Jacob Mills started vegetable farming in 2017 and, after a few years of building the business, faced the reality that washing and packing out of the end of a greenhouse wasn’t going to help him meet the goal of working full-time on the farm.
He was coming to a crossroads realizing that if this was going to become a full-time venture the farm needed to upgrade into a dedicated, efficient, and clean space for washing, packing and handling the produce.
McDonald Farmstand is located in Danville, Vermont and sells both wholesale and retail, out of their farmstand on the side of Route 2.
They were able to start farming without much of a packshed as many of the key crops they grew then don’t require much in the terms of packshed infrastructure: corn, winter squash, pumpkins, etc. With the recent addition of root crops and high tunnels full of greens, they had increased need for washing and packing.
About McDonald Farmstand
- Danville, VT
- Crew: Family members and few seasonal workers
- Main Crops: Tomatoes, greens, pumpkins, corn, roots
- 6 Greenhouses
- 10-15 acres in production
- $100-300k in sales
- ⅓ Wholesale, ⅔ Retail
- Wash Equipment: Greens wash tanks, green’s spinner, barrel washer, stainless packing table
- 20 x 30 feet Wash Pack (1,200 sqft)
Watch the Interview from Jacob
The Building
Jacob considered both stick-framing a structure with lumber and putting up a metal building. He ended up going with a metal building as he found a pre-purchased, but not assembled kit for almost ½ the price of new. The Toro Buildings kit already included doors, but Jacob worked with them to get the proper insulation package and additional parts to suit his building project.
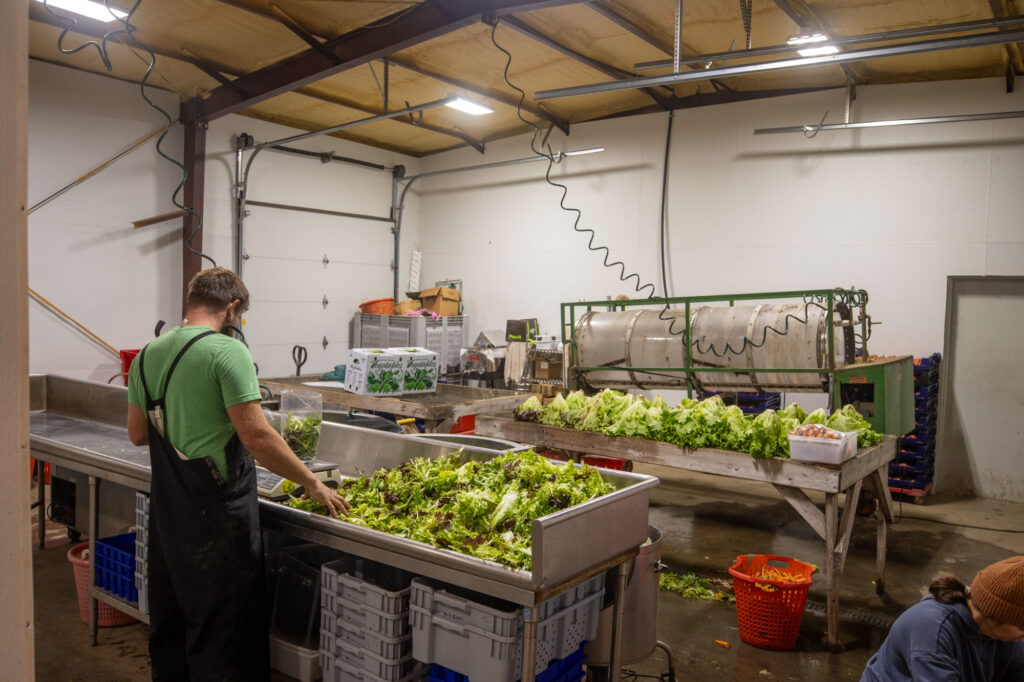
A local contractor put up the building since they had experience assembling metal buildings. Once the site work was done and concrete was in place the structure went up in just about a week.
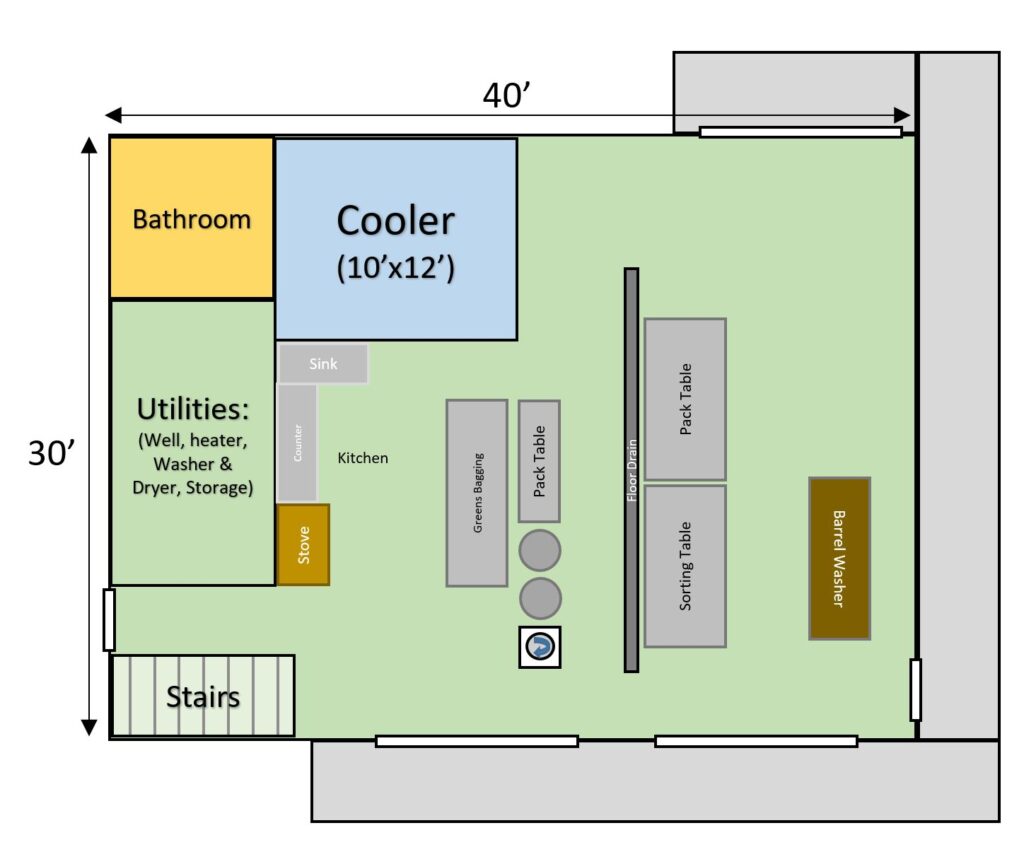
The building is 30’x40’, which Jacob reflects is adequate, but could be larger. On a typical day they harvest in the morning, and work inside the shade of the building with 2-3 people working in the area at a time. It can feel cramped at times with all of the product and equipment filling up the space. One idea he shared was placing the cooler in another building to open up more working space. When all is said and done, he reflects, “As long as it’s organized, it’s functional”.
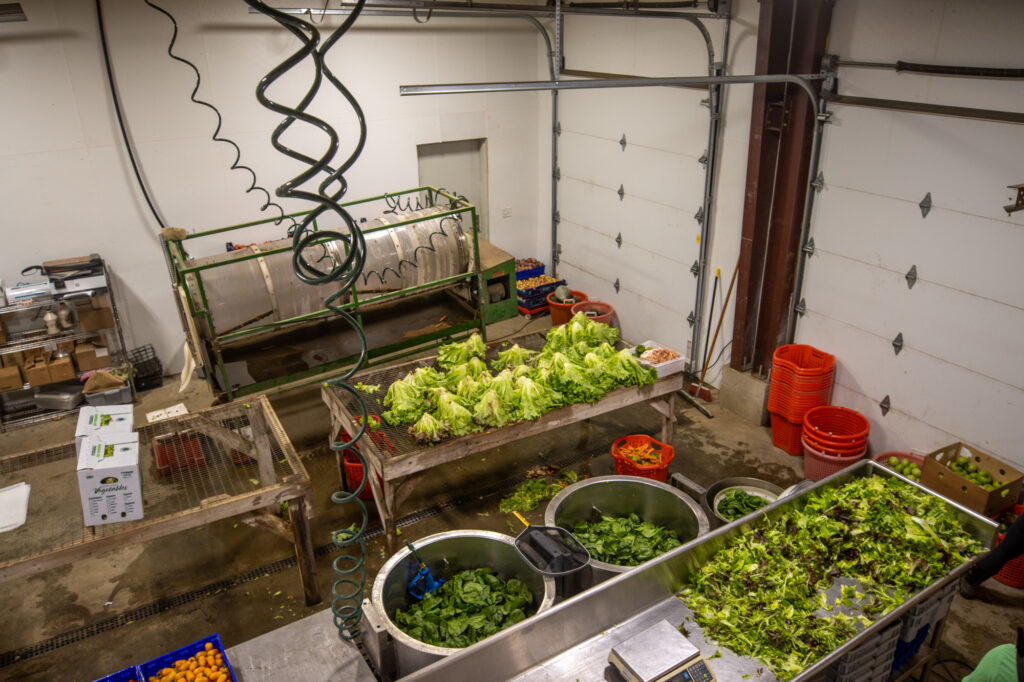
Jacob sketched a few layouts ahead of construction and continues to adapt the space with new equipment, but the utility room, bathroom, cooler, and kitchen are in fixed locations. The garage doors were also set where they are from the original kit design which has worked out pretty well.
Construction Costs
The cost of the project turned out to be about $100/sq. ft. or $120,000. This included the building ($20,000), Contractor labor ($10,000) concrete ($25,000), plumbing, electrical, a walk-in cooler, interior walls and site work. Overall the project “turned out to be a little bit more of a project than I anticipated.”
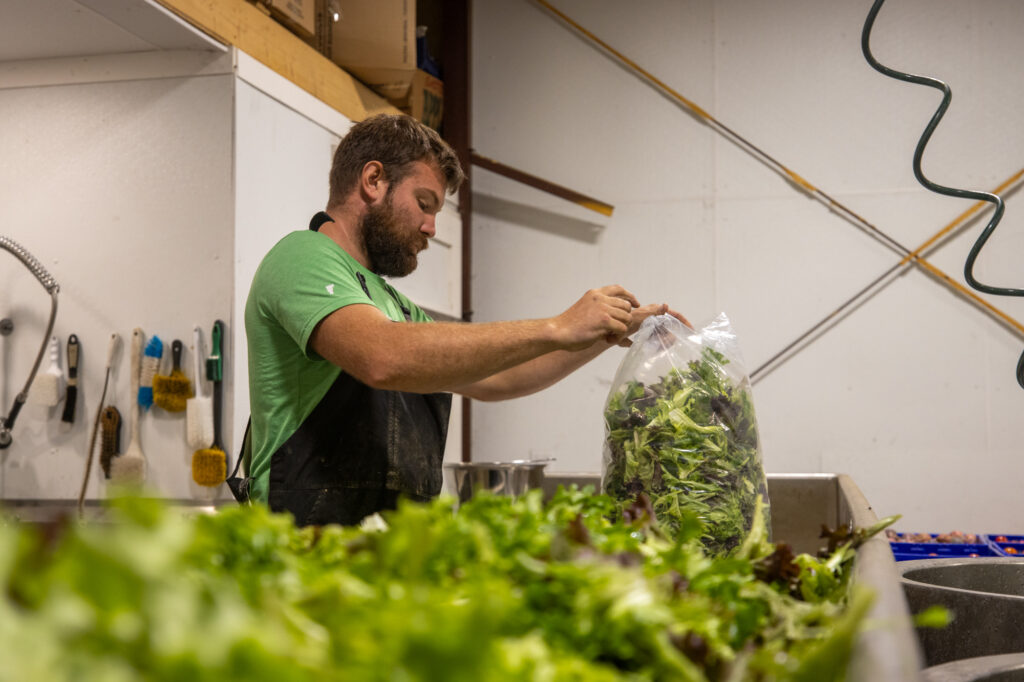
“Having a good plan helps to make a project like this feasible.”
Favorite Features
Good Drainage.
Good lighting.
BEST Feature: The walk in cooler “just makes it possible to handle all the vegetables that come in and out and keep from spoiling. [The refrigeration unit] was built a bit oversized, but helps having a quick recovery time to remove the field heat.”
Future Upgrades
One of the challenges of this space is managing moisture, there is a lot in there and the addition of a dehumidifier, or a heat pump is being considered. This would further condition the space which could help better maintain the produce quality as well.
Eventually he would like to add a loading dock, designed for a pick-up truck height, to support unloading products out of the fields. A porch area around the building is also being considered to use as a covered space for spraying off some heavily soiled crops outside.
Instead of the kitchen, he wishes he had a break area for employees to have lunch and have cubbies or lockers for gear etc. Shoes, change of clothes, snacks/lunch etc. All these ideas are nice to have upgrades, but this building has been a great investment thus far.
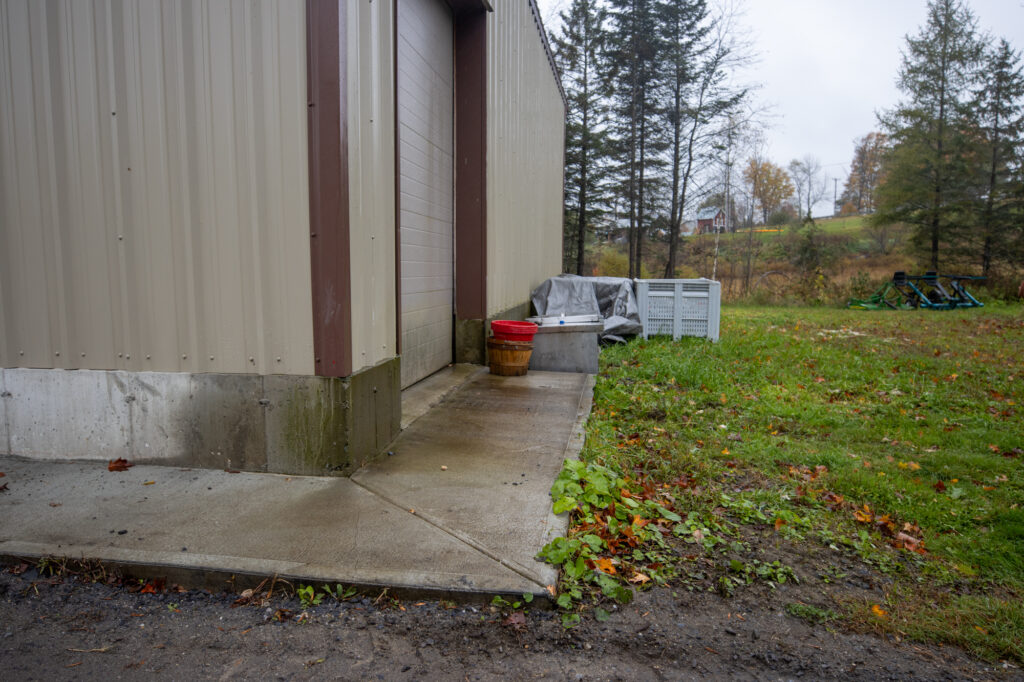
Advice for other farmers: “Better off to make it a little too big than to be cramped.”
How has this space saved you money?
Building this space has saved the farm money largely by reducing the amount of waste. Because they have the space to handle, wash, package, and store the products in the walk-in they are able to make the time to market the surplus to wholesale accounts. Previously the seconds would just get left in the field, or tossed back into the field since there was no space to store it.
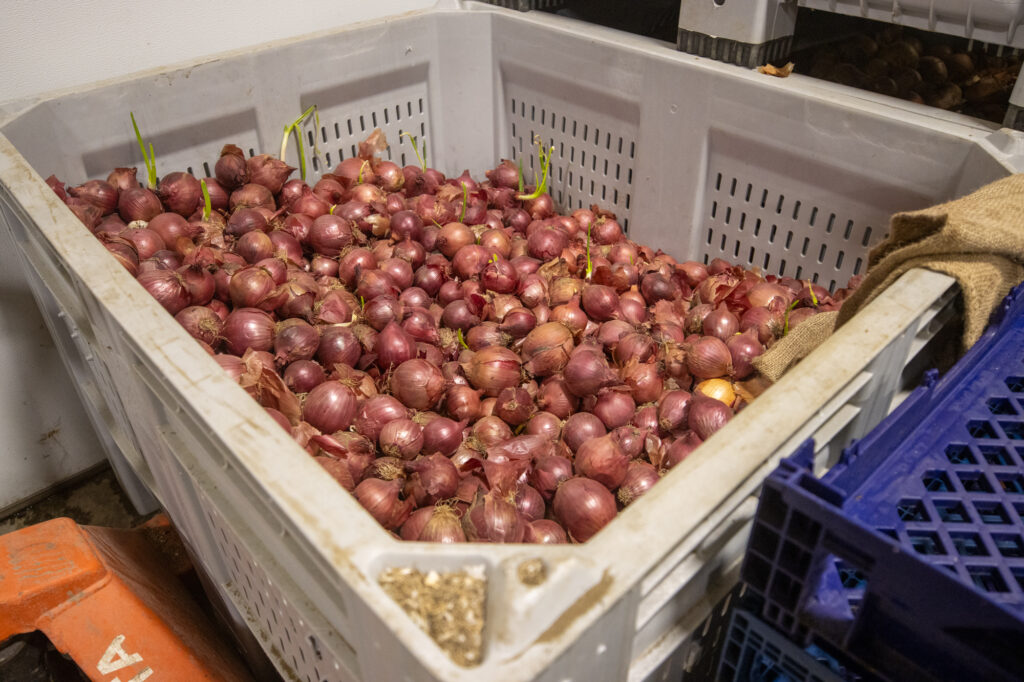
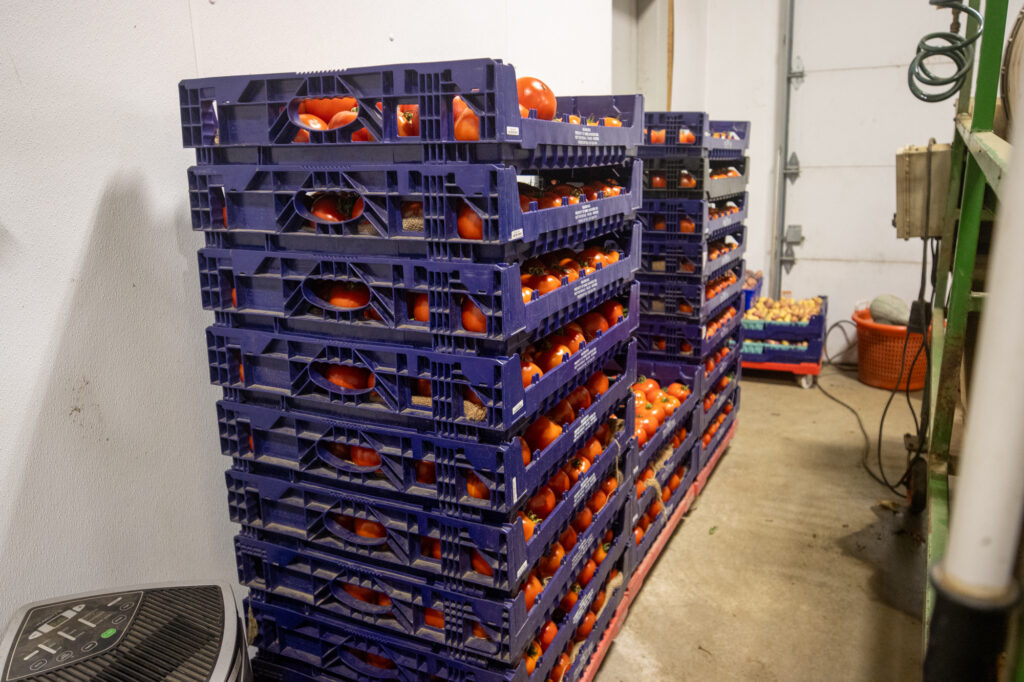
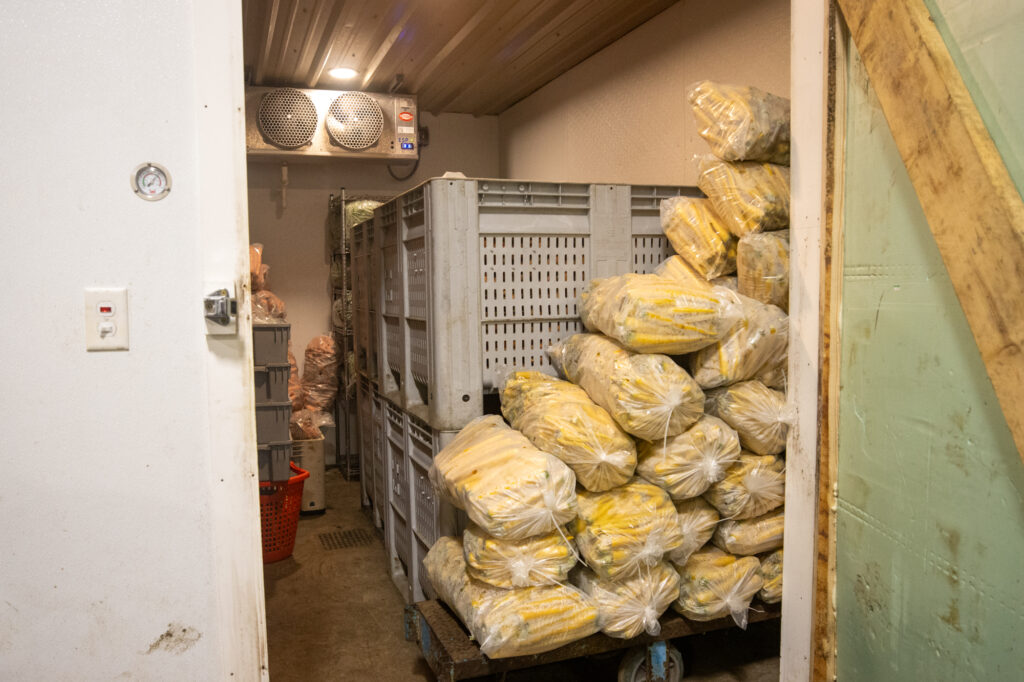
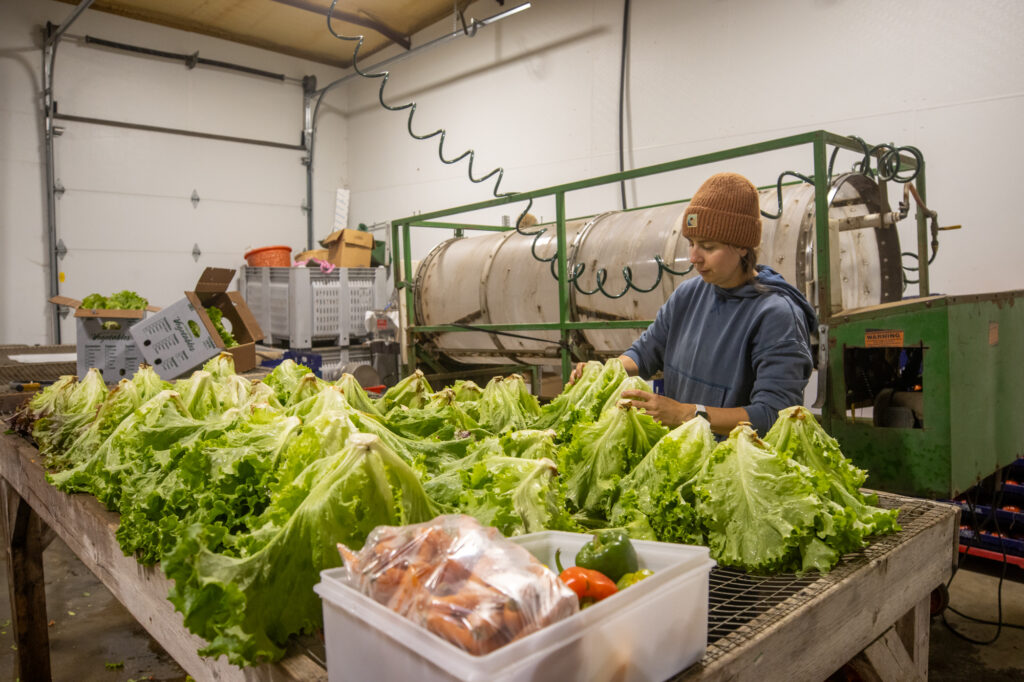
Produce Safety Upgrades
The produce safety investments that made a big difference included stainless steel packing tables and stainless steel wash tanks. The building also houses an employee bathroom and hand wash sink and a cooler to keep the produce cool.
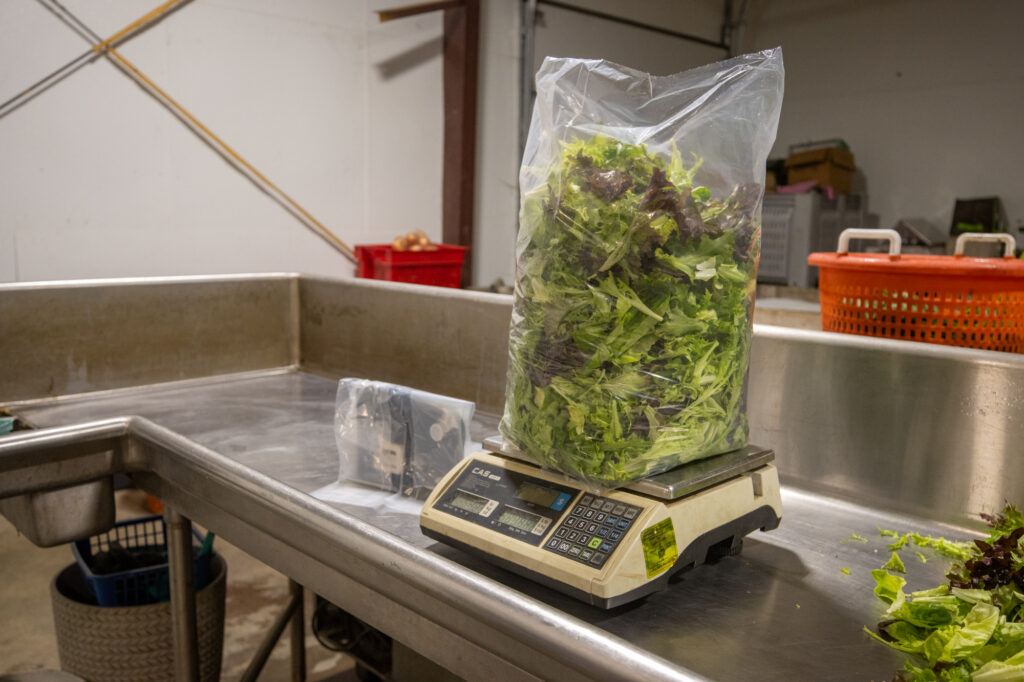
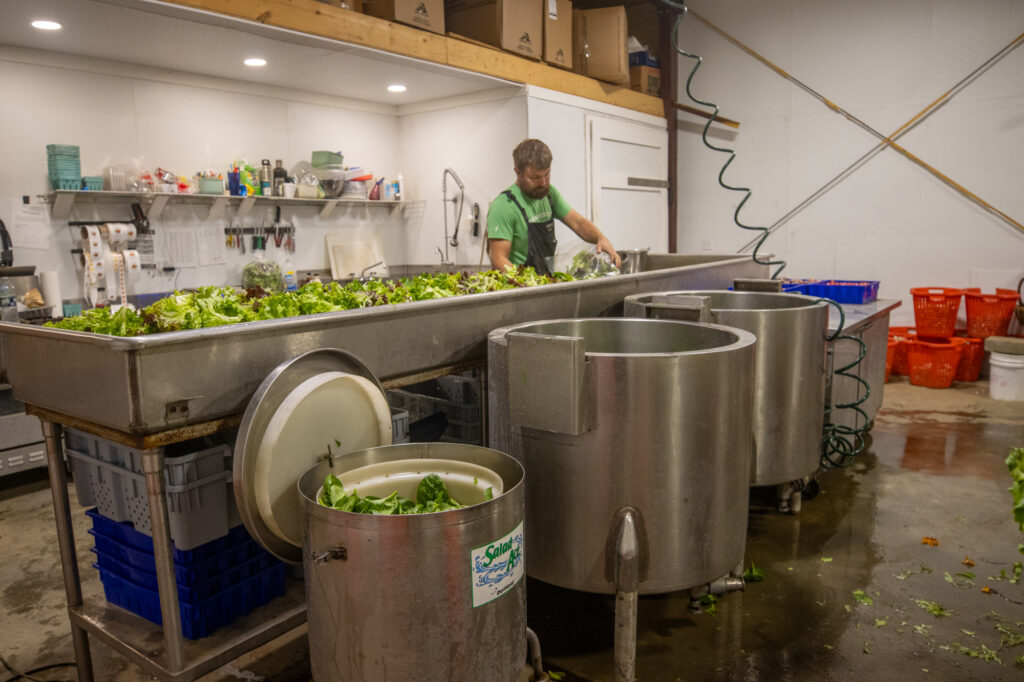
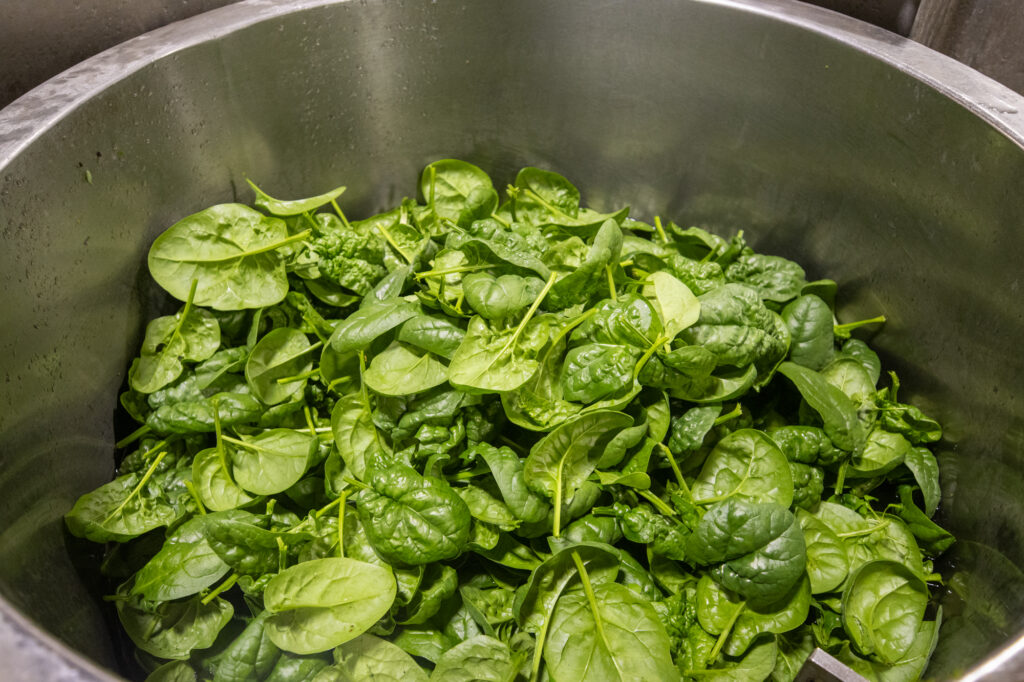
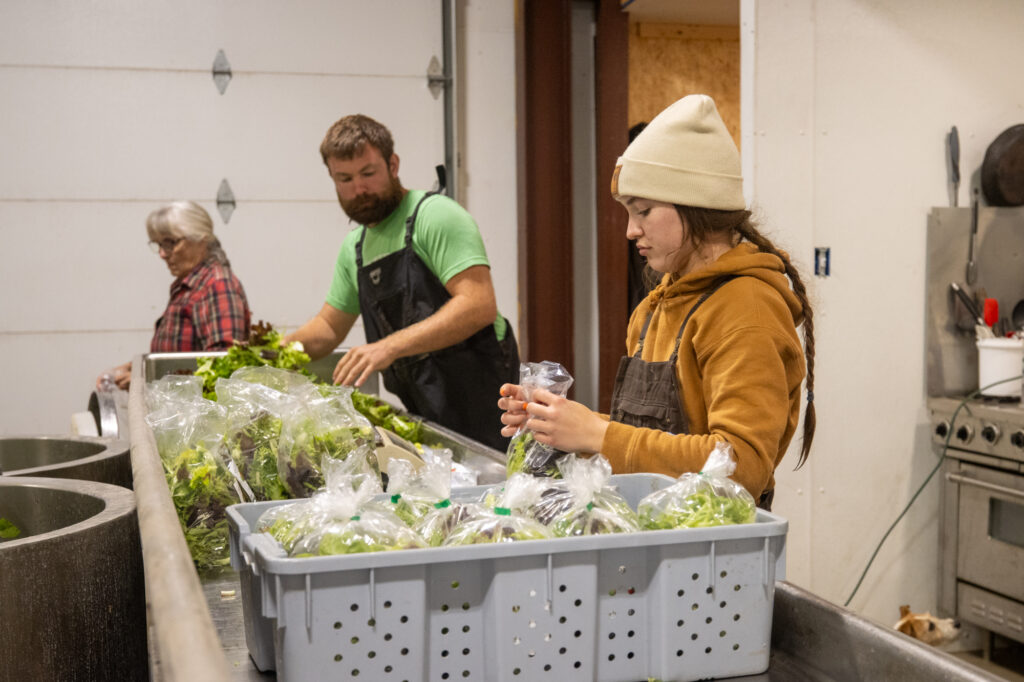
“Overall it has made us a lot cleaner and more efficient.”
Virtual Tour
Click here to explore the building with a virtual tour where you can click, drag, and look around the space.
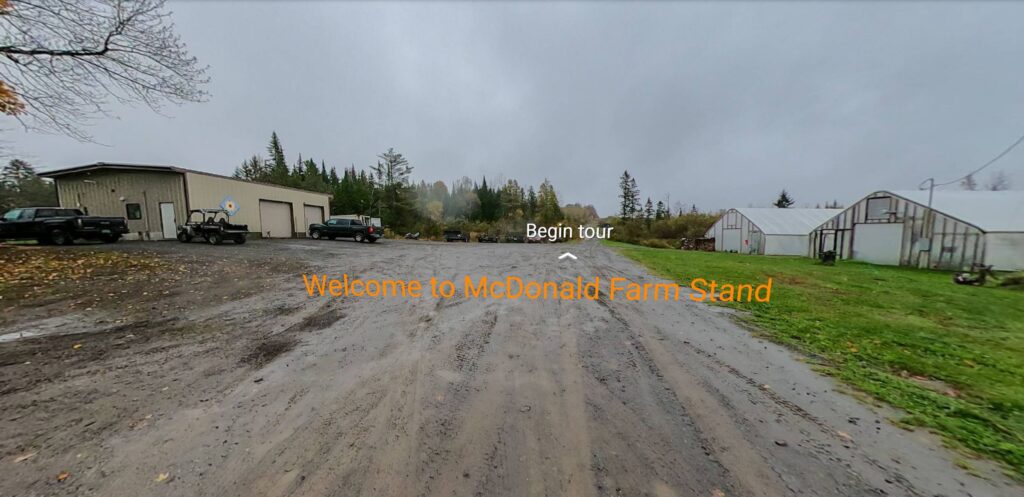