Pheonix and Megan O’Brien of Hall Brook Farm purchased their farm in Thorndike, Maine in 2016, and are growing over 20 acres of vegetables with over ⅓ acre in high tunnels. They have experienced rapid growth of the business in the last few years. In 2020 they had gross sales over $250,000 which expanded in 2021 to $430,000. They are on track to crest $500,000 in 2022. Their markets are 100% wholesale to both independent groceries, chains including Whole Foods and Hannaford supermarkets, and other local farms. These markets have had a strong appetite for the organic vegetables they are growing. Moving this volume of product demanded an upgraded washing and packing space and planning for a new building started in 2020. Their crew includes 8-9 workers (Pheonix included) in the summertime, 5 in the fall, and runs with 1-2 full time workers throughout the winter.
Crops Grown
- Bunched greens
- Tomatoes
- Cucumbers
- Summer squash
- Zucchini
- Carrots
- Beets
- Cabbage
- Winter Squash
Wash Equipment
Hall Brook Farm utilizes an AZS washline for rinsing produce. It features a barrel washer, rinse conveyor, air knife and rotating inspection table. The winter greens go through a dunk tank and a greens spinner.
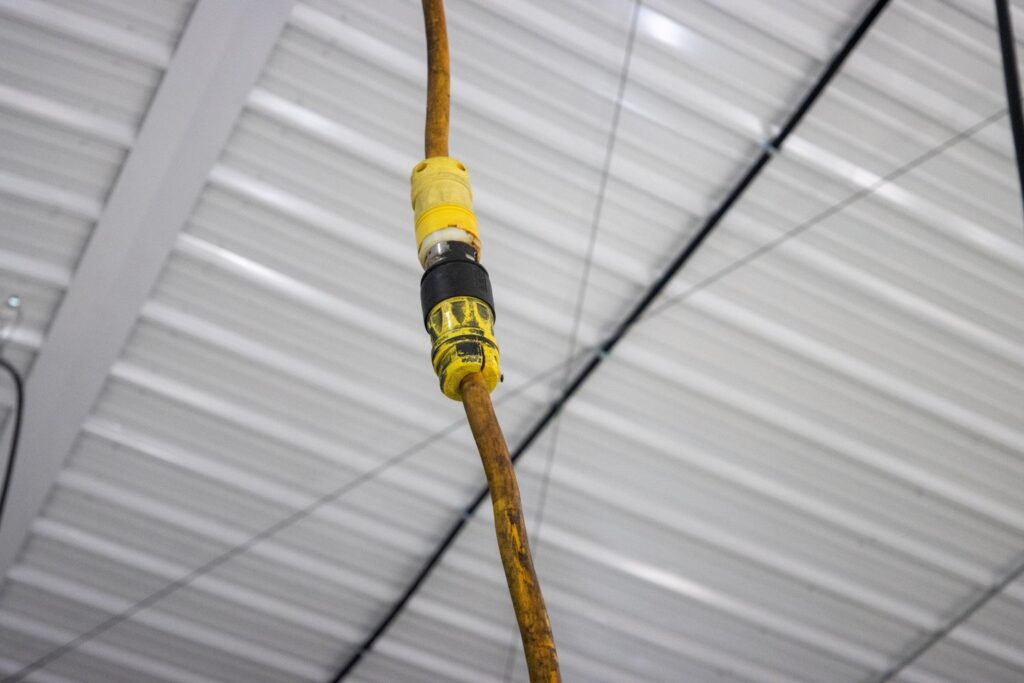
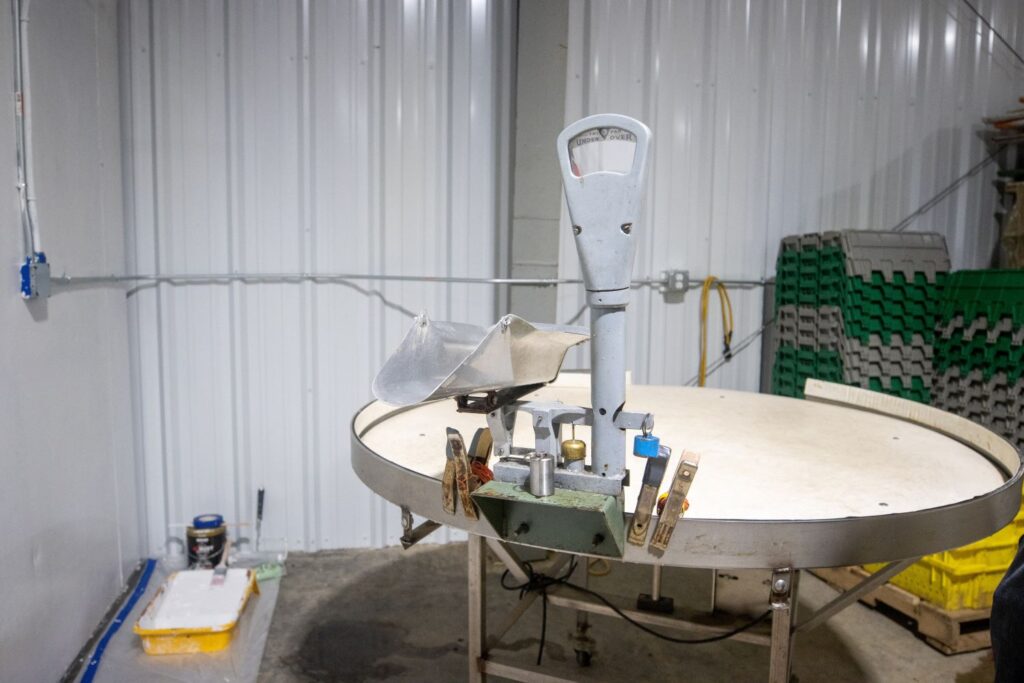
Building Features
The clear span metal building (has no posts) is 50’x60’ with 16’ eaves. It features the following:
- Slab with trench drain
- Radiant heat with on demand propane wall-hung boiler
- Bathroom with shower, washer & dryer
- Handwashing sinks
- Walk-in cooler
- 2 over-head doors
- Loading dock and dock leveler
- Crew lockers/break area
- New septic
This project also included drilling a new well (with NRCS support) that produces 20 gallons per minute (gpm) which is needed for the rinse conveyor that consumes upward of 15 gpm.
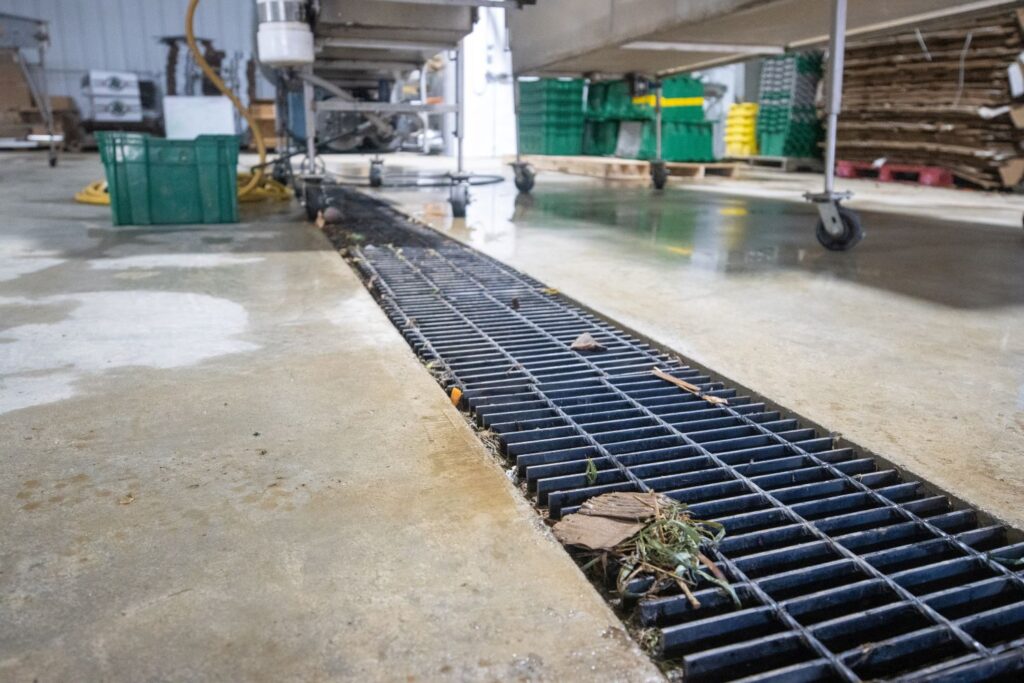
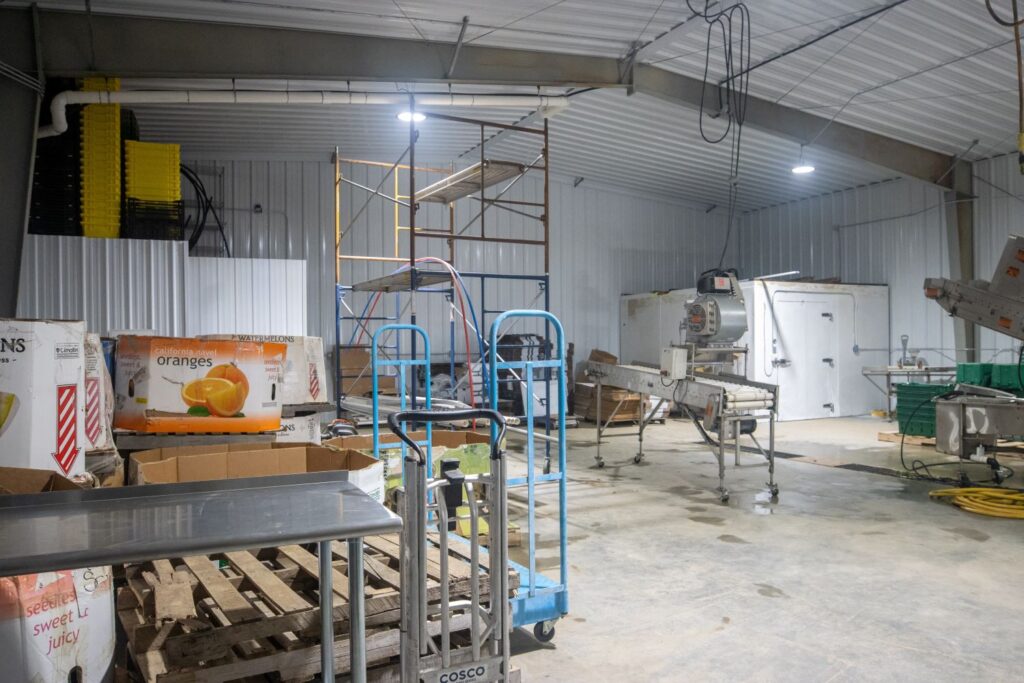
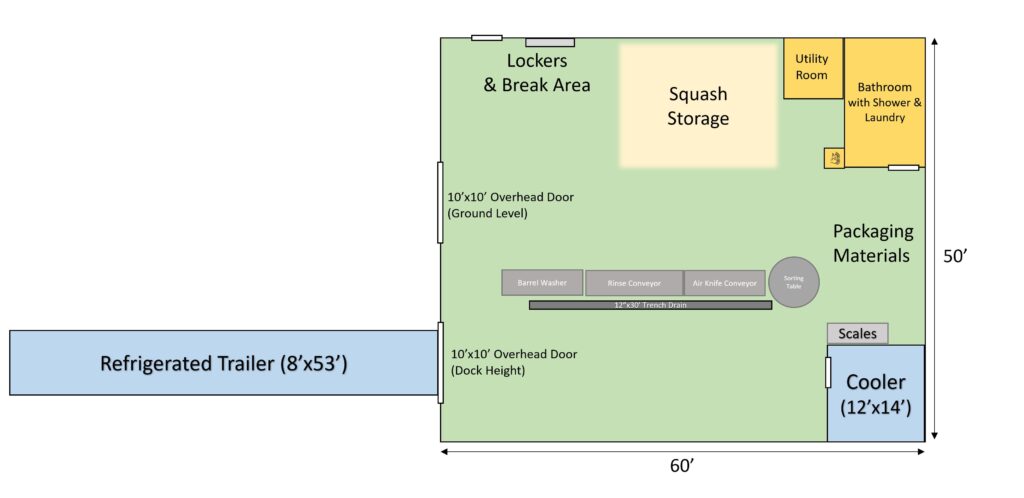
Building Process & Cost
The metal building came from Ithaca Steel Buildings (Philadelphia, PA), but Pheonix notes there are several of these types of companies out there. At the time, a local lumber yard estimated $90,000 for an insulated wood structure. The metal kit (which includes 8” fiberglass insulation) was quoted at $41,000 delivered. Additional contractor labor costs were needed and originally quoted at $38,000, but ended up costing $48,000 since the first contractor didn’t work out beyond installing the concrete. Other Contractor quotes ranged widely from $60,000-90,000.
Phoenix formed up the trench drain because the concrete contractor didn’t want to do it. He had a pad poured as a footing for the drain, then made a box out of 2” lumber and OSB. The slab and the drain walls were done as a single pour. The trench drain is 12” wide by 2’ deep, which seems a bit excessive when you look at it but will be nice to catch heavy loads of sediment. It is also important to note that the trench drain has an inclined floor to promote drainage. The grate was cut by a local metal fabricator from a larger sheet of pre-welded steel.
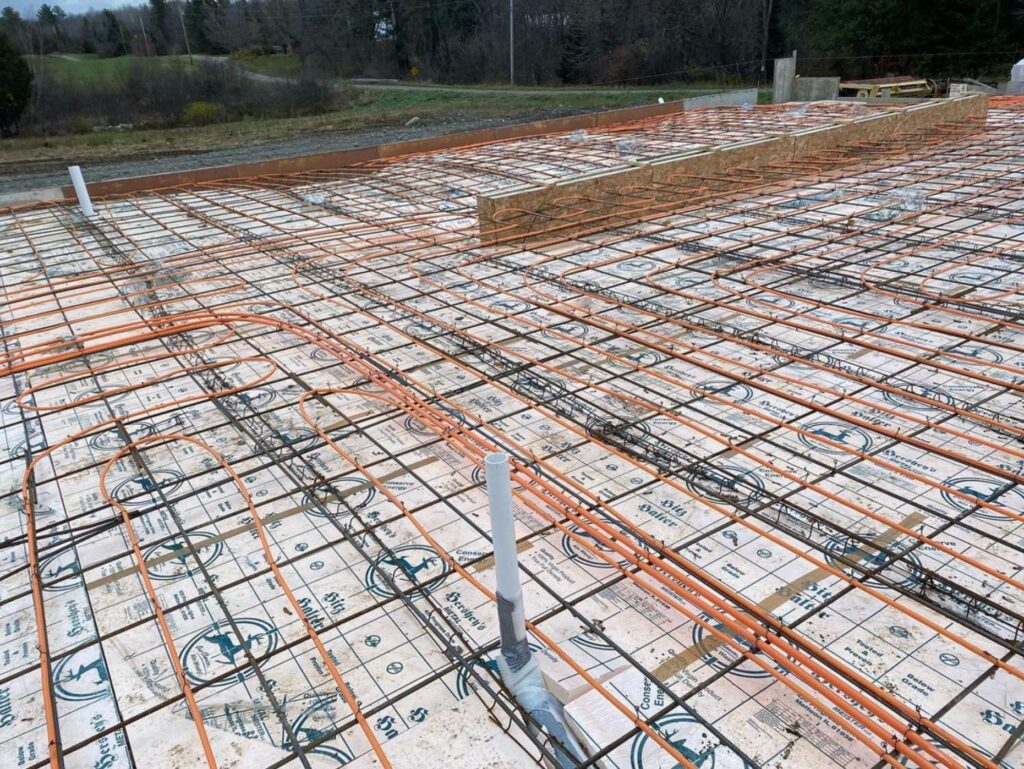
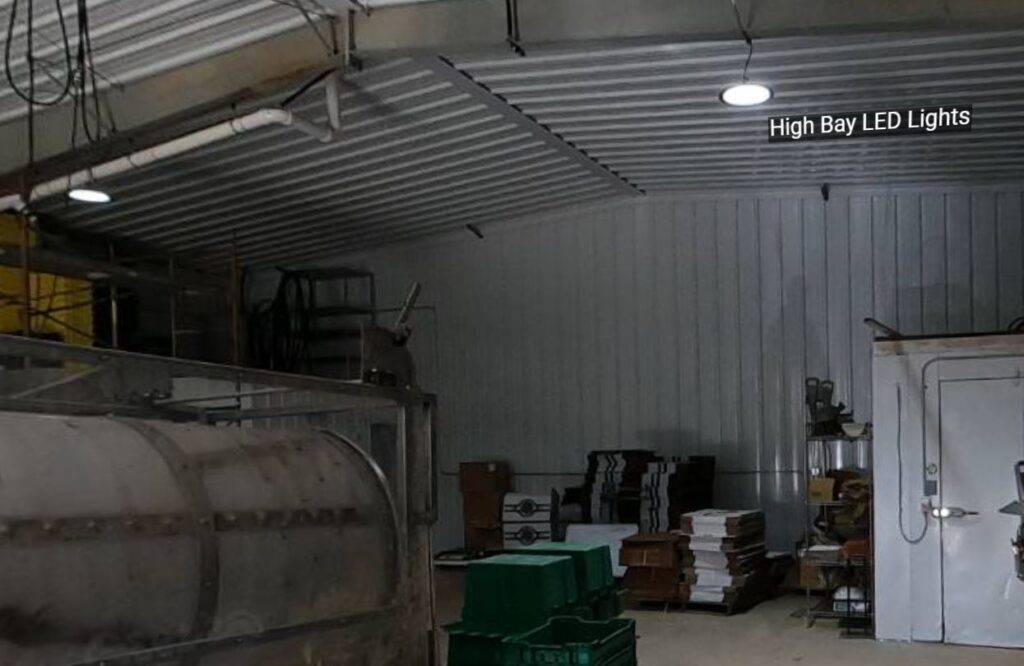
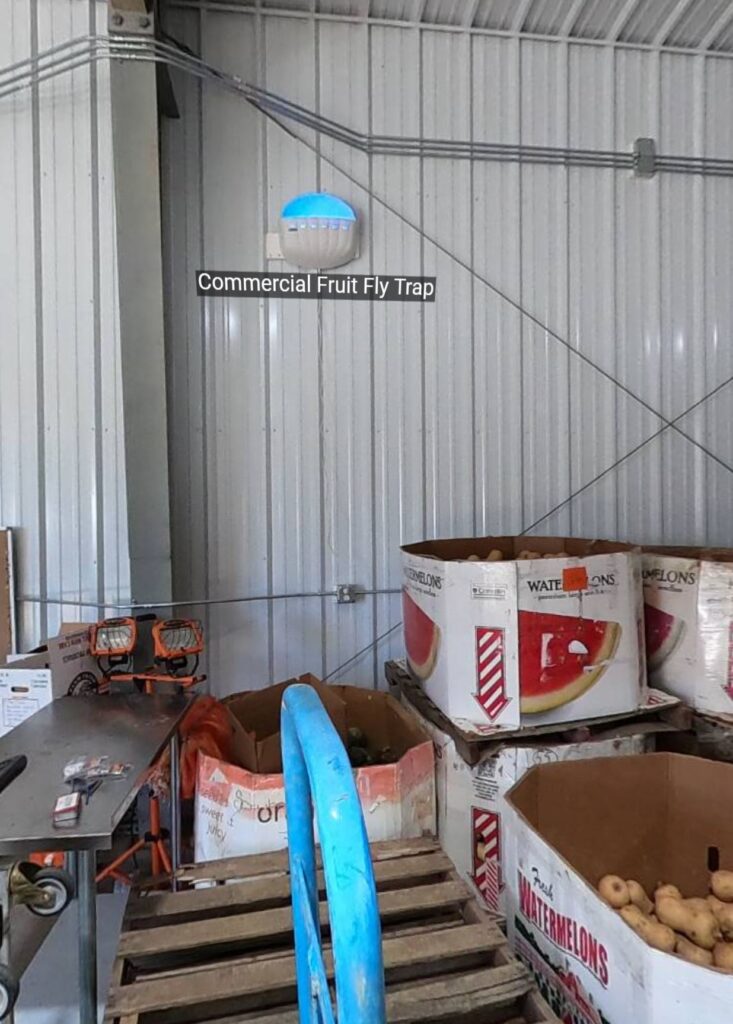
Projects Costs
$33,000 Sitework & Septic
$36,000 – Concrete
$41,000 – Building Materials
$48,000 – Building Labor
$28,000 – Plumbing & Heating
$18,000 Electrical
$4,500 Overhead Doors
$3,200 Dock Leveler
$2,000 Bathroom Framing Labor & Materials
Total Build Cost approx. $213,700
Contractor Troubles
Pheonix served as the general contractor (GC) for the project. After this experience, he might recommend having someone else handle that since it was challenging managing the project and running the farm. When interviewing Megan and Pheonix as the project was wrapping up and they were beginning to use the space they shared that what should be an exciting and fun project was no longer fun or exciting after dealing with the stress this project induced over the previous two years. “Be careful who you hire”, they concluded. Phoenix also shared that local contractors were busy and booked solid, so they were in a position to can get the work and the price they want.
At the beginning they hired a contractor based on a recommendation from a friend of a friend. The original quote was fair, but they ended up getting charged way more than anticipated. Despite discussing that they’d take off a significant portion of the cost if Phoenix did certain parts of the project, the bill increased. It took all summer to get the slab poured and once the final bill was questioned, contractor invoices weren’t shared, lawyers got involved. It was stressful and draining.
Their experience with many other subcontractors during the project was great, however. The excavator was great – very efficient and timely. It was hard to find a contractor for this project since it was larger than a residential building, but small in regards to a commercial project. The company eventually used to build the structure was Maine Coast Construction (Camden, ME) and proceeded at a steady rate. The plumbing, electrical and heating contractors were also good, but were held up waiting for the building which got delayed from the issues early on in the project.
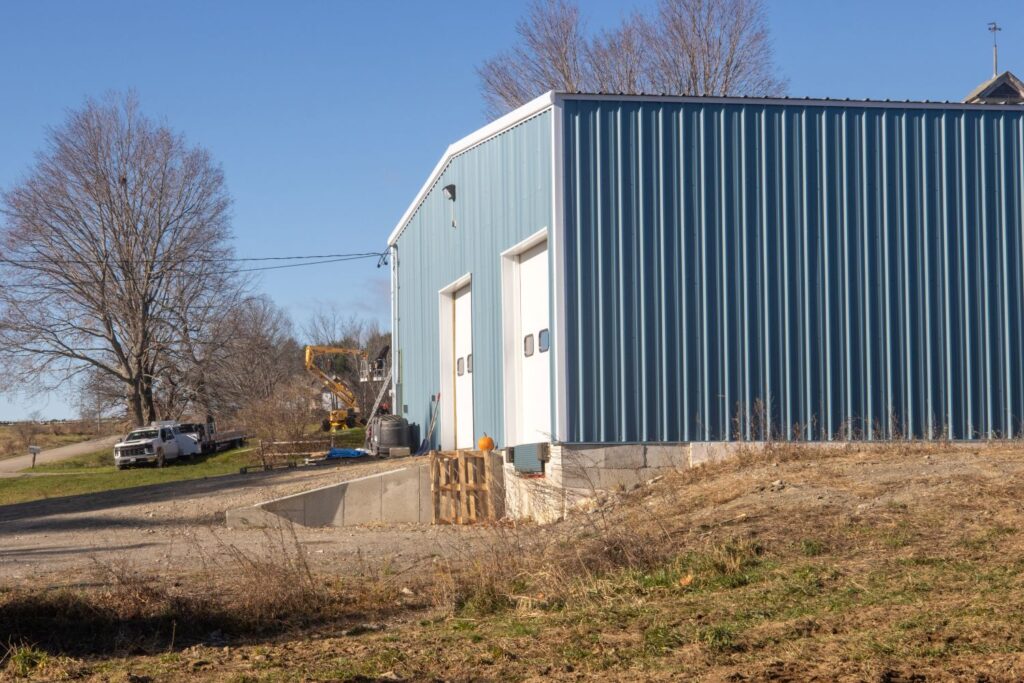
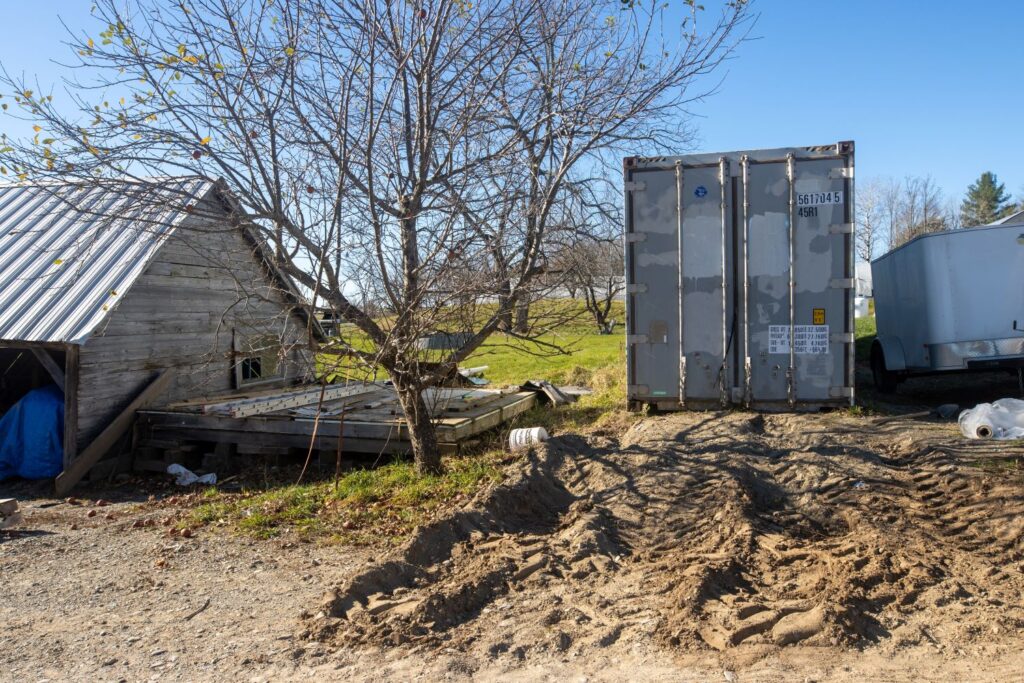
Lessons Learned
- Get references and have signed contracts with contractors.
- Didn’t enough parking space and the building limits access to older barns, though location options were limited.
- Not incorporating a drainage swale for wash water discharge during the the rest of the excavation. That will be done next.
- Not building big enough for all the cooler space needed, resulting in still needing to use a 40’ insulated container for cooler and a 53ft refrigerated trailer.
- Wished they got the high lift kit for the garage door, or a roll-up door to save some vertical space that could have been used for pallet racking. The overhead door track and supports take up space inside the building.
Previous wash/pack
Before moving into this new building Pheonix and Megan operated out of a propagation greenhouse. It had a poured slab with a drain. As the wash equipment took up more and more space the prophouse needs got pushed to renting space across town. That large expense will be reduced as a result of the a new building. Working out of a greenhouse was a great space to have morning meetings with the team and to store winter squash in the fall. While a greenhouse is a nice area to work in the winter, it is hot in the summertime which is tough on the crew, and the crops.
Walk Through the Packhouse with this 360 Tour!
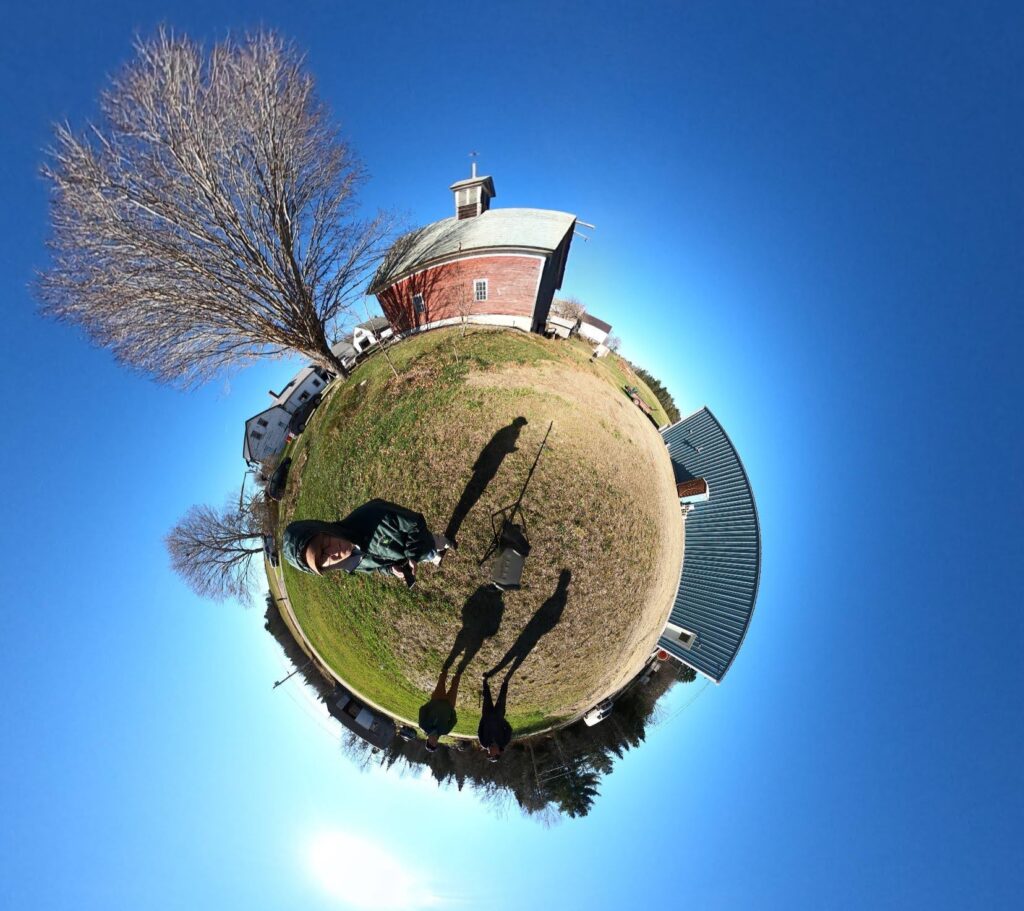
Overview of the Packhouse with Pheonix
Acknowledgements
This case study is possible because of the hard work, wisdom, and generosity of Pheonix and Megan O’Brien at Hall Brook Farm. Without their willingness to take the project on to begin with, deal with all the challenges that such projects bring, and complete it we would have nothing to share. We are grateful to them for their willingness to share their story and knowledge in this form so that others can learn.
Funding for this publication was made possible, in part, the USDA Northeast Sustainable Agriculture Research and Education program through award LNE19-375, by the Food and Drug Administration through The Vermont Agency of Agriculture Food and Markets via the Integrated Extension Educational Programming in Support of the VAAFM Produce Program Grant 02200-FSMA-2018-01. The views expressed in the publication do not necessarily reflect the official policies of the U.S. Department of Agriculture, the U.S. Department of Health and Human Services or the Vermont Agency of Agriculture; nor does any mention of trade names, commercial practices, or organization imply endorsement by the United States Government or the State of Vermont.