Mark Fasching and Christa Alexander run Jericho Settlers Farm where they grow “good food year round” in Jericho, Vermont. Like many, they started out with a garden and roadside stand and continually expanded to growing over 30 acres of vegetables with 18 greenhouses. As their business expanded over the years, so did their infrastructure needs.
Background
- Acres in production: 30
- 1.8 Acres in protected culture (18 high-tunnels & greenhouses)
- Main crops: Storage roots & salad greens
- New construction of a 45ft x 85ft x 18ft high packshed
- 40% of the packshed area is cooler space
Their infrastructure grew in stages. First, they started their wash/pack out of an old dairy barn and renovated it to suit their needs. Some of these upgrades included adding insulation, washable walls, lights, and a concrete floor with drainage. Adding concrete is what enabled their farm to expand and move things around by a hand truck. Rolling things increased efficiency and eased the burden on their bodies. They also added a wall to separate egg washing from vegetable production and made significant efficiency upgrades in doing so.
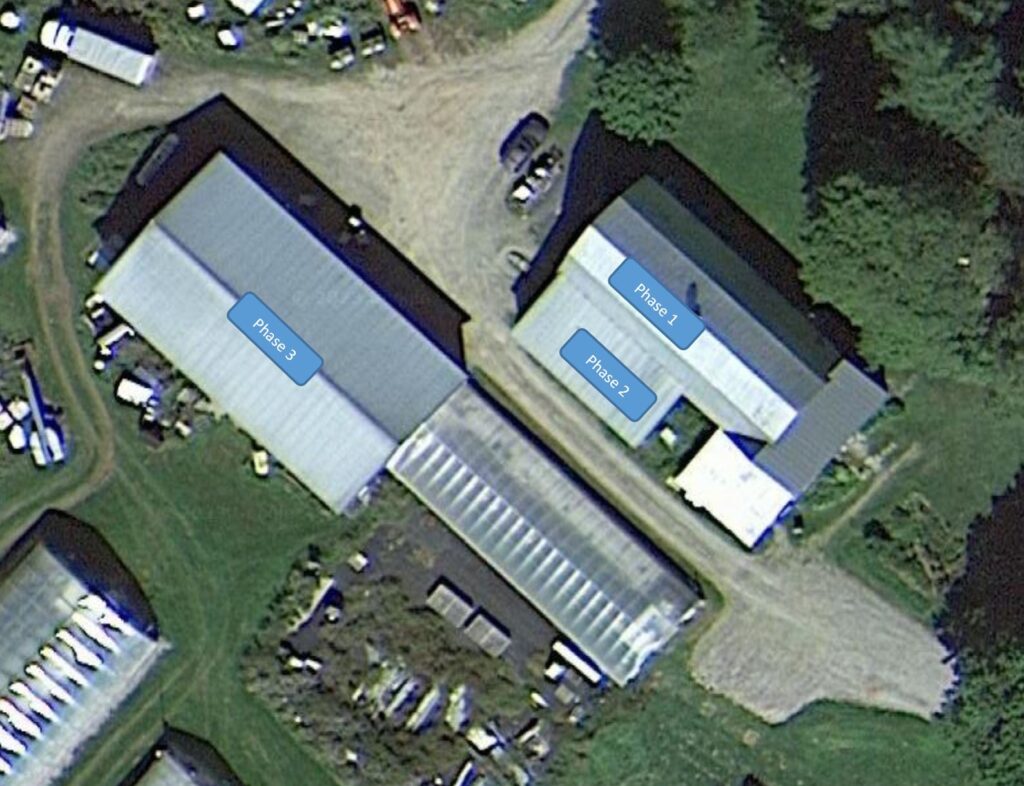
In 2011 they added on some more. They built a 21x43ft extension off the side of the barn which served as 50% cooler and 50% loading dock space to land, sort, and pack product. “At the time we thought it was big enough,” Mark noted. Then they added in dunk tanks, barrel washers, and employees which filled the space quickly.
For sanity, improved workflow, morale, and employee retention they decided it was time to expand again. This time they built a 45ft x 85ft barn to house wash/pack activities and cold storage with a goal of “building something to grow into over the next 5-10 years.”
Construction
The design of this barn was a “head house design” which butted up against an existing greenhouse that is used largely for propagating plant starts. It has proven convenient to have a building attached to it for utility reasons, and some harvest happening right there. This design did pose challenges during the construction trying to work up to, and not damage the existing infrastructure.
Mark shared, “Farming is about handling materials, so if there are ways to reduce the number of times you have to handle something you become more profitable.” By including large overhead doors it removed a potential pinch point moving product in from the field, or out from the coolers. This space also allowed moving from a hand truck to a forklift, enabling them to stack bins to the full height of the barn’s 18’ ceiling.
Everything that wasn’t on wheels, was put on wheels to make the space adaptable to the needs of a given day. Dunk tanks? Trash cans? You can roll them both into place, or out of the way. Part of the open floor plan design included utility drops from the ceiling. Both power and water is available in several locations without stepping on cords, or tripping over hoses. This greatly increases safety from multiple angles including tripping, electrical and produce safety concerns.
Before taking on a construction project Mark suggested that you should ask yourself “why are you expanding?” Are you doing so to fulfill an open market opportunity, or are you expanding to not feel so cramped? Knowing the why behind the expansion will help answer the questions around how big or elaborate the project becomes. Regardless of the reason though, he recommends “build as big as you can afford,” and visit other farms to understand how others move product. By visiting other farms, Mark and Christa were able to take away good ideas and apply what would work well for their application.
Building Photo Gallery
(Click on a photo to view larger)
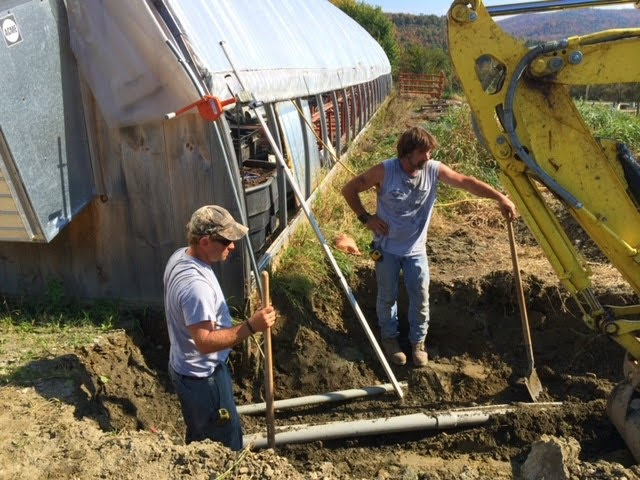
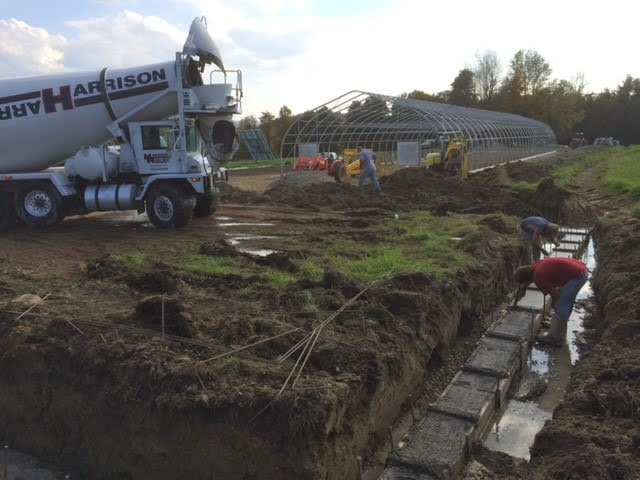
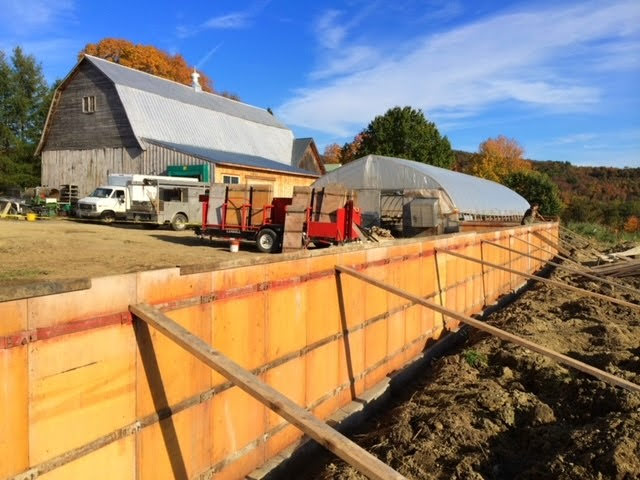
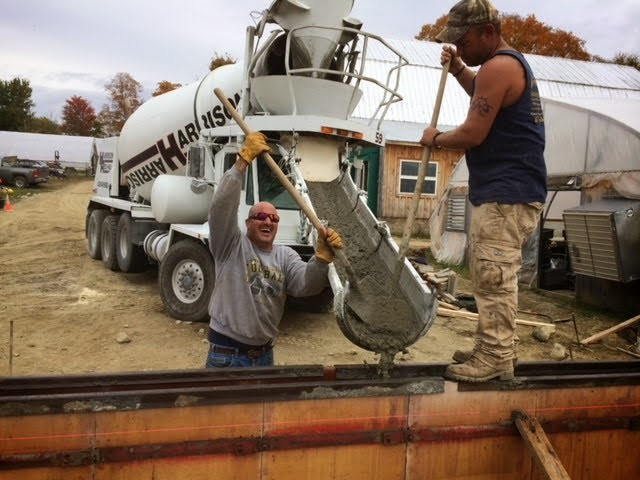
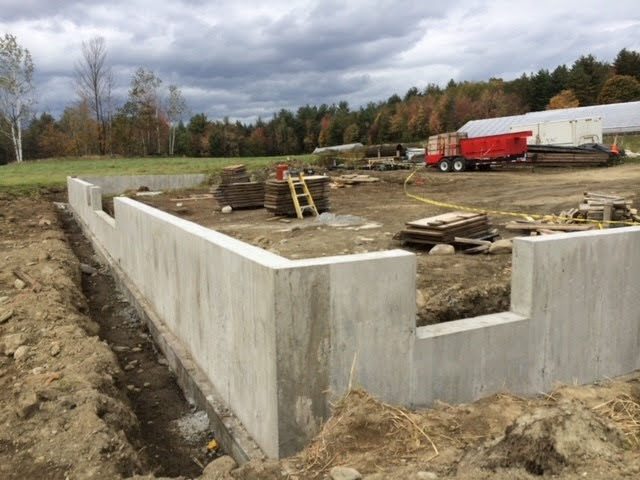
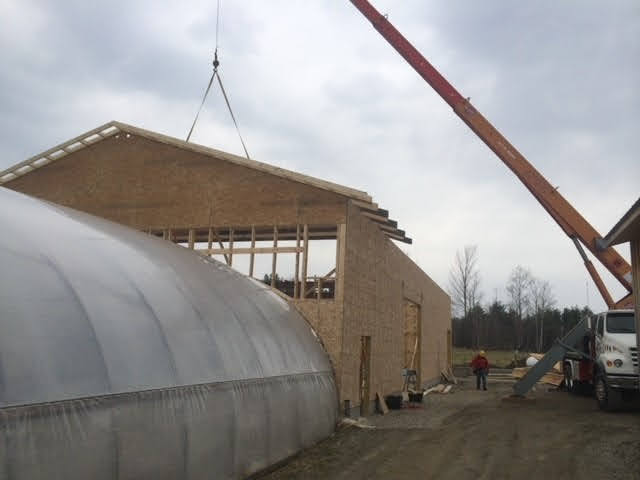
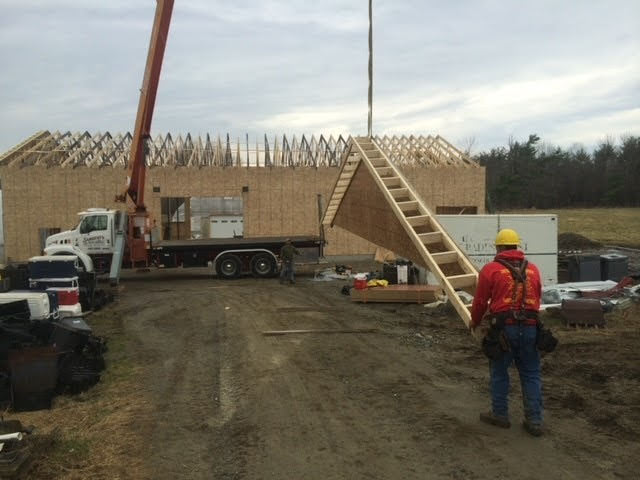
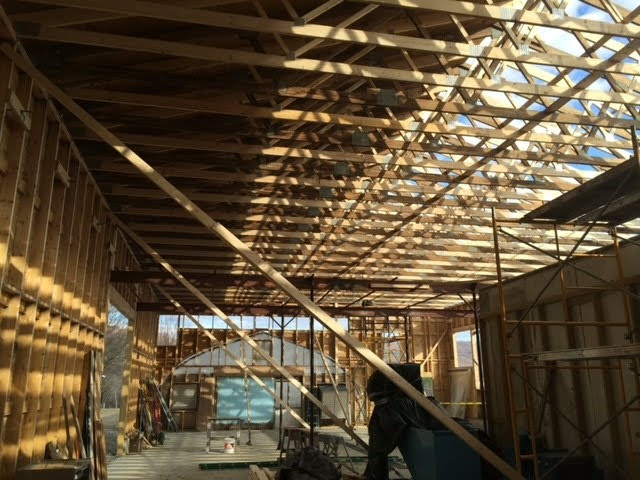
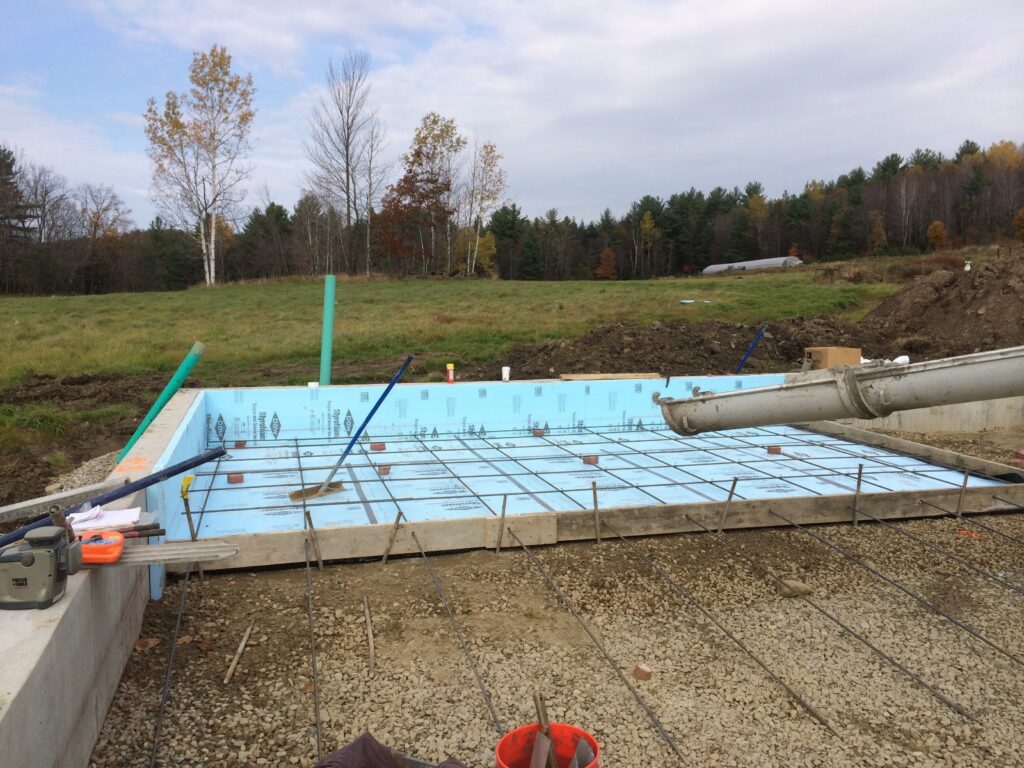
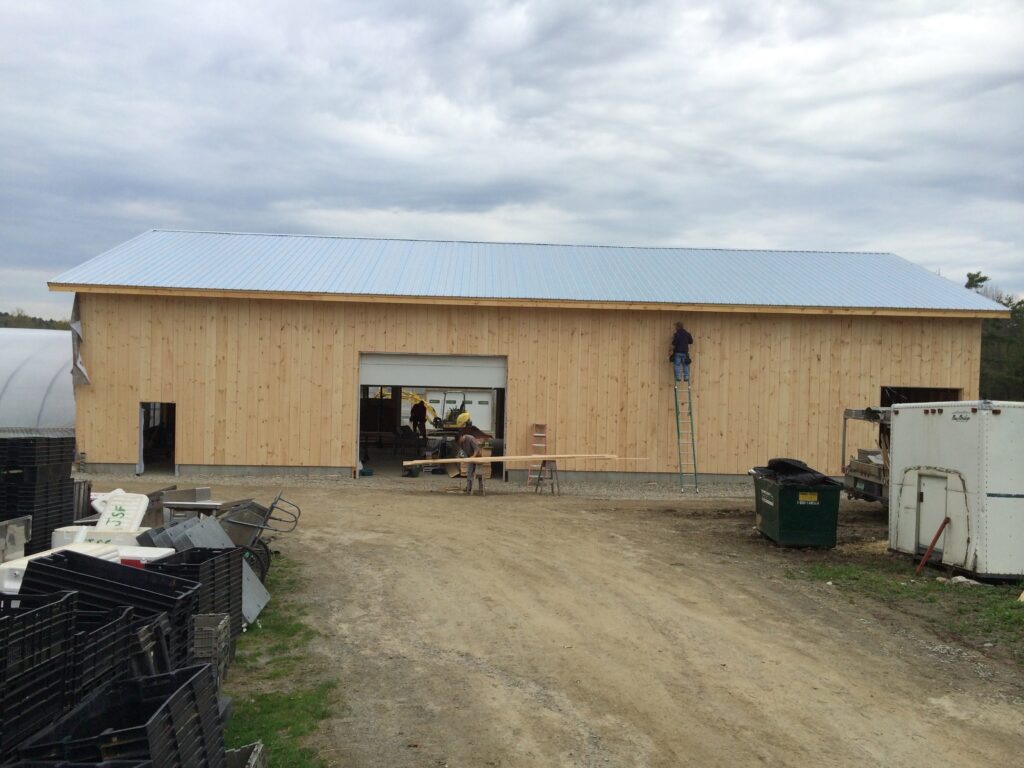
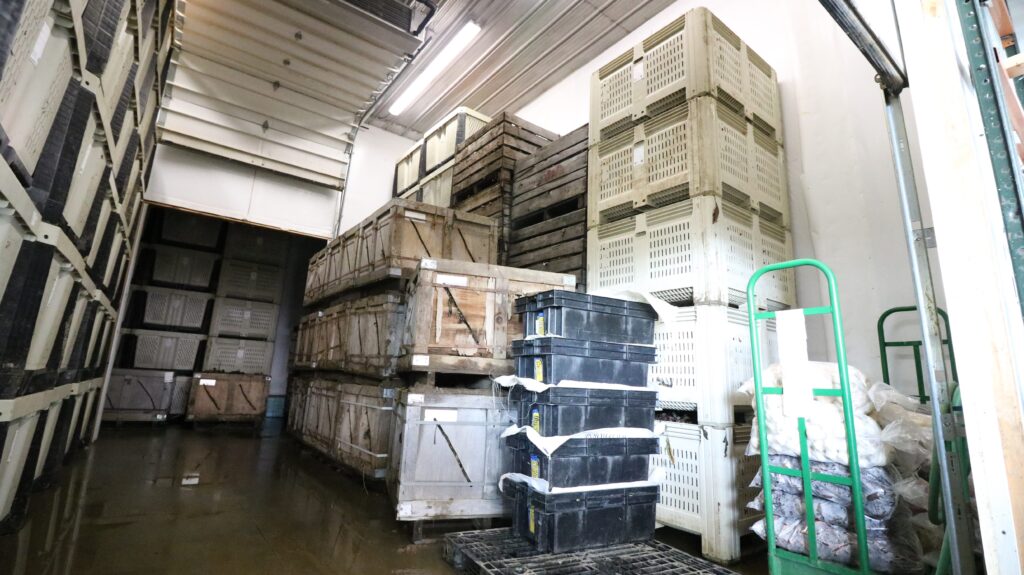
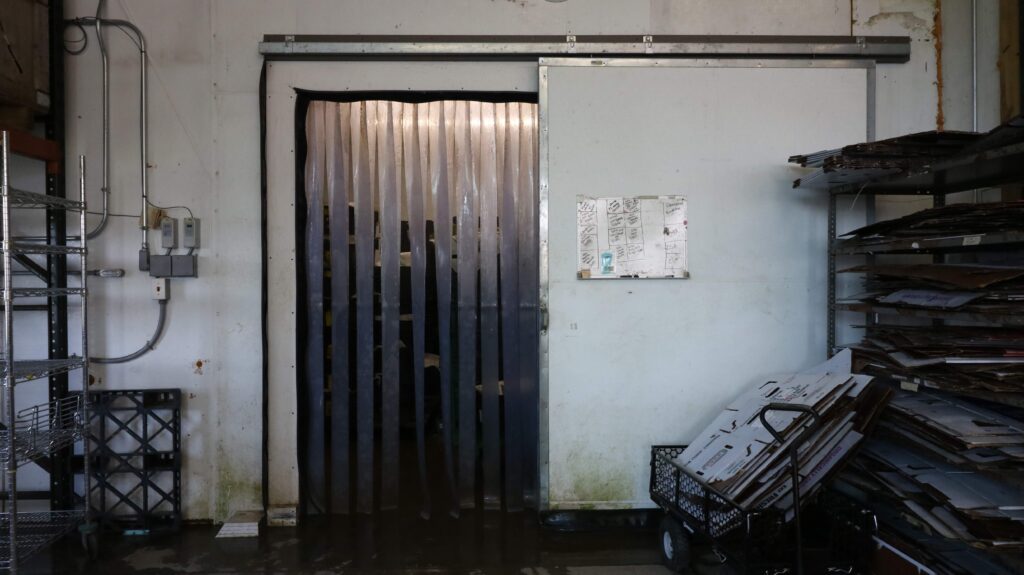
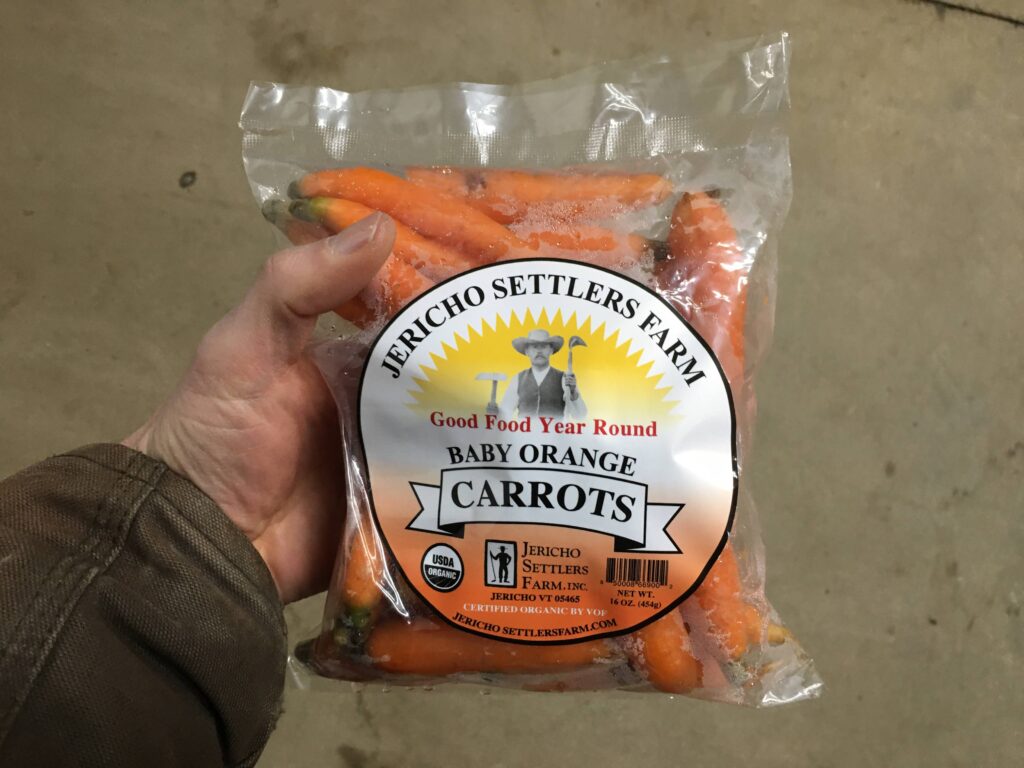
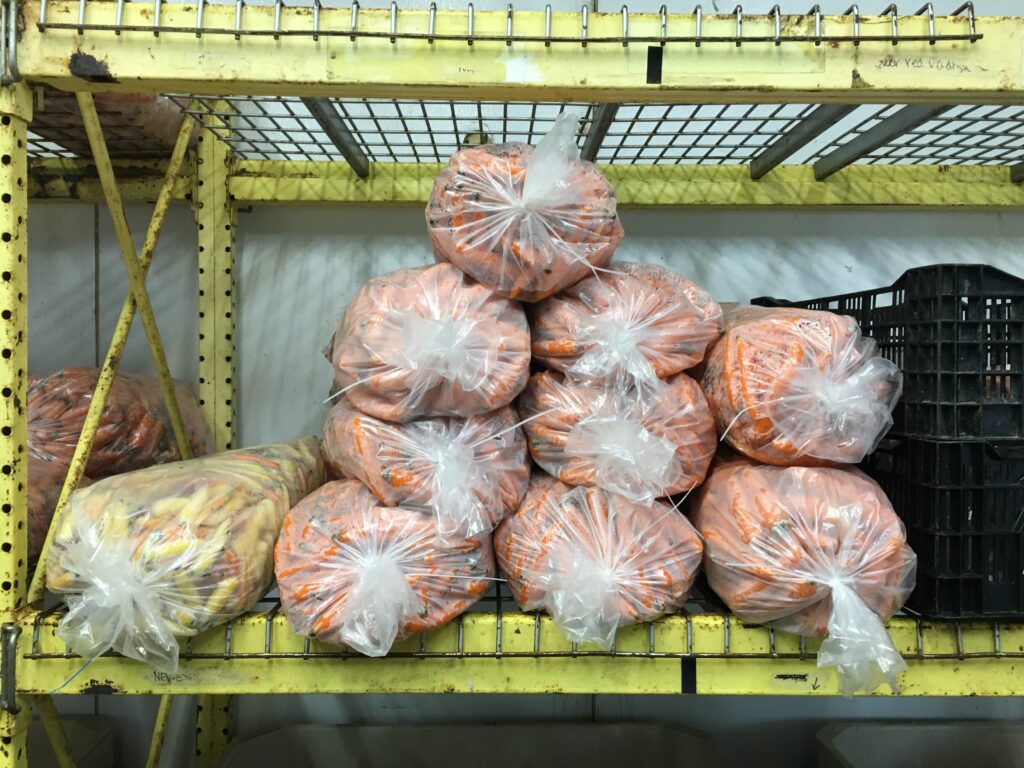
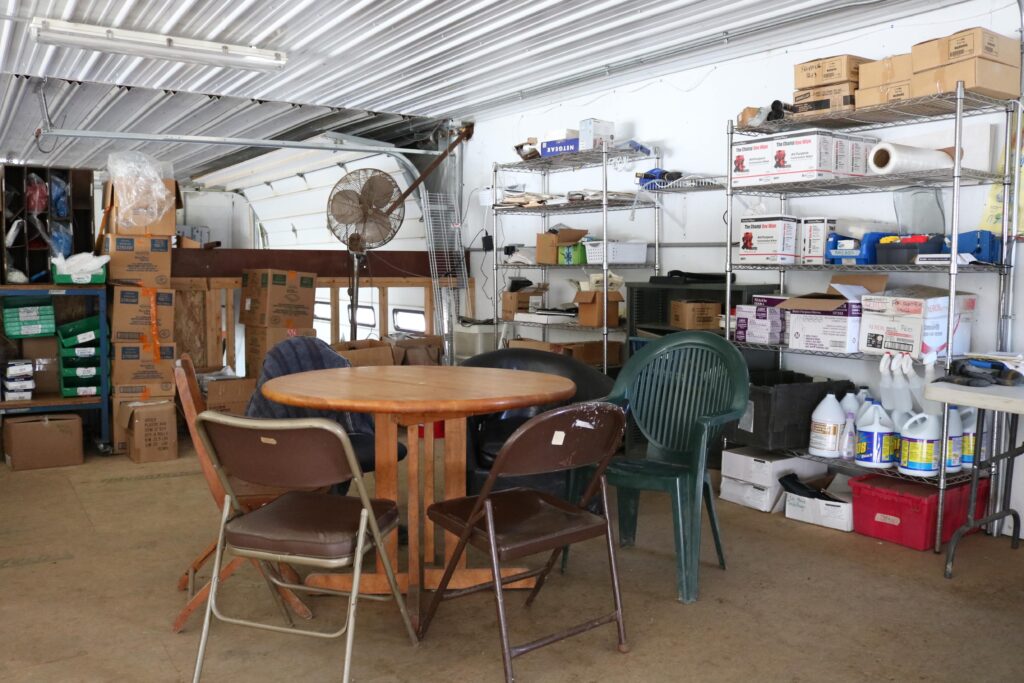
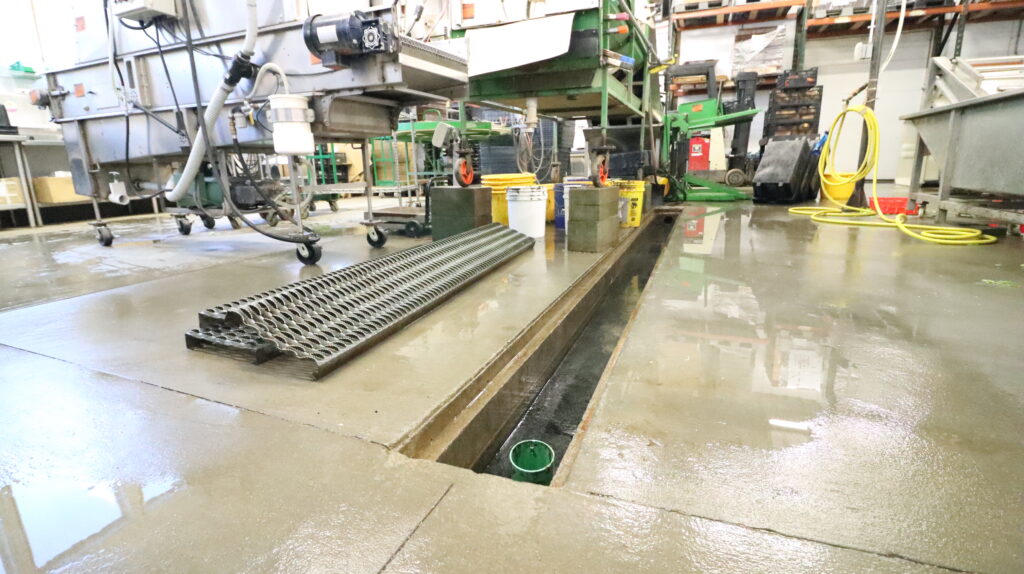
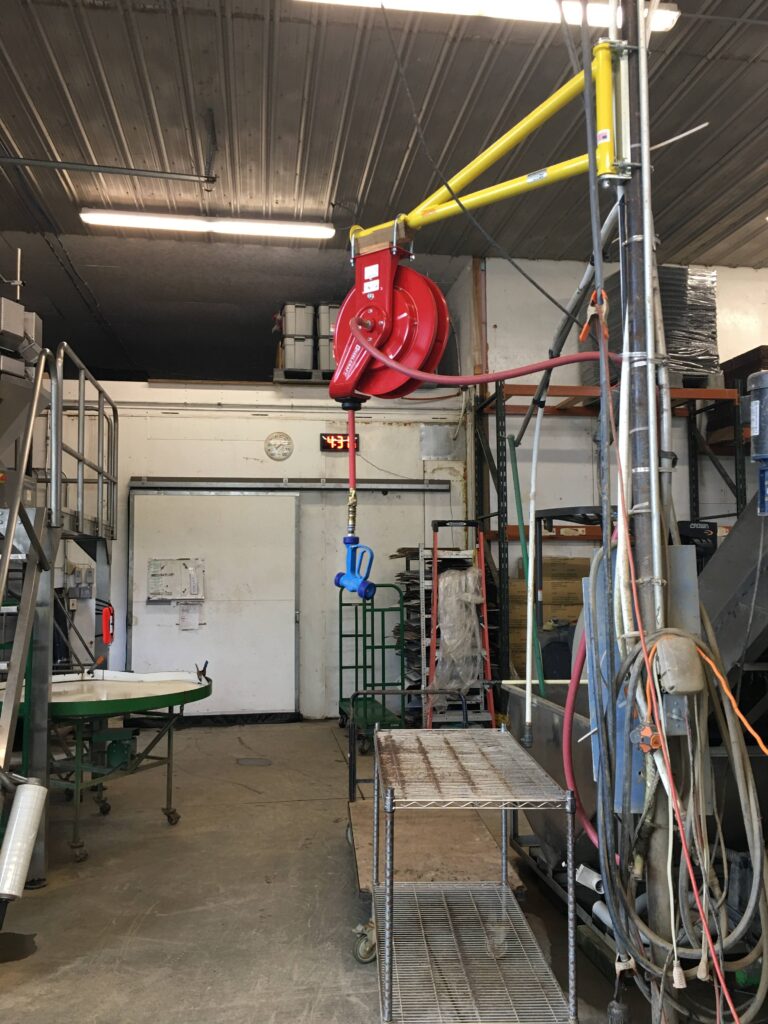
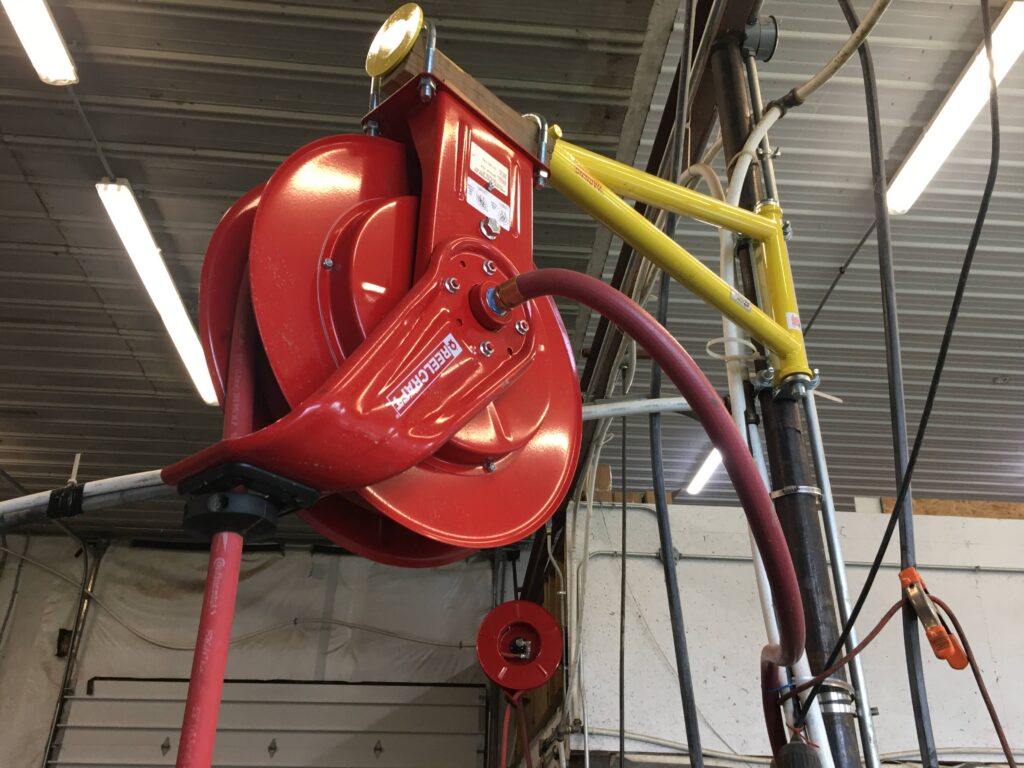
Flow & Floor Plan
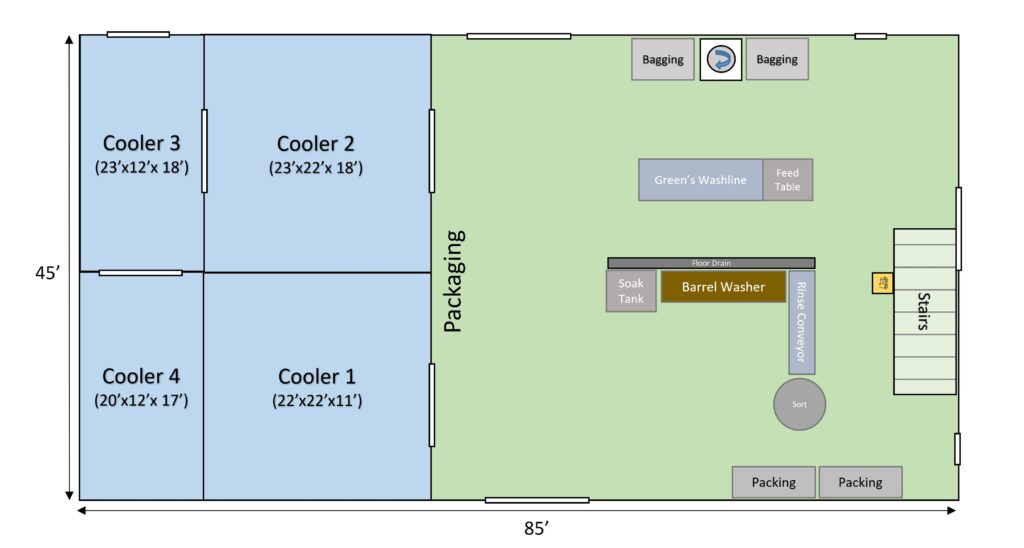
Cooler 1 is the market cooler filled with washed crops packaged and ready to go. Cooler 2 is the field cooler filled with freshly harvested crops. Originally they needed 4 storage zones because they grew a variety of crops. Cooler 4 was built heated with its own zone to cure and store sweet potatoes. They have since stopped growing sweet potatoes and opened up the wall between cooler 2 & 3 and now is all one “zone” for storage roots.
Wash/Pack Equipment
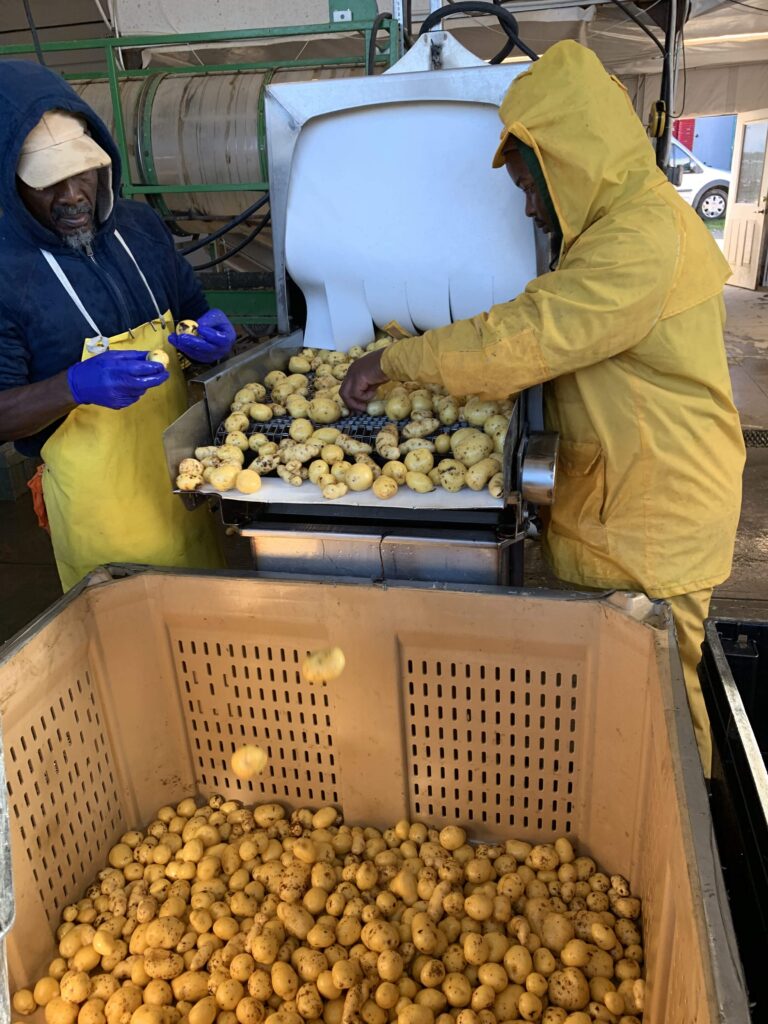
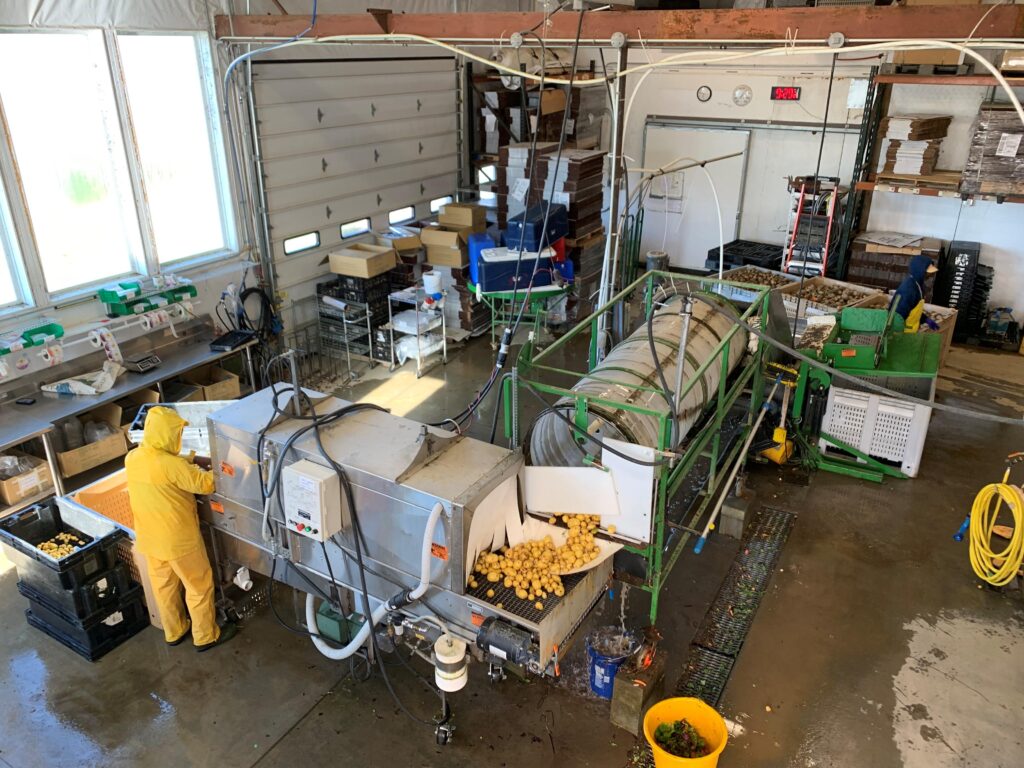
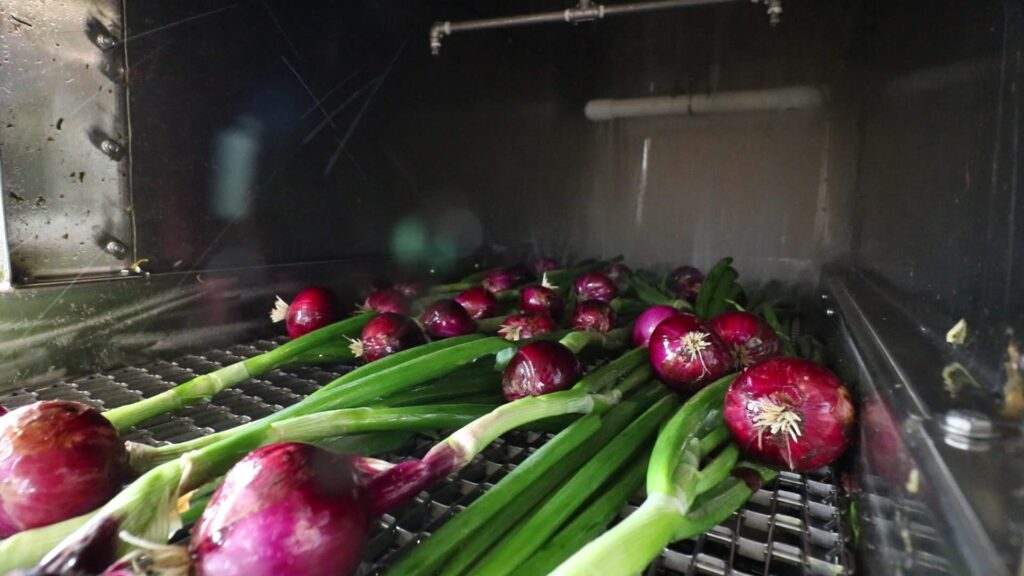
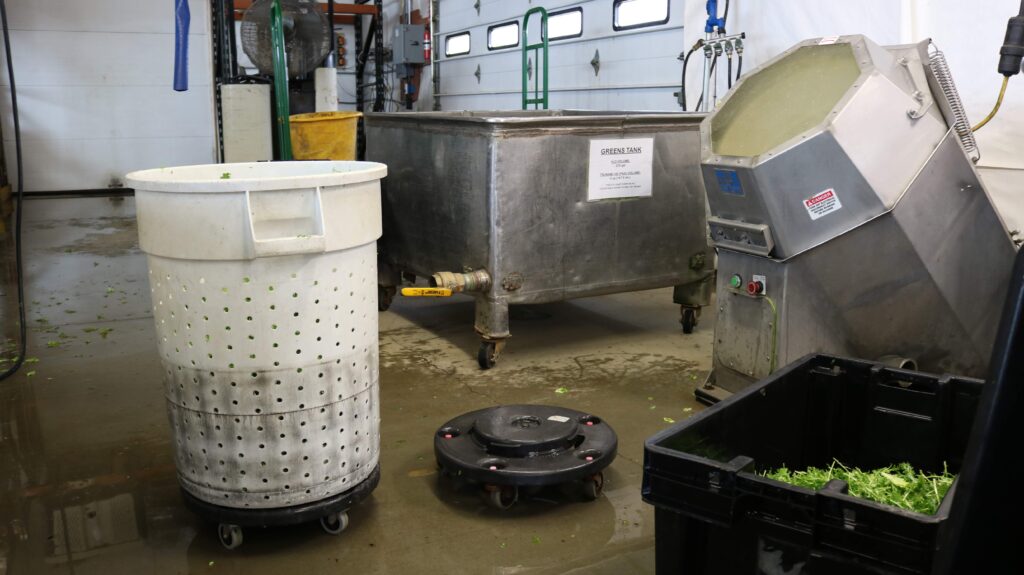
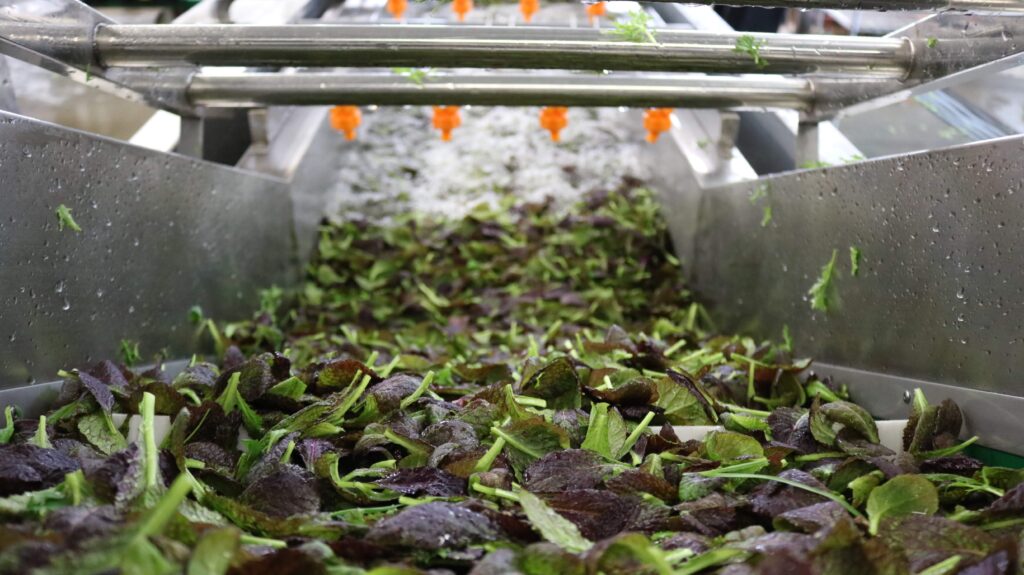
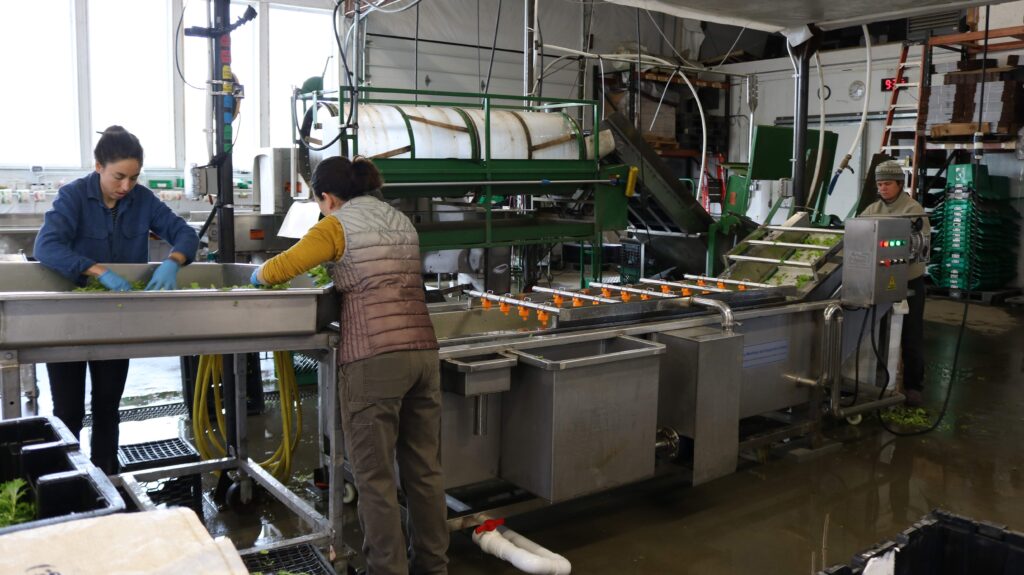
Lessons Learned
- “Build it twice as big as you think you need”
- Don’t limit your size just because you can get a deal (for example – cheap trusses limited the size of the building)
- “The first build is the cheapest build”
- Didn’t insulate the floor, and might have been a good idea in the long run.
- Exterior grading/drainage is a continued problem – should have built the building up higher than it is. Water (and silt) comes right down at, and into the building
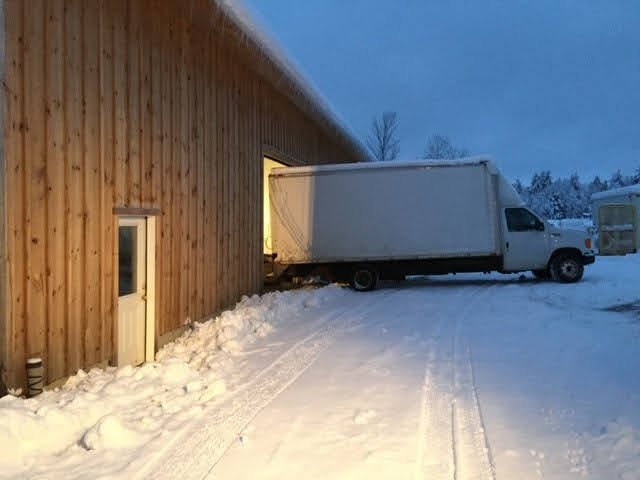
Virtually Visit Through Video & Interactive Media
More videos from their farm can be seen in this playlist.
Virtual Tour
Virtually walk through their wash/pack building with this 360 tour!
Listen to the Podcast
We interviewed Mark and Christa on The Farmer’s Share Podcast. It goes far beyond this barn expansion project as we learn how they grew their farm from selling at their local farmers market, to producing good food year round wholesaling storage crops into Vermont’s food system. They share the reasons why they stopped raising livestock and doubled down on veg, as well as reflect on what advice they’d give to themselves starting out, and how that answer would be different for new farmers in today’s age of agriculture. Mark and Christa both share the struggle of managing a business and how they’ve structured that to work together with raising their family.
Share this Post Harvest Case Study!
https://go.uvm.edu/jerichosettlers
Explore More Case Studies
Acknowledgements
This case study is possible because of the hard work, wisdom, and generosity of Mark Fasching and Christa Alexander at Jericho Settlers Farm. We are grateful to them for their willingness to share their story and knowledge in this form so that others can learn.
Funding for this publication was made possible, in part, by the Food and Drug Administration through The Vermont Agency of Agriculture Food and Markets via the Integrated Extension Educational Programming in Support of the VAAFM Produce Program Grant 02200-FSMA-2018-01. The views expressed in the publication do not necessarily reflect the official policies of the U.S. Department of Agriculture, the U.S. Department of Health and Human Services or the Vermont Agency of Agriculture; nor does any mention of trade names, commercial practices, or organization imply endorsement by the United States Government or the State of Vermont.
This project was supported by the Food and Drug Administration (FDA) of the U.S. Department of Health and Human Services (HHS) as part of a financial assistance award 02200-FSMA-24-01 totaling $30,000 with 100 percent funded by FDA/HHS. The contents are those of the author(s) and do not necessarily represent the official views of, nor an endorsement, by FDA/HHS, or the U.S. Government.