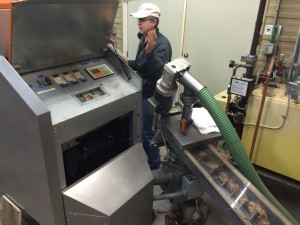
Recent testing at the Meach Cove Trust has demonstrated strong economic and technical feasibility of grass-based biomass combustion fuels. The use of solid, densified, cellulosic biomass fuels has been well demonstrated with wood pellets in residential and light commercial systems and wood chips in larger, often centralized systems. The Grass Energy Partnership of the Vermont Bioenergy Initiative has been exploring an alternative form of fuel; grasses densified in a specially developed processor to take the form of 1.5”-2.0” round cylindrical pucks. Grass fuels may be produced on otherwise marginal agricultural land, sometimes in perennial production and even in buffer strips offering environmental benefit. Additionally, fuel can be made by densifying agricultural residue or biomass harvested from idle pasture or fields. We have referred to this fuel as “Ag Biomass”. The testing summarized in this report has demonstrated the technical and economic feasibility of such fuels.
Earlier tests were done using pellets of various feedstocks (mulch hay, reed canary grass, and switch grass) and combinations of feedstocks (mixed with wood) (Sherman, 2011). This testing was done in a Solagen boiler (500,000 BTU/hr) designed for wood pellets. The primary findings of this work confirmed reasonable heating value of the fuels, relatively high ash content of the grass fuels (4.3-6.7%), different combustion air and mixing requirements of the fuel with potential for fusion (clinkers), and relatively high levels of chlorine in the grass fuels which is suspected to accelerate corrosion of internal appliance surfaces. This report also noted that the challenges associated with high ash content and clinker formation could be alleviated with appliance design considerations such as automated ash removal and a moving floor or cleanout cycle. Detailed emissions profiling was also conducted as part of this prior work.
A review of the potential for a grass energy industry in Vermont has also been conducted earlier (Wilson Engineering, 2014). This work focused on assessing several production and marketing models (Closed Loop No Processing, Small Scale On-Farm Processing, Regional Processing, Consumer Pellet Market). The report concluded that Small Scale On-Farm Processing presents the greatest challenges and that Closed Loop No Processing would be the easiest to implement.
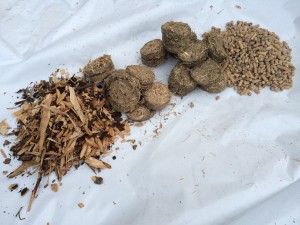
This new report documents recent testing involving the densification and combustion of solid, grass biomass fuels in a small commercial boiler (342,100 BTU/hr output rating). Fuel briquettes (or “pucks”) were made from Switchgrass, Miscanthus, Reed Canary, Mulch Hay and “Ag Biomass” / Field Residue as well as mixtures of these feedstocks with ground wood chips. Our findings were:
- On-farm, small scale densification of grass and agricultural biomass solid fuels via pucking is feasible with a conversion (densification) cost of $49-148 per ton and a finished fuel cost in the range of $85-228 per ton ($5.2 – 14.4 per million BTU).
- Sustained, reliable combustion of densified grass and agricultural biomass solid fuels in a light commercial boiler (EvoWorld HC100 Eco) is feasible with 73-90% combustion efficiency, and with no ash fusion or clinker development. Longer, sustained overnight runs did result in some combustion chamber clogging with ash and fuel residue which may be resolved with further boiler tuning and clean out cycle timing adjustment.
- The test of the Ag Biomass / Field Residue fuel demonstrated feasibility at a current delivered price of $214 per ton ($13.2 per million BTU) supporting a potential payback period of 3.6 years on the boiler. At higher production volume projects a path to $85 per ton ($5.2 per million BTU) and a potential payback period of 2.4 years.
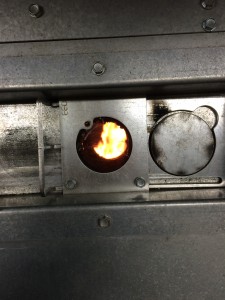
This project was funded by The Vermont Bioenergy Initiative of the Vermont Sustainable Jobs Fund in partnership with UVM Extension and Meach Cove Trust. Project partners included Chris Davis (Meach Cove Trust), Chris Callahan (UVM Extension Agricultural Engineer) and Sid Bosworth (UVM Extension Agronomist), and Adam Dantzscher and John Bootle (Renewable Energy Resources).
Report Citation:
Other References: