Download this Postharvest Case Study as a PDF Here!
Lisa MacDougall has led Mighty Food Farm through start-up, relocation from rented land to owned land, and now through the construction of a brand-new 60 ft x 90 ft wash and pack shed. She’s done this all while producing a diverse mix of organic vegetables, tree fruit, and berries on fourteen acres, now, in Shaftsbury.
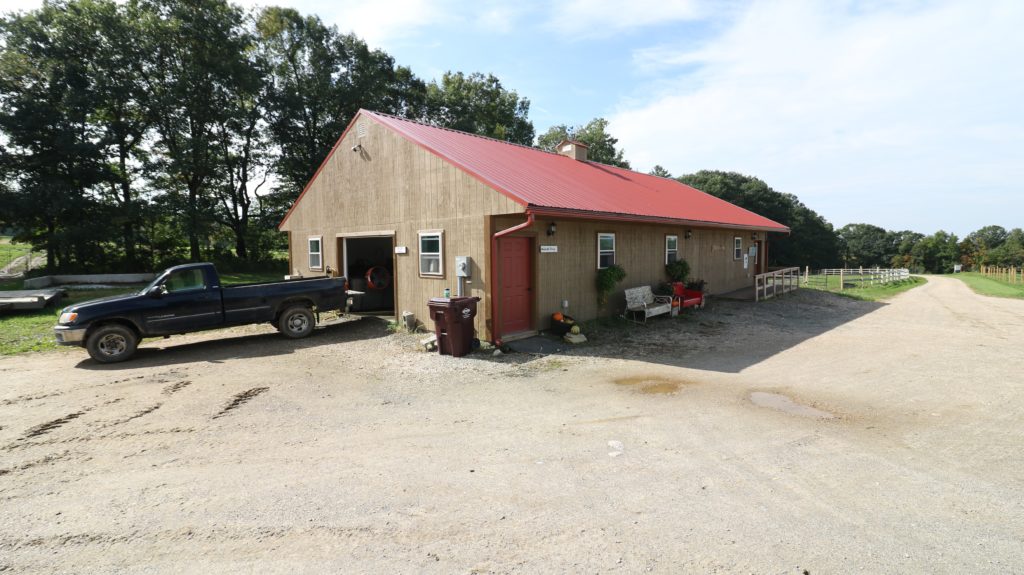
One of Lisa’s primary goals in her new location was “a proper P-shed”; a pack shed where she and her crew could comfortably and safely wash, store, and pack produce for delivery to her customers year-round. Mighty Food Farm serves retail farm stand, farmers market, CSA, and wholesale customers.
“It was 10 years of just slogging through the process every time we had to pack out at our prior location.” says MacDougall, “It’s what we do all of this work for, to bring fresh, awesome produce to our customers. And the final step was just… not very enjoyable. Every week.” Lisa also noted that drainage was really poor in her prior location. Packing out for market in winter would inevitably mean negotiating ice or slush with arms full. They had a door that you had to duck through if you were over 5’9”.
About Mighty Food Farm
- Location: Shaftsbury, VT (previously in Pownal, VT)
- Acreage: 14 acres in production
- Crops: lettuce, kale, mixed greens, winter greens, scallion, onion, winter squash, carrot, tomato, cucumber, strawberries, blueberries, apples, pearsand plums.
- USDA Sales bracket: $100,000-249,999
- Markets: CSA, On-farm Retail, Farmers Markets, Wholesale
- Crew: Summer (May-September) is 7; Fall (September-November) is 5; Winter (December-March) is 1.
- Wash/Pack Operations: Triple bay greens washing with gently shaken crate for drying, Barrel/drum washer, bunch washing in spray sink, 3 coolers (CoolBots)
About the Project
Overview: New, slab-on-grade construction 30’x60 (1,800 sq. ft.), single story. Mixed use of wash/pack, storage, retail/CSA, and crew space.
Before deciding to build from scratch, Lisa considered retrofitting a space into an existing, relatively new horse barn. Walking through the space with some rough floor plan sketches in hand she explored the pro’s and con’s. Finally, she landed on new construction so that she could get just what she wanted. She also felt converting a perfectly good horse barn to a vegetable wash/pack could reduce the future value of the horse barn and also her use of it for her own horses. Ultimately, the new construction added 20% to the project cost when compared to a renovation. Though not insignificant, the additional cost was well worth the benefits for Mighty Food Farm.
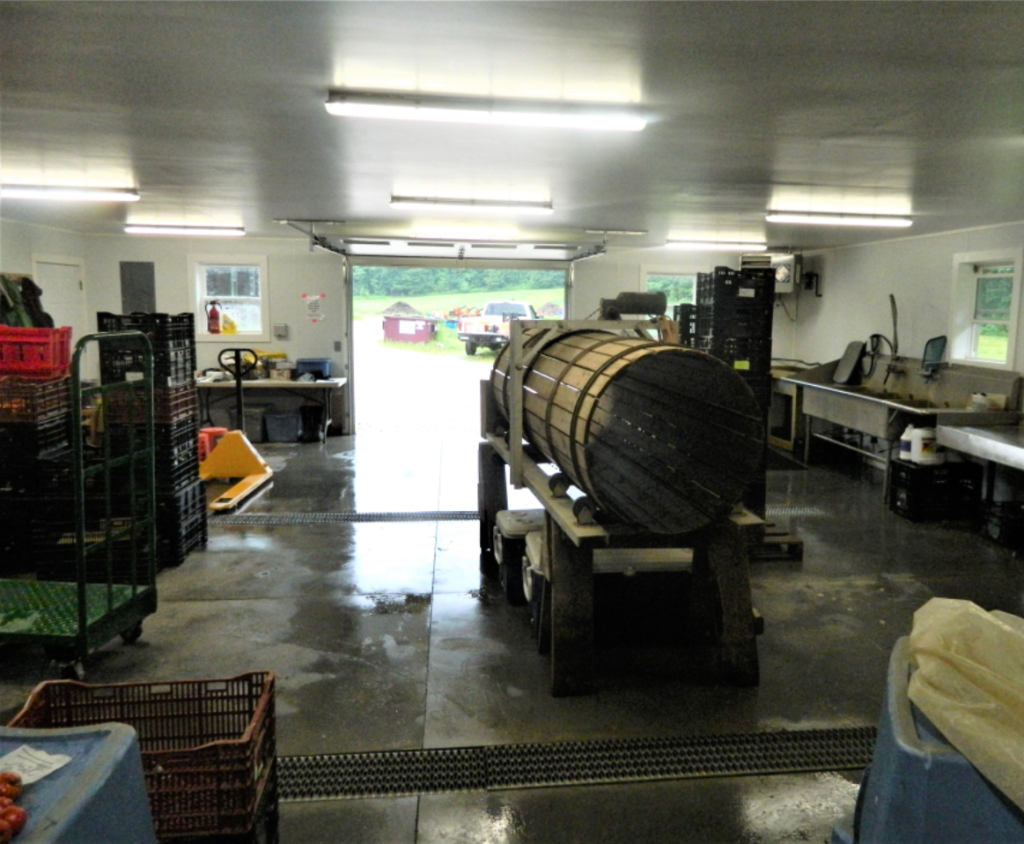
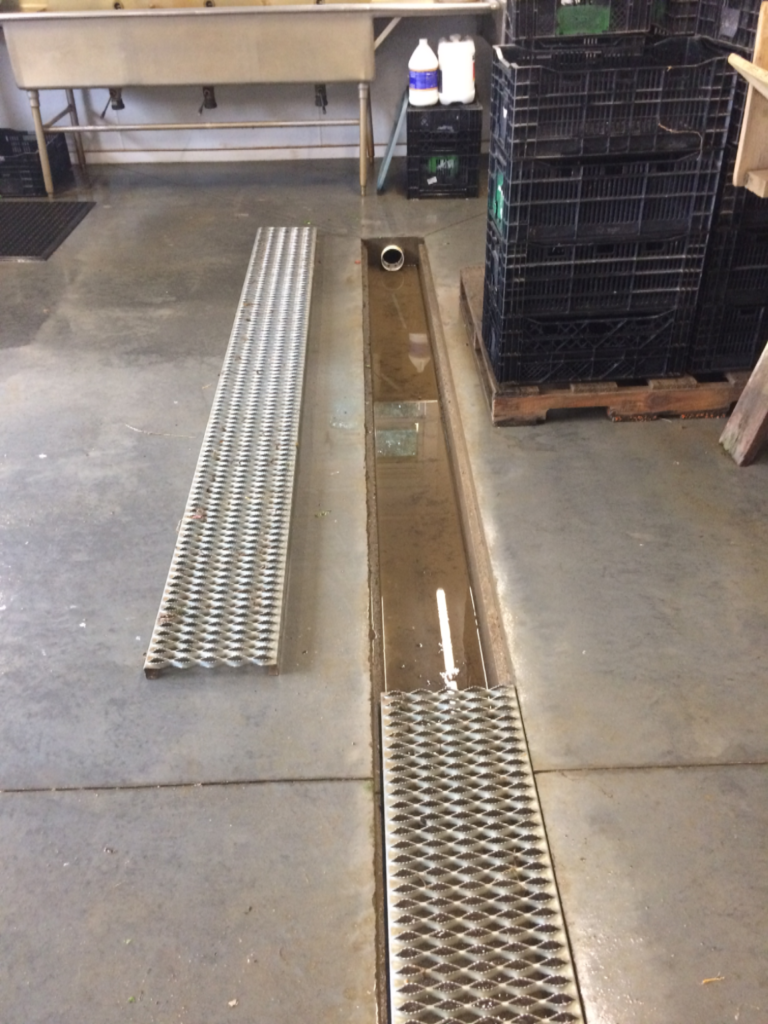
What was at the top of the list? Comfort, efficiency, and safety.
Lisa knew she wanted large doors and shaded floor space to “stage” produce coming in from the field and out to market. Her previous washpack required maneuvering crates in both hands up and down stairs, through narrow doors and around corners. The need for more space was a given; her previous location was about one-third the size of the new building.
“I’ve realized that there is a key question you need to ask yourself as a growing farm.” she notes, “Am I going to be a fork truck farm or a not?” Lisa decided that the right scale for her was supported by harvesting into handheld crates not pallet bins and that the majority of product movement could be in crates. Once in the packshed and storage coolers, the crates can be palletized and moved with a simple pallet jack. The smooth, continuous concrete floor serves the need for storage in both cartons and pallets.
A key feature of the new wash area are two central trench drains. Trench drains provide for a high volume floor drain that is flush with the floor surface and able to accommodate solids and sediment. They are also easier to clean regularly. “The steel grates pop off and a standard 12” square shovel can scoop out the soil”, MacDougall pointed out. These drains can also fully dry once cleaned which is an added produce safety benefit.
“It’s just clean and bright. We like to be in the space.” Lisa noted as she pointed out smooth and cleanable wall finishes making use of fiber reinforced plastic (FRP), also known as “dairy board.” Ample, energy efficient LED lights overhead also make for an improved workspace.
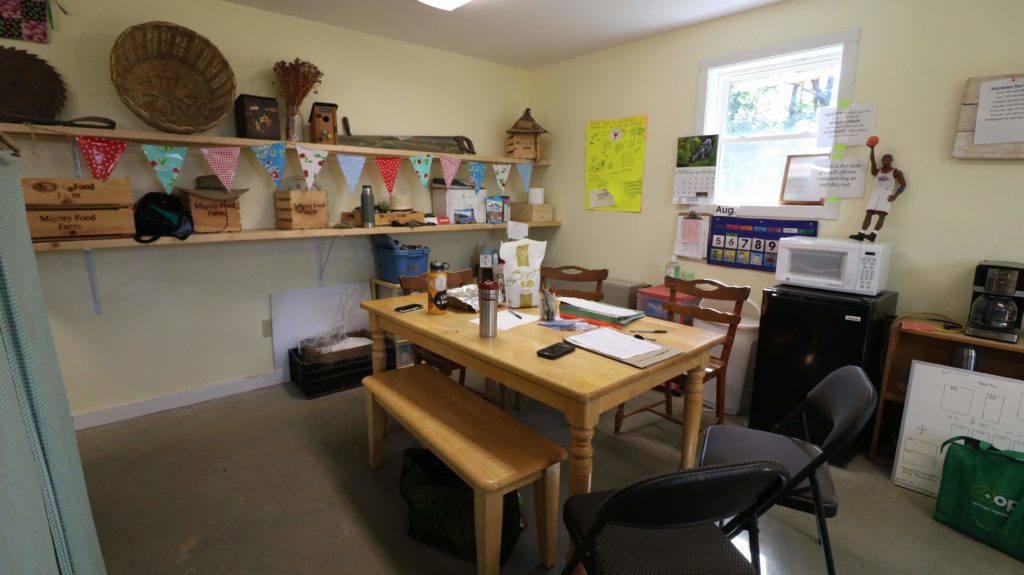
The space is so new, clean, and bright that the contractors commented on the “old”, “used” wash equipment being moved back in “messing up the place.” Lisa actually helped complete the construction crew with some of her farm crew who had some building experience.“I just feel better about my product and my crew.”
Lisa also wanted to provide a space for the crew to actually take a break and eat lunch, not to mention having a dedicated sink for handwashing. “Once you have a crew of more than three people, you really need to provide a dedicate break area.” She also wanted a clean and comfortable place for customers to visit for retail purchases and CSA pickup. The western third of the new building serves these needs. “The wash/pack has really become ‘the hub’ for the farm.”
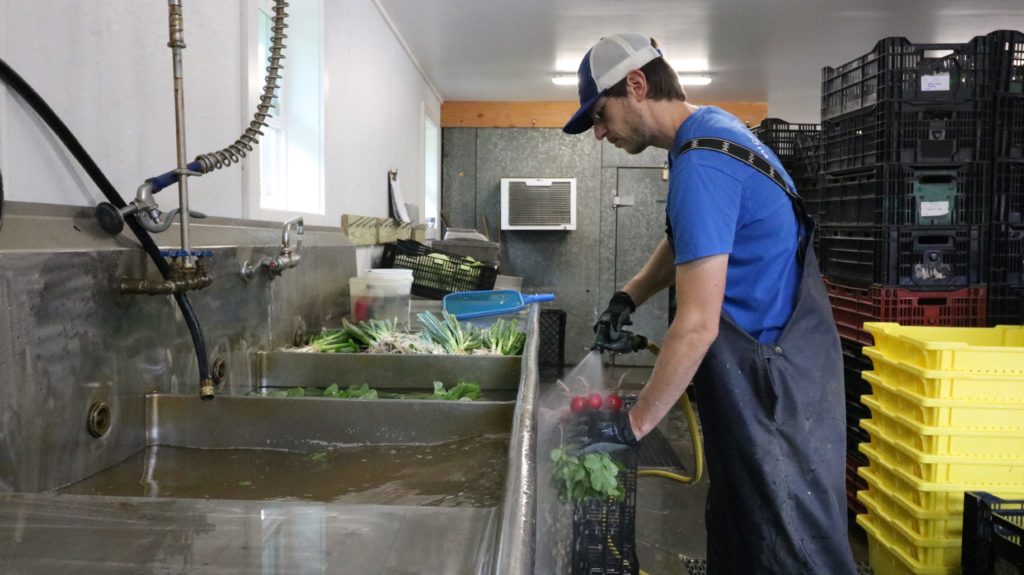
Looking back on the project there are a few things that Lisa would spend a little more attention on. She knows she’ll have to add some ventilation into the space eventually and it might have been easier to do from the start. There is no toilet in the new building which was avoided due to the need for septic system (though there are facilities nearby). The building is a “dry building” with the only water source being a frost-free hydrant outside which is currently brought in by hose. Wash water is sent to a vegetative swale.
Favorite Things
- Large Overhead Door—$3,000
- Landing Zone for Harvest and Packout— about $6.00 per square foot. $1,500 to 15,000 depending on the size of slab and features (drains, etc.) – go.uvm.edu/floors
- Heated Space – Propane unit heater—$1,000-3,500 depending on size and efficiency.
- Bright Cleanable Walls – FRP – go.uvm.edu/smoothnclean – about $1.00 per square foot.
- Trench Drains – Two 12”x20’ – Included in slab.
- Techno Post Helical Pile vs. traditional footings for slab on grade – www.technometalpost.com – Saves $4,000 on concrete (no footings).
Lisa notes that the project has really opened up a lot of possibilities for Mighty Food Farm. The farm was previously limited by cold storage capacity and was able to build additional storage space as part of the construction. It is easier to maintain a high crew morale thanks to some of the softer aspects of the project such as making it a clean and bright space and providing a dedicated place for breaks. Lisa is proud to have a great crew with longevity and aims to keep them as long as possible. Coolers and CoolBots are easier to maintain indoors and the life of the CoolBots have been increased. Lisa has also noticed a marked improvement in her ability to regulate cooler temperatures with the coolers inside. Product quality has also improved with a dedicated, clean space to efficiently wash, pack and store. Produce safety practices are much easier to achieve in the new space. Record keeping and crew organization has also been improved now that there is a central “hub” for activity.
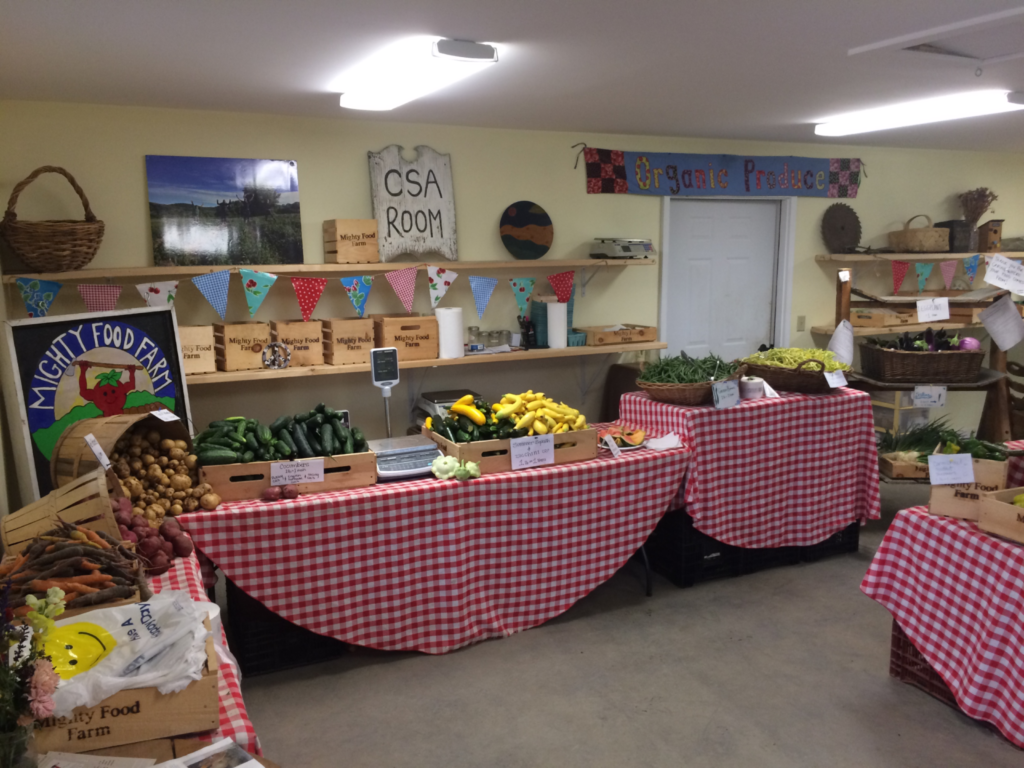
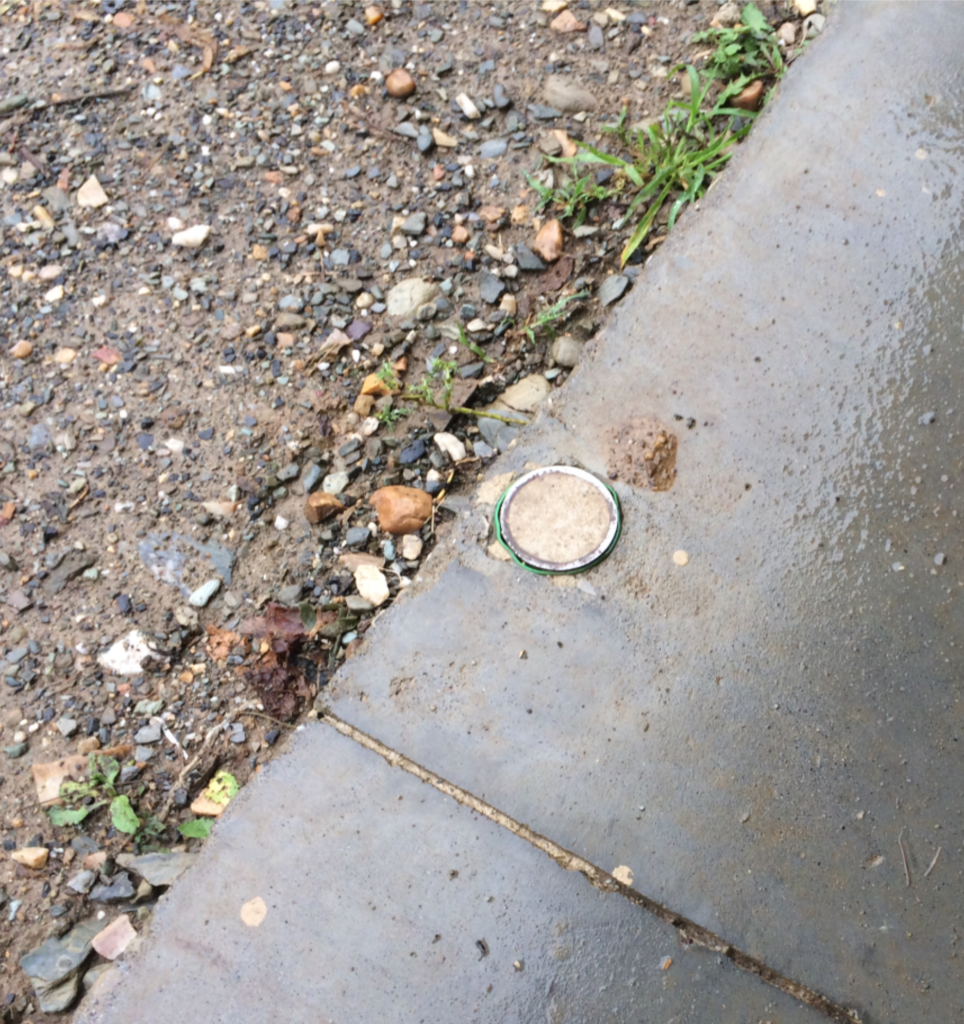
If your interested in checking out the pack shed in action see the videos below! In the following playlist, there is a promo video (1min), vegetable washing (2min), Use of a Grindstone barrel washer (2min) and an interview with Lisa talking about the project (11min). Enjoy!
Share this post!
Looking for more Post Harvest Case Studies?
We showcase several farms of various sizes, features and budgets in this series. Visit: go.uvm.edu/phcs
Acknowledgments
This case study is possible because of the hard work, wisdom, and generosity of Lisa MacDougall at Mighty Food Farm. Without their willingness to take the project on to begin with, deal with all the challenges that such projects bring, and complete it we would have nothing to share. We are grateful to them for their willingness to share their story and knowledge in this form so that others can learn.
Funding for this publication was made possible, in part, by the Food and Drug Administration through grant PAR-16-137, by the USDA’s National Institute of Food and Agriculture through the Food Safety Outreach Program award 2016-70020-25792 accession 1010528 and by The Vermont Agency of Agriculture Food and Markets via the Vermont Specialty Crop Block Grant (USDA-AMS-SCBGP-2015). The views expressed in the publication do not necessarily reflect the official policies of the U.S. Department of Health and Human Services, the U.S. Department of Agriculture or the Vermont Agency of Agriculture; nor does any mention of trade names, commercial practices, or organization imply endorsement by the United States Government or the State of Vermont.