A PDF of this case study is available for download here.
Danielle Allen and Ben Dana own and operate Root 5 Farm in Fairlee, Vermont. This organic vegetable farm on the Connecticut River provides over 200 CSA members, farmers market, restaurant, and wholesale customers with local, healthy food. Over 100 different varieties of crops are grown on the 38 acres that make up the farm.
About the Project
The existing barn that was used for washing and packing was used for three seasons before Ben and Danielle decided to renovate it. The first three seasons provided time to learn what worked and what did not before making investments of time and money into improved postharvest infrastructure. The existing structure provided the basic footprint and included a solid shell, roof, and a gravel floor.
“One of our challenges was… we were overflowing,” notes Danielle, “We just didn’t have enough space.” This prompted the decision to expand the building and add floor space under a roof. The expanded space provides an area for washing totes, storing and using the barrel washer, and unloading product from the field in a shaded area before it is washed.
A second motivation for renovating the space was to achieve certification for food processing to make sauerkraut on the farm. This kept their eyes on food safety for processing in addition to considerations of food safety for raw, whole produce while designing their new space.
Danielle and Ben chose a new mantra for their postharvest design: “Everything on wheels!” Wash equipment, storage cabinets, dollies for product, and packing tables were all made to be mobile. This increases efficiency, reduces physical effort, and keeps the space modular and versatile for a variety of tasks. It also helps make the space easier to clean. Things can be moved out of the way and hidden corners can be made visible, making them cleanable. If something is not on wheels itself (e.g. dunk tanks or packed product) it is stacked and placed so it can be easily moved via dolly, pallet jack, or U-boat.
At Root 5 Farm all harvesting is done in just 3 days a week. A rotating schedule is used so different people use the wash-pack area each day and aren’t always required to do the same tasks. Having a walk-in cooler, equipped with a sliding door enables short term storage of crops and increased storage life as they prepare for markets and deliveries. Washing systems for all of the crops are versatile due to the diversity of produce grown and sold. Wash lines are set up to be easy for everyone using the same equipment. Some of this equipment includes three dunk tanks for triple washing greens, a greens spinner (converted washing machine), wooden barrel washer, and several hoses with multiple drops for spraying things off in multiple areas.
Project Specs
The project involved the renovation of an existing barn and turning an area of 25’x36ft (900 sq. ft) into washing, packing and storage space and adding a 12’ wrap around concrete apron around two sides of the building for additional workspace totaling 1,776 ft².
Cost: Approx. $40,000 ($23 per sq. ft.)
About Root 5 Farm
- Fairlee, Vermont
- 38 acres with 8 acres in vegetables
- Over 100 Different varieties of vegetables
- 200 Member CSA, farmers markets, restaurants and co-op stores (65% CSA/ 20% Wholesale 15% farmers market)
- $250,000-499,000 in Sales
- 8 Full-time Workers (March-December)
2 Full-time Workers (December-April) - Dunk tanks, barrel washer, and hoses
- On-farm sauerkraut production
Cost
Total cost for the renovation of the barn was $40,000. This project was supported by a Vermont Working Lands grant which matched half of this cost.
Best Decisions
There were several things that were implemented to boost crew morale in this space. Installing proper light fixtures over the work area and including windows and large doors let in lots of natural light. The eight foot wide doors also make it easier to move product and equipment. Adding overhangs and expanding the usable space also provides shelter from the weather. When a thunderstorm rolls in, everyone can hang out under safety and pass the time by washing totes.
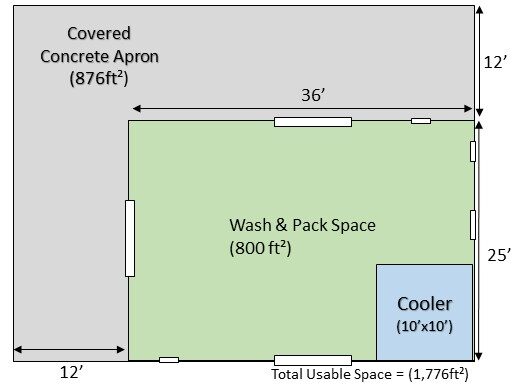
The crew has adopted practices and set up the space in a clean and well lit way which makes the work natural and “produce safety just happens” as a result of prior planning. Features that make the space efficient and food safe include:
- Easy to clean surfaces
- Metal washable walls
- Stainless tables
- Concrete floors
- Good drainage
- High visibility
- “Everything On Wheels!”
equipment to move around during this in-between time from the field to the consumer. Adding overhangs and expanding the usable space also provides shelter from the weather. When a thunderstorm rolls in, everyone can hang out under safety and pass the time by washing totes.
The crew has adopted practices and set up the space in a clean and well-lit way which makes the work natural and “produce safety just happens.” Features that make the space efficient and food safe include:
- Easy to clean surfaces
- Metal washable walls
- Stainless tables
- Concrete floors
- Good drainage
- High visibility
- “Everything On Wheels!”
If it’s easy to move, it’ll be easy to clean around. All of these features make it an unwelcoming place for pests to hang out which reduces contamination risk due to rats and rodents.
“Produce Safety happens because it is set up in a clean and well-lit way.”
Danielle shared how nice it was to now be able to make sauerkraut on the farm and explained what else was needed for food processing over produce safety regulations. This extra step included meeting with the state health inspector both during construction and for a final inspection. The inspector was looking at several things that were already in the plan like washable walls, washable floors, shatterproof light fixtures, etc. Additional requirements included a dedicated hand washing sink plumbed to the septic and a triple bay sink for washing dishes.
The most recent addition to improve the workspace was adding heat. With increased season extension work, adding heat makes the work more enjoyable during these shoulder seasons. They insulated the building during the early renovations so it was ready to be converted into a conditioned space without many other modifications.
Danielle shared one other piece of advice when talking about taking on a construction project like this. “Have realistic expectations because it takes a lot of money and takes a lot of time, don’t be too hard on yourself,” she noted.
To watch the interview with Danielle and to see more of the packshed, visit our YouTube Channel.
Contributors to the Project
UVM Extension Ag Engineering and the Produce Safety Team
Vermont Agency of Agriculture Through the Specialty Crop Block Grant (USDA) which funded the Postharvest Management Team
Acknowledgments
This case study is possible because of the hard work, wisdom, and generosity of Danielle Allen and Ben Dana at Root 5 Farm. Without their willingness to take the project on to begin with, deal with all the challenges that such projects bring, and complete it we would have nothing to share. We are grateful to them for their willingness to share their story and knowledge in this form so that others can learn.
Funding for this publication was made possible, in part, by the Food and Drug Administration through grant PAR-16-137 through the Vermont Agency of Agriculture Food and Markets via the Integrated Extension Educational Programming in Support of the VAAFM Produce Program Grant (#02200-FSMA-2018-01) and by the USDA’s National Institute of Food and Agriculture through the Food Safety Outreach Program award 2016-70020-25792 accession 1010528. The views expressed in the publication do not necessarily reflect the official policies of the U.S. Department of Health and Human Services, the U.S. Department of Agriculture or the Vermont Agency of Agriculture; nor does any mention of trade names, commercial practices, or organizations imply endorsement by the United States Government or the State of Vermont.
Share this Post!
Looking for More?
We have additional post harvest case studies of various renovations and new builds that can be seen here. go.uvm.edu/phcs
All things post harvest covers individual blog posts discussing building features, equipment, and other PDF guides.