Kate Donald began farming at Stout Oak Farm in Brentwood, NH in 2012. As the farm grew she quickly realized they could only handle one, or maybe two infrastructure projects at a time. Much of these improvements went into production practices, and greenhouses that clearly penciled out to be wise investments in the farm. Now, 10 years later, the dream of having a more comfortable wash/pack space became a reality.
Background Info
- 5 Acres of production
- Markets: On-farm store, CSA, and Wholesale through Three Rivers Alliance
- Previous wash pack was under two 10’x20′ carport tents
- New wash space is 20’x40’
- Use of spray tables, and dunk tanks for washing produce
Overview of Construction
Amber Wilson, wash/pack manager at Stout Oak, served as the project manager for this infrastructure upgrade. She solicited ideas from the team to figure out what would work best for their farm, and communicated with the contractors to see this project through.
The crew was motivated to keep working outdoors, which is what brought them to farming in the first place, but agreed some protection from the elements would be nice. A key goal was to to minimize the maintenance headache of constantly securing the carports they were working under previously. When discussing the alternative of renovating the old dairy barn or staying outside Kate reflected, “We felt like the washing step has been able to happen outdoors, and we really like that. The open air, the natural light. We wanted to recreate that outdoor feeling” that would be inhibited in the barn with low ceilings, full walls, etc.”
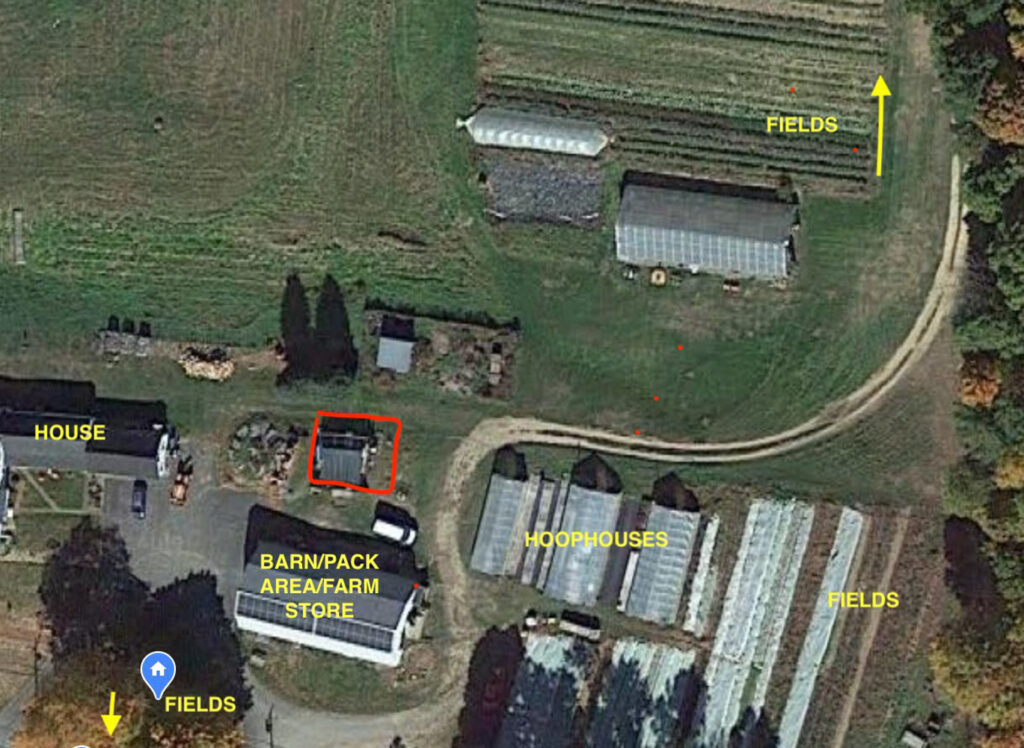
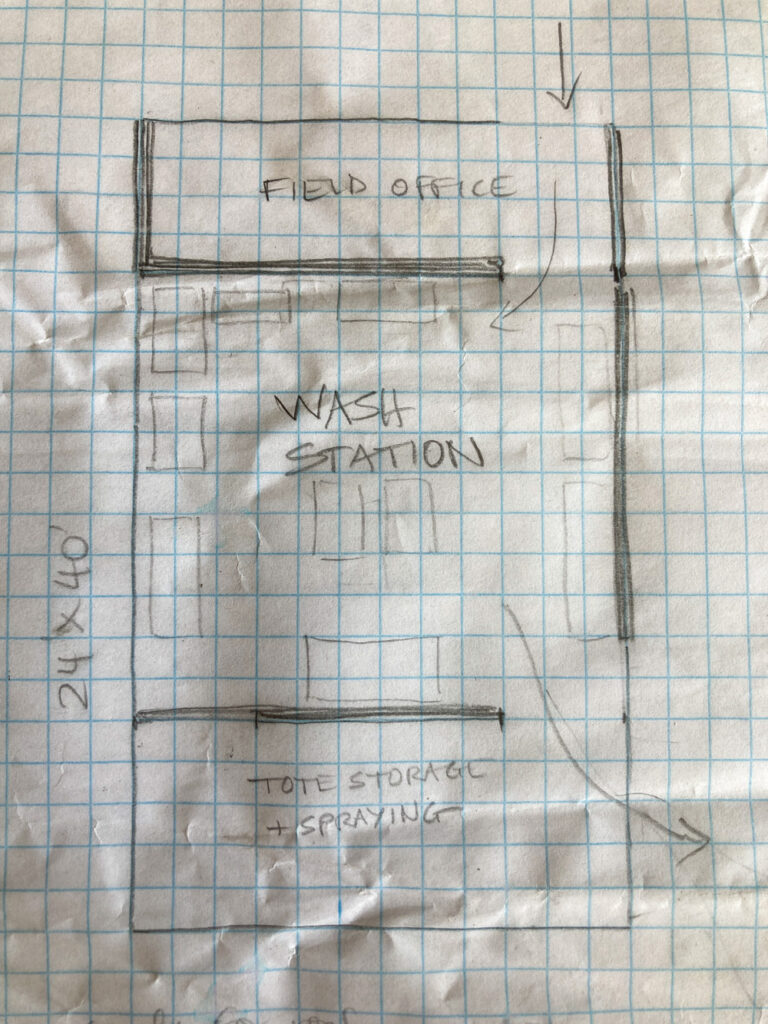
Together, they sketched out a design for a 20’x40′ pavilion and reached out to the UVM Extension Ag Engineering Team to discuss the plan. This conversation helped to clarify key features like keeping the layout of wash equipment flexible, and adding a centrally located drain to manage the water flow.
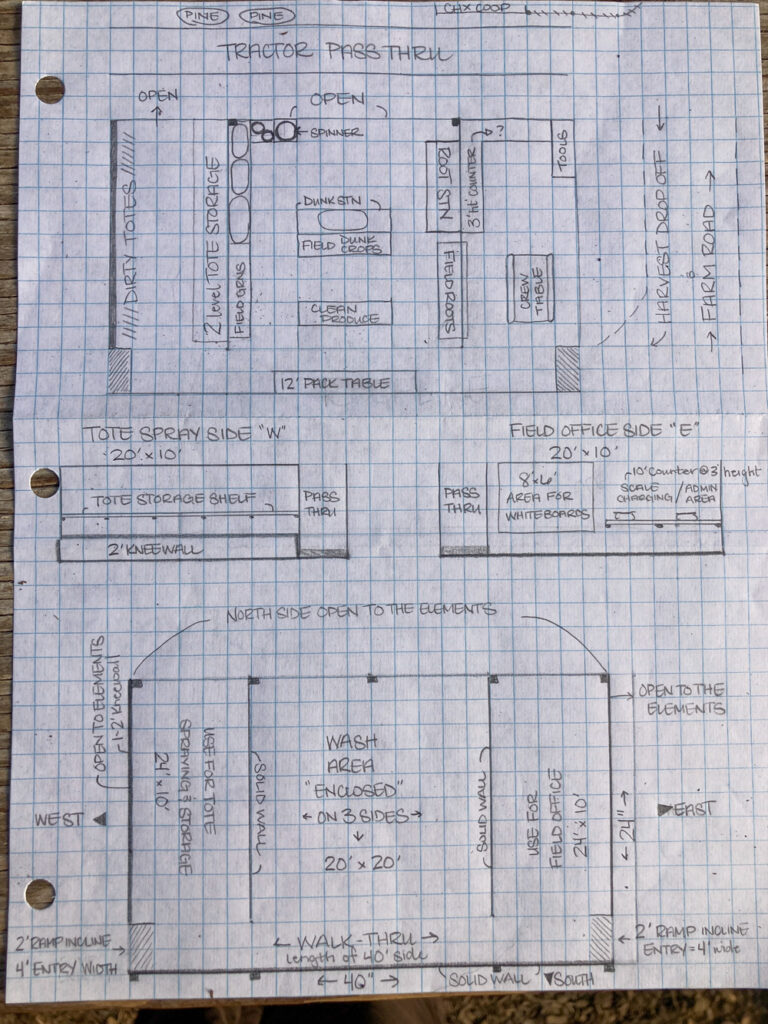
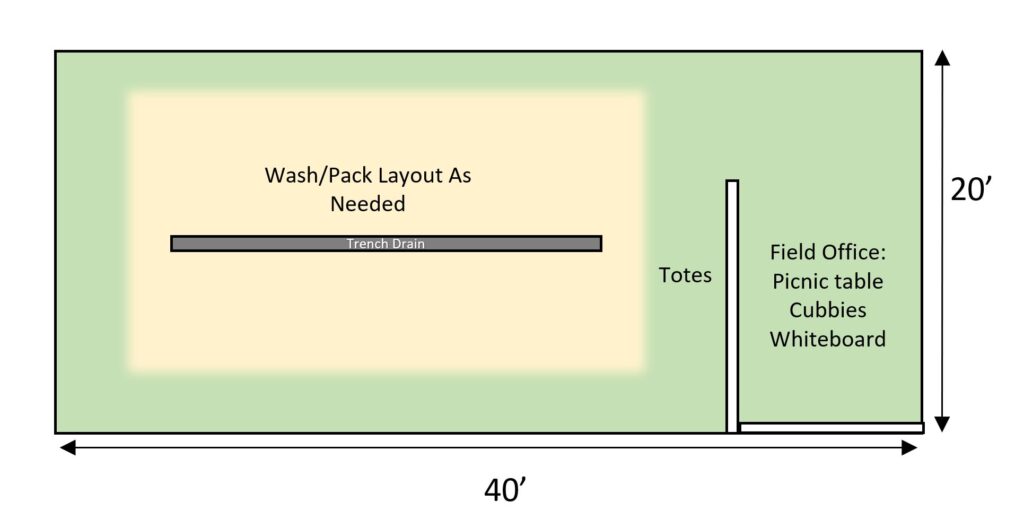
The Pavilion
The foundation is a slab made of fiber-reinforced concrete and features precast concrete piers installed to support the posts.
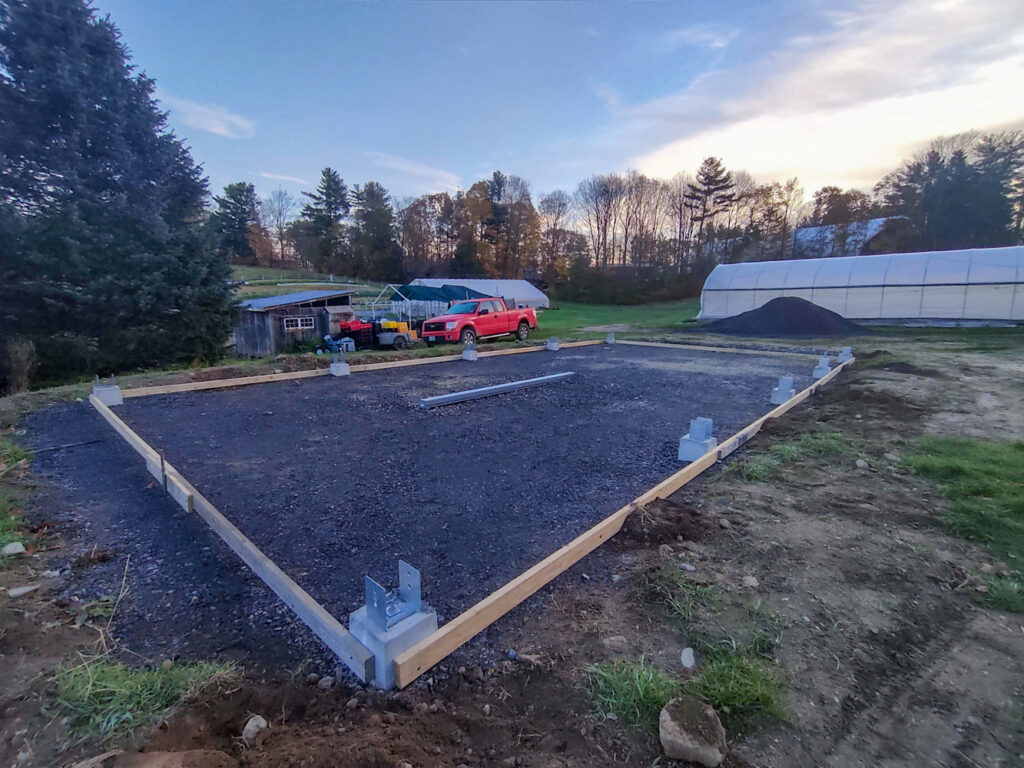

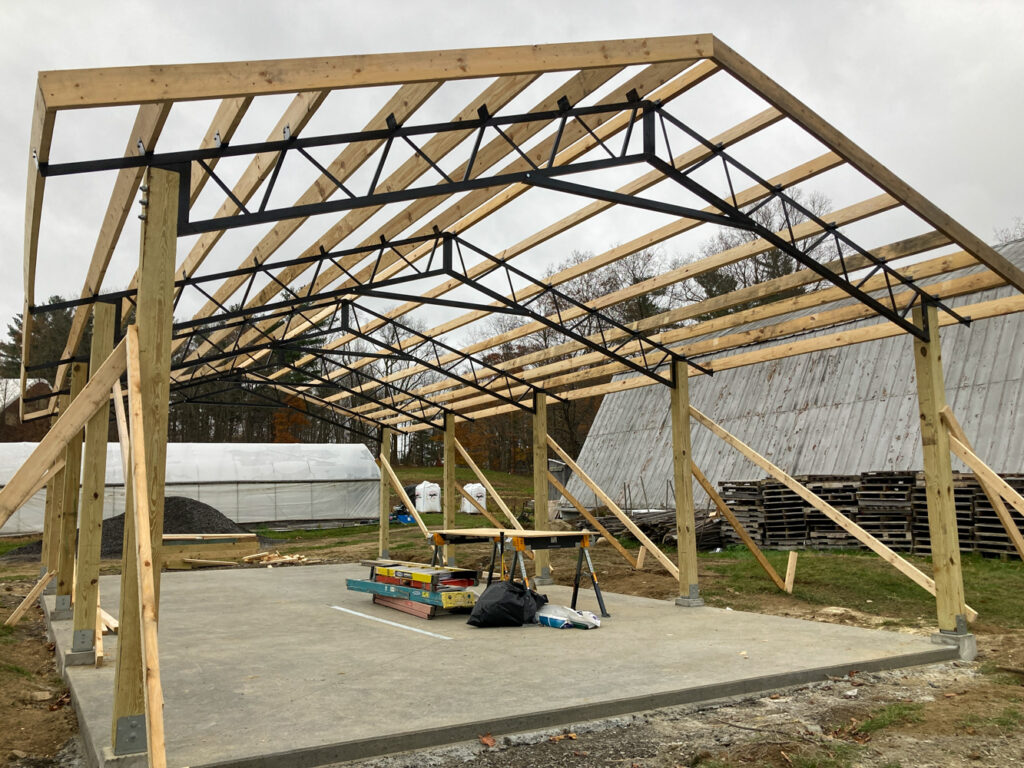
This open pavilion structure is assembled with a steel truss kit that were built to order by Strouds Building Supply (Morganton, NC) and was delivered on one small truck load. Trusses are bolted in the center and went up in a few days. A local contractor did the building and assembly for them.
Project Cost: $40,000
$12,000 Building materials (Posts, trusses and roofing)
$10,000 Concrete
$10,000 Contractor labor
$8,000 Sitework
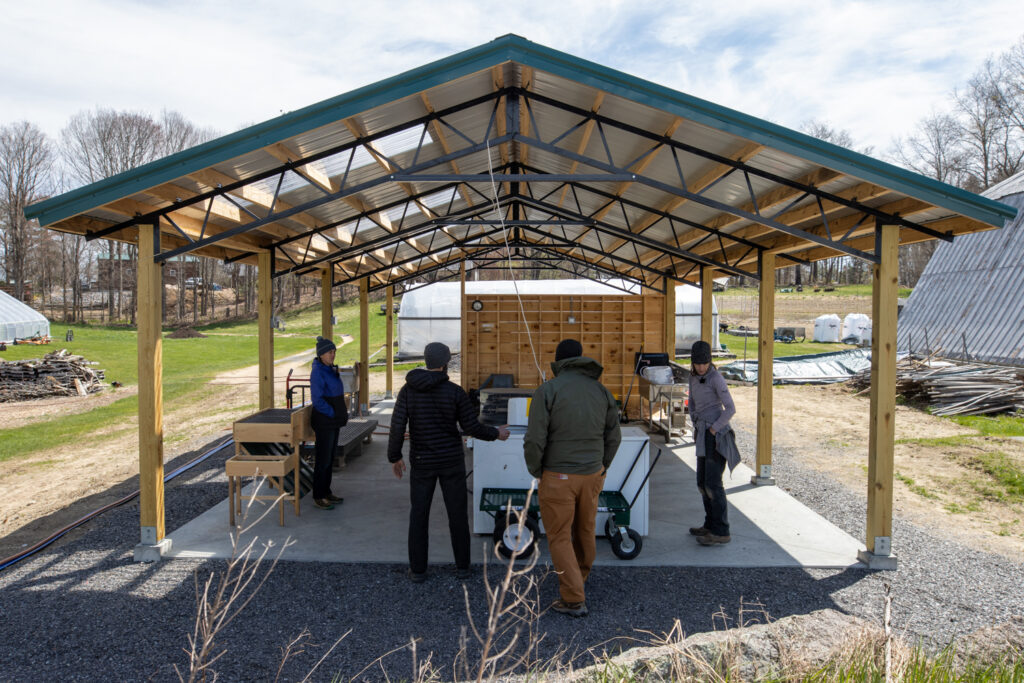
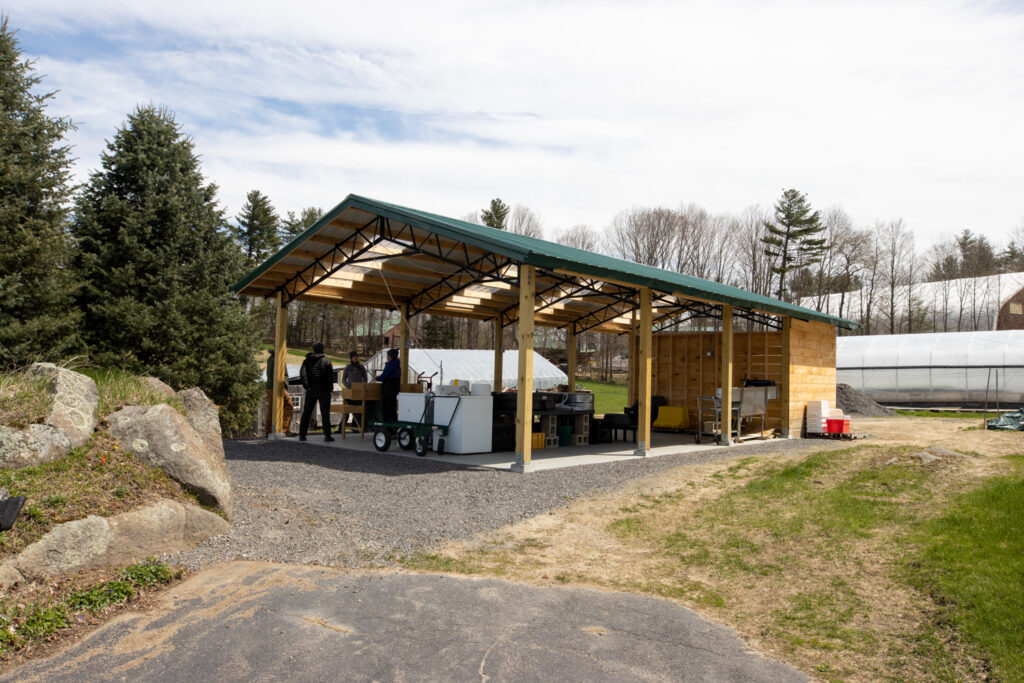
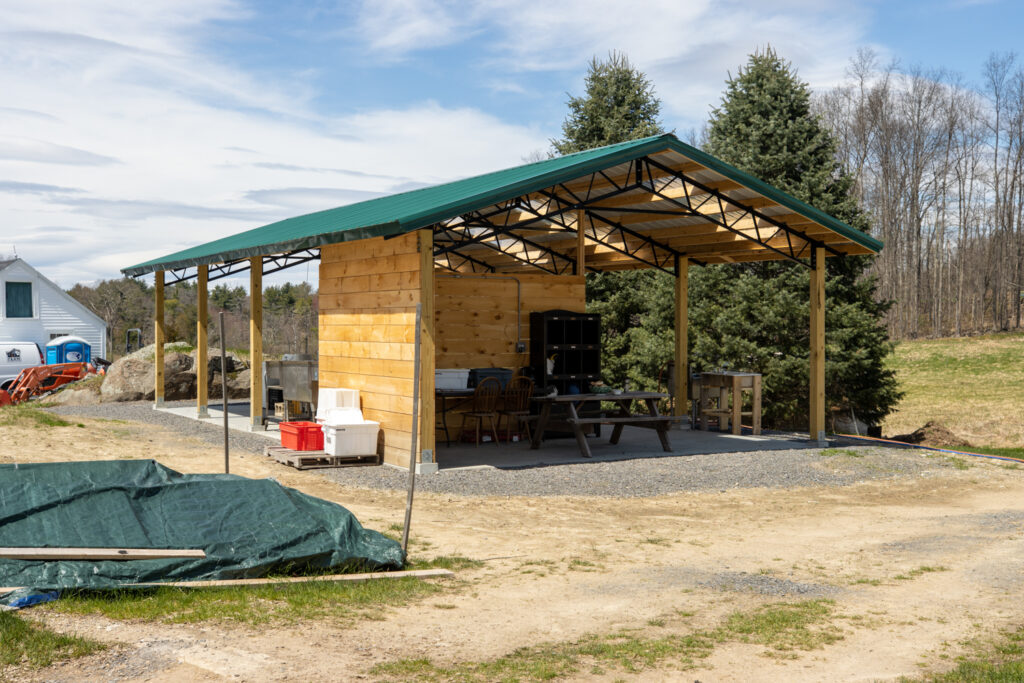
Favorite Features: Size, aesthetics, and a structure that requires minimal maintenance, upkeep or attention compared to canopies or temporary carports.
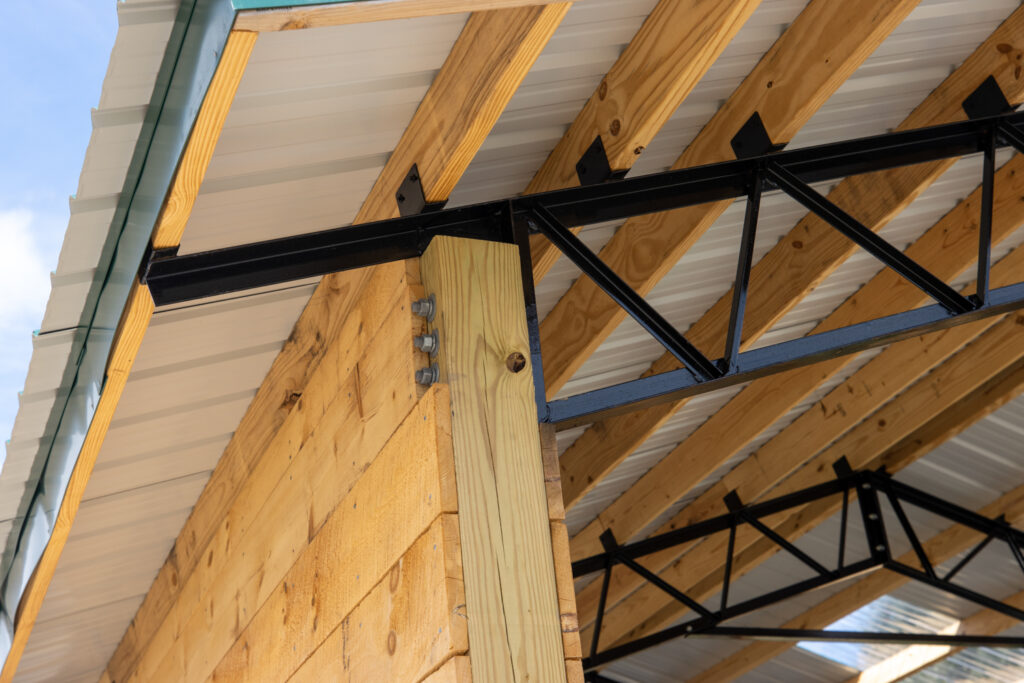
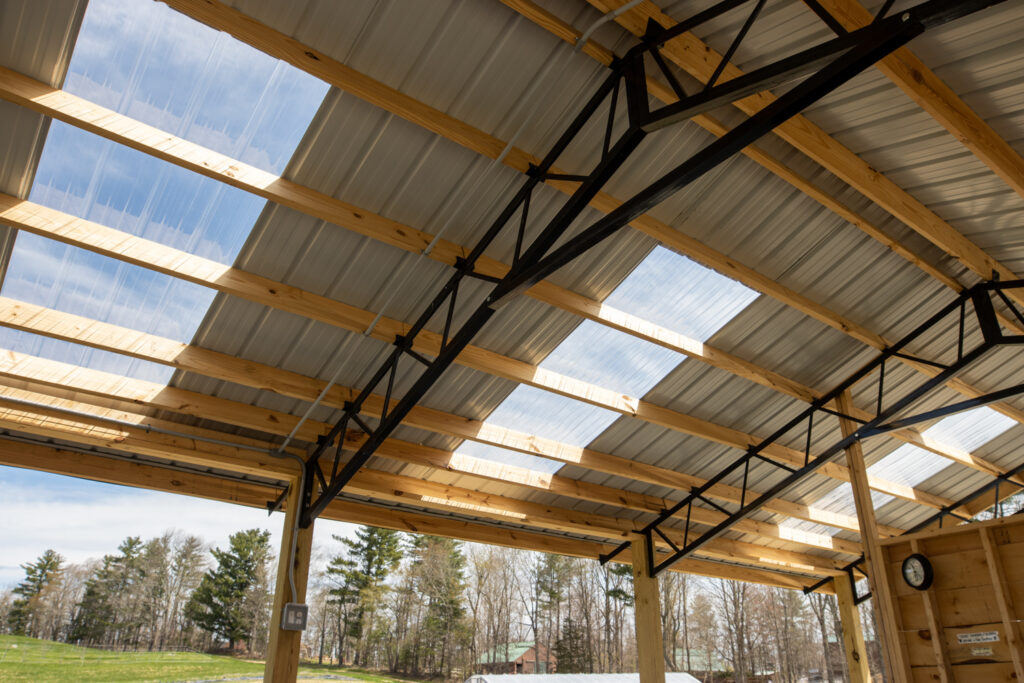
Gallery
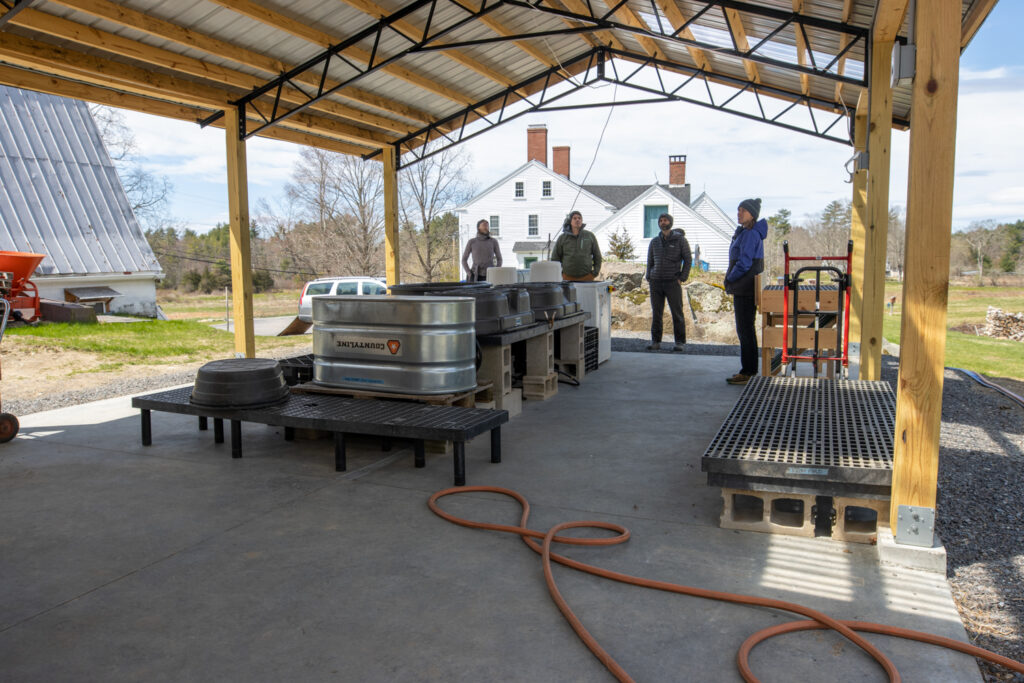
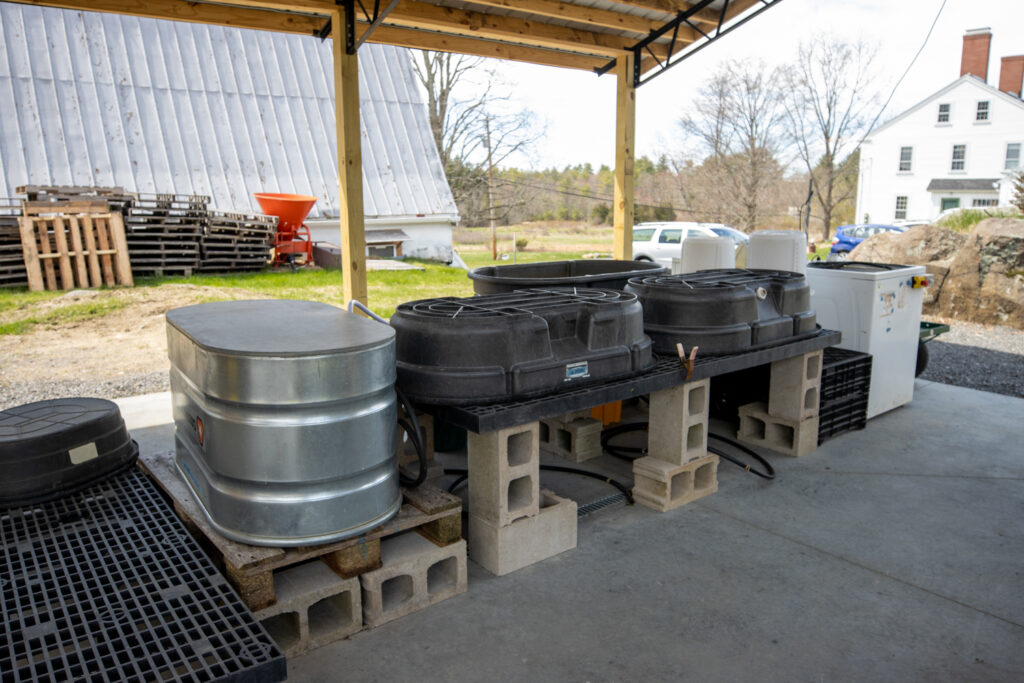
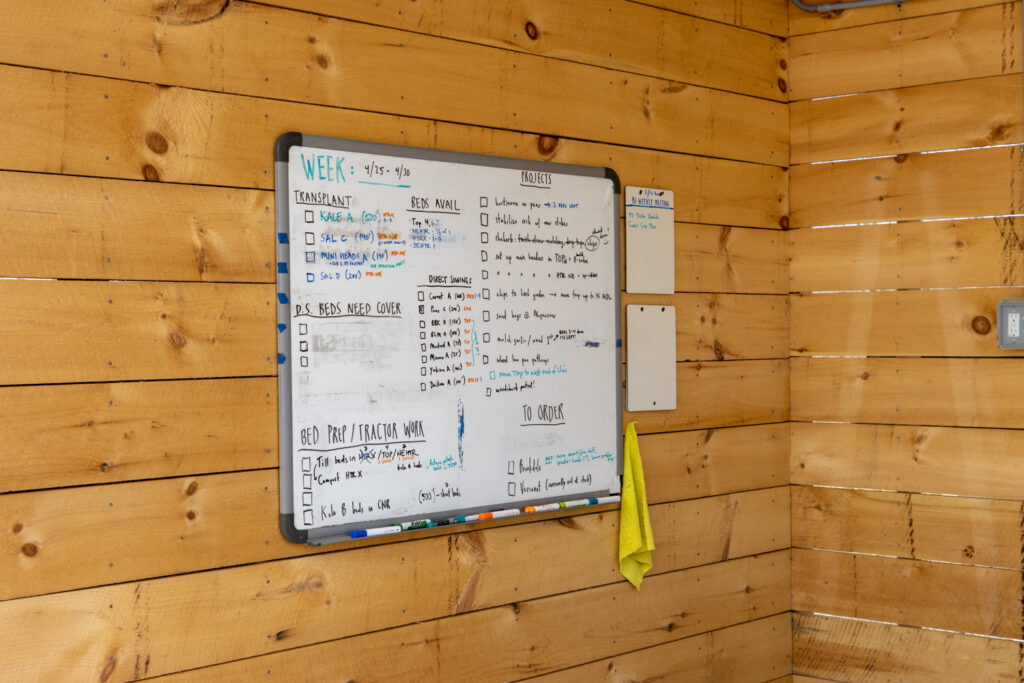
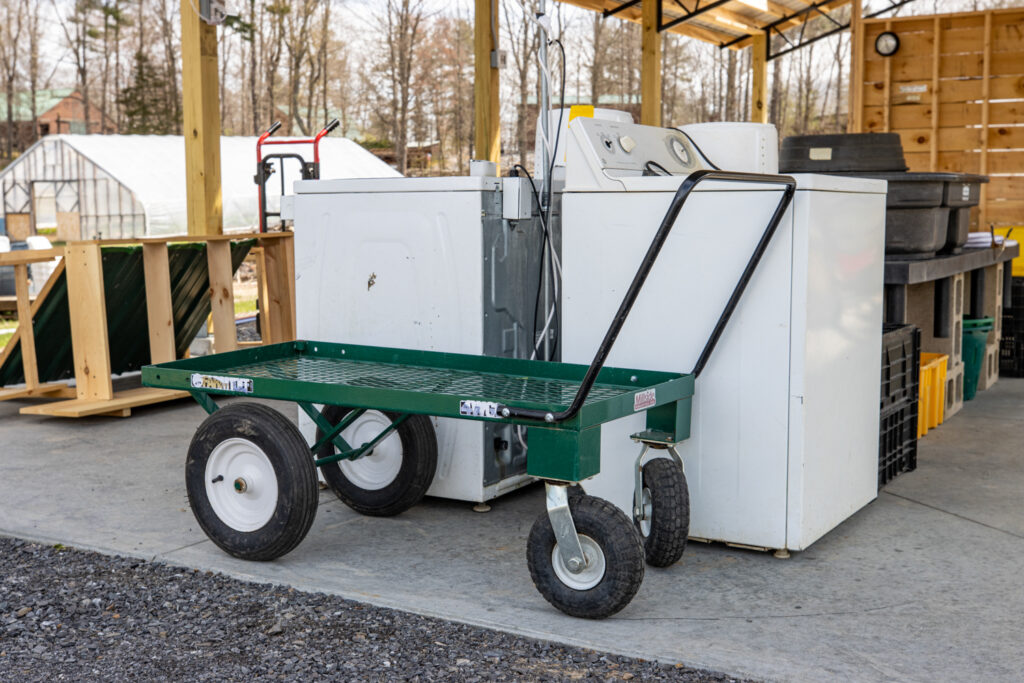
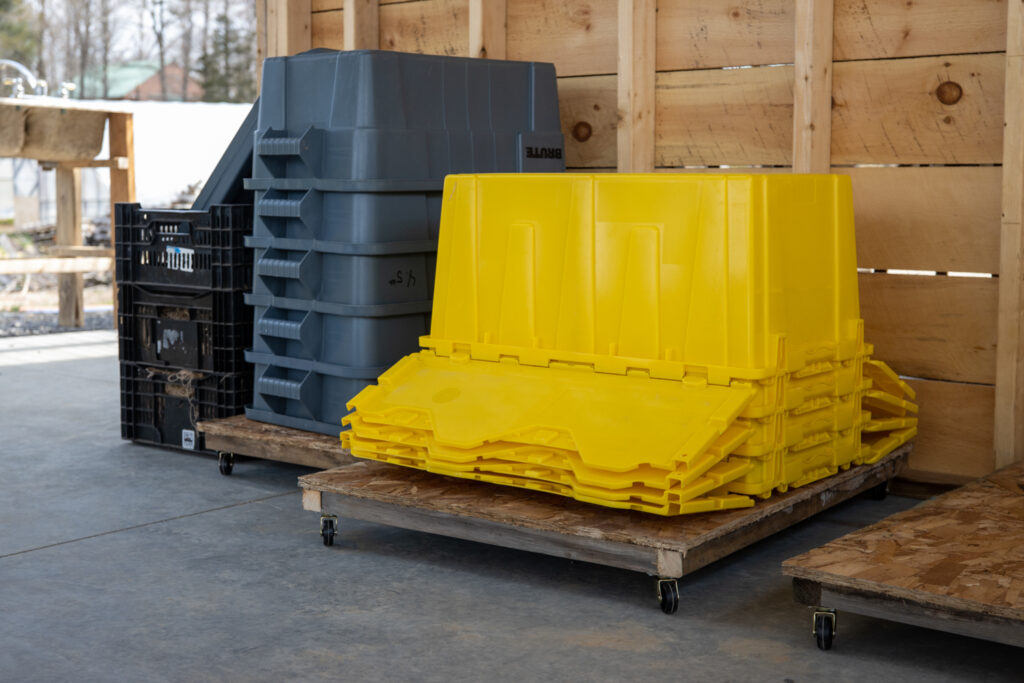
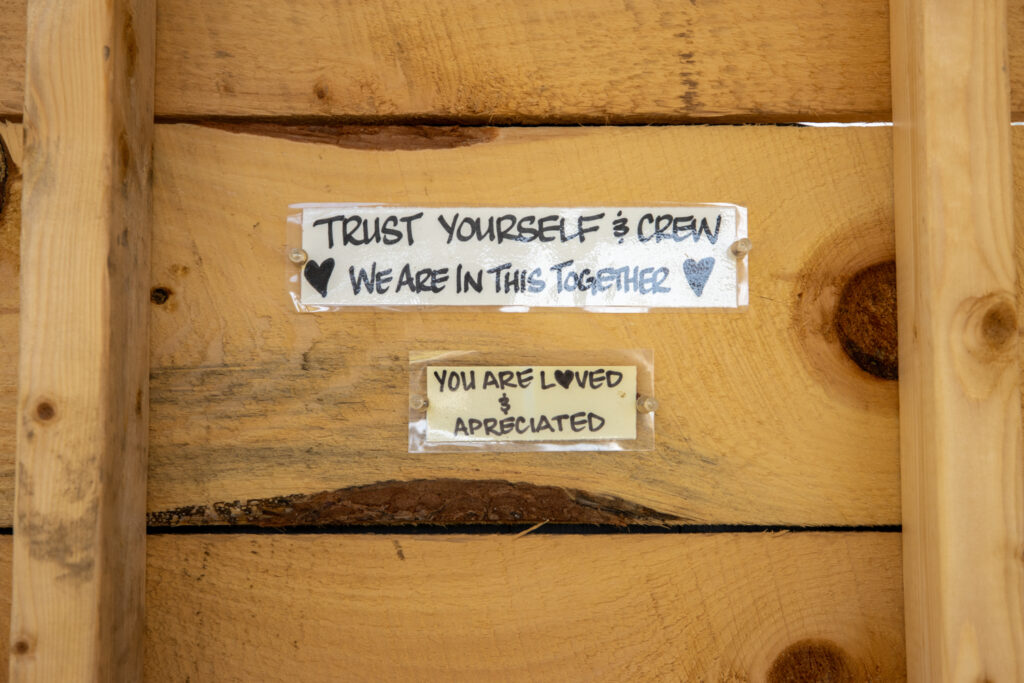
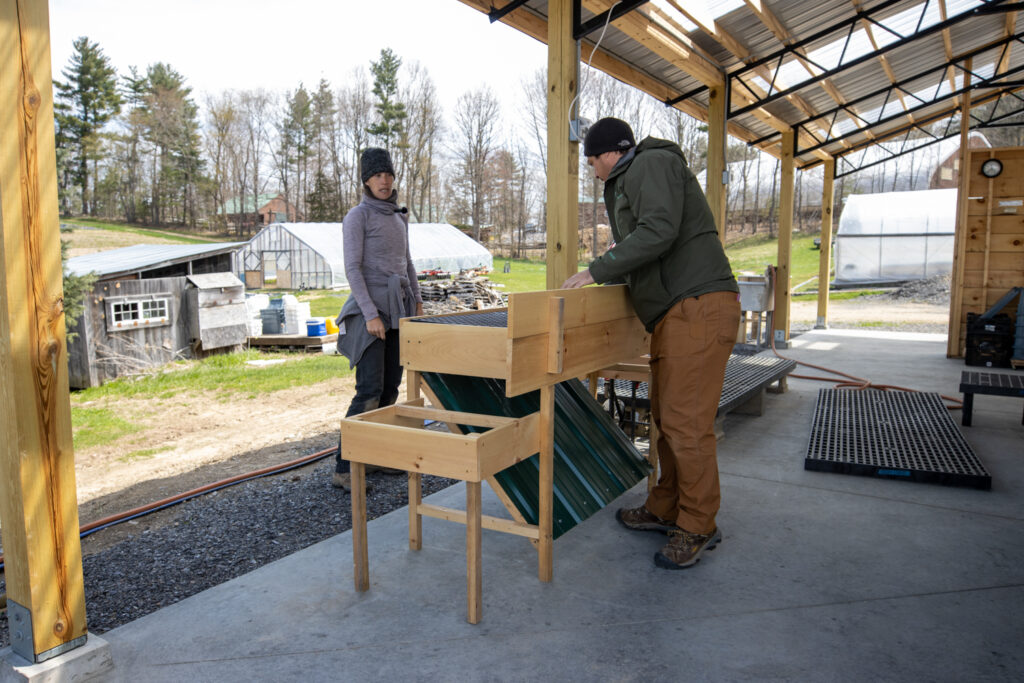
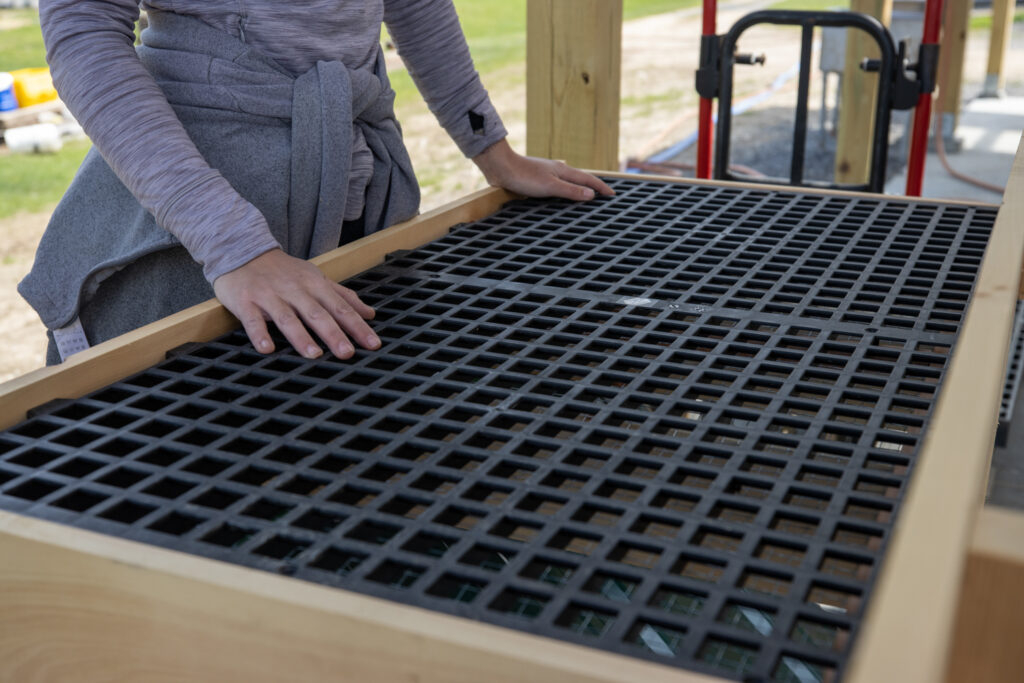
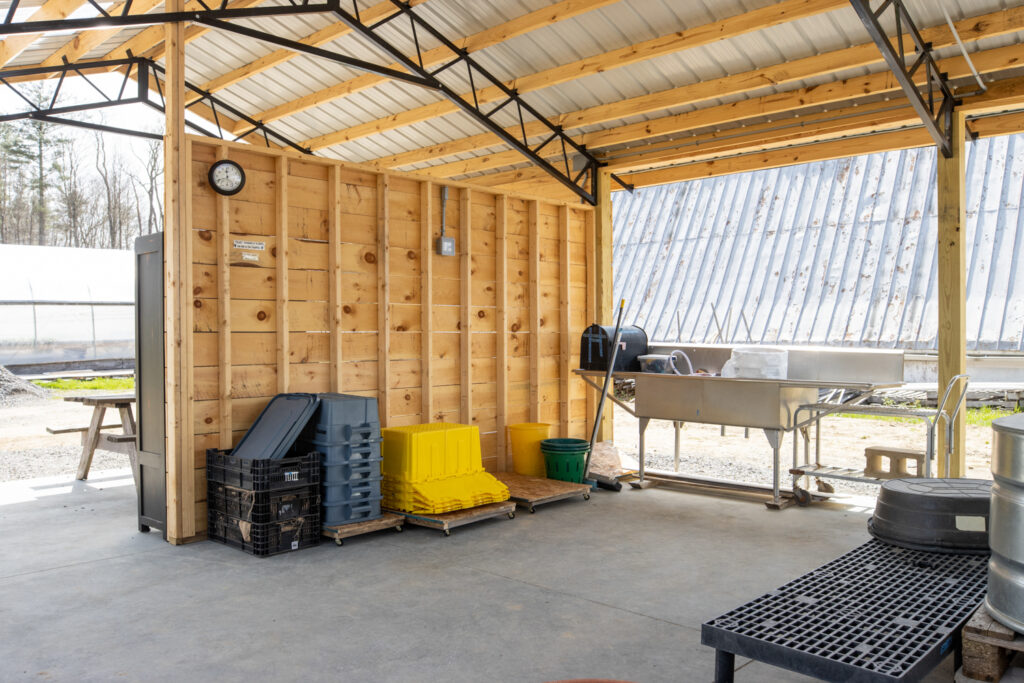
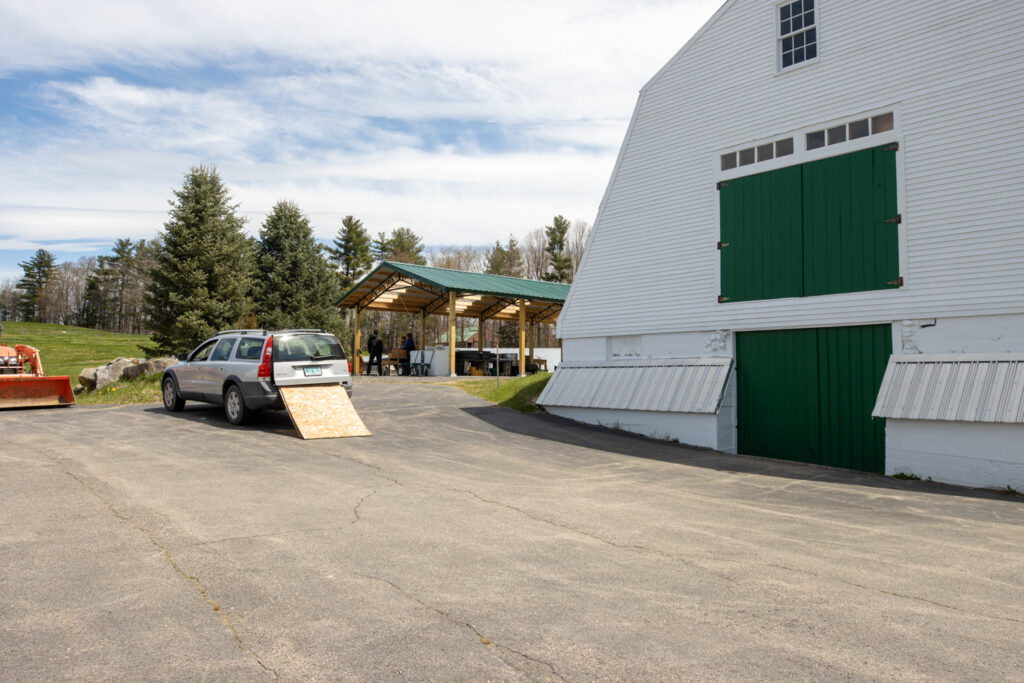
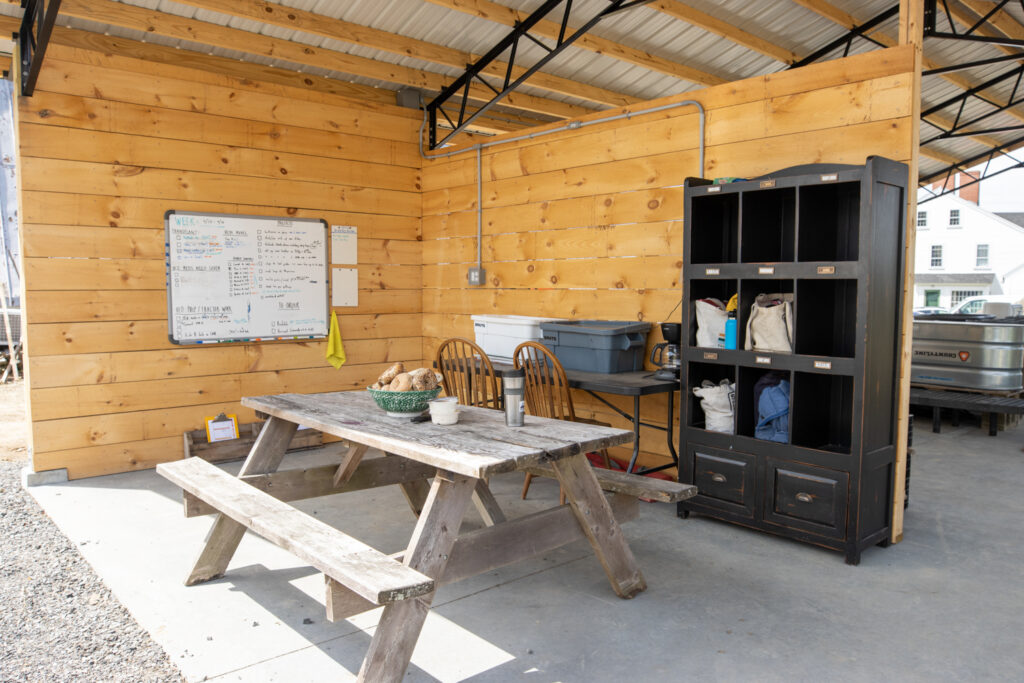
Key Features:
- Open floor plan for flexible set-ups
- Open air is nice on nice days
- Tote dollies ease movement
- Field office/picnic table in shaded area protected from prevailing wind
- Drainage is managed and goes to a swale
Other things to consider
- Competing water use – sharing the water pressure to the greenhouse, irrigation, and the wash pack is an inconvenient dance of coordination, and an upgraded well/pump is in the future.
- Optimal height? Having a roof so high does not shade or protect underneath as much as a lower roof would, but high ceilings keep the space flexible for off season storage of other farm equipment. The team is considering a roll-down tarp or building a new wall to help improve protection against the weather.
Watch the Interview and See the Area
Acknowledgements
This case study is possible because of the hard work, wisdom, and generosity of Kate Donald and Amber Wilson at Stout Oak Farm. Without their willingness to take the project on to begin with, deal with all the challenges that such projects bring, and complete it we would have nothing to share. We are grateful to them for their willingness to share their story and knowledge in this form so that others can learn.
Funding for this publication was made possible, in part, by the USDA Northeast Sustainable Agriculture Research and Education program through award LNE19-375, by the Food and Drug Administration through The Vermont Agency of Agriculture Food and Markets via the Integrated Extension Educational Programming in Support of the VAAFM Produce Program Grant 02200-FSMA-2018-01. The views expressed in the publication do not necessarily reflect the official policies of the U.S. Department of Agriculture, the U.S. Department of Health and Human Services or the Vermont Agency of Agriculture; nor does any mention of trade names, commercial practices, or organization imply endorsement by the United States Government or the State of Vermont.