Download the PDF Fact Sheet of this Post Harvest Case Study Here!
Taylor and Jake Mendel own and operate Footprint Farm in Starksboro, VT. Starting their own farm in 2013, they now produce pretty much everything except storage potatoes and storage squash with 66 different kinds of vegetables grown in both fields and high-tunnels.
About Footprint Farm
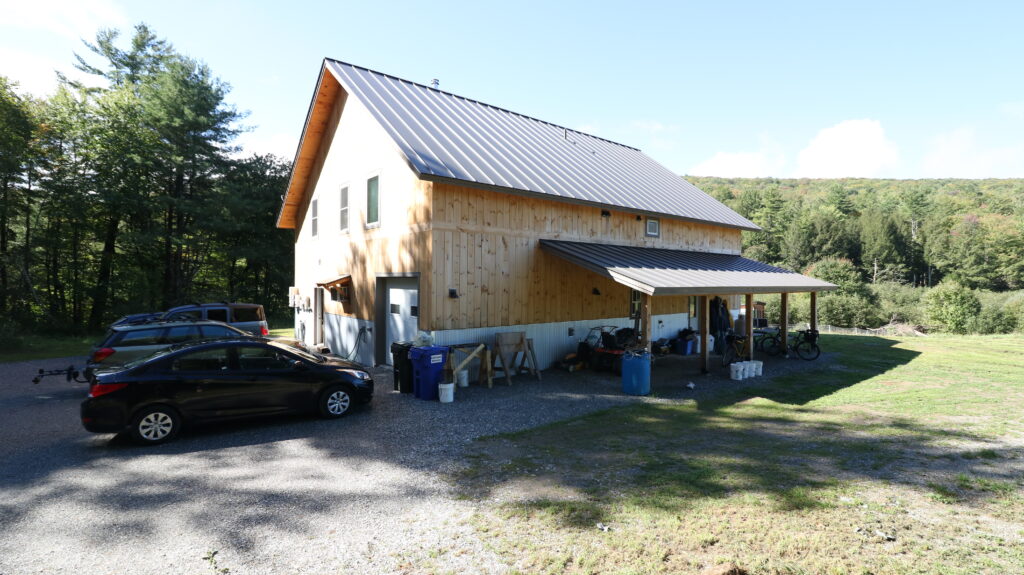
- Location: Starksboro, VT
- Acreage: 2.5 (1.5 in production, 1 acre in cover crop)
- Crops: Greens, tomatoes, root crops and more with 66 different types of vegetables grown
- USDA Sales bracket: $100,000-249,999
- Markets: CSA, farmers markets, restaurant/wholesale accounts
- Crew: 4 (May-October), 2 (November – April)
- Wash/Pack Operations: Triple bay greens washing with a converted washing machine salad spinner, Barrel/drum washer, bunch washing on spray table, 1 CoolBot walk-in cooler
Overview
The “BarnHouse” is 36’x48’ and has two stories of 1,728 square feet. Two-thirds of the first floor is dedicated to washing and packing, the other third includes space for an egg washing station, cooler, employee break area, restroom, and a shop. The second floor is finished living space.
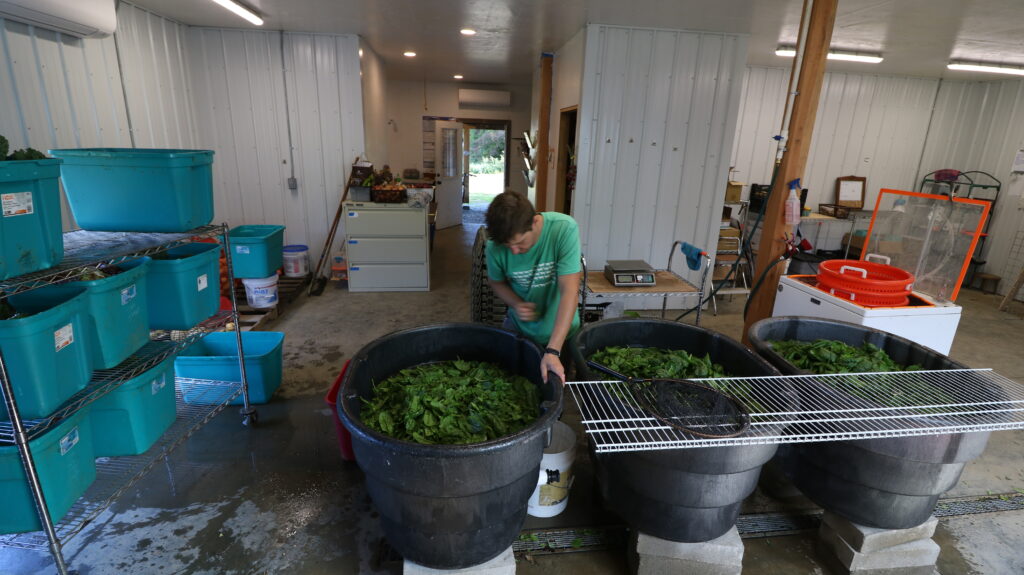
Special considerations that went into the design process included the main crops that will be washed, and what aspects of that process have been uncomfortable or inefficient in the past. For them, the focus on greens washing was the main priority.
Building materials were carefully considered to be durable, washable, and water resistant. In the wash area, they chose to go with corrugated metal roofing for the interior walls to meet these requirements.
Produce safety was in mind during the design process of this space. Some of the key elements include:
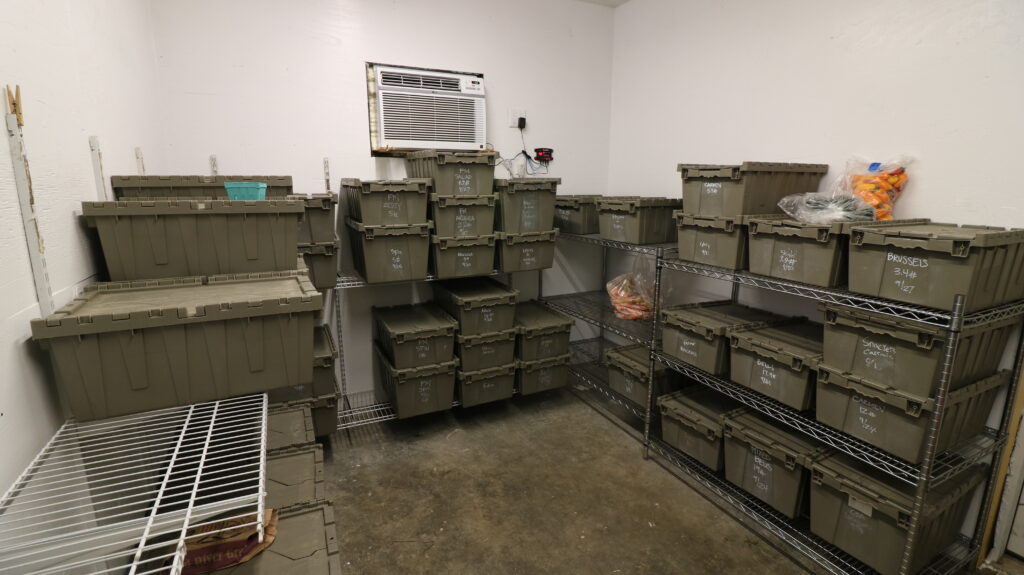
- Highly durable for long-lasting function
- A bright and clean space that’s pleasant for humans and not for pests
- Separation of clean and dirty bins
- Covered bin storage area
- Egg cleaning area separated from produce, including its own entrance to the building separate from vegetables.
- Easily cleanable floor (concrete) and walls (metal)
- Proper drainage to control water
- Bright lighting (easy to see dirt and grime)
- Wash water is sourced from a drilled well
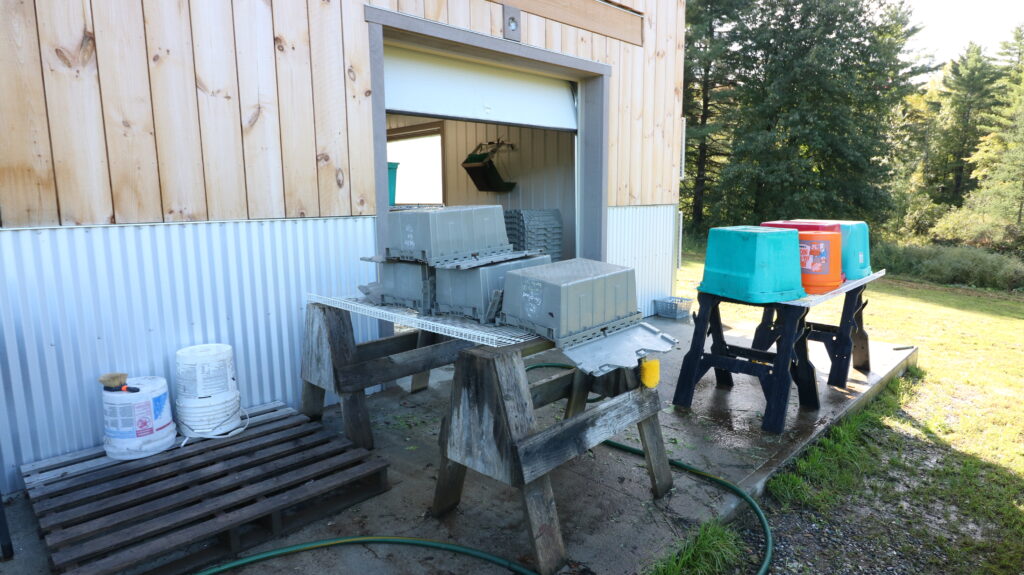
Reflecting on the new space, Taylor notes, “It’s so fast now, there is not even an opportunity for things to get damaged or dirty.” Going from the field, to the barn, washed, packed, and stored in a cooler quickly and methodically reduces the risk of contamination.
Many design features were implemented to make this a very practical space. Examples include the use of 4’ wide people doors for easy maneuverability and an overhead door where the product comes in. A trench drain was installed in the washing space to carry the wash water out into a dedicated leach field constructed with perforated pipe that ends in a gravel area.
Labor savings both in time and money has been seen as a result of this new build. Having a place for everything makes it easy to find. Putting things on wheels provides for adaptability. Having enough space to work and move makes it easy to get the vegetables washed and to market as quickly and easily as possible.
A typical cleaning procedure for the harvest containers, tools, and equipment consist of a daily rinse off of dirt and debris and scrubbing with soap and water as needed. For example, a deeper clean is typically needed after harvesting squash or other vegetables that can leave a sticky sap. Everything gets a scrub down with soap and water monthly if not needed prior.
The Why
“We wanted to do year-round production with-out a winterized building,” Taylor explains thinking back about their previous setup. “But, it was too painful on our hands to be able to wash greens through the winter.” They also had problems getting rid of the wash water with nowhere for it to drain. The continued growth of the farm pointed toward having employees in the winter and they couldn’t put others through the pain of cold wet hands. At the time of planning, they also were commuting to the farm and wanted to build a house on location. They decided it made more much more sense to build one combined building rather than two separate ones. This simplified both planning and construction and reduced worrying about how to winterize both a barn for work and a house for living.
Another great benefit that’s arisen from the BarnHouse build is that the profitability is greatly increased due to product quality improvements. “Our cull rates have plummeted since we got this building and our quality has increased immensely this year.” This increase in quality has made it possible for them to sell everything they harvest, reducing both food waste and time into production!
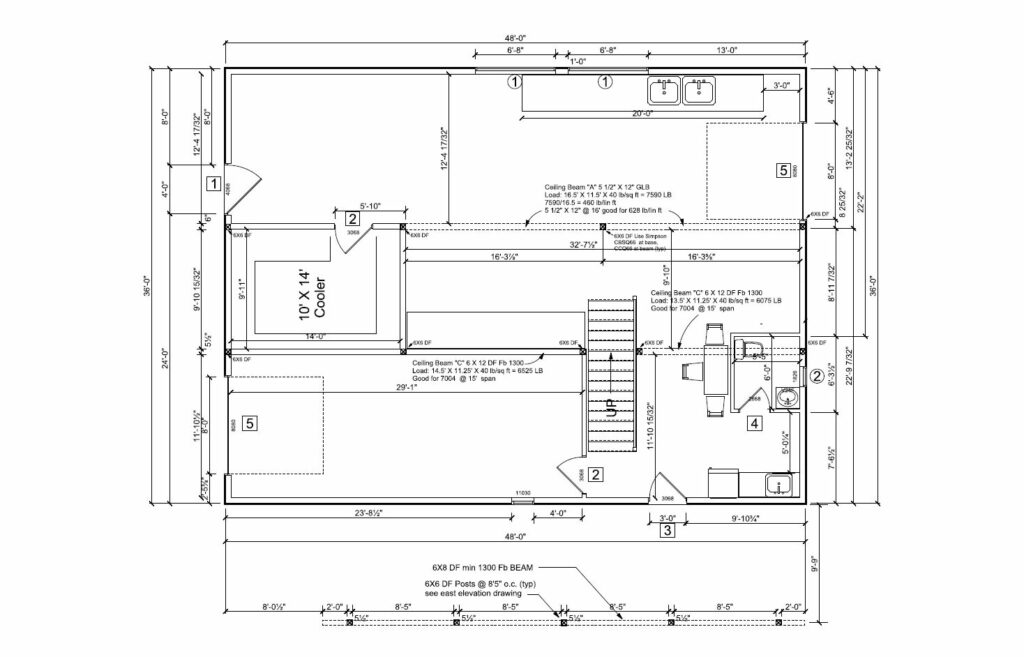
Cost
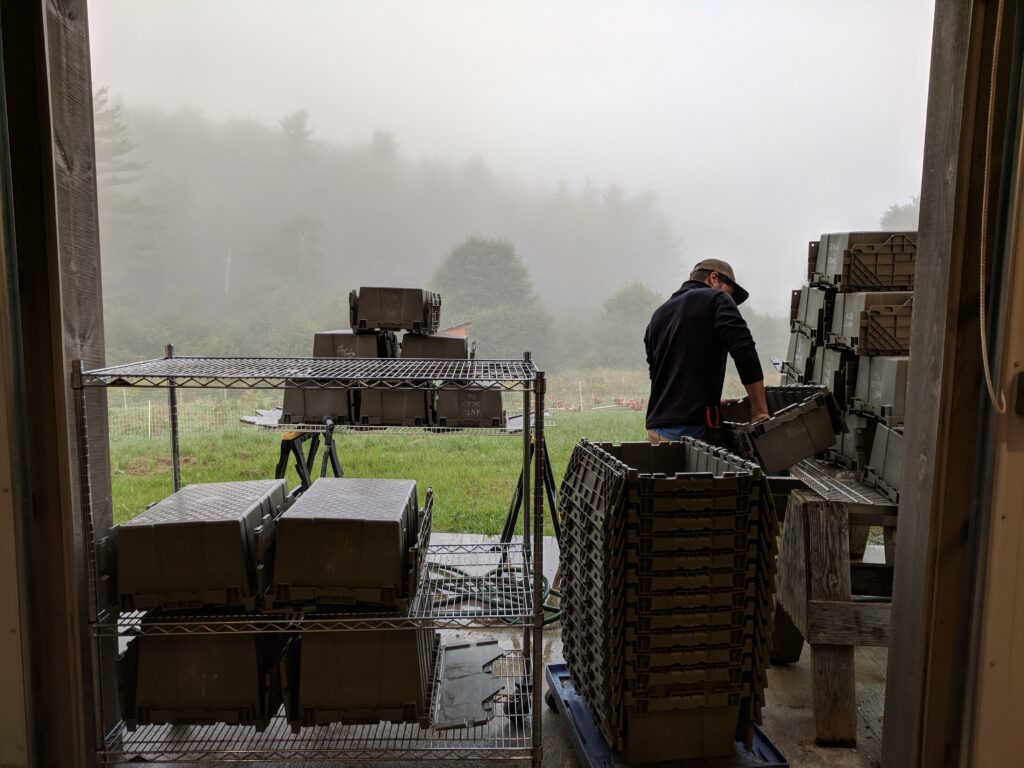
The total cost to build the BarnHouse was about $300,000. The contractors they worked with said that a project like this fully hired out would have cost close to half a million dollars.
Tactics to keep costs down
- Self-designed the building
- Helped out with the construction
- Milled the lumber on-site
Favorite Things
“Natural light through large windows and everything painted white with tall ceilings make it a bright and cheery place to work.”
Other Favorite Elements of this build:
- Heated Space via an electric heat pump
- 100% of electrical needs covered by green energy (Solar)
- Bright Cleanable Walls – Metal Roofing – go.uvm.edu/smoothnclean – about $1.00 per square foot.
- Trench Drains
- Everything on wheels
- Covered outdoor space
Regrets
This project was well thought out and the benefits far outweigh the regrets. A few things that didn’t go as planned was the floor didn’t get pitched perfectly to the drain, so water doesn’t flow as well as it should. Taylor wishes there was a person-door in addition to the garage door on the side where the product comes in, but the rest of the crew agrees one is not needed. They had to change the way they pull up from the field to their unloading space due to the location of the septic, which changes the flow of operation which is less than ideal. Other than thinking about septic placement a little further ahead of time, regrets so far are minimal items like light switch placement and a few small things like that.
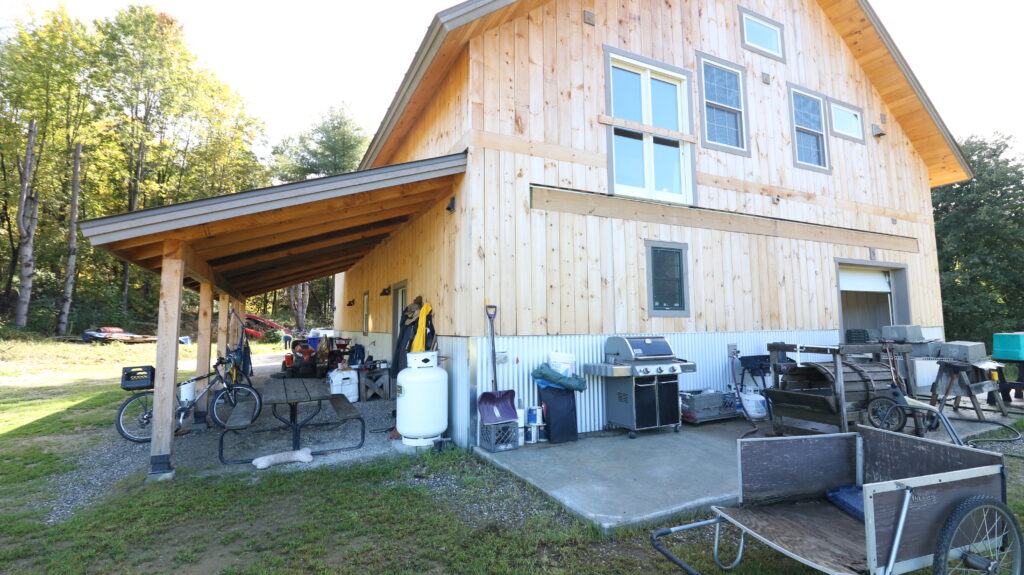
Virtually Visit this Farm
Explore this virtual tour of Footprint Farm with an immersive 360 degree experience.
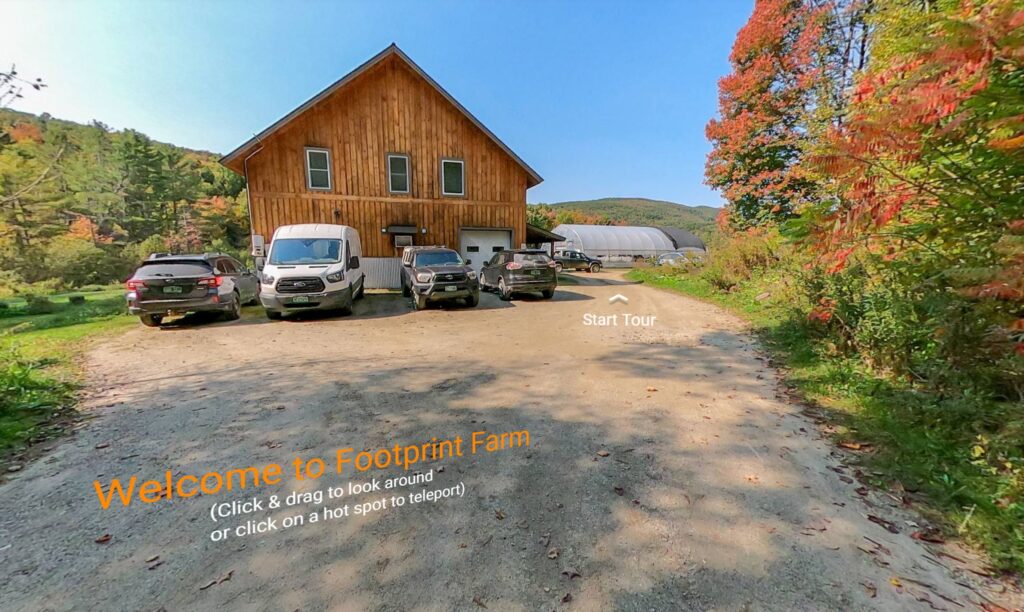
Key Influencers and partners
USDA REAP Program – This Rural Energy for America Program is a grant that paid a portion of the solar panels installed by SunCommon which cover all of their electrical cost for the entire year!
CoolBot (Store It Cold) was helpful in figuring out the temperature differences causing humidity and condensation.
Consultation from other farming peers was helpful including Danielle from Root 5 Farm in Fairlee, VT for their building design with covered outdoor space or Christa from Jericho Settlers Farm for guidance influencing natural light to make it an enjoyable space. Ben Hartman, farmer of Clay Bottom Farm and author of The Lean Farm, helped nail down the flow of production.
University of Vermont Extension Ag Engineering helped with guidance on wall finishes surfaces and VVBGA CAPS helped with examples of how to make things comfortable and safe.
Taylor and Jake are both thrilled to have built this building. It has improved their daily lives so well that it’s an enjoyable place to live and work. Though it was a costly project it’s quickly paying for its self by increasing quality, widening margins and providing more goods to go to market. By having a clean, bright, and comfortable place to work they are able to retain their employees for the following season. By utilizing solar energy, reducing food waste, and growing organic vegetables this improvement is enabling a sustainable farm to be a sustainable business.
If you would like to see Footprint Farm’s wash space in action check out the videos below! The playlist features a 2.5min promo, the full interview explaining the features of the wash-pack space (6min), more in-depth experiences and challenges from the build process (12min) and the last video showcases washing a batch of greens through their system (2min). Enjoy!
Share This Post
Looking for more Post Harvest Case Studies?
We showcase several farms of various sizes, features and budgets in this series. Visit: go.uvm.edu/phcs
Acknowledgments
This case study is possible because of the hard work, wisdom, and generosity of Taylor and Jake Mendel Footprint Farm. Without their willingness to take the project on to begin with, deal with all the challenges that such projects bring, and complete it we would have nothing to share. We are grateful to them for their willingness to share their story and knowledge in this form so that others can learn.
Funding for this publication was made possible, in part, by the Food and Drug Administration through grant PAR-16-137, by the USDA’s National Institute of Food and Agriculture through the Food Safety Outreach Program award 2016-70020-25792 accession 1010528 and by The Vermont Agency of Agriculture Food and Markets via the Integrated Extension Educational Programming in Support of the VAAFM Produce Program Grant 02200-FSMA-2018-01. The views expressed in the publication do not necessarily reflect the official policies of the U.S. Department of Health and Human Services, the U.S. Department of Agriculture or the Vermont Agency of Agriculture; nor does any mention of trade names, commercial practices, or organization imply endorsement by the United States Government or the State of Vermont.