A video version of this case study is available here and a printable PDF is available here.
Evan Perkins & Heidi Choate own and operate Small Axe Farm in Barnet, Vermont. Together, they have been farming mixed vegetables for over 20 years and have been running Small Axe Farm since 2008.
About Small Axe Farm
- 50/50% Greens/mixed vegetables
- 1 acre in production
- $140,000 in Sales
- 80% Direct to consumer wholesale, 20% CSA or local online sales
- 28’x38’ Wash/pack with a 25’x28’ second floor workshop and a loft
- Off-Grid, no-till, certified organic, hillside farm
Goals of the Project
The number one driver for Heidi and Evan’s ‘farm building’ was to bring the vegetable wash and packing activities inside and into a dedicated space. They had done this wet work under overhangs, in sheds, and even their kitchen over the years. They wanted to transition into a dedicated space for the farm activities to be done with increased efficiency and comfort.
The second motivation for the farm building was to provide a climate controlled, clean, sunny space to grow microgreens year round in an efficient manner. Among other reasons, they were trying to manage rodent pressure that caused problems in high tunnel production of these crops.
Evan and Heidi were really excited for the efficiency that this farm building would provide. It all came together with new locations to store containers, walls to post signage, places for orders & standard operating procedures (SOPs), and spots to ensure the right tools were there when needed.
“We really needed a space where we could have everything together. Where we could wash, pack, label, and have cool storage so that we wouldn’t spend a lot of our day walking around looking for stuff because it wasn’t all in one place.”
Evan Perkins
By bringing the work inside, the farmers provided a comfortable working environment. This made life better for them and their employees. Heidi reflected on how she expects to improve retention. “It’s a super pleasant place to work,” she noted, “Everybody enjoys it. Just get some music going or a podcast or something and pack out all day. It’s really fun.” As these comforts were being implemented over the last year Heidi appreciated every improvement they made. “Every little step forward just feels so dramatic.”
About the Project
Evan designed this space to have as few walls as possible and to make almost nothing in the space permanent. The equipment is easy to move, easy to wash and helps the farm pivot between specific uses today and also provides longer term business flexibility. By dedicating a space on the farm for washing and packing “It’s a lot easier for us to keep track of everything,” Evan reflected.
Purpose of the Building
- Wash pack
- Washable surfaces, bin storage, to be more organized, to have cleaning products materials and SOPs all easily accessible, and a centrally located handwash sink
- Storage for packing materials
- Farm shop
- A place to grow microgreens (over $20k a year)
Favorite Features
The Packing Table – It’s compact, clean, holds all labels, and lets 4 people work together side by side.
Growing microgreens – Even growth all year round with consistent airflow, temperature and humidity with very little energy input.
Heidi Choate
“We’ve increased our productivity so so so much we’re looking around saying we’re done! … It’s been really great to put up more food with more ease.”
These increasing efficiencies have led to a more lean farm and it’s allowing Small Axe to pay employees a fair wage. “It allows our higher skilled employees to be really productive, and it also allows us to employ lower skilled employees because we have clear systems that are easy to follow. It’s easier for them to get going.” Evan shared how they were able to employ their teenage son and his friends over the summer and very quickly bring them up to speed since they had SOPs and the right tools in place to quickly train them.
At the time of visit the exterior plan was still under construction, but there will be an outdoor washpack space included, on a slab, under an overhang. This will provide a space to spend outdoors if the weather is nice, serve as a home for bins to be stored, and a place for bins to dry after being cleaned. This covered outdoor space will also be a place for the root washer to live instead of just sitting in the yard.
Building Features
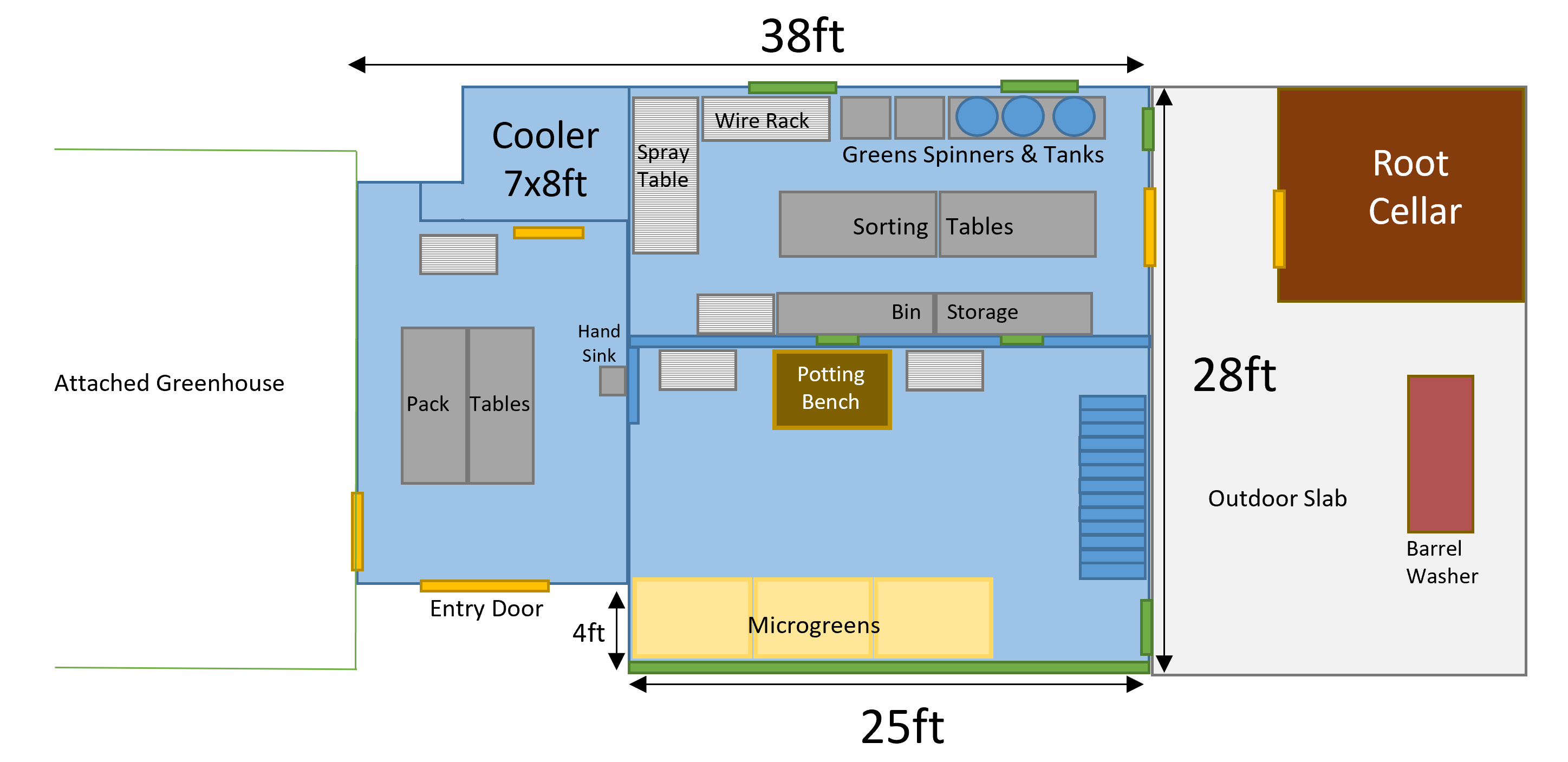
The farm building has a concrete slab with radiant heat pipes in the floor to keep the space warm. The heat source is an efficient outdoor wood boiler but the building uses passive solar heating from south facing windows. These windows also provide a warm sunroom for starting seeds in the springtime and growing microgreens year round. Water connections are installed all around the first floor ceiling to keep hose locations flexible avoiding the need to move them very far across the floor of the building. The floors are sloped to drains in every section of the building to remove the wash water.
Heidi and Evan installed washable surfaces on the walls (Trusscore) which they found to be quite economical due to it being able to be installed directly to the studs. The next closest thing was painted plywood but they felt that wouldn’t hold up as well in the high moisture (hose down) environment of a produce wash room. The ceiling is a painted wood ceiling. They used a process called pickling to protect and preserve the look of the wood grain while brightening up the space. Recessed LED light fixtures are installed throughout, but not usually needed during the daytime thanks to the large windows on the building letting in natural light.
Cost
The cost of this building was around $100,000 to build. The lumber was milled from the property, and it was built by Heidi and Evan with help from friends and family. They also utilized contractors, plumbers, and electricians to get it built during the winter so it could be used the following season.
Evan wishes he didn’t need the retaining wall in the center of the building, and that all the floors could be on the same elevation, but part of these constraints were due to the fact that they were building into the side of a bank, and they were working off part of an existing foundation from an original building that was lost in a fire. Ideally it would be constructed as one big wide open space, with no walls.
Cool or Cold Storage
Small Axe Farm operates off the grid and powers their farm off of solar panels so they do their best to limit electricity use. Cold storage is a need on the farm so they make use of root cellars. These passively cooled spaces are the right temperatures during the shoulder seasons but don’t quite stand up to the summer heat. During the construction phase they built the second, larger root cellar to hold more produce, which is also positioned closer to the farm building. Within the farm building they also built an insulated room which will be a walk in cooler, powered by a CoolBot to keep crops at the appropriate temperature during the peak season.
Evan and Heidi built their root cellar themselves by forming the concrete and building it into a bank. The arched roof is heavily reinforced with rebar and supports a heavy soil load on the roof. The concrete slab will connect the wash pack into the root cellar with a slight ramp to transport crops in and out easily and efficiently.
Connected Greenhouse
Another special feature of the farm building is having an attached greenhouse. This heated high tunnel connects to the farm building. It’s not very often that they get to harvest greens out of this tunnel in the winter time but when they do it’s a dream to never have to step outside. This greenhouse also serves as a place to grow out and harden off seedlings in the spring. Eventually they are going to pour a slab in it so they can just wheel the seedings from the heated farm building and out to the greenhouse to harden off. This will reduce the need to carry flats in and out of the building. This slab utilizes the efficiency of wheeled carts reducing strain on their shoulders and backs. Though young and healthy now they are planning these improvements now so they can keep the passion going and farm into the future.
Contributors to the Project
Small Axe Farm was supported by several different people and organizations. Friends, family and the community rallied together to help them rebuild.
UVM Extension Ag Engineering & Produce Safety Team discussed key elements to include in the design to aid in the flow to embed efficiencies for use.
Vermont Farm & Forest Viability coached them on making the right business decisions to make their farm business successful and sustainable.
A Produce Safety Improvement Grant from the Vermont Agency of Agriculture Food and Markets provided $10,000 in support of washable surfaces and wash/pack equipment.
The Vermont Farm Fund provided an emergency loan to help cover the costs of the rebuild.
Photo Gallery
(Click on the images for a larger view.)
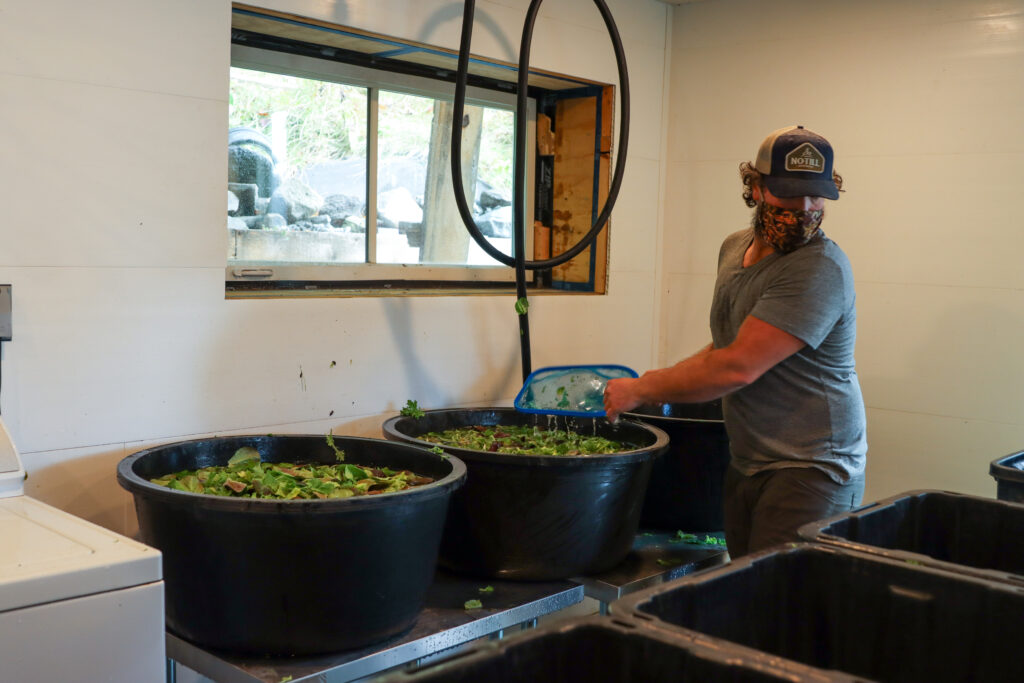

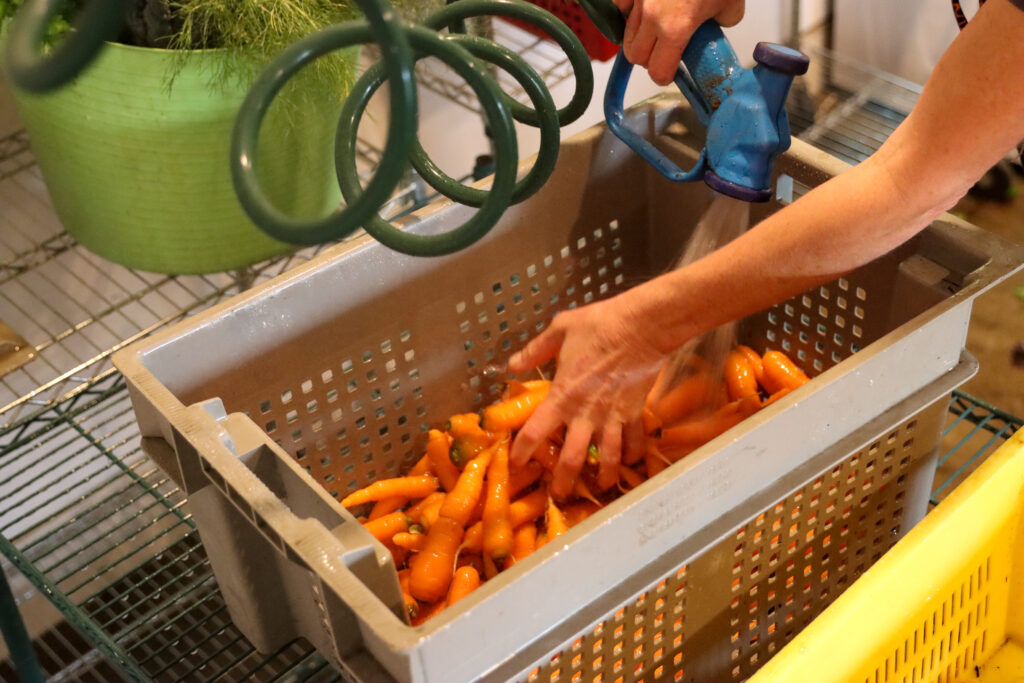



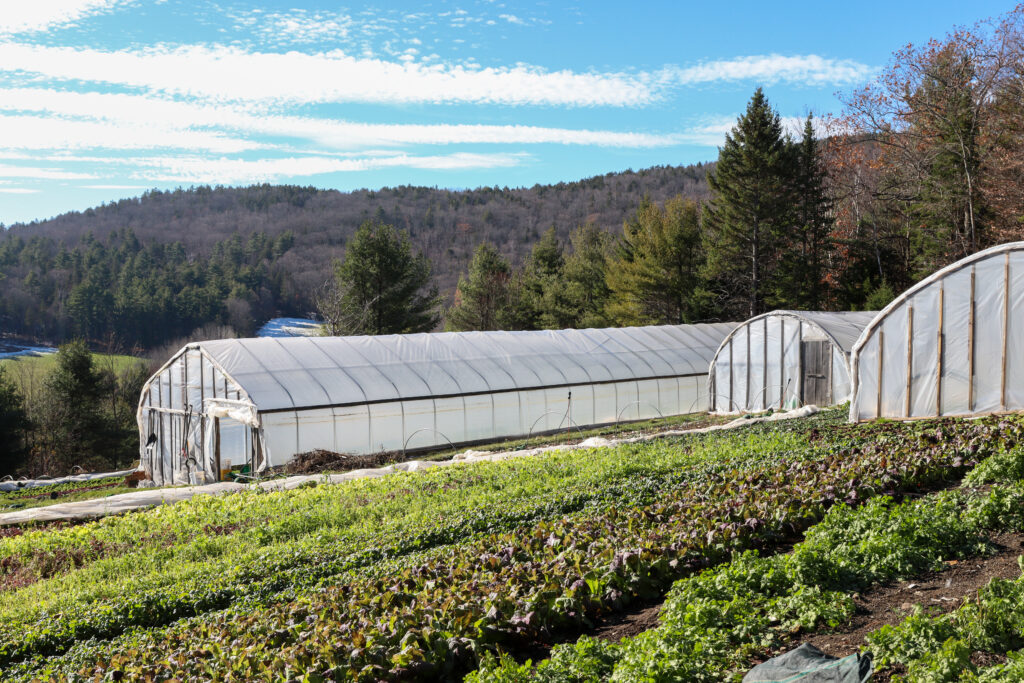
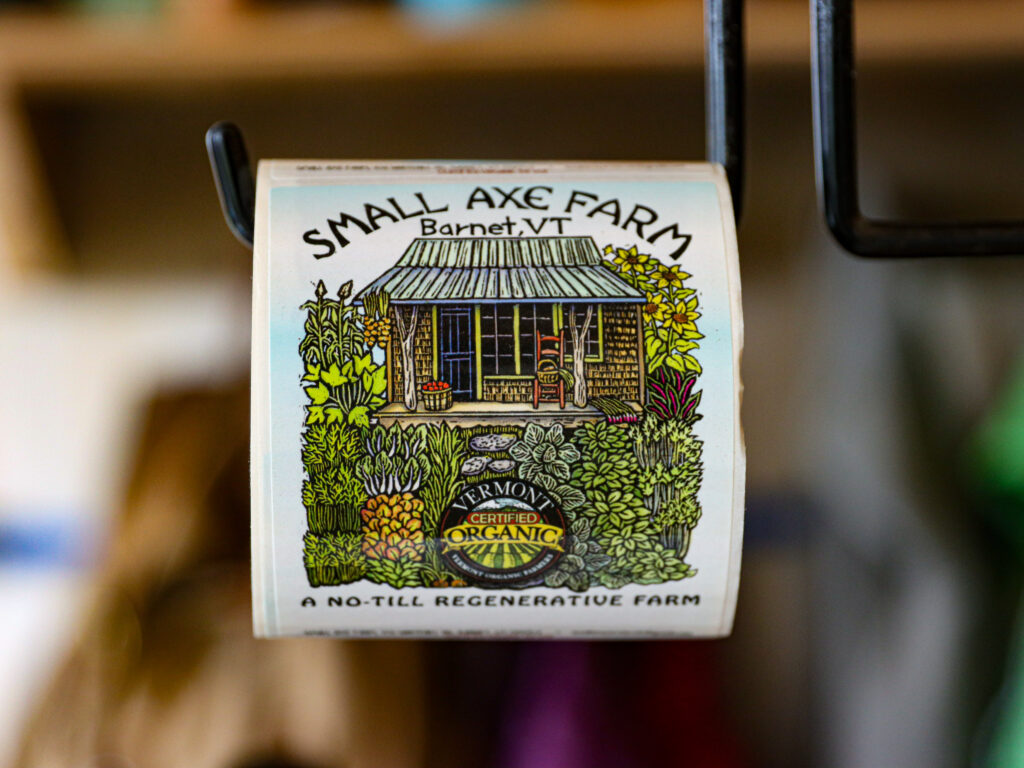

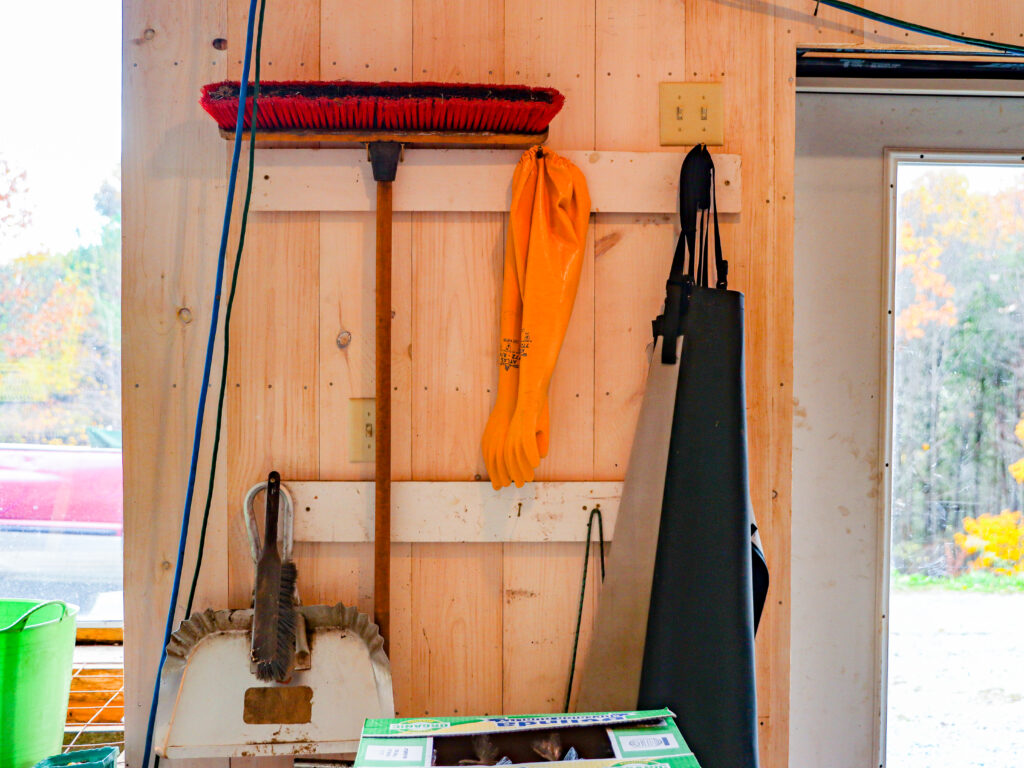
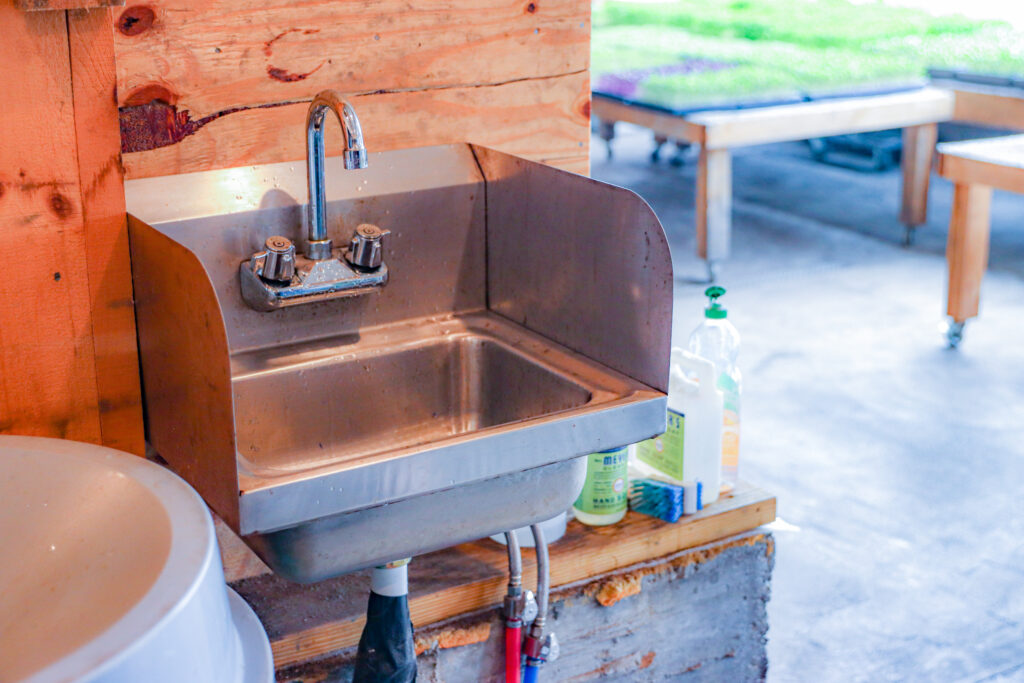
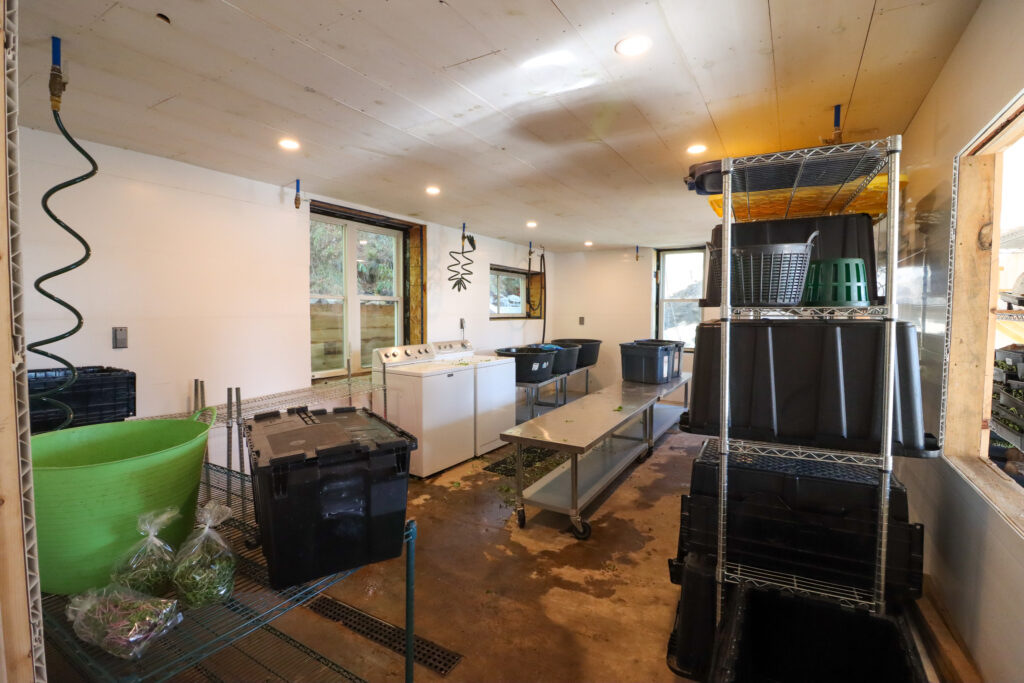
Explore the Virtual Tour
Explore the virtual experience by clicking through and looking around their wash/pack area in this virtual tour.

Watch the Interview
This case study was captured as an interview. To see the full interview, and a look inside their farm check out the playlist on YouTube.
Share this post!
Looking for More?
We have additional post harvest case studies of various renovations and new builds that can be seen here. go.uvm.edu/phcs
All things post harvest covers individual blog posts discussing building features, equipment, and other PDF guides.
Acknowledgements
This case study is possible because of the hard work, wisdom, and generosity of Evan Perkins and Heidi Choate at Small Axe Farm. Without their willingness to take the project on to begin with, deal with all the challenges that such projects bring, and complete it we would have nothing to share. We are grateful to them for their willingness to share their story and knowledge in this form so that others can learn.
Funding for this publication was made possible, in part, by the USDA Northeast Sustainable Agriculture Research and Education program through award LNE19-375, by the Food and Drug Administration through The Vermont Agency of Agriculture Food and Markets via the Integrated Extension Educational Programming in Support of the VAAFM Produce Program Grant 02200-FSMA-2018-01. The views expressed in the publication do not necessarily reflect the official policies of the U.S. Department of Agriculture, the U.S. Department of Health and Human Services or the Vermont Agency of Agriculture; nor does any mention of trade names, commercial practices, or organization imply endorsement by the United States Government or the State of Vermont.