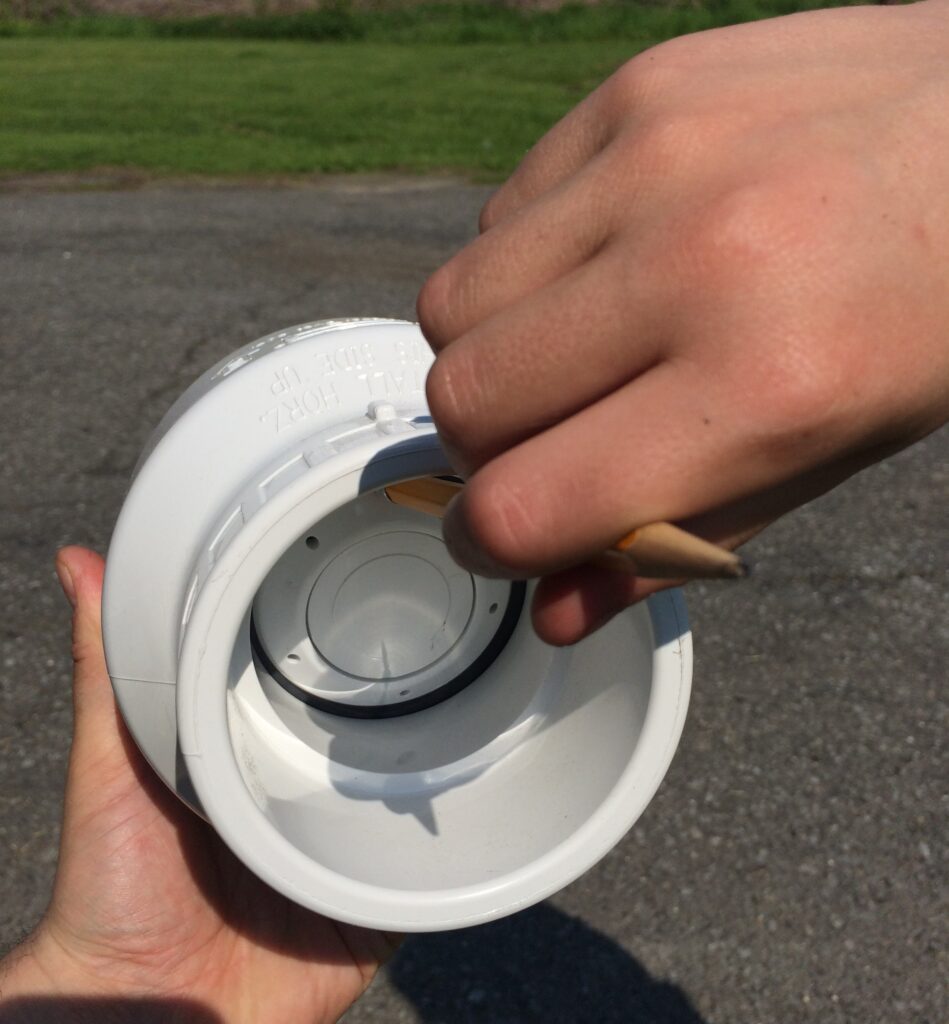
The intentional, directional, and reliable flow of water is important to ensure agricultural water is “safe and of adequate sanitary quality”.
This post provides information on the importance of backflow prevention and some common practices that help mitigate the risk of backflow. You can also view presentation slides and a recorded webinar on this topic that were provided for the May 2019 Produce Safety Alliance Educators Call.
PDF Download of this information: Backflow Prevention Factsheet
Regulatory and Training Context
There are at least three places in the FSMA Produce Safety Rule (PSR) that are relevant and two in the Produce Safety Alliance (PSA) National Curriculum (emphasis added):
FSMA PSR §112.41
What requirements apply to the quality of agricultural water? All agricultural water must be safe and of adequate sanitary quality for its intended use.
FSMA PSR §112.42:
What requirements apply to my agricultural water sources, water distribution system, and pooling of water?
(a) … you must inspect all of your agricultural water systems… including consideration of the following: …
(5) The likelihood of introduction of known or reasonably foreseeable hazards to agricultural water by another user of agricultural water before the water reaches your covered farm.
(b) You must adequately maintain all agricultural water distribution systems … to prevent the water distribution system from being a source of contamination to covered produce, food contact surfaces, areas used for a covered activity, or water sources…
(c) You must adequately maintain all agricultural water sources… Such maintenance includes regularly inspecting each source to identify any conditions that are reasonably likely to introduce known or reasonably foreseeable hazards into or onto covered produce or food contact surfaces; correcting any significant deficiencies (e.g., … and control of cross-connections); and keeping the source free of … other possible sources of contamination …
(d) … implement measures reasonably necessary to reduce the potential for contamination … as a result of contact of covered produce with pooled water. …
FSMA PSR §112.133:
What requirements apply to plumbing?
The plumbing must be of an adequate size and design and be adequately installed and maintained to:
(a) Distribute water under pressure as needed, in sufficient quantities, in all areas where used for covered activities, for sanitary operations, or for hand-washing and toilet facilities;
(b) Properly convey sewage and liquid disposable waste;
(c) Avoid being a source of contamination to covered produce, food contact surfaces, areas used for a covered activity, or agricultural water sources; and
(d) Not allow backflow from, or cross connection between, piping systems that discharge waste water or sewage and piping systems that carry water used for a covered activity, for sanitary operations, or for use in hand-washing facilities.
PSA Module 5.1 – Slide #12
PSA Module 5.2 – Slide #17
Flow of Water
When thinking about controlling water flow, it may be helpful to remember some basic things about water.
- Water flows downhill due to gravity and/or along the path of least resistance (which could be sideways).
- Water flows from high to low pressure. We use pumps to increase the pressure in one place so that flow goes in a certain direction. There are times when the pressure difference shifts due to suction or siphoning. A fire hydrant draw is a good example.
- Water flows in pipe and tube. This helps to direct flow in only certain directions or along certain paths. But it also “connects” different locations. This can lead to “cross connection” between a relatively dirty or hazardous use and a food contact surface.
- We control the flow of water with valves. Most are manual or electronic solenoid valves. But, we also use “check” valves as passive, automatic flow controls. They bias flow in only one direction.
Introduction to Backflow
Backflow is when water (and anything in it) travels in the “wrong” direction or a direction other than the intended one.
Backflow Prevention is taking steps to ensure water flow is in the intended direction or along a path that minimizes produce safety risk due to cross-connection and cross-contamination.
Backflow is typically prevented by
- Obstructing flow in one direction (using a check valve, foot valve, etc), or
- Providing an easier flow path in a different direction that results in lower risk (using air gaps, floor sinks, etc.)
The Charleston, SC Water Department offers a great video summarizing the ways backflow can happen and why it can be a problem.
Step One – Don’t Buy Anything
Know your water systems and assess your risks. Start by mapping out your water system using an existing farm map from, e.g., USDA Farm Services Agency (FSA). Or take a screen shot of a Google Map (zoom in using satellite mode) and paste it into PowerPoint or some other easy editor. You can use PowerPoint to easily draw your water networks on the farm map.

Check & Foot Valves
Check valves are used to allow flow only in one direction in plumbing.
There are two main types of check valves:
- Swing – Gravity forces the gate down, but high enough water pressure will swing it up.
- Spring – A spring forces the shuttle closed, but high enough water pressure from the other side will open the valve.
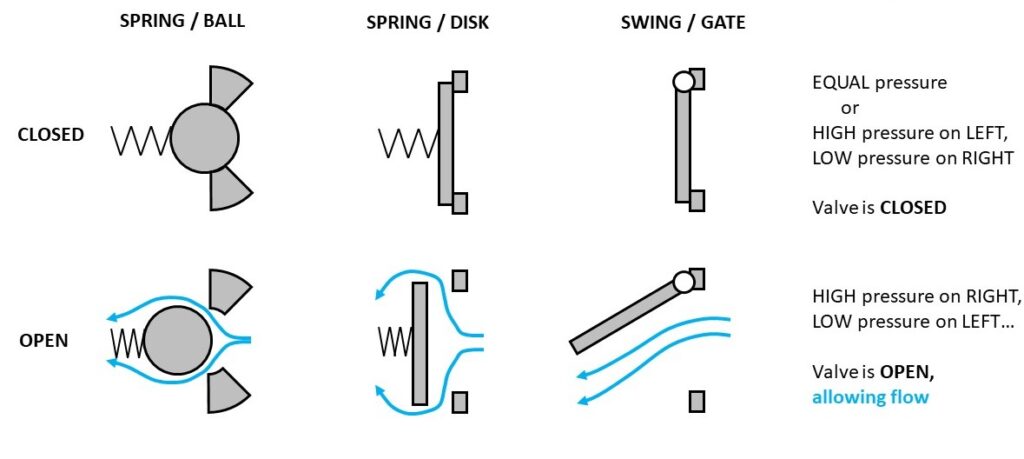
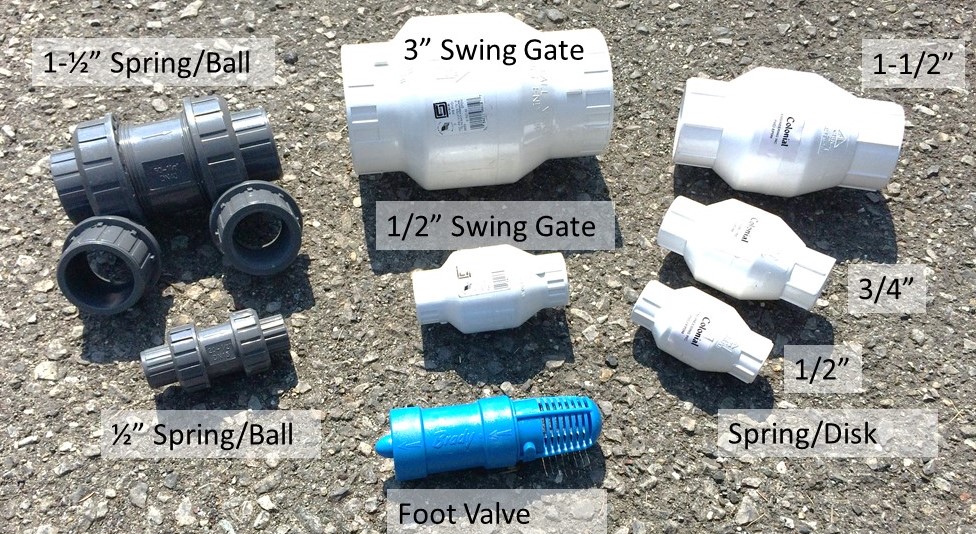
Supplyhouse.com offers a great video that explains the differences between swing and spring check valves.
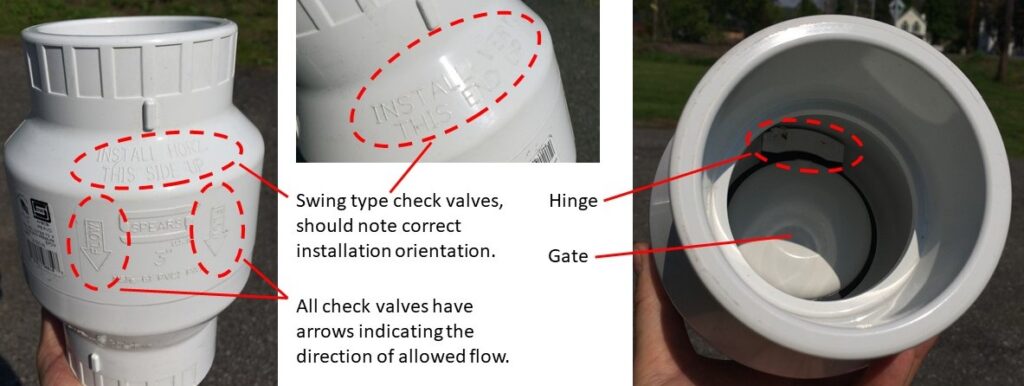
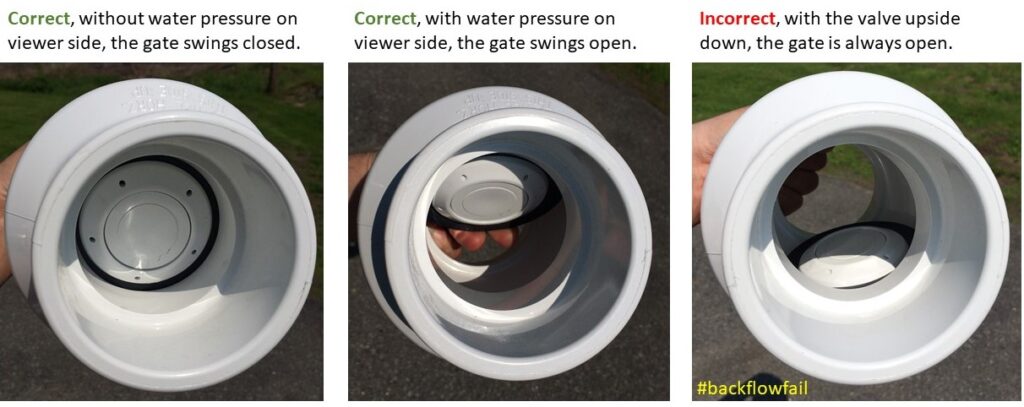
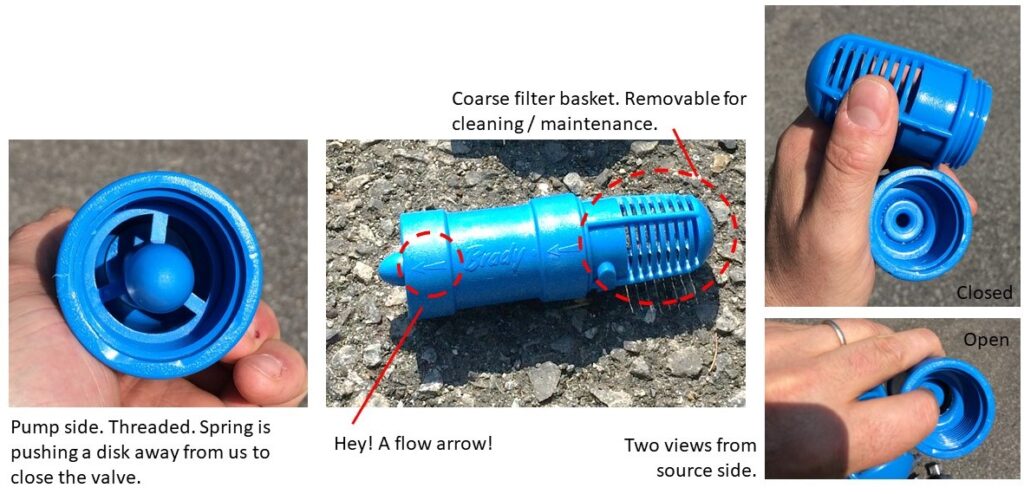
Check Valves – 5 Key Points
Intent – What is the intent of the check valve. Think it through from a systematic perspective and make sure it is going to prevent the flow you’re trying to prevent. Map your water system, identify potential backflow risks and insert check valves as needed.
Type – Know the difference between swing and spring check valves. SupplyHouse offers a good video: https://youtu.be/Sj1vJkhc5XE
Material Compatibility – Almost everything should work with water. If you’re dealing with any injected chemicals, review the housing and seal materials for compatibility. For PAA and chlorine bleach mixed to common packshed concentrations (24-80 PPM and 25 PPM respectively), there shouldn’t be any issues. If you have plumbing lines at higher concentrations it could require more attention. Watch out for chemical and mechanical contamination risks such as lead from brass check or foot valves.
Orientation – There is an arrow on the housing of check valves. It indicates the direction of intended flow. Some check valves have other restrictions on installation orientation as noted previously (esp. swing type).
Sizing – It is yypically OK to go with the existing line size as a guide. If there are pressure drop concerns (limited pressure pump, gravity feed, etc.) up-sizing the check valve or using a low pressure drop type may be required.
Air Gap Drains and Floor Sinks
Air gaps can be introduced into drain lines to break the path of backflow. This can help to ensure that food contact surfaces are not exposed to backflow resulting from downstream blockages. A special floor receptacle known as a “floor sink” can be used to capture the intended discharge flow from one or more sinks or vessels. Consider reviewing local and national building code for specific dimensions and location of different lines coming into a floor sink.
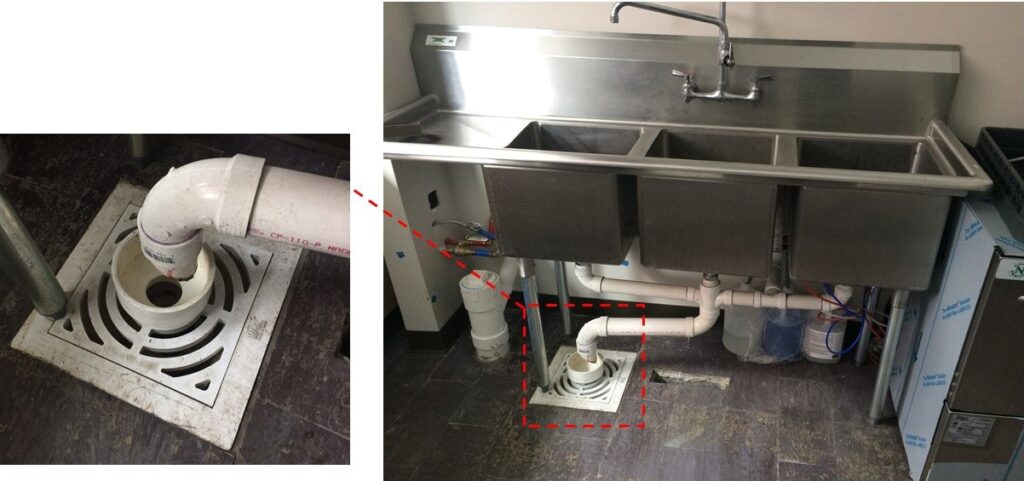
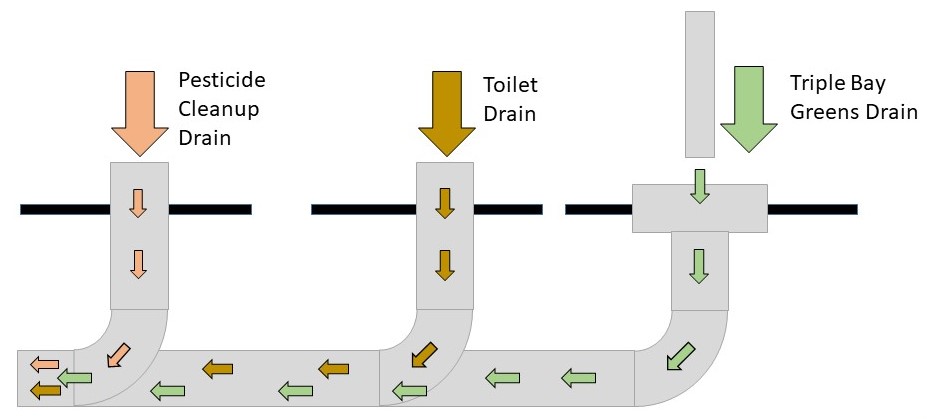
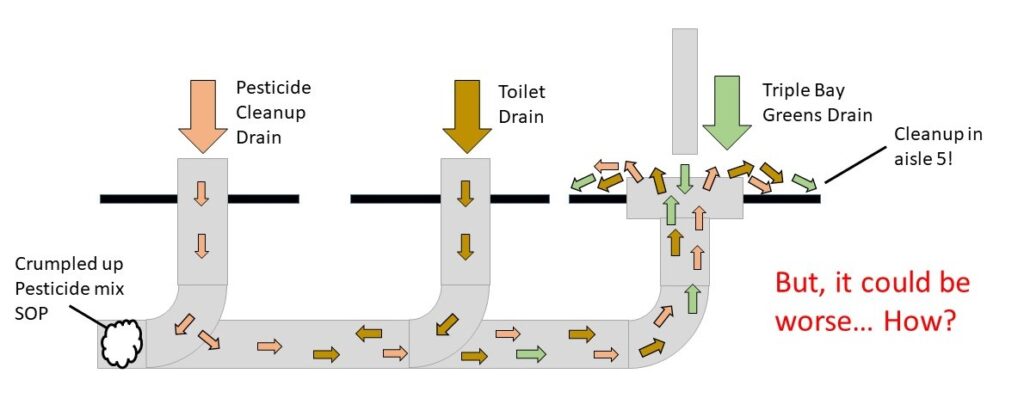
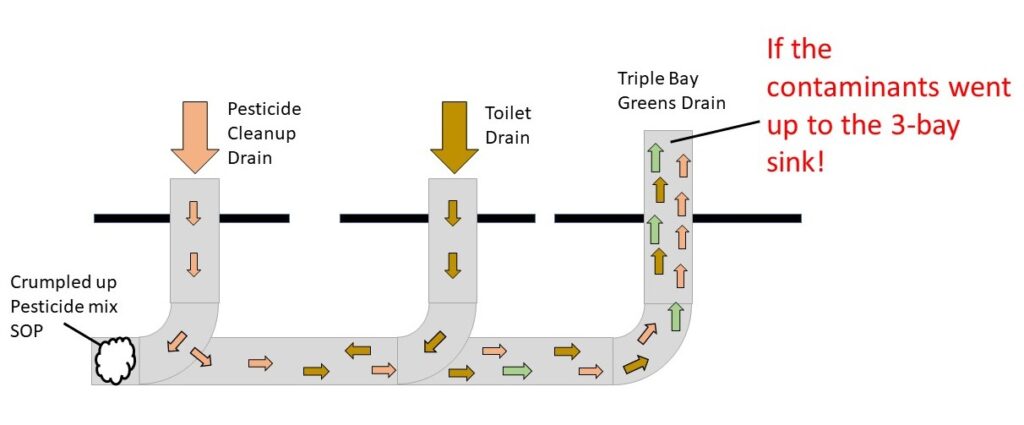
Additional Resources
Charleston (SC) Water System – Backflow Video – https://www.youtube.com/watch?v=YyUi4RMb-bA
SupplyHouse.com – Check Valve Video – https://youtu.be/Sj1vJkhc5XE
Case Histories of Selected Backflow Incidents. FLORIDA DEPARTMENT OF ENVIRONMENTAL PROTECTION. UF TREEO. https://treeo.ufl.edu/backflow/epa-resources/backflow-case-histories/.