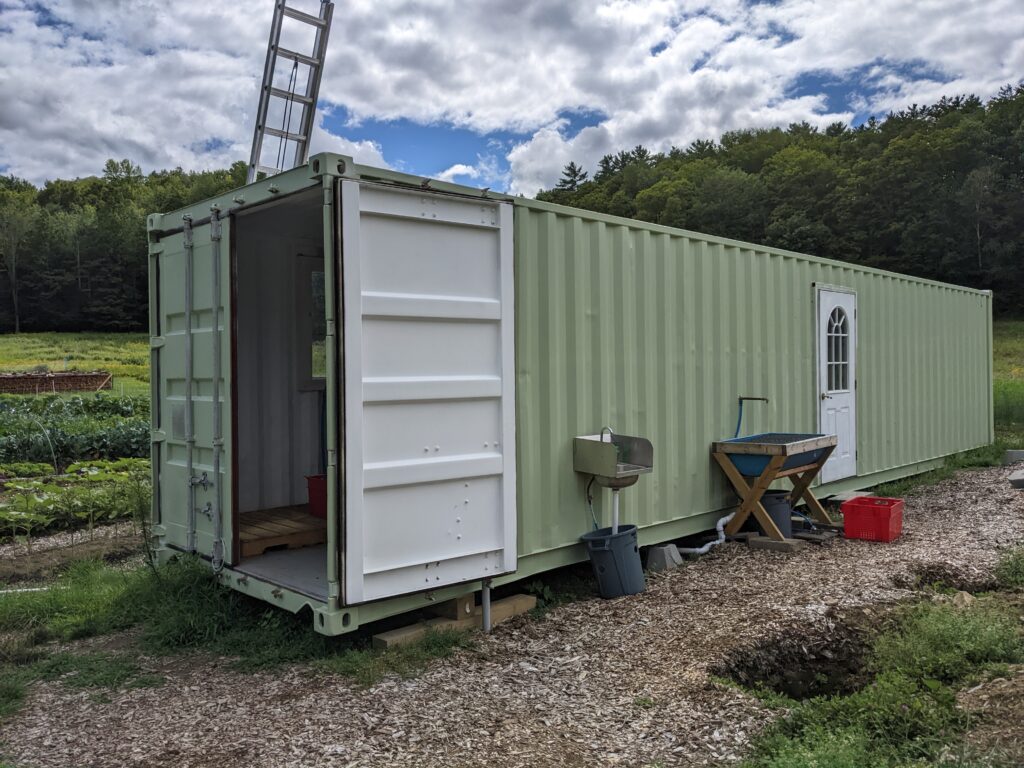
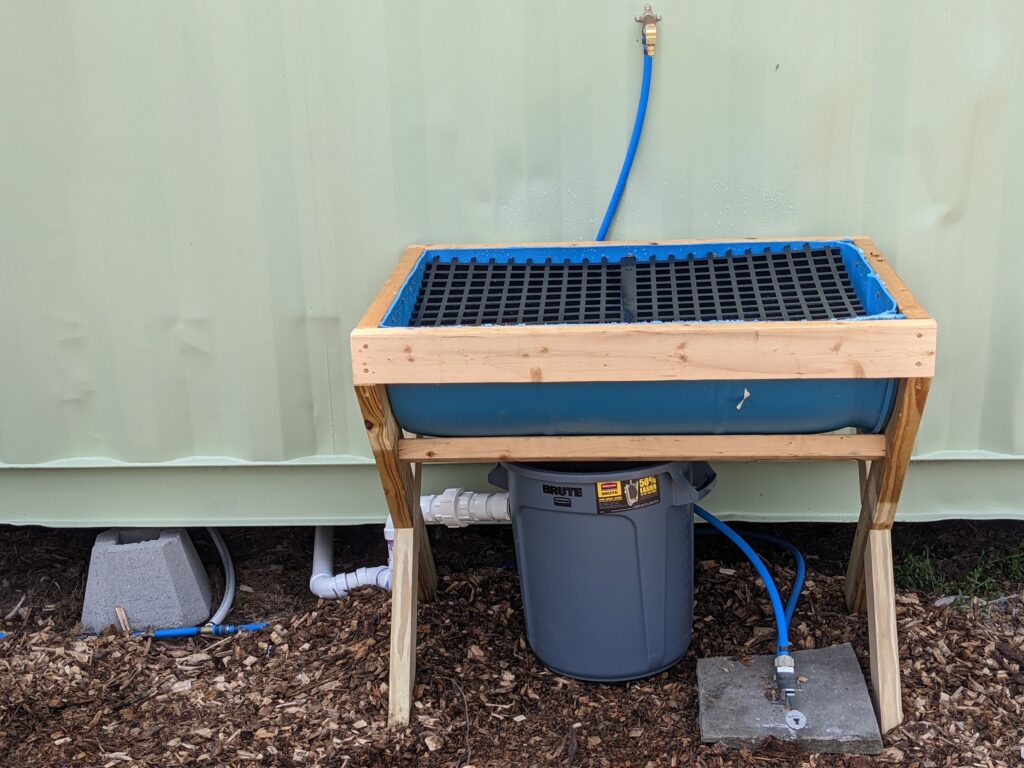
Nettie Fox Farm
Nettie Fox Farm (Newburgh, ME) uses an insulated shipping container as the center-point of their wash pack. They built a small room on one end that serves as sealed storage for seed and supplies. They framed in a side entrance door for their main cooler access which makes daily entrance simple.
Next to the cooler they poured a slab, with a trench drain and loading dock. The shipping container will act as support for an office and storage space above once stairs get added on to make entrance accessible. On the other side of the building they have a south facing propagation house which also gets used for curing storage crops in the fall.
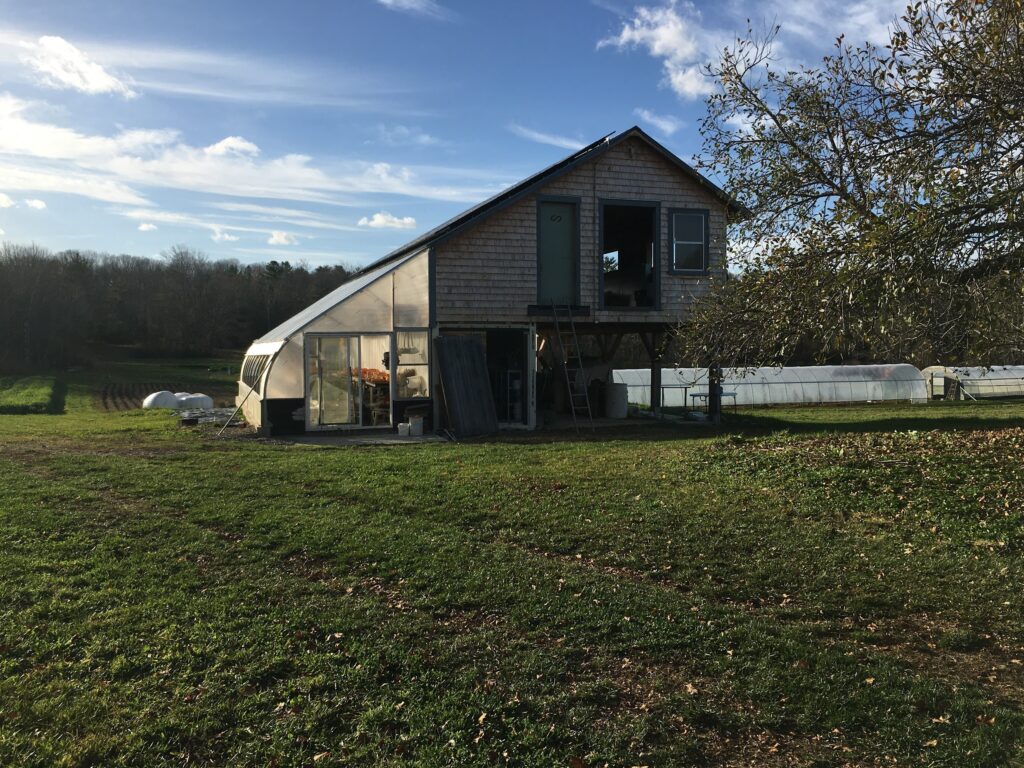
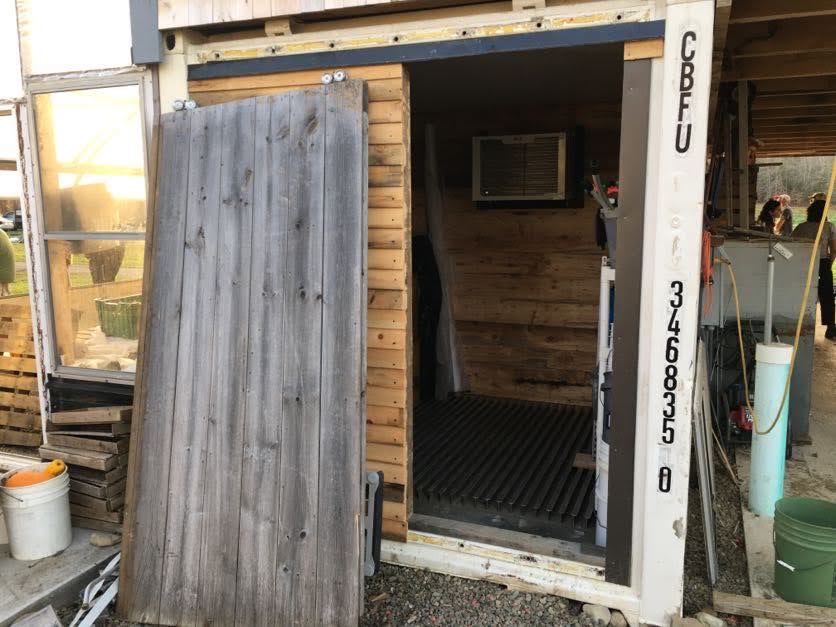
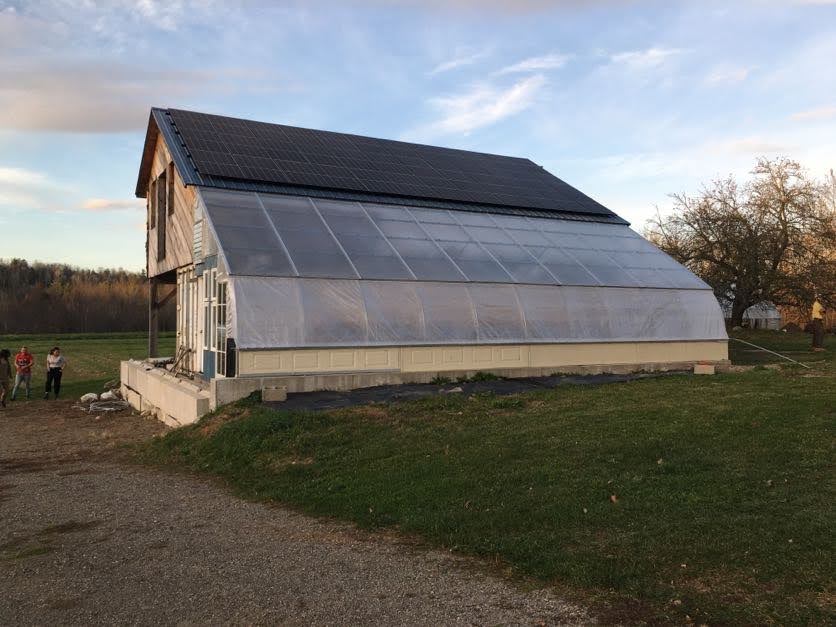
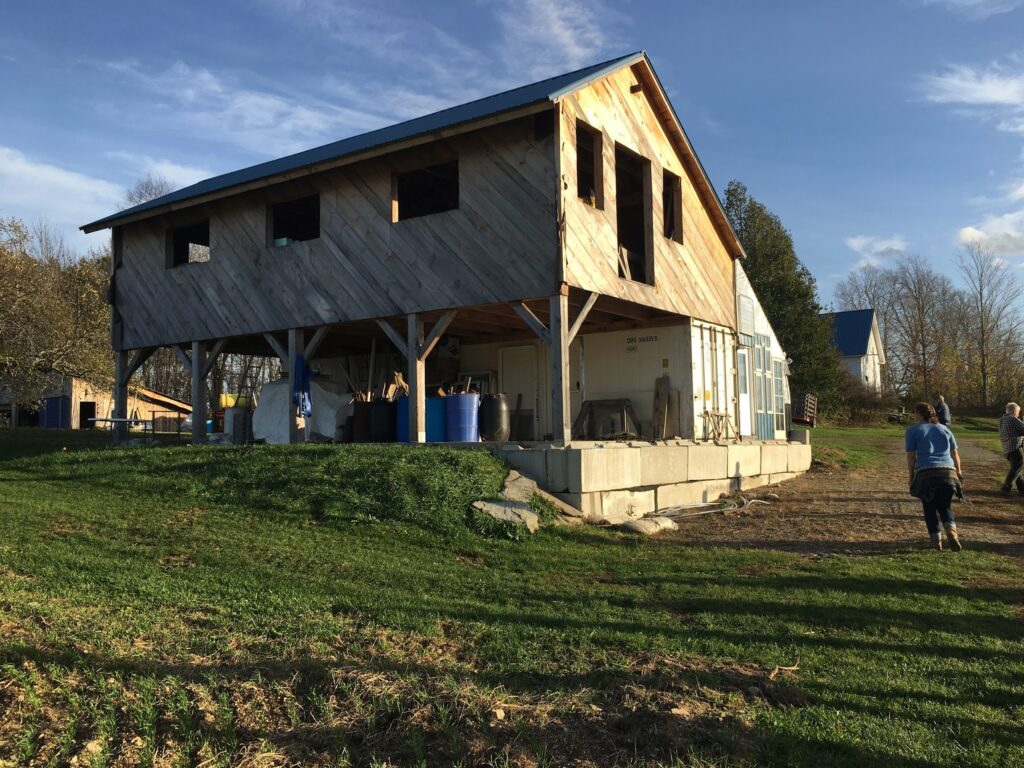
Wild Work Farm
Wild Work Farm (Keene Valley, NY) built a new wash/pack in 2020/2021. They had some specific needs and restrictions, so they ended up pouring a 30’ x 40’ concrete slab with reinforced edges, trench drain and built-in sump pit. They included a retrofitted 8’ x 40’ insulated shipping container on one edge of the pad and built a monoplane roof over the whole thing, which provided them with both outdoor and indoor washing space and a cooler. It’s not huge, but it works for them and is moveable and relatively flood proof (important on our leased, flood-prone land). The interior walls of the shipping container are stainless steel so they are easily washable and the floor inside was built up and pitched to drain into the in-ground sump-pit.
Costs:
Site Prep (included installation of new driveway for access, main electrical and plumbing lines, and connection to drainage): $10,000
Concrete slab: $8,000
Roof: $30,000
Retrofitted container: $40,000 (Gradients LLC based out of Plattsburgh NY)
Electrical connection: $2,000
Installation of cooling/heating system: $8,000
The shipping container has been converted to be used partially for cold storage and partially as a conditioned wash/pack space. It’s a 40′ container which encloses ~8’ office space, 20’ wash/pack, and 10’ cooler space.
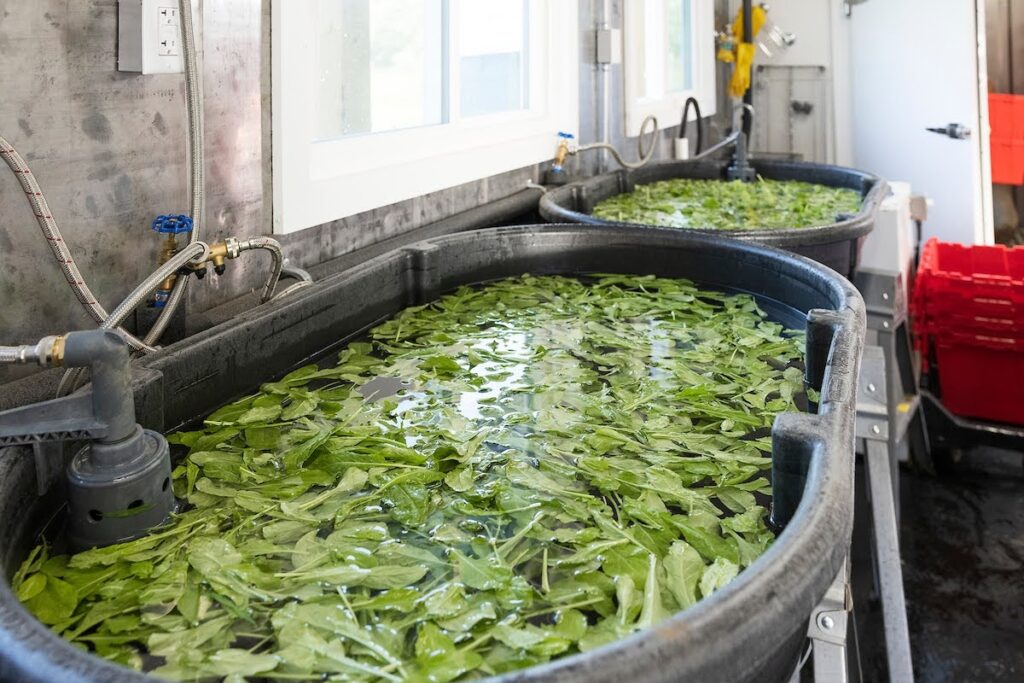
Special features:
- The floor has been modified to drain into a sump pit that then gets pumped out.
- It’s a converted refrigerated container (so came insulated and with stainless steel wall finish), but we decommissioned it and installed more traditional cooling/heating systems. Wash/pack area is heated with a mini split and the cooler is cooled using a compressor and fans.
- Has a small propane water heater and handwashing sink which is nice in the winter!
The cooler is used as our 33 °F degree space year round and the inside is our greens line year round. They don’t generally wash roots in the winter as they store them clean. They have a separate storage space for 55 °F low humidity crops.
It is a small space and doesn’t work with moving large volumes on pallets, however it is a good option for those with small operations especially with other considerations. For this farm, leased land and a flood prone site were two good reasons not to build a more traditional structure.
Roxbury Farm
Roxbury Farm (Kinderhook, NY) has three 40’ shipping containers that came insulated. They are a little over 8’ wide inside and tall enough to stack 3 macrobins with space above them. They also have one 20’ insulated shipping container. All of them sit outside.
Container 1: 8’x40’ – Cold Storage
- Purchased in 2017 for $9,000 from Kelley Container in CT with refrigeration installed
Container 2: 8’x40’ – Cold Storage
- Purchased in 2017 for $9,000 from Kelley Container in CT with refrigeration installed
Container 3: 8’x40’ – Warm or Cold Storage
- Purchased in 2019 for $5,000
- Self installed coolbot-powered mini-split for ~$2,500
- Has a dehumidifier with a drain out the back
- Used for winter squash unless additional cold storage is needed
Container 4: 8’x20’ – Freezer
- Purchased in 2020 for $5,000 plus $1000 in repairs, site prep, and power
- Used as a meat freezer
They bought the two 40’ containers from Kelley Container in CT. The seller installed the cooler systems. If they were to do it again, they would have their cooler person install the coolers and just buy the container. The seller installed all the controls inside in the back of the container. So the farm had to rewire the control box and thermostat to the outside. The farm will fill them full of macro bins so they can’t get to the back once it’s full. They installed the cool bot in the 3rd container. They purchased the 20’ freezer from another farmer.
They ran the power and had the cooler contractors do the final hook up. They love it mostly and reflect that they are quick to install, rodent proof, durable, and… ugly… but they can live with that. They use them for root crops and storage crops. They have two other walk-in coolers for day to day use. They note that doors are a struggle and it’s hard to open those buggers. They have to use ramps to get in and out with the forklift. They also use hand carts but those are heavy to move. The ramps sometimes fly out from underneath the forklift so they made straps attached to the ramps that they clip onto the floor of the container with carabiners. Filling it with macrobins means you sometimes have to empty the whole thing out to get to the item you want. Or to do the last in, first out (LIFO) arrangement if you harvest over the course of a few weeks.
A clipboard lives in the forklift to constantly draw new maps of where things are in the cooler. In the winter they have to plan ahead shuffling things around on days that are above freezing temperatures. Using a pallet jack inside can be difficult, as it tends to get caught on the floor. It is also dark in there so if you were doing daily distribution installing lights would be a good idea. However, if you are forklifting in there it’s pretty tight so light fixtures might get in the way depending on how low profile they are. On that note, measure your forklift and the pallet bins you plan to use to make sure they fit as intended.
Final Thoughts
Make sure the site is level and plan on concrete pads under the front and back if using a forklift. Roxbury Farm had the 40’ containers installed on packed gravel but one container sunk and they couldn’t close it anymore (unless they lifted one front corner with the forklift). This was addressed by adding 10’ wide pads in the front and back for the containers to sit on. The freezer sits on treated 6’ x 6’ beams as don’t use that one with a forklift or carts.
Another consideration is to make sure there is enough space for the delivery truck to back up to the container and in and out of the driveway. Without the space to maneuver comfortably they ended up having to get creative with the tractor maneuvers to get the containers in place.
They plan to cut a human door into the freezer container to make it easier to get in and out of and if they were using a container as a walk in cooler on the regular they would want a different style door. The container they originally purchased had a 3 phase reefer unit that they used on the cargo ships. They bought a converter to change it to single phase power and that cost a ton in electricity. The reefer unit did prevent the coolers from ever going below the temperature we set so crops never froze in the winter. It may have been more cost effective if they had 3 phase power on the farm, but that also comes at a cost! Also their refrigeration contractor didn’t want to work on that reefer unit which was difficult. They would like to install some sort of air exchange system, right now they just crack open the doors. All in all they are happy with the containers as coolers.
Crossmolina Farm
Crossmolina Farm (West Corinth, VT) has a reefer truck that they use as a root cellar in the winter months. It was supposed to be a temporary solution but they are using it for another winter due to issues with delivery and installation of a walk-in freezer that will be attached to their self-built CoolBot. The existing CoolBot does pretty well in the summer but it is harder to keep from freezing in the winter.
They can run the cooling unit if it gets too hot in the fall but they mainly heat it with a space heater on a thermostatic plug. It doesn’t need to run very often and stays right around 40 °F most of the time.
They bought the reefer truck from another farm in 2021 and it was an easy purchase for $10,000. They drove it home from where they bought it, parked it at the new pack shed and were up and running! It can even be driven right into the field to pick up root crops!
They hope to complete the new CoolBot this spring and then transition out of the truck and sell it. It was a great temporary fix – they got it from a farm who used it for the same purpose – and would recommend it.
“Refrigeration and freezing are SOOO expensive both for storage and for retail. CoolBots are a wonderful solution but that still leaves the retail issues. (We also run a store) Navigating the world of HVAC has been sort of terrifying – not sure what could help that but maybe there could be a primer for folks new to the game.” – Margaret Loftus
Heron Pond Farm, South Hampton NH – Andre Cantelmo
Heron Pond Farm (South Hampton, NH) Could not get by without the seasonal cooling they get from a 48’ reefer trailer. They use it during bulk harvest to get crops to temp and also as winter overflow storage.
Andre Cantelmo, at Heron Pond, sells these and has a hard time keeping them in stock. The Thermoking units seem to be easier to work on then Carriers. Reefer trailers are a great dock height option but do not work well if you don’t have a dock as going up and down is not very convenient or efficient.
The diesel fuel option cools much cheaper than electric unless you have three phase service on site.
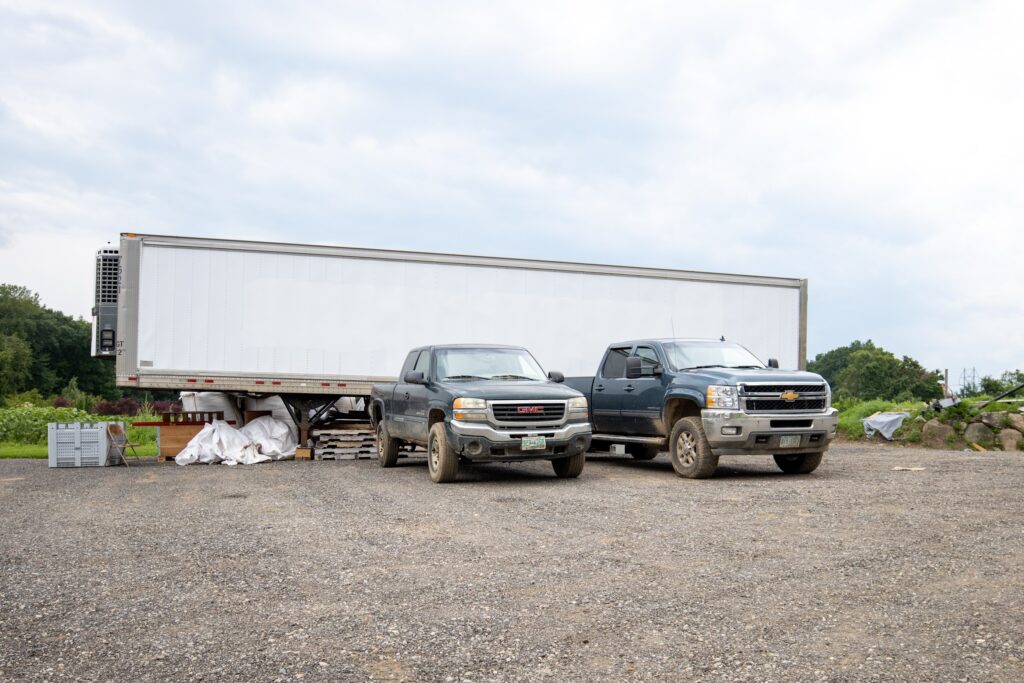
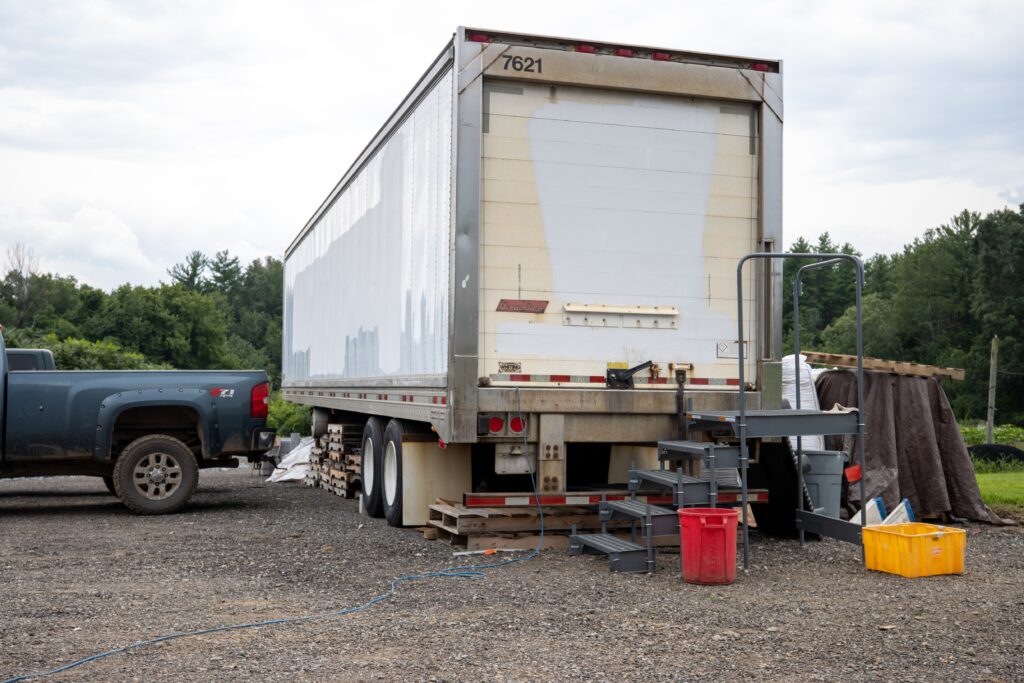
Haystack Farmstead
Haystack Farm (Pawlet, VT) shares a project summary that Brian Leach composed as part of a NE SARE research project related to modular building, specifically for a meat processing plant.
In summary he tried to draw on some of the best elements of shipping containers but create more of a “clean slate” with a modular timber framing scheme. You’ll see the use of custom corner brackets. They are kind of intense, but if they could be sold affordably, farmers could build the rest of the envelope from rough-sawn lumber. He thinks shops like his could potentially sell complete units as stand-alones or as a combined structure and then flattened build-kits could be an option as well.
“I converted 2 shipping container units with reasonable success. As a stand-alone, the containers work just fine, but they are kind of brutal to modify. Cutting through the floor is a genuinely terrible experience. I’m fortunate enough to have a supplied air setup and I was still getting nasty odors under the hood from cutting the plywood. I would consider fabrication services for-hire if it was local enough. I also have a mobile welder and gear that are potentially available for rent for folks proficient enough not to destroy them.” – Brian Leach
Modular Meat Plant Summary Report 2022.pdf
Purchase Locations
- Up North Storage Containers – Chorcorua, New Hampshire
- Shipping Containers of New England – Alton, New Hampshire
- P.E. O’Halloran Inc. – Ellsworth, Maine
- MBI Trailers – Scarborough, Maine
- Maine Trailer – Hampden, Maine
Acknowledgements
Many thanks to the VVBGA Members who contributed their experience to put together this blog post. Specifically the following: Brie Quinn – Fairlane Farm, Jody Bolluyt – Roxbury Farm, Andrea Grom – Green Jeans Market Garden, Justin Rich – Burn Rock Farm, Margaret Loftus – Crossmolina Farm, Brian Leach – Haystack Farmstead, Lissa Goldstein – Wild Work Farm, Andre Cantelmo – Heron Pond Farm
This project was supported by the Food and Drug Administration (FDA) of the U.S. Department of Health and Human Services (HHS) as part of a financial assistance award 02200-FSMA-24-01 totaling $30,000 with 100 percent funded by FDA/HHS. The contents are those of the author(s) and do not necessarily represent the official views of, nor an endorsement, by FDA/HHS, or the U.S. Government.