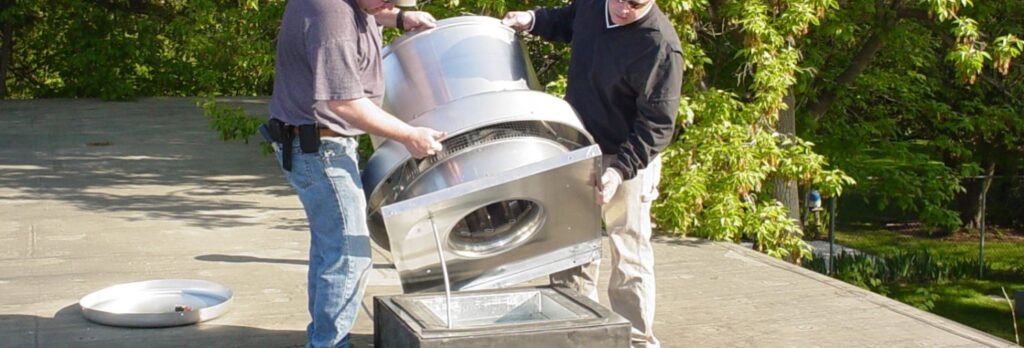
In contrast to Reactive Maintenance — which is performed in response to a request or if something is broken — Preventive Maintenance (PM) refers to activities that are done to prolong the life of an asset or piece of equipment, i.e., to prevent it from breaking or wearing out prematurely. Routine tasks such as replacing air filters and drive belts, and performing safety inspections of equipment are examples of preventive or planned maintenance.
Every equipment asset has an associated “standard service plan” which lists the specific maintenance tasks and frequencies (e.g., weekly, monthly, annually) that are needed to keep the asset running in tip-top shape. Plans are often based on the manufacturer’s recommended service schedule or can be modified based on actual field experience.
Although a popular adage tells us, “If it ain’t broke don’t fix it”, we Facilities Management professionals prefer to “fix things before they break” to minimize any disruptions to campus operations caused by equipment failures.
The Preventive Maintenance (PM) module of Planon will primarily be used by maintenance supervisors who plan and schedule PM work and by technicians who perform the work in the field. Planon will provide similar functionality as our current system but through a more intuitive and graphical user interface and with more bells & whistles. For example, technicians will have the ability to view related building floorplans and system schematics from their mobile device. Supervisors will also have access to a visual scheduling tool (sort of like a fancy calendar) for planning work based on actual available staffing levels. For example, if a supervisor knows that an HVAC technician will be on vacation the coming week, they can simply “click and drag” a scheduled PM task ahead in the calendar.
One of the IWMS Core Team design tasks is to extract, review and transform all of our existing PM service plans on all equipment (from FAMIS) in order to build out the new “library” of standard service plans in Planon. Adam Holmes (Asset Coordinator) has been coordinating this task and meeting individually with Physical Plant managers and supervisors to gather the relevant information.
Stay tuned.
~The IWMS Core Implementation Team