Could wheels help you out in your pack shed? When do they make sense and when don’t they? Below are examples illustrating how growers are using wheels in different ways to ease the movement of product out of the field and around the wash/pack.
Why Scale, Diversity, Markets and Bins Matter?
At the heart of it, farming involves a lot of moving things from one place to another. This is especially true in the postharvest period once produce is harvested and before it reaches the consumer.
Crop selection, diversity of crops, scale of production, labor strategy, and market types all influence how produce is best moved into, around, and out of the packshed.
A relatively small-scale operation with a highly diverse mix of crops being distributed through a community supported agriculture (CSA) marketing model may be best served with a collection of small, one-bushel crates carried by hand.
A medium scale operation may use the same approach, but aggregate these bins onto pallets or U-boats to move more of them in one trip.
A larger operation with a wholesale market focus may prefer 20 bushel pallet bins for bulk harvest and primary storage of crops which then are packed out into smaller retail bags or cartons which, themselves, may be palletized for distribution.
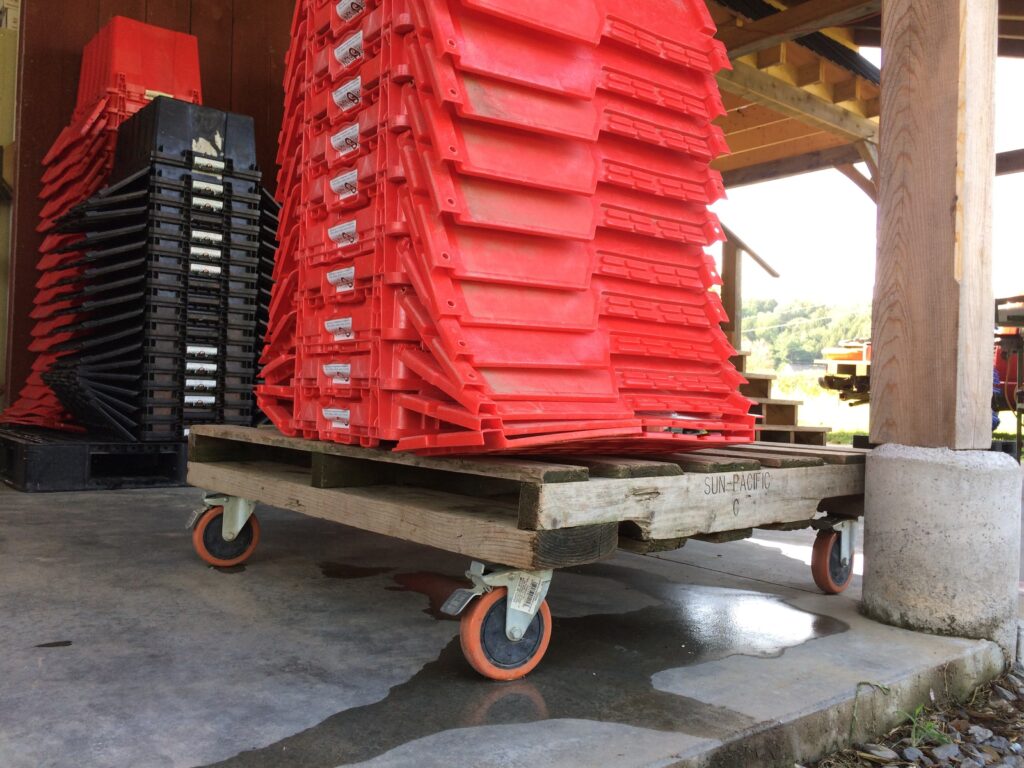
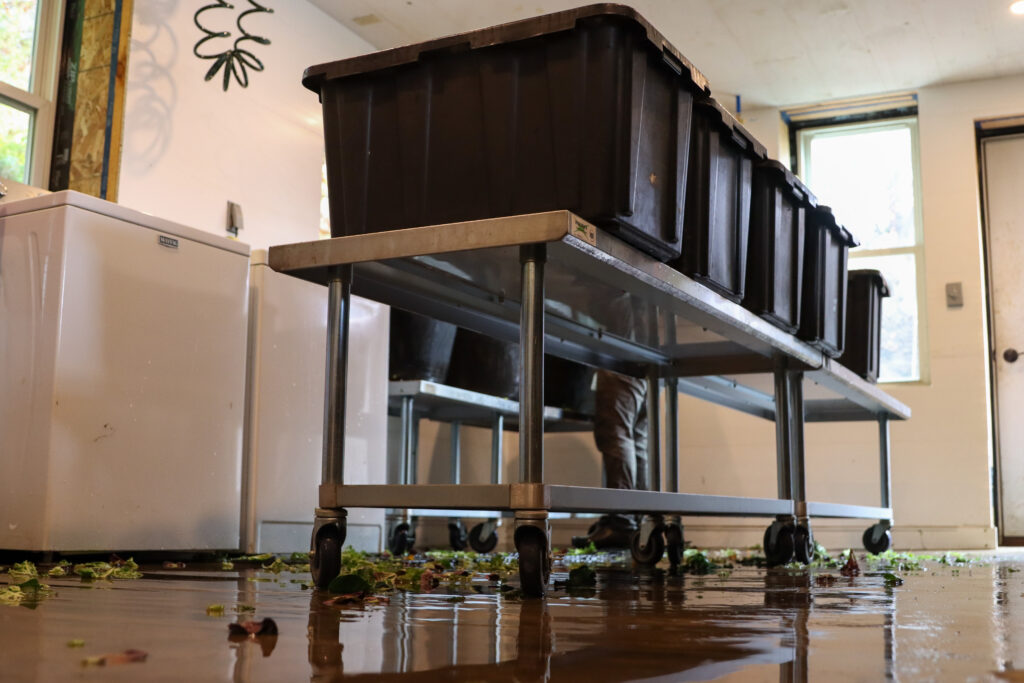
When to Change What You’re Doing?
How do you know when you should move up? Do routine tasks feel like a waste of time? Are you hurting your body?
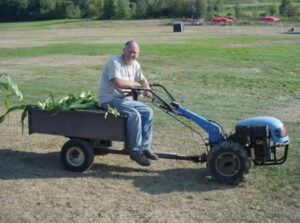
As with many decisions about “how” to do anything, individual preferences and planning are important. The acceptable level of pain and frustration is highly variable from person to person and over one’s lifetime.
Hand carrying bins of produce to and from storage and market may be acceptable or even preferred by some people while being considered a waste of time and energy by others.
As a farm grows and changes over time, the volume of product (and the age of the farmer) can also influence what product movement systems are appropriate.
It is rare that an experienced farmer ever looks back on their career and says , “I wish I lifted more heavy things more often.” Think about how your decisions in this area might impact yourself 20 years from now.
Hand Carts, Trailers, and Pickup Trucks
Movement from the field to the packshed also takes many forms from handcarts to trailers to pickup trucks. Side-by-side all-terrain vehicles (ATV’s) and golf carts are becoming increasingly popular among small and medium-scale, diversified produce growers juggling lots of different crops and activities that do not need a tremendous amount of load capacity .
Side by sides, like a John Deere Gator, are easy to drive, have a light footprint, and can easily haul tools, supplies, plants or harvested goods around the farm where a truck may be cumbersome.
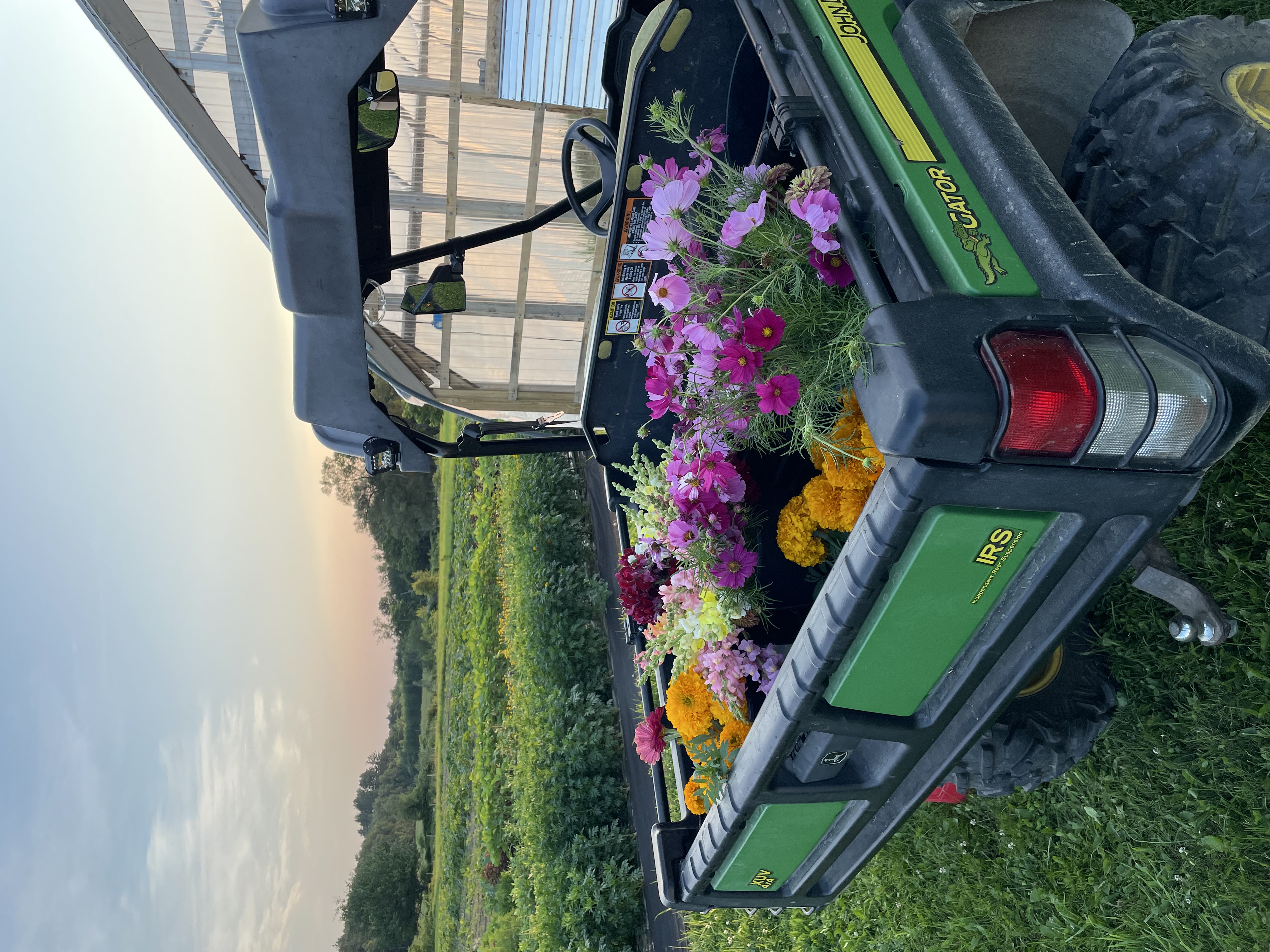
If considering using carts, dollies, or hand trucks keep in mind that you may need pneumatic tires or smooth floors in order to easily traverse the surfaces of the farm or packshed.
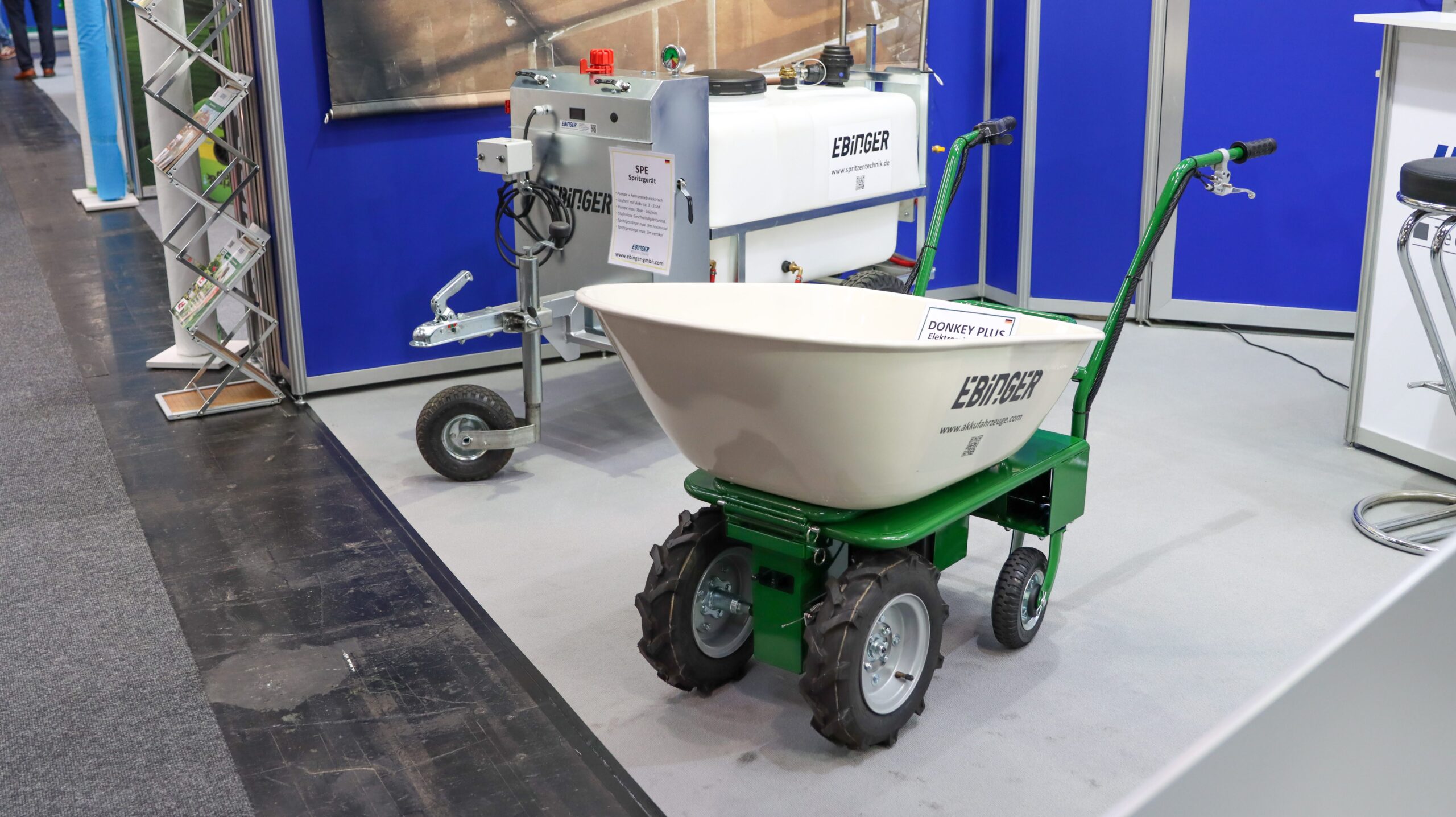
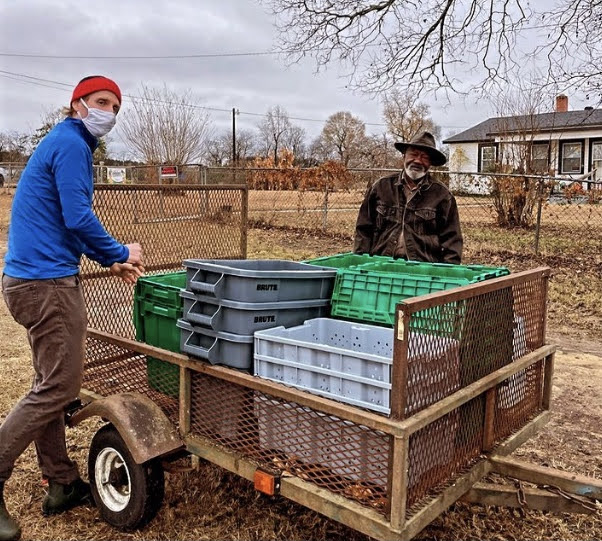
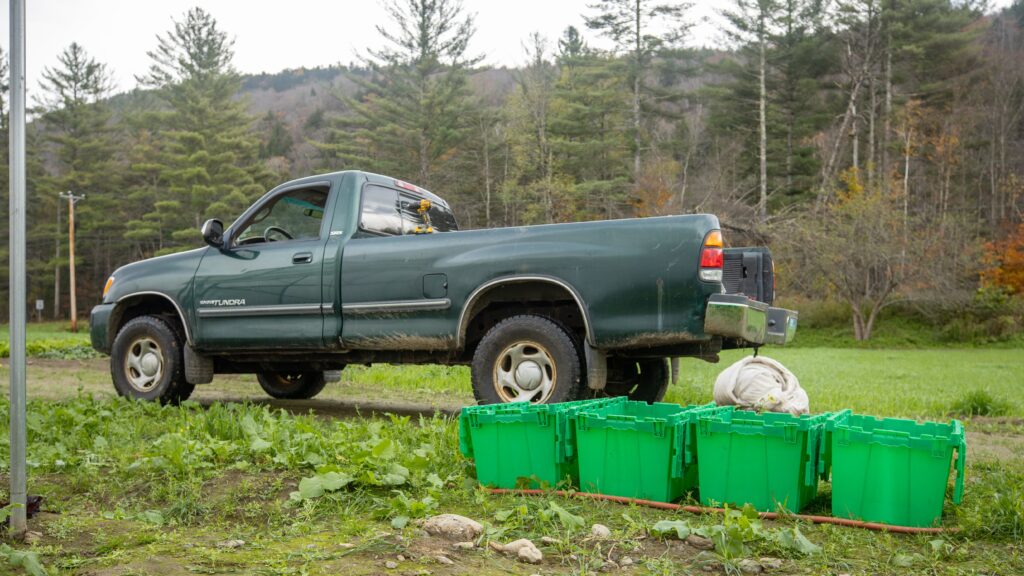
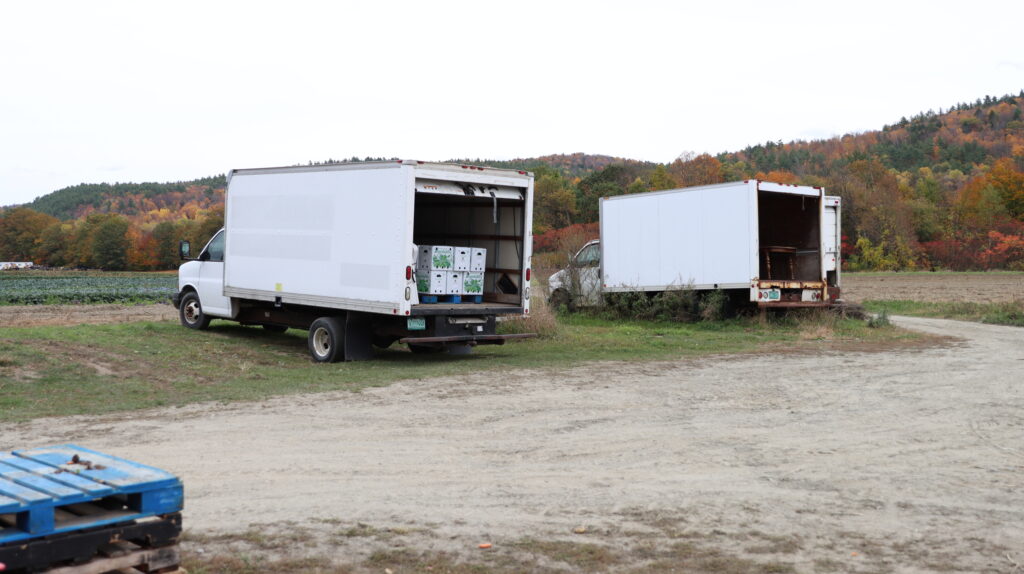
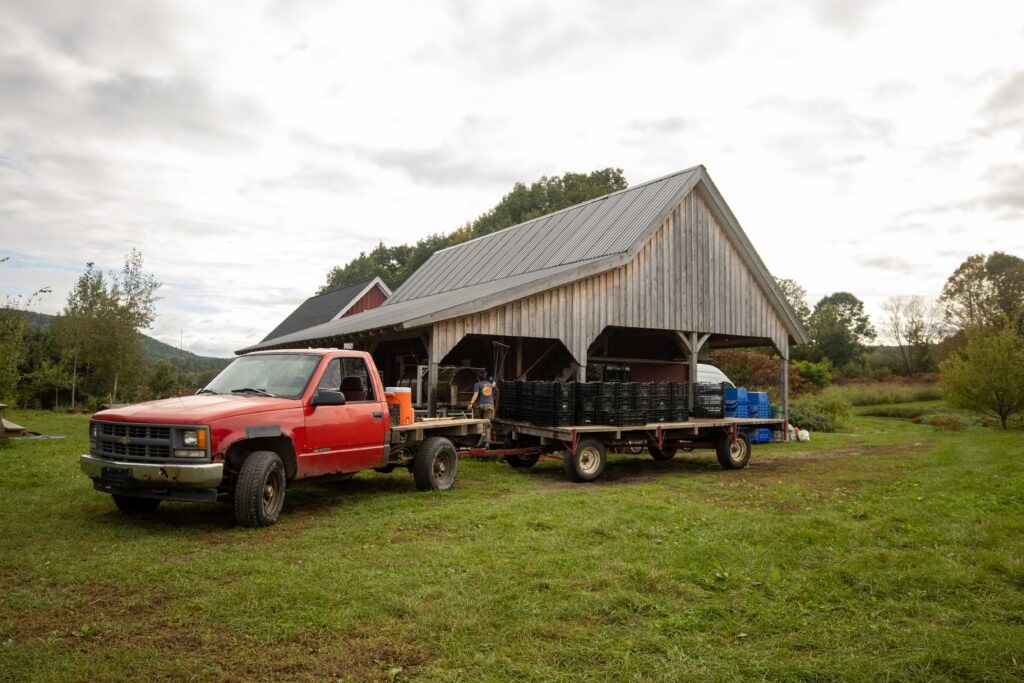
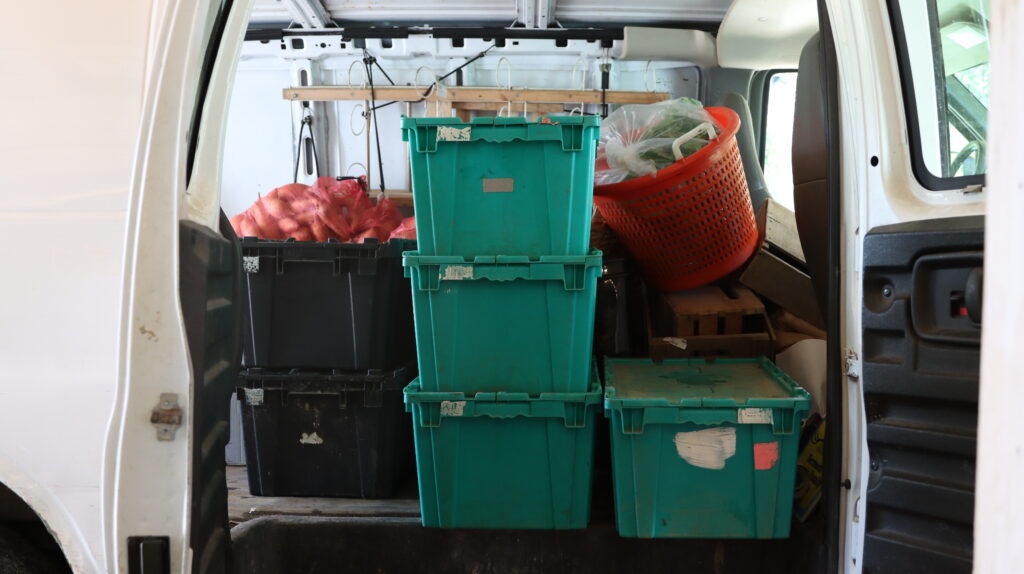
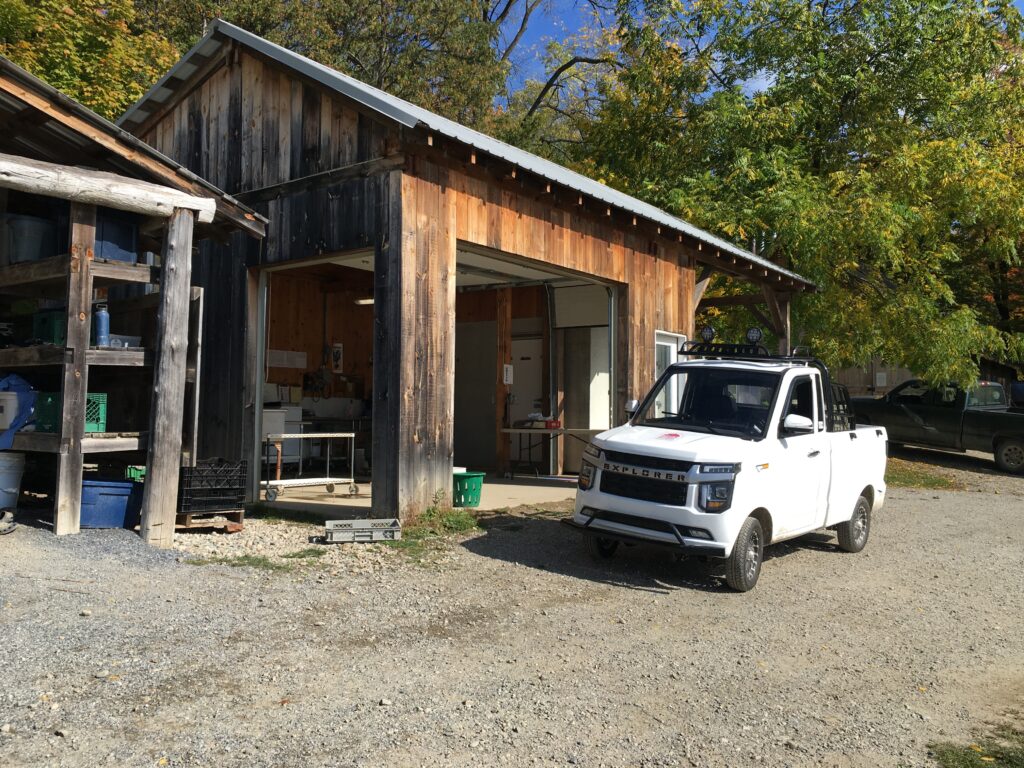
Hand Carry
One key factor in the decision-making process for product movement is the layout of the packshed and the condition of the floors. Often when starting out, the pack shed is a very “make-do” situation leveraging whatever space is left over after field equipment and other supplies are covered. This often means there may be less space, more turns, more steps up and down, and uneven floors. All of that points to a hand-carry approach over anything that is rolled along the floor.
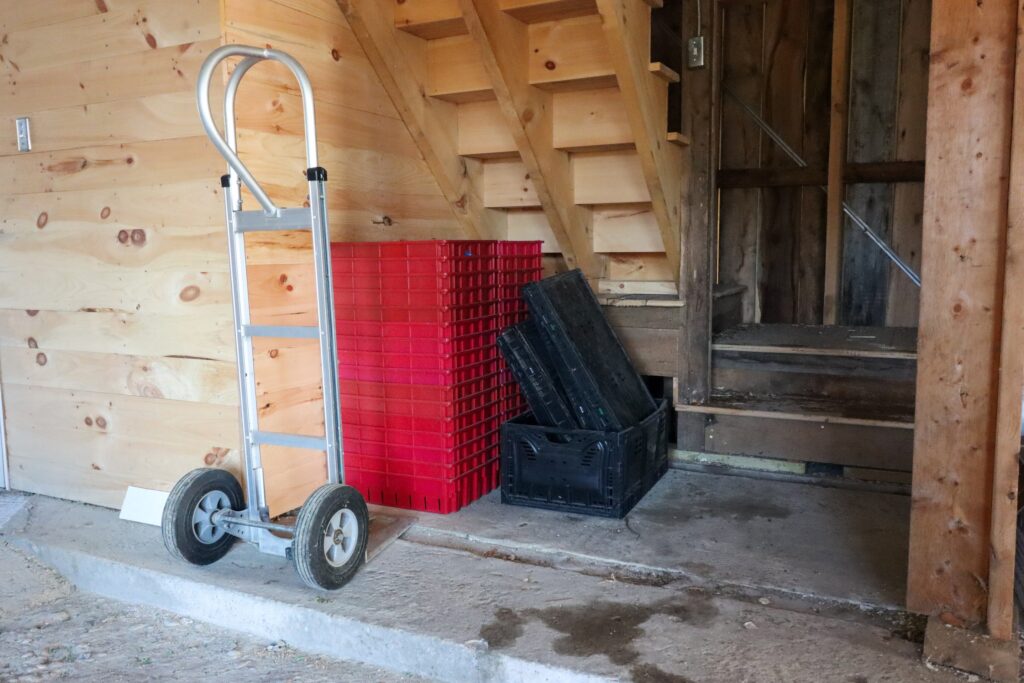
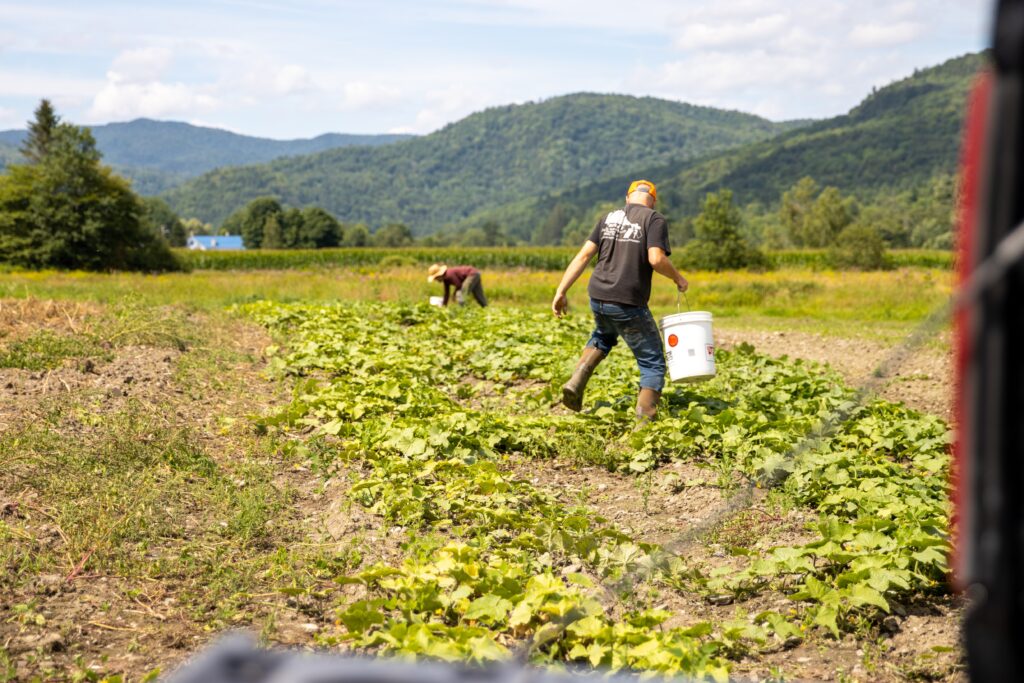
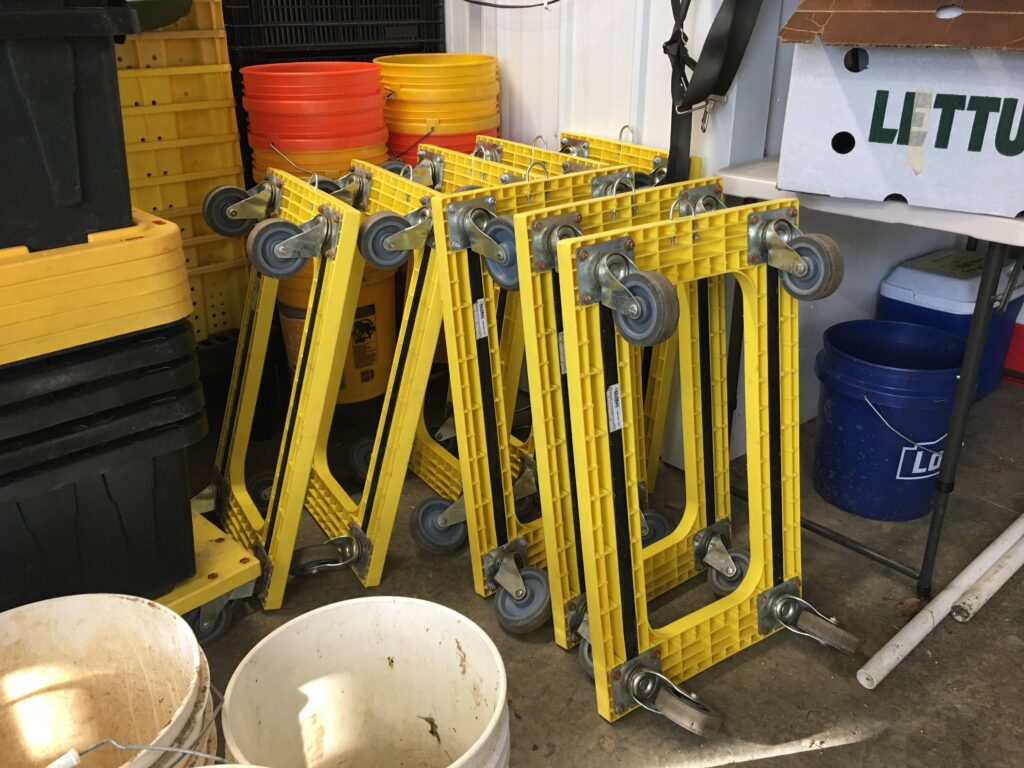
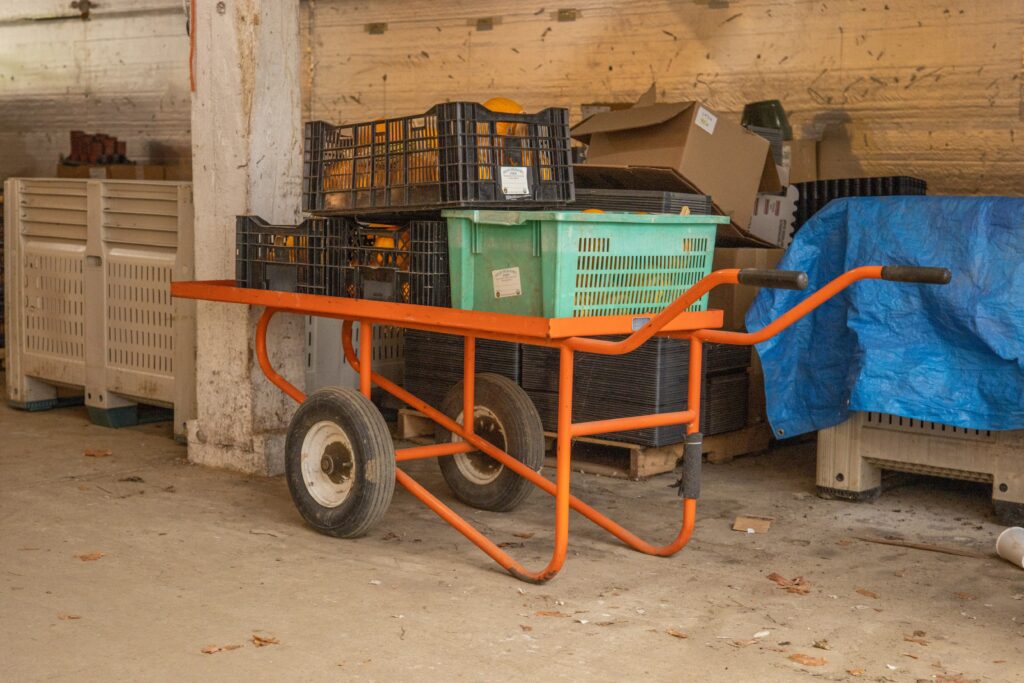
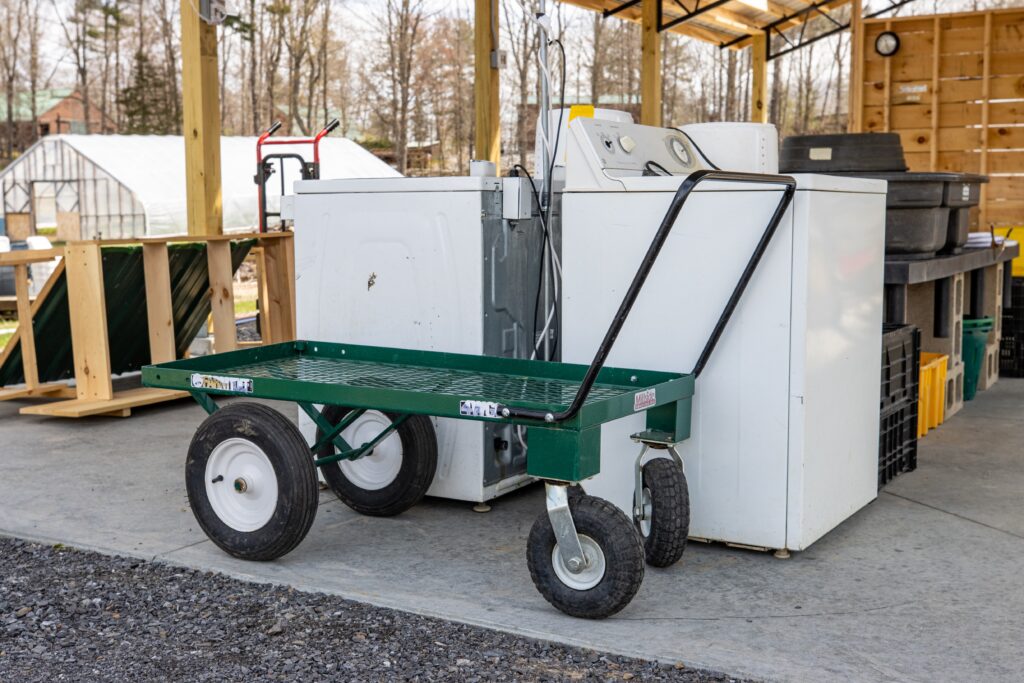
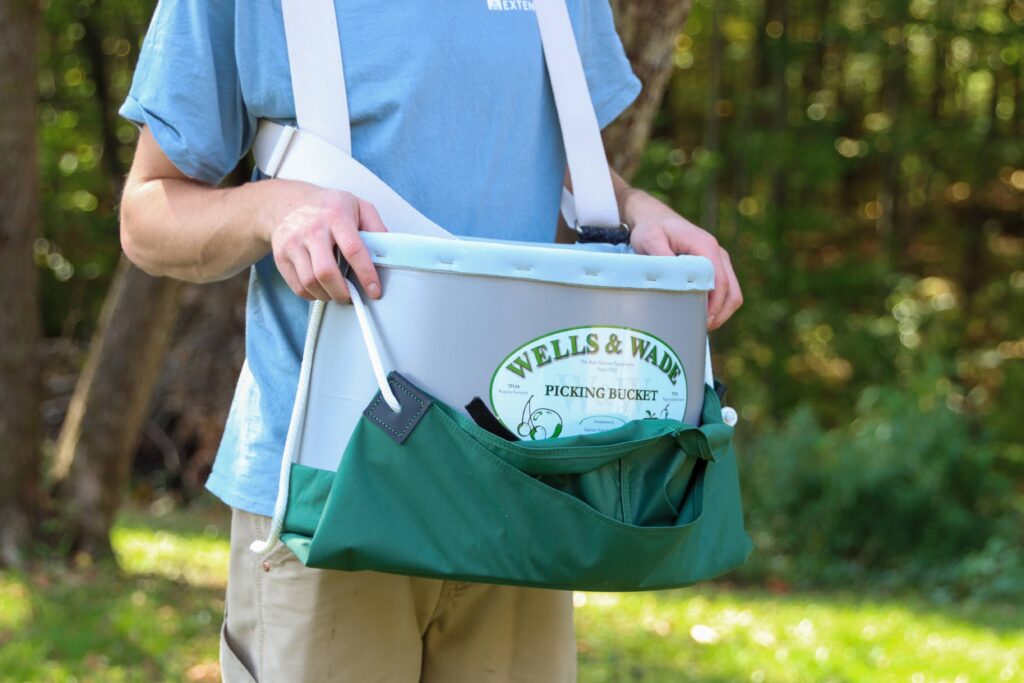
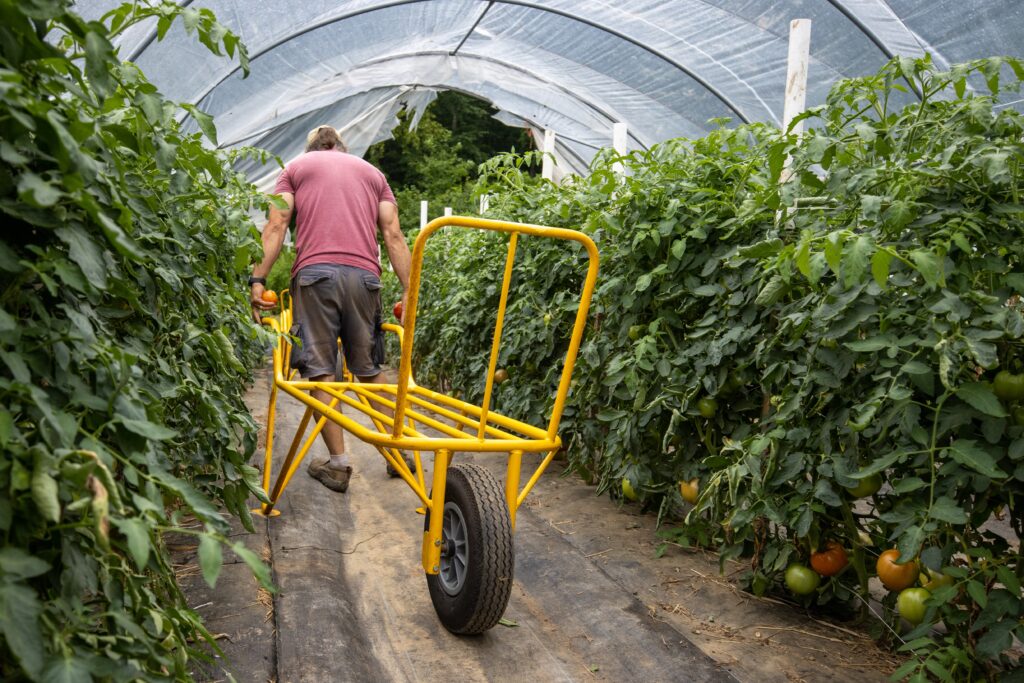
DIY Options
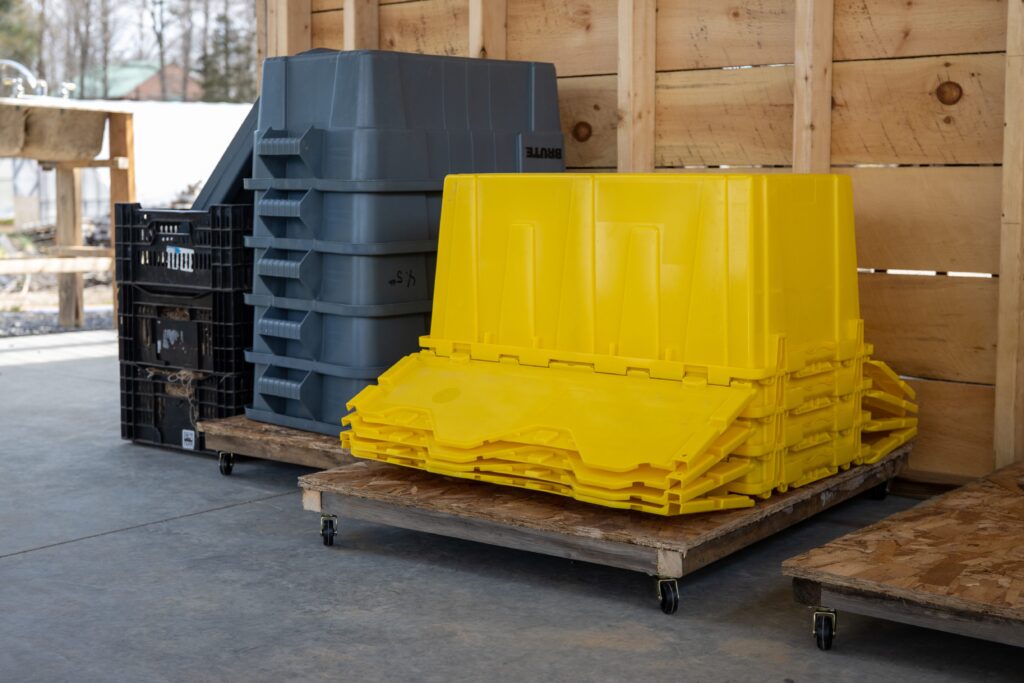
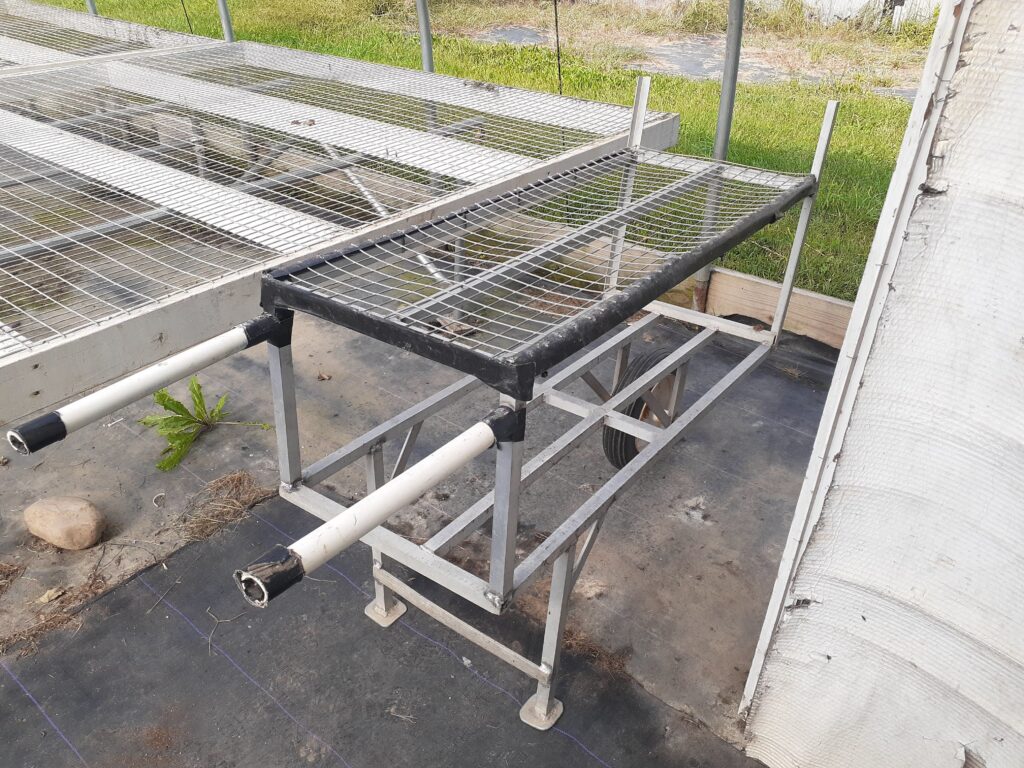
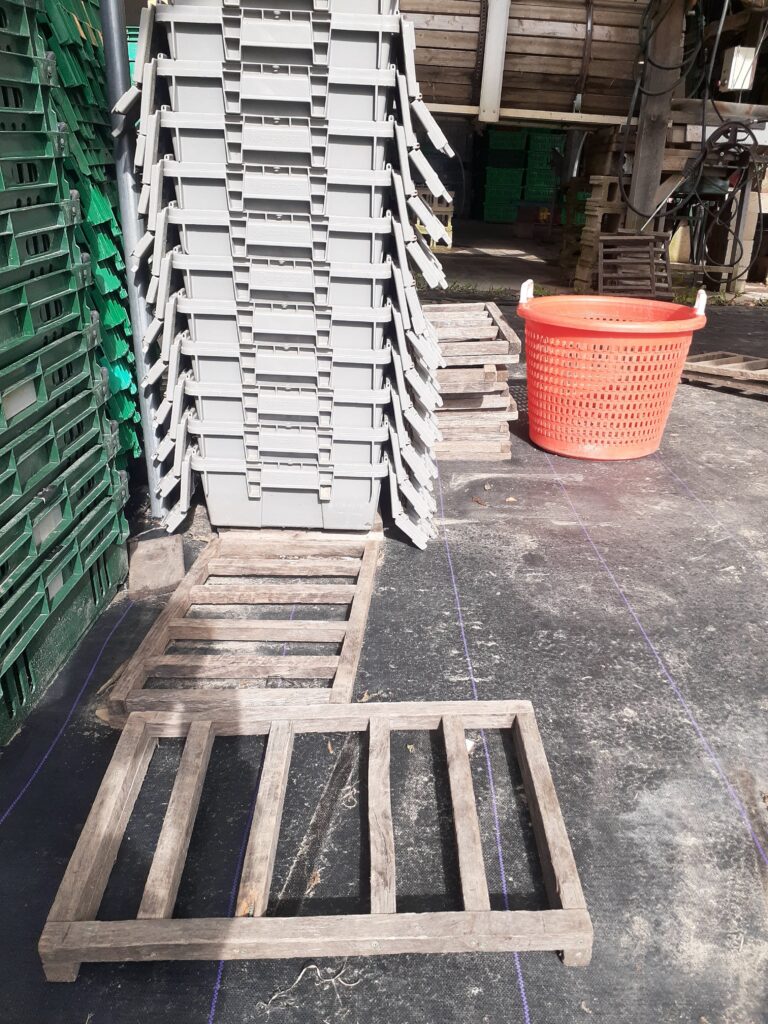
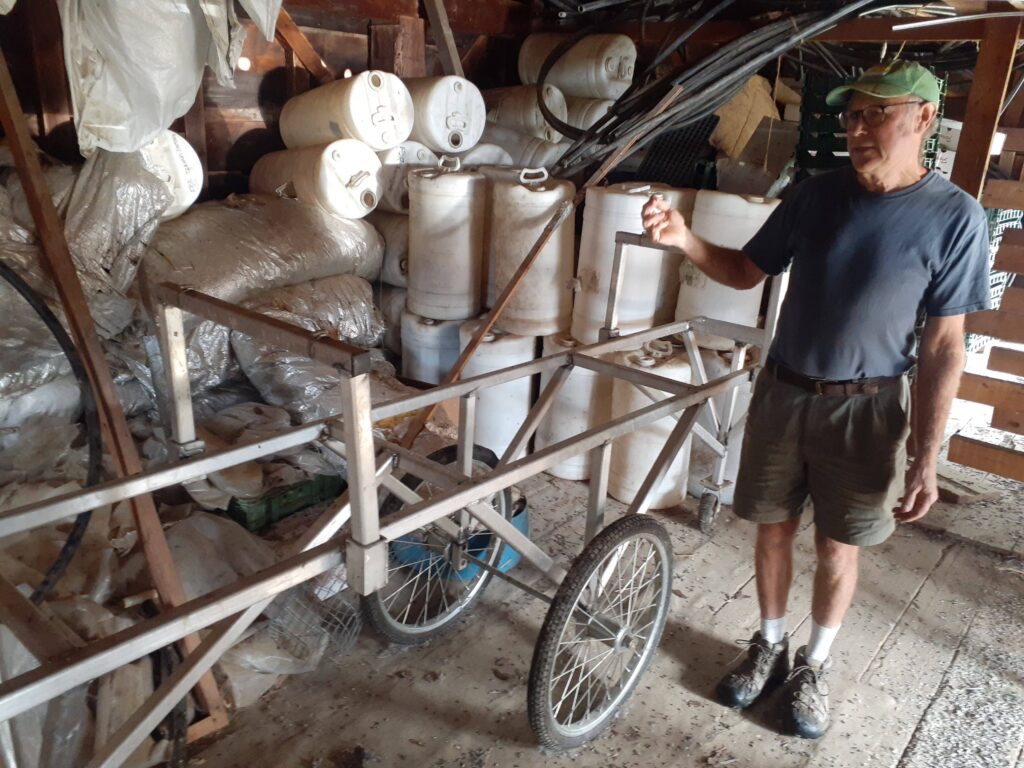
Conveyors – Box / Roller Conveyors & Sliding on Tables
Even in these less-than-ideal situations, where rolling things on a hard smooth surface isn’t an option, wheels and other tools can be helpful. A clean table or box conveyor can serve the dual purposes of a landing zone for a heavy bin of produce and a way to slide or roll it from one place to another without lifting.
Hand carts, dollies, and U-Boats are also a common way to ease the movement of multiple bins of produce between wash-pack and cooler or to market. These are relatively inexpensive solutions that allow you to move more produce with less effort. Some growers customize hand carts with a larger base so it catches a bin just right and allows for a more stable movement of a tall stack.
The goal should be reducing steps and awkward lifts. Think about yourself 20 years from now and give your future-self a break.
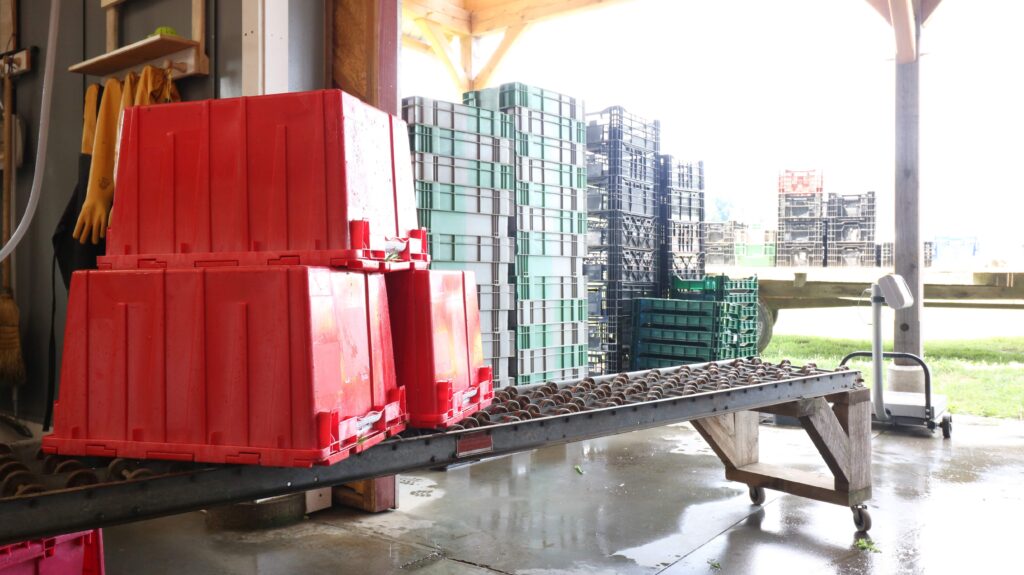
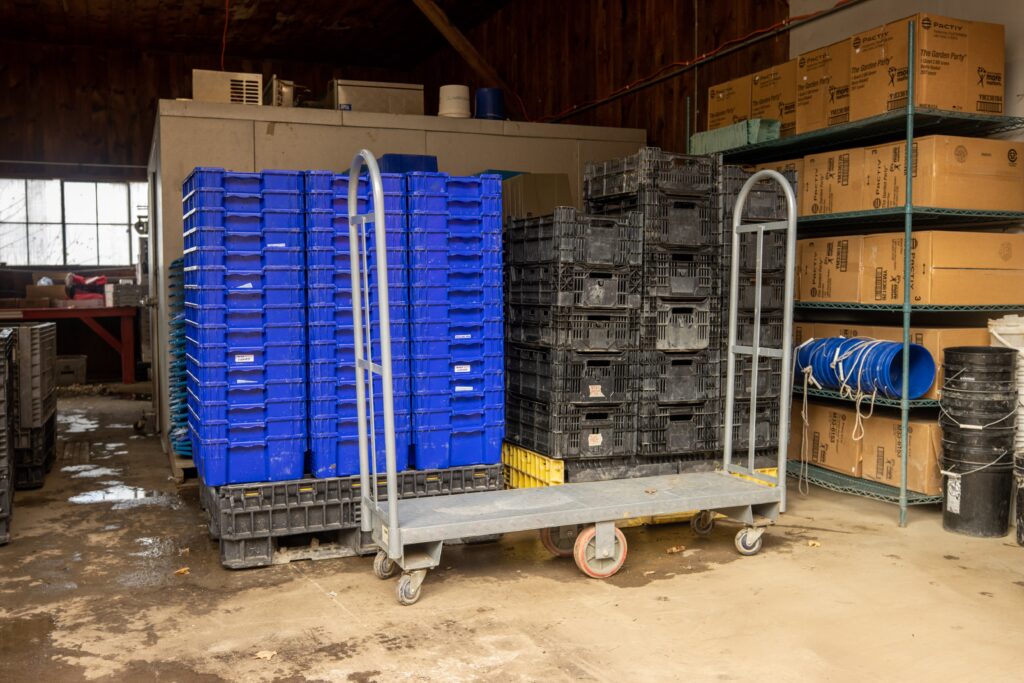
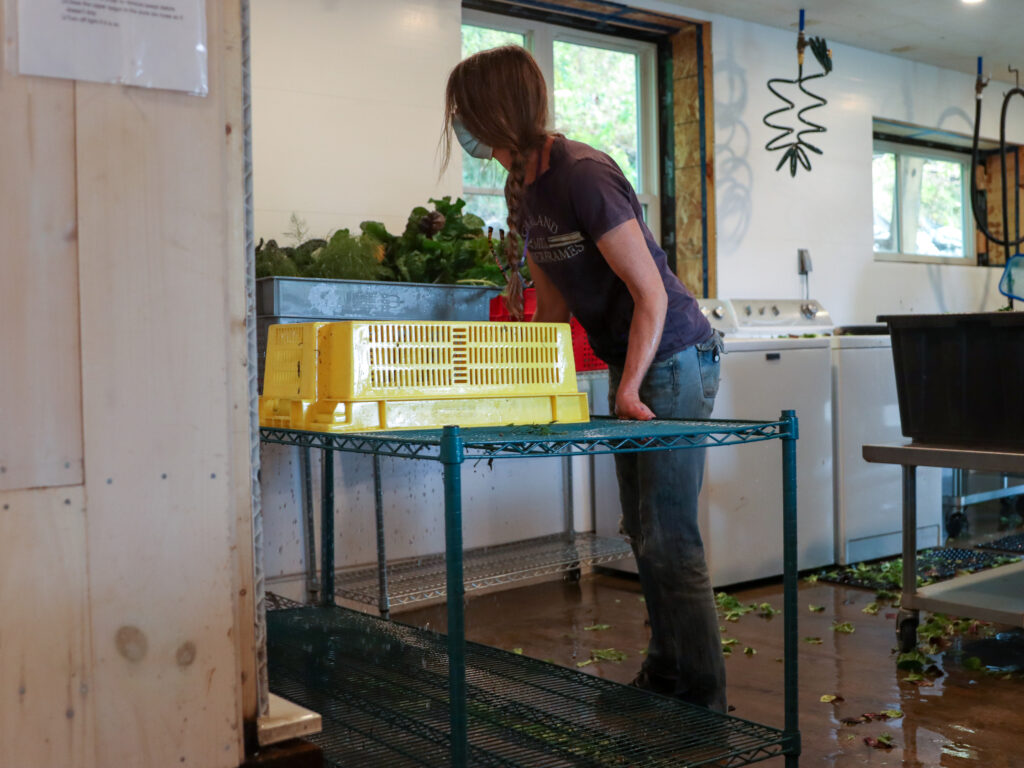
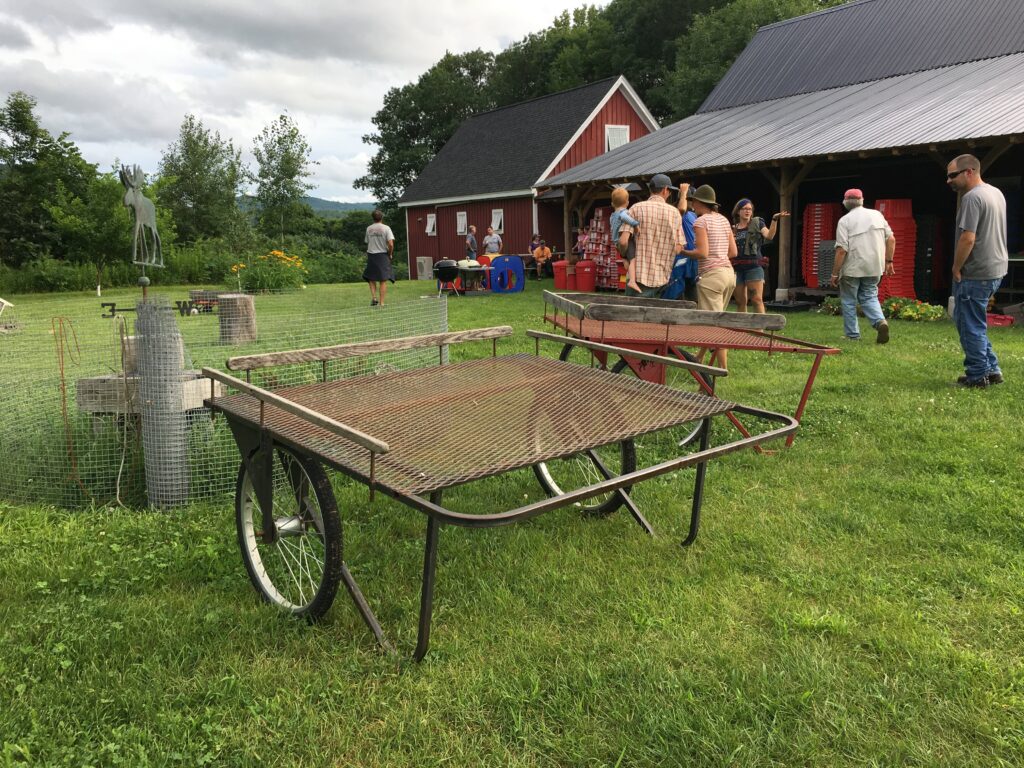
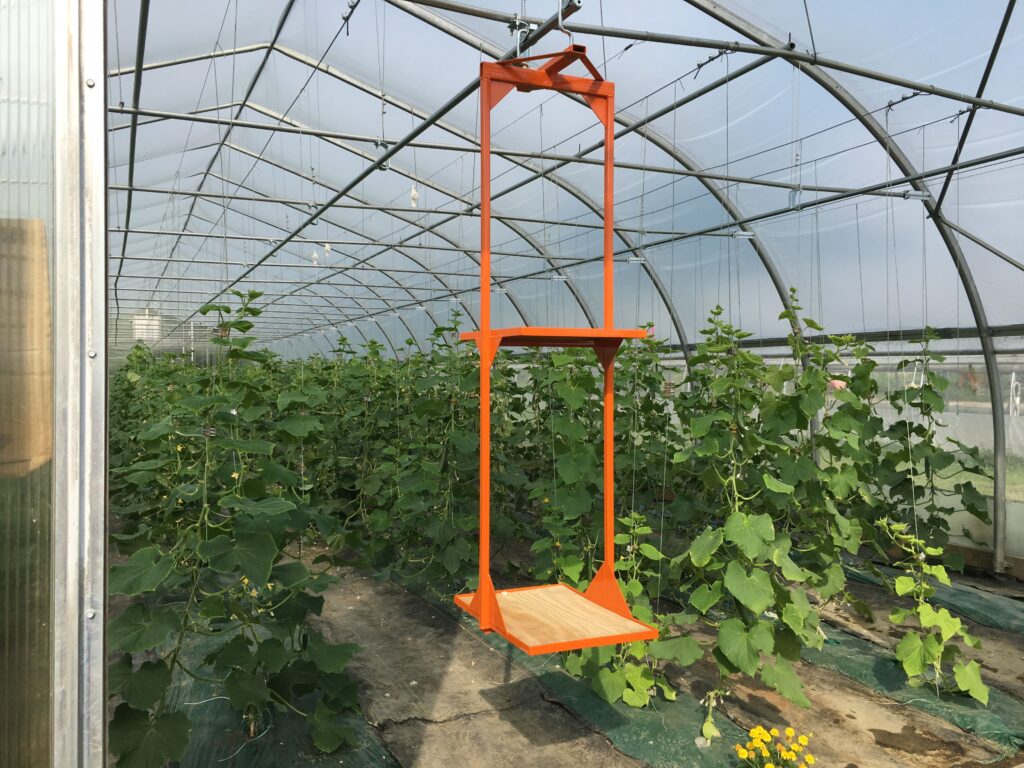
Pallets and Pallet Bins
There may come a time when your farm reaches a scale where palletizing cartons or using 20 bushel pallet bins is appropriate. Melons, fall squash and other winter storage crops all benefit from this approach. Some farms harvest directly into these “bulk bins” and head straight for the curing area (winter squash, onions, sweet potatoes, potatoes) others head right for cold storage (beets, carrots, turnips).
Often referred to as “20 bushel” bins or “macro” bins, these containers have a range of maximum capacity from about 20 to 28 bushels or 650 to 1,100 pounds depending on the bin and the crop. The point is that you are now moving lots of produce in one trip and are no longer hand carrying that load!
Do bear in mind, though, that you are also lifting significant weight at greater and greater heights, using heavy equipment. This is a safety risk and training and procedures should be in place to prevent accidents.
One consideration of scaling into a pallet or bin sized operation from hand carry is the needed space for maneuverability. (for wash/pack planning resources visit: Planning an Efficient and Safe Wash/Pack Area) Typical pallet size is 40×48 inches. It is critical to make sure doorways, hallways, and landing zones account for this increased space requirement of the pallet, the equipment moving said pallet, and a little wiggle room for added ease of handling.
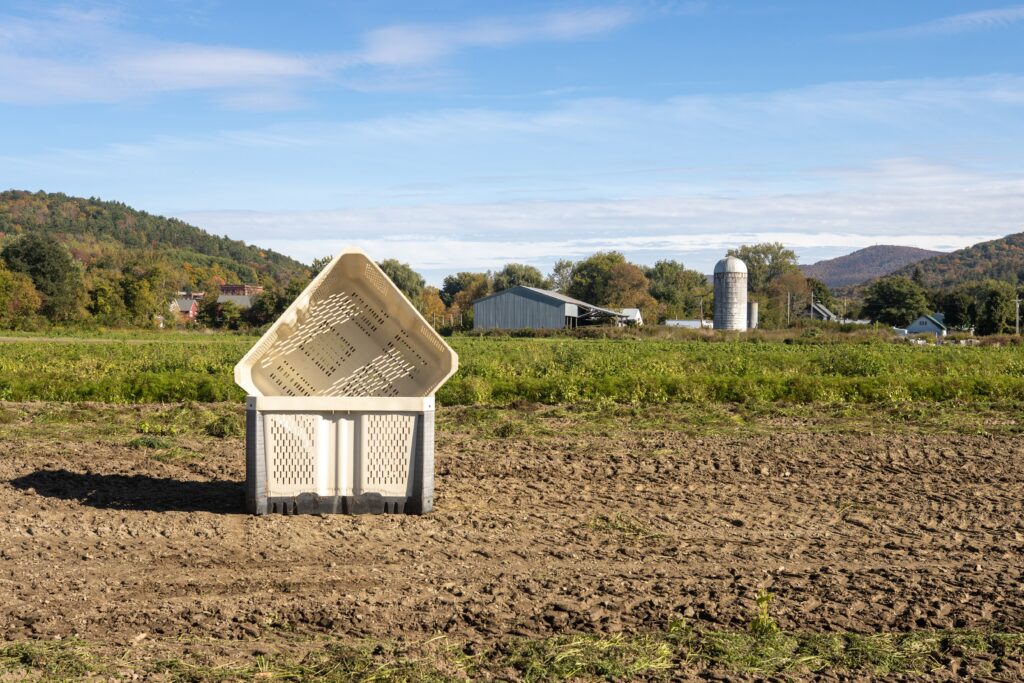
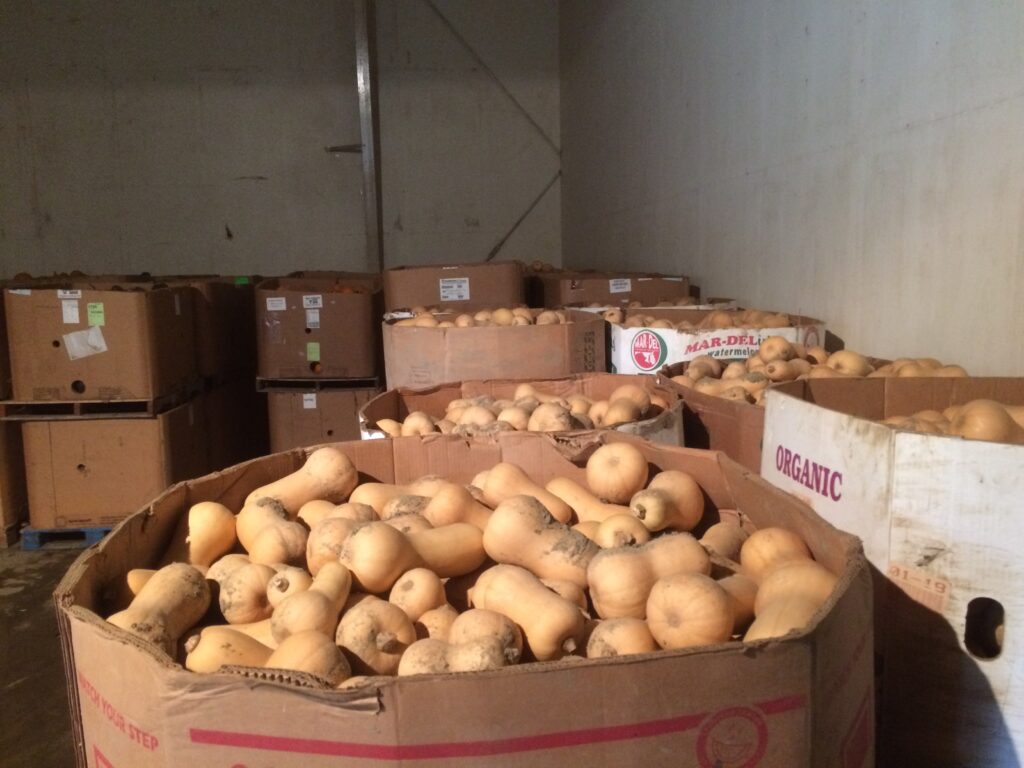
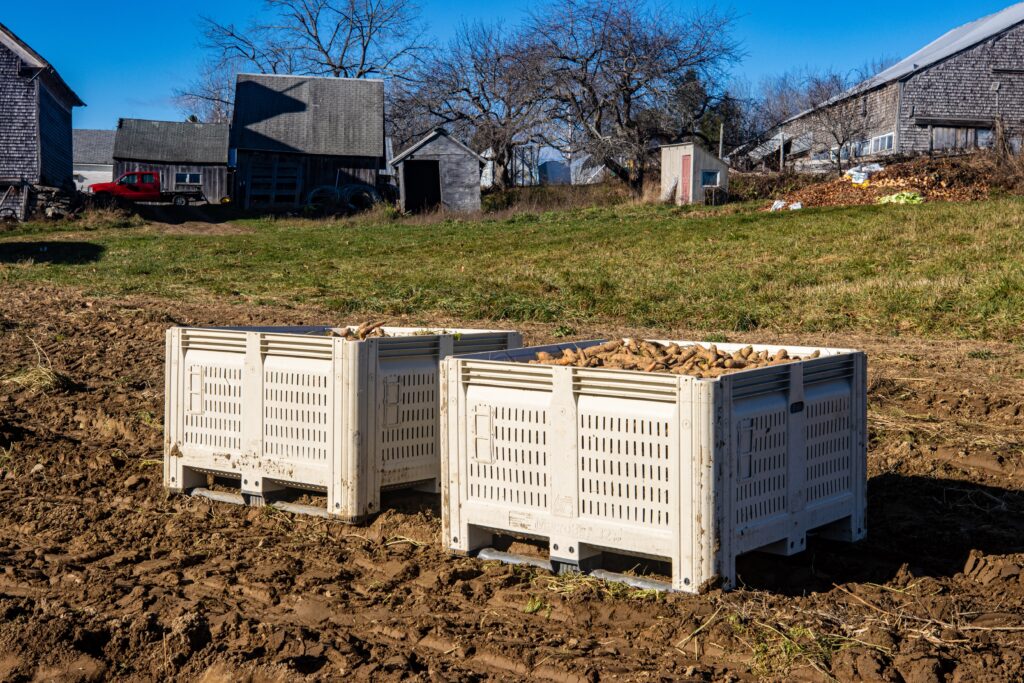
Forks and Pallet Jacks ($400-$1000)
The other feature pallet bins have is an opening between the bottom of the container and the actual floor. This allows a set of forks to be inserted so a pallet jack, tractor forks, or fork truck can lift the bin and move it. Each of these approaches for moving bins comes with costs and benefits.
READ MORE: Pallet Jacks 101 – The Lowdown on Less-Than-Forklift Options for Pallet Handling
Tractor forks ($400-1000) are typically the first tool used when a farm has adopted pallet bins for moving crops. If there is already a tractor on the farm, tractor forks offer an inexpensive way to use an existing tool for a new, important purpose.
Some farms already have these in their toolkit since they are also handy for unloading bulk supply deliveries. The one challenge that this solution introduces is agility, especially related to turning in tight spaces. Often the pack shed hasn’t been designed or built for tractor movement or, even, using pallet bins.
Forks that clamp onto the bucket loader are the cheapest accessory to enable the handling of pallets or bins, but the visibility of the fork tips is limiting and often requires a second set of eyes to guide the operator.
Dedicated forks feature a more open design, improving visibility and lift capacity as it brings the lifted mass closer to the tractor.
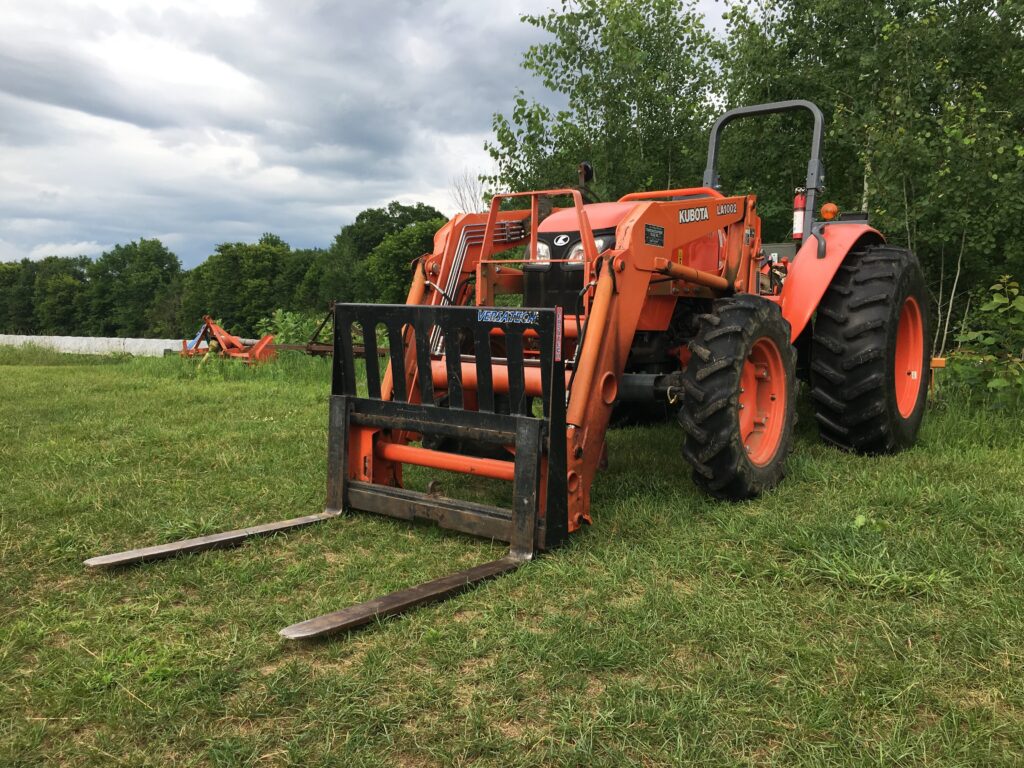
Pallet Jacks $400 and Electric Pallet Jacks $2700
Pallet jacks ($400) offer increased maneuverability over tractor forks but are generally limited to indoor use on relatively smooth floors. They typically have smaller wheels integrated into the forks which limits where they can be easily used. An operator pushes or pulls the pallet jack like a cart, and the handle on the operator side of the jack is used to pump the hydraulic lift jack that raises the forks. Most pallet jacks offer a very tight turning radius since they are not much bigger than a pallet themselves.
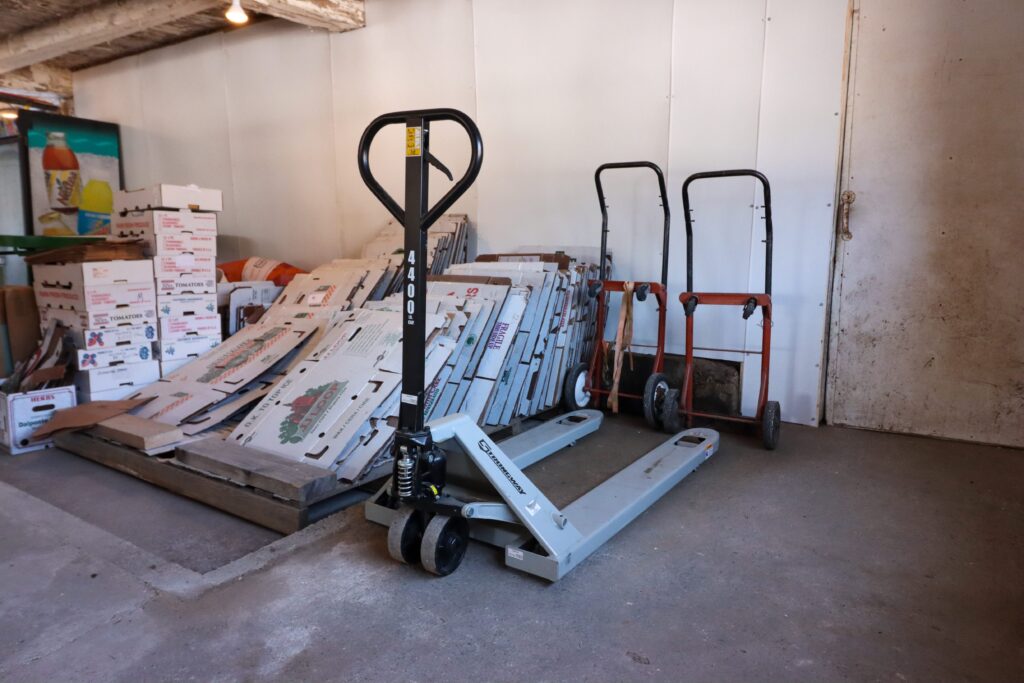
Electric pallet jacks ($2,700) make this even easier and more efficient on the operator using rechargeable batteries to aid the lifting and movement.
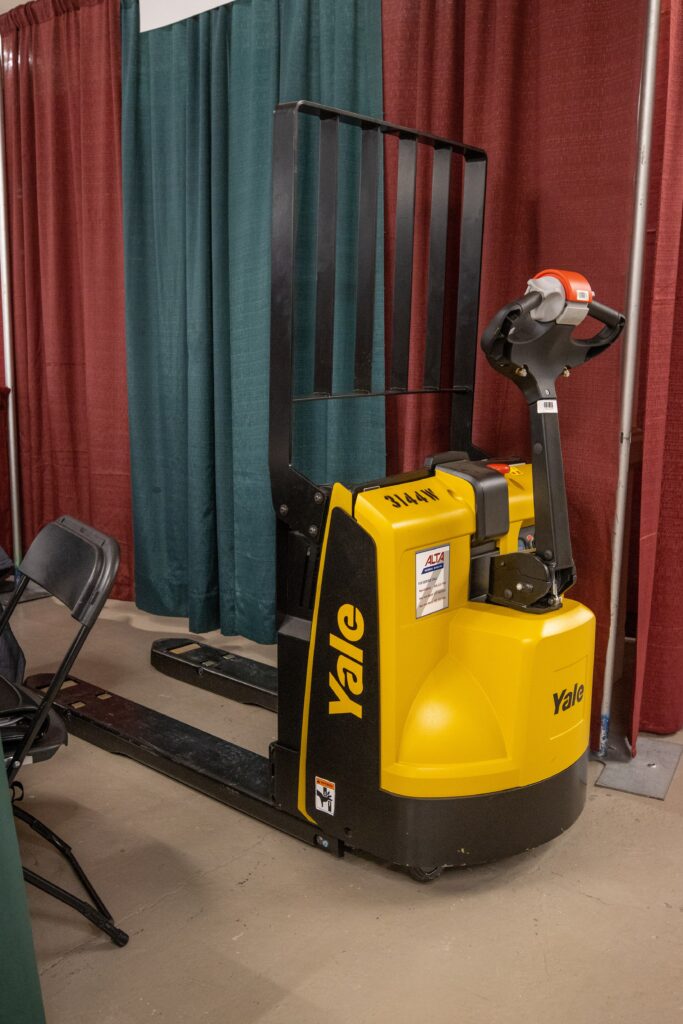
Pallet Stackers (manual / hydraulic $1,500-1900) and Electric Stackers $5300
A key skill or technique used with tractor forks and pallet jacks is stacking bins in a relatively open area with the tractor forks and using the pallet jack to roll them into the tighter spaces such as coolers. This adds a step, but think about the number of steps a hand carry approach would involve for that amount of produce. Care should be taken with stacked bins, of course. Two stacked pallets is quite a bit of weight and an uneven floor or sudden unexpected movement can be hard to control.
Pallet stackers are also available in both manual ($1,500-1,900) and electric versions ($5,300), though they are less common on farms than in warehouses. These come in a variety of models with distinctive features. The key feature is that they can lift pallets up to 15 feet high for stacking or placing on racks. Some companies even make a rough terrain pallet stacker which would be great for farms that don’t have a perfect loading area.
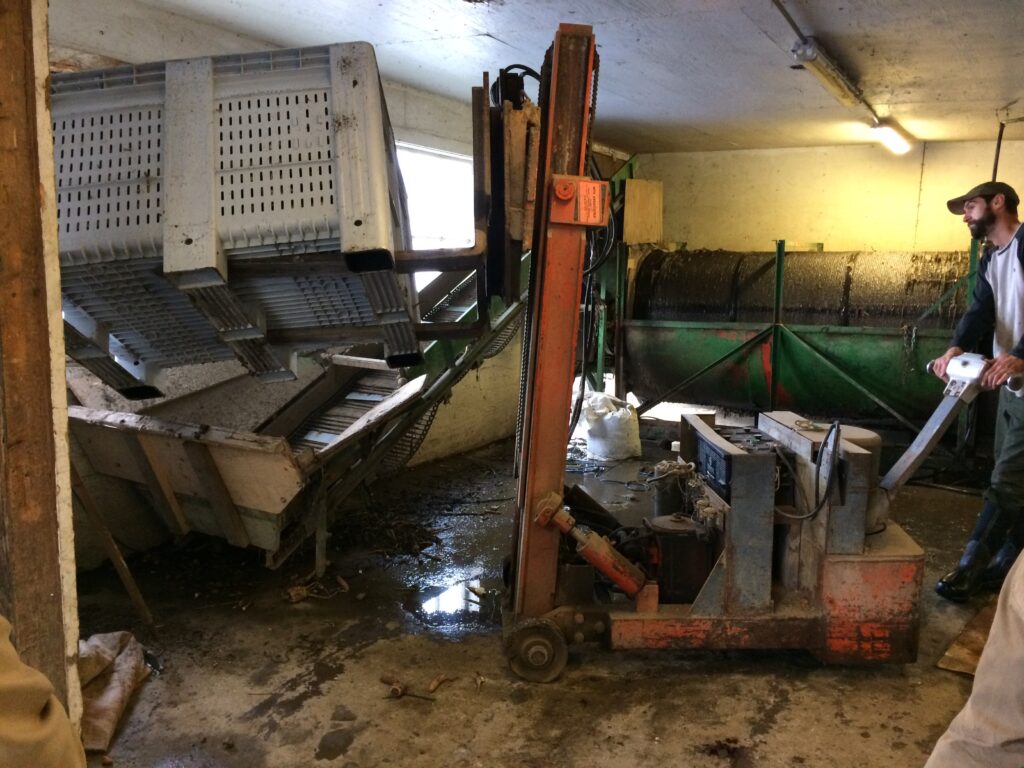
Riders ~$5300
Both pallet jacks and pallet stackers come in models that have small seats or standing platforms that allow for the operator to ride. These “rider” models are significantly more expensive but could be a good option if pallets are being moved over long distances.
Fork trucks
There’s a reason fork trucks are the standard tool in warehouses. They have large lifting capacity, can raise loads high, and offer relatively easy movement of lots of product with minimal operator effort.
For most small and medium scale farms, they may be too much. When compared to a pallet jack or stacker, they have a larger turn radius and require more backing space. Since most produce wash pack spaces are retrofitted into existing buildings and/or built on a super tight budget, there’s often not enough to justify lots of empty space that is only used by maneuvering fork trucks.
That said, farms doing a significant amount of wholesale or in-house retail packing may find the capacity of a fork truck irresistible and valuable.
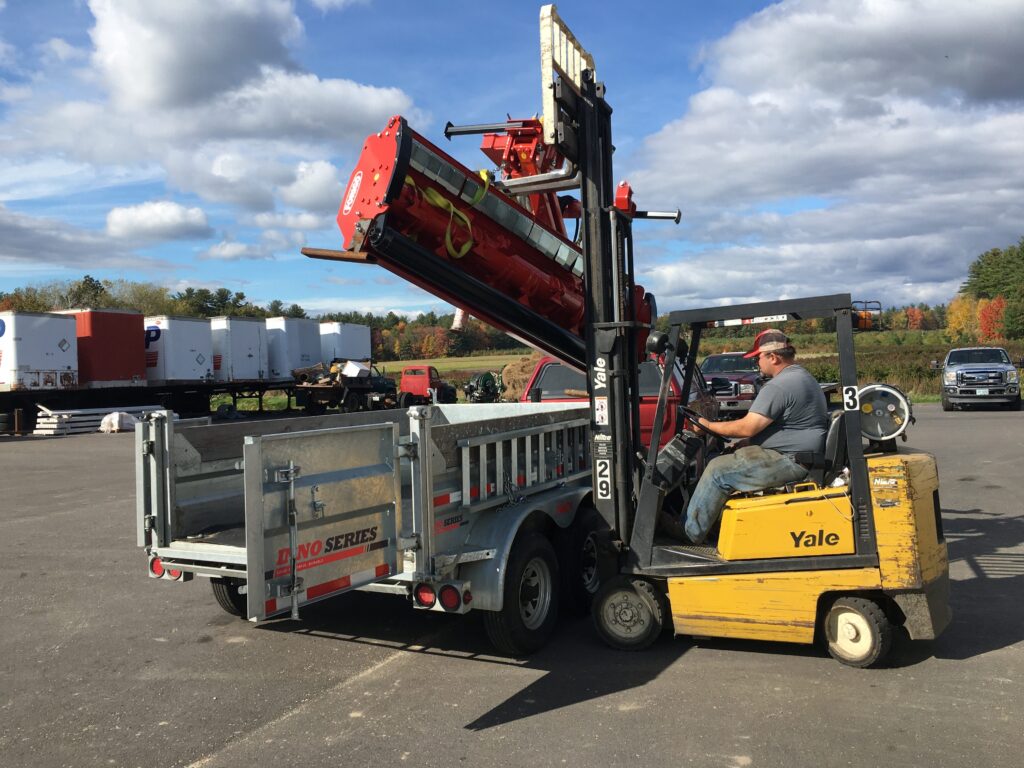
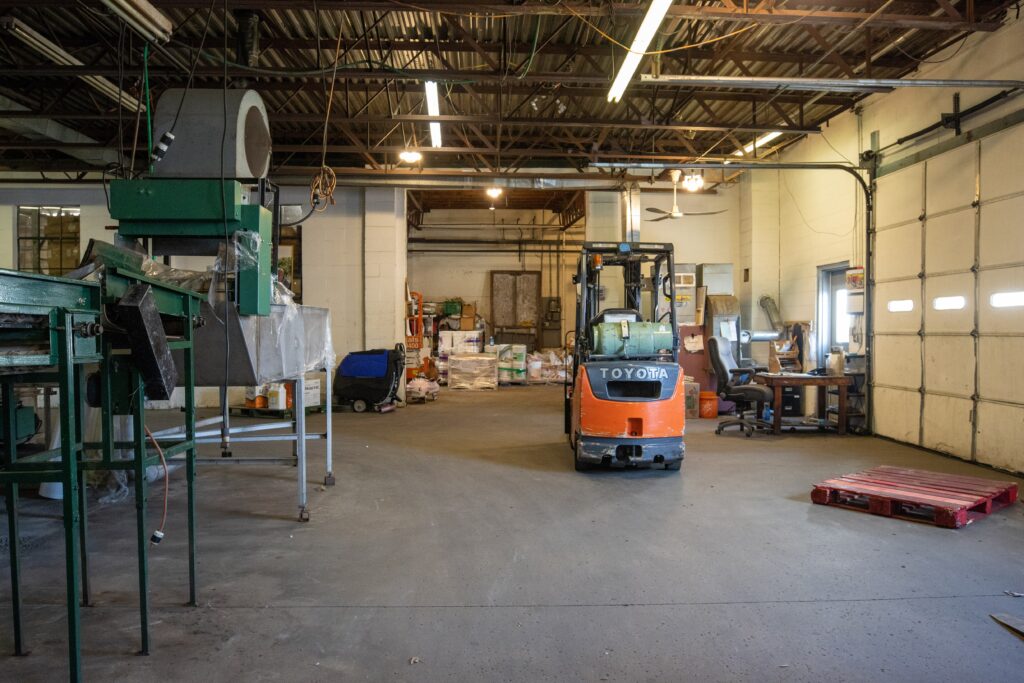
Articulating Forks
Fork trucks, pallet jacks, and stackers are available with articulating forks. These forks can rotate from straight-ahead to sideways which reduces the turning required to grab or place a pallet of to the side of the travel lane. Some forks can also be rotated to dump a pin of produce.
4×4 Handlers
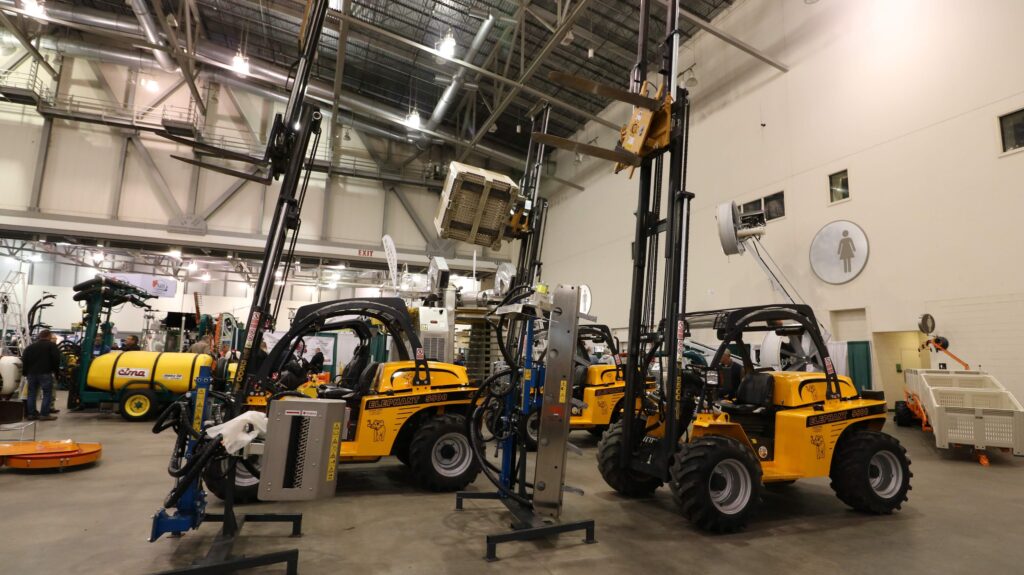
Off-road fork trucks are an option if gravel terrain is needed to be traversed frequently. Skid steers, or track loaders work well too and may already be on the farm and be a multi use tool.
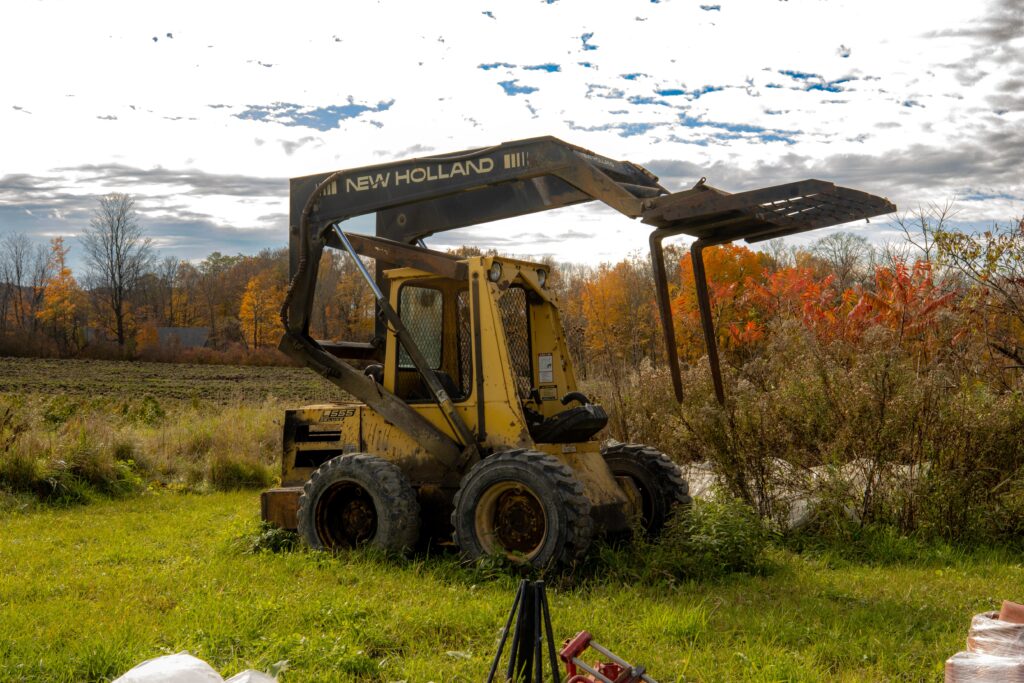
Used and New
As with most farm equipment, any of the options above can be purchased new or used. The prices noted above are for new options and may be subject to change. Maintenance of lifting and moving equipment should be added to the annual schedule and may best be served by an outside service company on contract if a more sophisticated or specialized option is chosen such as a fork truck.
Missing something?
Do you have a great solution to moving things around the farm? Feel like we’re missing something? Let us know so we can add it as an example for others.
Acknowledgements
This project was supported by the Food and Drug Administration (FDA) of the U.S. Department of Health and Human Services (HHS) as part of a financial assistance award 02200-FSMA-24-01 totaling $30,000 with 100 percent funded by FDA/HHS. The contents are those of the author(s) and do not necessarily represent the official views of, nor an endorsement, by FDA/HHS, or the U.S. Government.